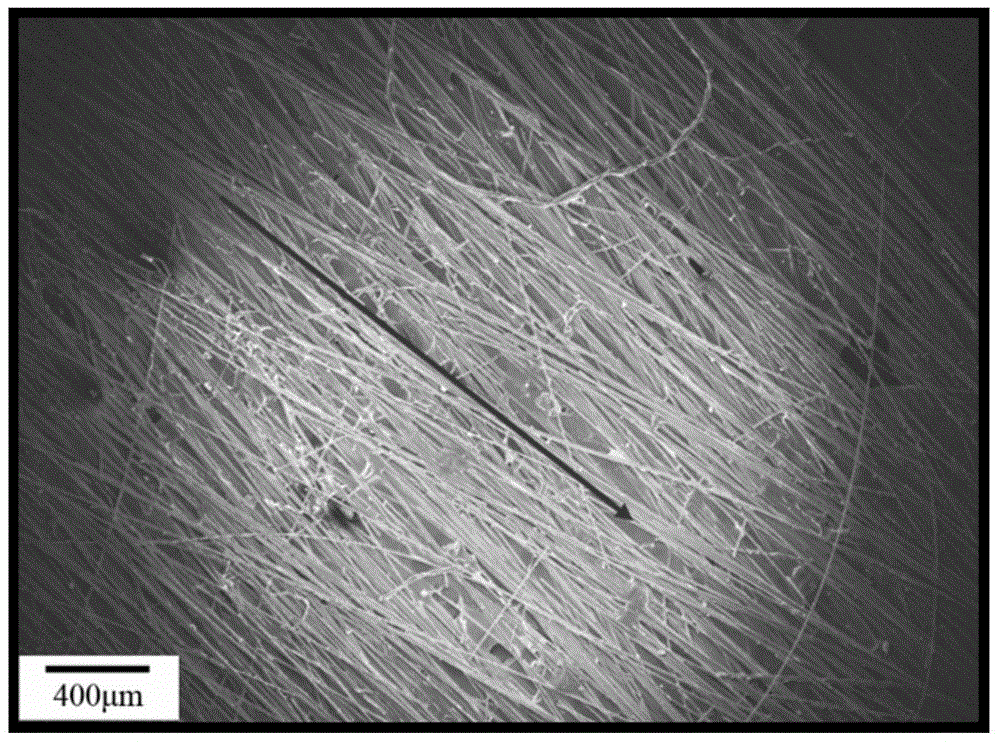
:本發(fā)明屬于纖維織物材料領域,特別涉及一種短切纖維取向氈的制備方法。
背景技術::短切纖維增強復合材料不僅具有一般纖維增強復合材料的優(yōu)點,如抗腐蝕、耐疲勞、高比強度和比模量、較好的熱穩(wěn)定性以及可設計性等特點,同時具有加工工藝簡單,生產(chǎn)成本較低等優(yōu)點,已經(jīng)越來越受到工業(yè)界及學術界的廣泛關注。而短切纖維增強復合材料的性能與纖維種類、、纖維長度、纖維含量、纖維界面結合及纖維取向狀態(tài)等因素有關。對于某一特定短切纖維增強復合材料,其力學性能主要取決于短切纖維的取向狀態(tài)及含量。即沿著纖維取向方向,短切纖維增強復合材料具有較高的強度及模量等力學性能。因此,如何制備短切纖維取向氈成為獲得高性能的短切纖維增強復合材料的關鍵。近年來,國內外研究人員對短切纖維取向氈制備技術進行了大量研究。V.Timbrell等(JournalofAppliedPhysics,1972,43(11))利用磁場方法,將纖維置于強磁場中,利用磁矩力的作用驅動短纖維沿磁場力的方向進行一定的取向排列,獲得一定取向度的短切纖維取向氈,但這種方法其取向裝置復雜,且要求纖維具有導磁性,限制了可取向纖維的種類。Vyakarnam等(U.S.Patent5846356)利用電場法制備短纖維取向氈,其取向原理與磁場法類此,該方法的取向裝置復雜,同樣限制纖維種類,要求纖維有一定的導電性,同時生產(chǎn)成本較高。流場法(U.S.Patent3617437;SAEInternational,Seattle,Washington,USA,2009;PolymerEngineering&Science,1975,15(7))是利用將短切纖維分散在甘油等具有較大粘度的有機溶劑中,通過一定的漸縮裝置產(chǎn)生收縮流動,在拉伸力和速度梯度力的作用下,使纖維在介質中取向排列獲得短切纖維取向氈。但目前利用流場法制備短切纖維取向氈的制備技術中其分散介質均采用具有較大粘度的有機溶劑,造成環(huán)境的二次污染;同時該制備技術需要完全除去纖維表面的有機溶劑,并添加一定量的粘結劑,生產(chǎn)設備較復雜,生產(chǎn)效率較低,獲得的短切纖維取向氈中的短切纖維取向程度較低。因此,急需開發(fā)一種短纖維取向度高、環(huán)保、高效的短纖維取向氈的制備方法。
技術實現(xiàn)要素::本發(fā)明的目的在于提供一種短切纖維取向氈的制備方法,以水為主分散介質和甲基纖維素為助分散介質,解決現(xiàn)有技術中存在的有機溶劑分散介質對環(huán)境污染的問題,同時通過特定的制備工藝和裝置,進一步解決現(xiàn)有技術獲得短切纖維取向氈中短切纖維的取向程度較低、其取向裝置復雜且生產(chǎn)效率低等問題。本發(fā)明具體技術內容如下:一種短切纖維取向氈的制備方法中,以水為主分散介質,取代現(xiàn)有技術中的有機溶劑分散介質,并以甲基纖維素為助分散介質,將短切纖維添加于分散介質中,經(jīng)過攪拌分散制成分散均勻的短切纖維懸浮液;將獲得的分散均勻的短切纖維懸浮液通過漸縮取向噴頭,利用漸縮流體使短切纖維取向,并通過分離工序與干燥工序制得短切纖維取向氈。所述一種短切纖維取向氈的制備過程中,所述短切纖維包括碳纖維、玻璃纖維、聚酰亞胺纖維、芳綸纖維、聚苯并咪唑纖維、聚對苯撐苯并二噁唑纖維、超高分子量纖維、尼龍纖維一種或多種,長度為3-12mm。所述一種短切纖維取向氈的制備方法中,制備過程如下:1)纖維分散:將短切纖維、甲基纖維素和水放入攪拌槽中均勻攪拌,攪拌速度為500-1000r/min,攪拌時間為20-60min,使短切纖維呈均勻單絲狀分布,得到短切纖維懸浮液;其中短切纖維重量含量是水重量的0.1%-0.8%,甲基纖維素與水的體積相比的加入量為6g/L-15g/L,以確保短切纖維懸浮液粘度在0.5-15Pa.s范圍內,通過漸縮取向噴頭時形成足夠的拉伸及剪切作用,使短切纖維懸浮液中短切纖維沿著流體流動方向取向排列,氣粘度測試方法采用采用美國博勒飛DV-III旋轉粘度儀進行測量,轉子為21號轉子,扭矩控制在75-80%,測試溫度為30℃;短切纖維懸浮液含氣率控制在4%-10%;2)纖維取向:將均勻分散的短切纖維懸浮液通過空氣壓縮機壓入或箱泵送入漸縮取向噴頭,漸縮取向噴頭長度為10-50cm,流道夾角為10-40°,噴嘴狹縫寬度為0.5-2mm,利用漸縮取向噴頭使短切纖維取向,并不斷送入連續(xù)運行的傳送網(wǎng)帶獲得濕態(tài)的短切纖維取向氈;其中空氣壓縮機提供壓力為0.05-0.5MPa,傳送網(wǎng)帶傳送速度8m/min-15m/min。3)分離工序:分離工序:濕態(tài)的纖維取向氈被傳送網(wǎng)帶送入真空抽吸箱,真空度為-0.05至-0.1MPa,真空分離時間為3-20min,除去多余的水分及甲基纖維素后,被送入鼓風干燥箱進行烘干。4)烘干工序:采用鼓風干燥箱熱風烘干,干燥箱溫度為100-200℃,烘干時間為30-120min,從干燥箱取出后得到厚度為0.08-0.3mm的短切纖維取向氈制品。發(fā)明效果本發(fā)明效果:(1)以水為主分散介質和甲基纖維素為助分散介質,取代現(xiàn)有技術中的有機溶劑分散介質,解決現(xiàn)有技術中有機溶劑造成環(huán)境污染,危害生產(chǎn)工人身體健康等問題;(2)本發(fā)明助分散介質甲基纖維素即為短切纖維取向氈粘結劑,避免完全除去有機溶劑后繼續(xù)添加粘結劑的步驟,本發(fā)明具有制備工藝簡單,所制得的短切纖維取向氈取向程度較高等優(yōu)點。本發(fā)明的短切纖維取向氈可顯著提高環(huán)氧樹脂等基體的力學性能,其中拉伸強度提高程度可達100%以上,拉伸模量提高程度可達300%以上,彎曲強度提高程度可達350%以上,彎曲模量提高程度可達10倍以上。附圖說明圖1是本發(fā)明一種短切纖維取向氈的制備方法制得的短切纖維取向氈;圖2是本發(fā)明一種短切纖維取向氈的制備方法制得的短切纖維取向氈掃描電鏡表征圖;圖3是本發(fā)明一種短切纖維取向氈的制備方法制得的短切纖維取向氈取向角度分布統(tǒng)計圖;圖4是本發(fā)明一種短切碳纖維取向氈增強環(huán)氧樹脂力學性能表征;純環(huán)氧樹脂(Epoxy),18wt%短切纖維無歸氈增強環(huán)氧樹脂復合材料(R-SCFs),18wt%短切纖維取向氈增強環(huán)氧樹脂復合材料(A-SCFs)拉伸(a)及(b)彎曲性能。具體實施方式:通過以下實施例對本發(fā)明的實施方案進行詳細說明,本實施例中所有粘度均采用美國博勒飛DV-III旋轉粘度儀進行測量,轉子為21號轉子,扭矩在75-80%,測試溫度為30℃;本實施例中厚度均采用廣州標際包裝設備有限公司GH-01數(shù)字測厚儀進行測量;本實施例中拉伸強度均采用英國INSTRON1121萬能材料試驗機進行測量,但本發(fā)明不限于以下實施例。實施例1:1)纖維分散:將短切纖維、甲基纖維素和水放入攪拌槽中均勻攪拌,攪拌速度為600r/min,時間30min,短切纖維呈均勻單絲狀分布。其中纖維為短切碳纖維,長度為4mm,含量(重量百分比)為0.1%,甲基纖維素加入量為13g/L,實際測量懸浮液粘度為8.539Pa.s,懸浮液含氣率為4%。2)纖維取向:將1)中均勻分散的短切纖維懸浮液通過空氣壓縮機壓入漸縮取向噴頭,取向噴頭長度為10cm,流道夾角為30°,取向噴頭的噴嘴寬度為1.0mm,利用漸縮取向噴頭使短纖維取向,并不斷送入連續(xù)運行的傳送網(wǎng)帶獲得分布均勻的纖維取向濕氈。其中空氣壓縮機提供壓力為0.12MPa,傳送網(wǎng)帶傳送速度8m/min。3)分離工序:纖維取向濕氈被傳送網(wǎng)帶送入真空抽吸箱,真空抽吸箱真空度為-0.06Mpa,真空分離時間為10min,除去多余的水分及分散劑后,濕氈被送入鼓風干燥箱進行烘干。4)烘干卷曲:采用鼓風干燥箱熱風烘干,干燥箱溫度為100℃,干燥時間為120min,從干燥箱中取出并獲得短切纖維取向氈。對所制得的短纖維取向氈進行表征,其取向程度為82.5%沿著纖維長度方向±15°范圍內,厚度為0.145mm,拉伸強度為45Mpa,比表面積質量為20g/mm2,分散劑含量為10wt%。利用所制得的短切碳纖維取向氈增強環(huán)氧樹脂復合材料,并對其力學性能進行表征,表征結果如圖4所示,結果顯示,短切纖維取向氈可顯著提高其基體的力學性能。實施例2:1)纖維分散:將短切纖維、甲基纖維素和水放入攪拌槽中均勻攪拌,攪拌速度為1000r/min,時間20min,纖維呈均勻單絲狀分布。其中纖維為短切玻璃纖維,長度為3mm,含量(重量百分比)為0.8%,甲基纖維素加入量為8g/L,實際測量懸浮液粘度為1.056Pa.s,懸浮液含氣率為8%。2)纖維取向:將1)中均勻分散的短切纖維懸浮液通過空氣壓縮機壓入漸縮取向噴頭,取向噴頭長度為10cm,流道夾角為40°,取向噴頭的噴嘴寬度為0.5mm,利用漸縮取向噴頭使短纖維取向,并不斷送入連續(xù)運行的傳送網(wǎng)帶獲得分布均勻的纖維取向濕氈。其中空氣壓縮機提供壓力為0.10MPa,傳送網(wǎng)帶傳送速度10m/min。3)分離工序:纖維取向濕氈被傳送網(wǎng)帶送入真空抽吸箱,真空抽吸箱真空度為-0.08Mpa,真空分離時間為8min,除去多余的水分及分散劑后,濕氈被送入鼓風干燥箱進行烘干。4)烘干卷曲:采用鼓風干燥箱熱風烘干,干燥箱溫度為150℃,干燥時間為50min,從干燥箱中取出并獲得短切纖維取向氈。對所制得的短纖維取向氈進行表征,其取向程度為89.5%沿纖維長度方向±15°范圍內,厚度為0.104mm,拉伸強度為35Mpa,比表面積質量為22g/mm2,其中分散含量為12wt%。實施例3:1)纖維分散:將短切纖維、甲基纖維素和水放入攪拌槽中均勻攪拌,攪拌速度為500r/min,時間60min,纖維呈均勻單絲狀分布。其中纖維為短切聚酰亞胺纖維,長度為6mm,含量(重量百分比)為0.2%,甲基纖維素加入量為6g/L,實際測量懸浮液粘度為0.591Pa.s,懸浮液含氣率為9%。2)纖維取向:將1)中均勻分散的短切纖維懸浮液通過空氣壓縮機壓入漸縮取向噴頭,取向噴頭長度為25cm,流道夾角為20°,取向噴頭的噴嘴寬度為1.5mm,利用漸縮取向噴頭使短纖維取向,并不斷送入連續(xù)運行的傳送網(wǎng)帶獲得分布均勻的纖維取向濕氈。其中空氣壓縮機提供壓力為0.20MPa,傳送網(wǎng)帶傳送速度13m/min。3)分離工序:纖維取向濕氈被傳送網(wǎng)帶送入真空抽吸箱,真空抽吸箱真空度為-0.09Mpa,真空分離時間為3min,除去多余的水分及分散劑后,濕氈被送入鼓風干燥箱進行烘干。4)烘干卷曲:采用鼓風干燥箱熱風烘干,干燥箱溫度為180℃,干燥時間為40min,從干燥箱中取出并獲得短切纖維取向氈。對所制得的短纖維取向氈進行表征,其取向程度為85.3%沿纖維長度方向±15°范圍內,厚度為0.203mm,拉伸強度為50Mpa,比表面積質量為25g/mm2,其中分散含量為20wt%。實施例4:1)纖維分散:將短切纖維、甲基纖維素和水放入攪拌槽中均勻攪拌,攪拌速度為1000r/min,時間25min,纖維呈均勻單絲狀分布。其中纖維為芳綸纖維,長度為12mm,含量(重量百分比)為0.1%,甲基纖維素加入量為15g/L,實際測量懸浮液粘度為14.8Pa.s,懸浮液含氣率為10%。2)纖維取向:將1)中均勻分散的短切纖維懸浮液通過空氣壓縮機壓入漸縮取向噴頭,取向噴頭長度為50cm,流道夾角為15°,取向噴頭的噴嘴寬度為2.0mm,利用漸縮取向噴頭使短纖維取向,并不斷送入連續(xù)運行的傳送網(wǎng)帶獲得分布均勻的纖維取向濕氈。其中空氣壓縮機提供壓力為0.50MPa,傳送網(wǎng)帶傳送速度15m/min。3)分離工序:纖維取向濕氈被傳送網(wǎng)帶送入真空抽吸箱,真空抽吸箱真空度為-0.10Mpa,真空分離時間為10min,除去多余的水分及分散劑后,濕氈被送入鼓風干燥箱進行烘干。4)烘干卷曲:采用鼓風干燥箱熱風烘干,干燥箱溫度為200℃,干燥時間為30min,從干燥箱中取出并獲得短切纖維取向氈。對所制得的短纖維取向氈進行表征,其取向程度為80.6%沿纖維長度方向±15°范圍內,厚度為0.136mm,拉伸強度為40Mpa,比表面積質量為22g/mm2,其中分散含量為25%。實施例5:1)纖維分散:將短切纖維、甲基纖維素和水放入攪拌槽中均勻攪拌,攪拌速度為800r/min,時間25min,纖維呈均勻單絲狀分布。其中纖維為短切尼龍纖維和短切聚苯并咪唑纖維兩種混合纖維,重量比為1:1,長度為4mm,含量(重量百分比)為0.2%,甲基纖維素加入量為10g/L,實際測量懸浮液粘度為2.5Pa.s,懸浮液含氣率為4%。2)纖維取向:將1)中均勻分散的短切纖維懸浮液通過空氣壓縮機壓入漸縮取向噴頭,取向噴頭長度為10cm,流道夾角為40°,取向噴頭的噴嘴寬度為1.0mm,利用漸縮取向噴頭使短纖維取向,并不斷送入連續(xù)運行的傳送網(wǎng)帶獲得分布均勻的纖維取向濕氈。其中空氣壓縮機提供壓力為0.2MPa,傳送網(wǎng)帶傳送速度8m/min。3)分離工序:纖維取向濕氈被傳送網(wǎng)帶送入真空抽吸箱,真空抽吸箱真空度為-0.08Mpa,真空分離時間為10min,除去多余的水分及分散劑后,濕氈被送入鼓風干燥箱進行烘干。4)烘干卷曲:采用鼓風干燥箱熱風烘干,干燥箱溫度為200℃,干燥時間為30min,從干燥箱中取出并獲得短切纖維取向氈。對所制得的短纖維取向氈進行表征,其取向程度為85%沿纖維長度方向±15°范圍內,厚度為0.205mm,拉伸強度為35Mpa,比表面積質量為26g/mm2,其中分散含量為8%。