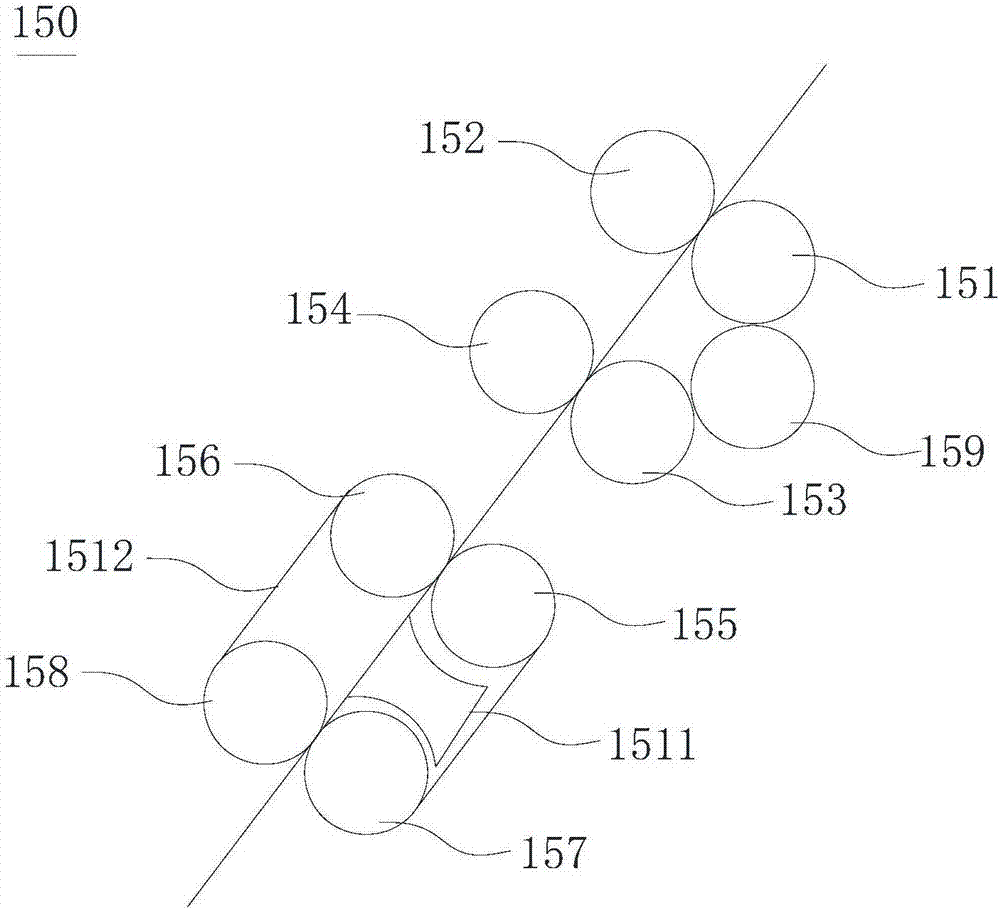
本發(fā)明涉及紡織
技術(shù)領(lǐng)域:
,特別是涉及一種聚酰亞胺纖維與竹纖維混紡紗線及加工方法、系統(tǒng)及應(yīng)用。
背景技術(shù):
:竹纖維是從自然生長的竹子中提取出的纖維素纖維,繼棉、麻、毛、絲后的第五大天然纖維。竹原纖維具有良好的透氣性、瞬間吸水性、較強(qiáng)的耐磨性和良好的染色性等特性,具有天然抗菌、抑菌、除螨、防臭和抗紫外線功能。然而竹纖維的濕斷裂伸長率較大,濕斷裂強(qiáng)度較低,導(dǎo)致竹纖維不耐洗、洗后尺寸不穩(wěn)定的問題。技術(shù)實現(xiàn)要素:基于此,有必要提供一種具有抗菌作用,且耐洗的聚酰亞胺纖維與竹纖維混紡紗線及加工方法、系統(tǒng)及應(yīng)用。一種聚酰亞胺纖維與竹纖維混紡紗線加工方法,包括以下步驟:將聚酰亞胺纖維和竹纖維分別采用清梳聯(lián)技術(shù)進(jìn)行開松和梳棉處理,然后分別進(jìn)行預(yù)并處理,得到聚酰亞胺條子和竹條子;將所述聚酰亞胺條子和所述竹條子進(jìn)行混并處理,然后進(jìn)行粗紗和細(xì)紗處理,得到聚酰亞胺纖維與竹纖維混紡紗線。上述聚酰亞胺纖維與竹纖維混紡紗線加工方法,將聚酰亞胺纖維和竹纖維采用清梳聯(lián)技術(shù)進(jìn)行開松和梳棉,并分別預(yù)并制成聚酰亞胺條子和竹條子混并合,減少了纖維損傷,提高了成紗質(zhì)量,然后通過粗紗和細(xì)紗處理,而且得到的聚酰亞胺纖維與竹纖維混紡紗線結(jié)合了兩者的優(yōu)點,避免了竹纖維易脆、不耐洗的問題,不僅抗菌性良好,且耐洗性能佳。在其中一個實施例中,所述聚酰亞胺纖維和所述竹纖維的旦數(shù)均為1~3d;所述聚酰亞胺纖維和所述竹纖維的長度均為30~40mm。在其中一個實施例中,所述混并處理采用三道并道處理。在其中一個實施例中,所述細(xì)紗處理為緊密紡細(xì)紗處理。在其中一個實施例中,在所述混并處理中,所述聚酰亞胺條子和所述竹條子的混紡比為20%~30%:70%~80%。上述聚酰亞胺纖維與竹纖維混紡紗線加工方法得到的聚酰亞胺纖維與竹纖維混紡紗線。上述聚酰亞胺纖維與竹纖維混紡紗線在制備織物中的應(yīng)用。在其中一個實施例中,所述聚酰亞胺纖維與竹纖維混紡紗線在所述織物中的質(zhì)量含量不小于30%。在其中一個實施例中,所述織物為襪子。一種聚酰亞胺纖維與竹纖維混紡紗線加工系統(tǒng),包括第一清梳聯(lián)合機(jī)、第一預(yù)并條機(jī)、第二清梳聯(lián)合機(jī)、第二預(yù)并條機(jī)、混并條機(jī)、粗紗機(jī)及細(xì)紗機(jī),所述第一清梳聯(lián)合機(jī)和所述第一預(yù)并條機(jī)相鄰設(shè)置且用于處理聚酰亞胺纖維,所述第二清梳聯(lián)合機(jī)和所述第二預(yù)并條機(jī)相鄰設(shè)置且用于處理竹纖維,所述混并條機(jī)與所述第一預(yù)并條機(jī)和所述第二預(yù)并條機(jī)分別相鄰設(shè)置,所述混并條機(jī)、所述粗紗機(jī)和所述細(xì)紗機(jī)依次相鄰設(shè)置。附圖說明圖1為一實施方式的聚酰亞胺纖維與竹纖維混紡紗線加工系統(tǒng)的結(jié)構(gòu)圖;圖2為圖1所示聚酰亞胺纖維與竹纖維混紡紗線加工系統(tǒng)的細(xì)紗機(jī)的結(jié)構(gòu)圖。具體實施方式為了便于理解本發(fā)明,下面將參照相關(guān)附圖對本發(fā)明進(jìn)行更全面的描述。附圖中給出了本發(fā)明的較佳實施例。但是,本發(fā)明可以以許多不同的形式來實現(xiàn),并不限于本文所描述的實施例。相反地,提供這些實施例的目的是使對本發(fā)明的公開內(nèi)容的理解更加透徹全面。除非另有定義,本文所使用的所有的技術(shù)和科學(xué)術(shù)語與屬于本發(fā)明的
技術(shù)領(lǐng)域:
的技術(shù)人員通常理解的含義相同。本文中在本發(fā)明的說明書中所使用的術(shù)語只是為了描述具體的實施例的目的,不是旨在于限制本發(fā)明。本文所使用的術(shù)語“和/或”包括一個或多個相關(guān)的所列項目的任意的和所有的組合。參照圖1,一實施方式的聚酰亞胺纖維與竹纖維混紡紗線加工系統(tǒng)100,包括第一清梳聯(lián)合機(jī)111、第一預(yù)并條機(jī)121、第二清梳聯(lián)合機(jī)112、第二預(yù)并條機(jī)122、混并條機(jī)130、粗紗機(jī)140及細(xì)紗機(jī)150。第一清梳聯(lián)合機(jī)111和第一預(yù)并條機(jī)121相鄰設(shè)置且用于處理聚酰亞胺纖維。第二清梳聯(lián)合機(jī)112和第二預(yù)并條機(jī)122相鄰設(shè)置且用于處理竹纖維?;觳l機(jī)130與第一預(yù)并條機(jī)121和第二預(yù)并條機(jī)122分別相鄰設(shè)置?;觳l機(jī)130、粗紗機(jī)140和細(xì)紗機(jī)150依次相鄰設(shè)置。細(xì)紗機(jī)150為緊密紡細(xì)紗機(jī)。上述聚酰亞胺纖維與竹纖維混紡紗線加工系統(tǒng)100,通過第一清梳聯(lián)合機(jī)111和第二清梳聯(lián)合機(jī)112分別對聚酰亞胺纖維和竹纖維采用清梳聯(lián)技術(shù)進(jìn)行開松和梳棉,然后分別通過第一預(yù)并條機(jī)121和第二預(yù)并條機(jī)122分別預(yù)并制成聚酰亞胺條子和竹條子。然后在混并條機(jī)130中進(jìn)行混并,并通過粗紗機(jī)140和細(xì)紗機(jī)150分別進(jìn)行粗紗處理及緊密紡細(xì)紗處理,減少了纖維損傷,提高了成紗質(zhì)量,而且得到的聚酰亞胺纖維與竹纖維混紡紗線結(jié)合了兩者的優(yōu)點,避免了竹纖維易脆、不耐洗的問題,不僅抗菌性良好,且耐洗性能佳。此外,上述聚酰亞胺纖維與竹纖維混紡紗線還具有親膚、保暖、遠(yuǎn)紅外能量特性及阻燃作用。在其中一個實施例中,第一清梳聯(lián)合機(jī)111及第二清梳聯(lián)合機(jī)112均包括依次設(shè)置的開棉機(jī)(圖未示)、混棉機(jī)(圖未示)、清棉機(jī)(圖未示)及梳棉機(jī)(圖未示)。具體地,開棉機(jī)為單軸流開棉機(jī)。更具體地,開棉機(jī)為fa101a型單軸流開棉機(jī)。具體地,混棉機(jī)為多倉混棉機(jī),實現(xiàn)了多包取用,精細(xì)抓棉。更具體地,混棉機(jī)為fa028c型多倉混棉機(jī)。具體地,第一清梳聯(lián)合機(jī)111中的清棉機(jī)為單輥筒清棉機(jī)。更具體地,第一清梳聯(lián)合機(jī)111中的清棉機(jī)為fa111a-120型單輥筒清棉機(jī)。具體地,第二清梳聯(lián)合機(jī)112中的清棉機(jī)為三輥筒清棉機(jī)。更具體地,第二清梳聯(lián)合機(jī)112中的清棉機(jī)為fa109a-120型三輥筒清棉機(jī)。具體地,第一清梳聯(lián)合機(jī)111及第二清梳聯(lián)合機(jī)112中的梳棉機(jī)均為fa221d型梳棉機(jī)。進(jìn)一步地,第一清梳聯(lián)合機(jī)111及第二清梳聯(lián)合機(jī)112均還包括抓棉機(jī)。具體地,抓棉機(jī)為往復(fù)型抓棉機(jī)。更具體地,抓棉機(jī)為fa006d型往復(fù)型抓棉機(jī)。在其中一個實施例中,第一預(yù)并條機(jī)121和/或第二預(yù)并條機(jī)122為fa311預(yù)并條機(jī)。第一預(yù)并條機(jī)121和/或第二預(yù)并條機(jī)122的并合數(shù)為6。在其中一個實施例中,混并條機(jī)130的并條道數(shù)為三道。具體地,混并條機(jī)130為fa311混并條機(jī)。具體地,粗紗機(jī)140為fa491型粗紗機(jī)。參照圖2,在其中一個實施例中,細(xì)紗機(jī)150細(xì)紗機(jī)包括后羅拉151、與后羅拉151對應(yīng)的后羅拉上皮輥152、中羅拉153、與中羅拉153對應(yīng)的中羅拉上皮輥154、前羅拉155、與前羅拉155對應(yīng)的前羅拉上皮輥156、集束器1511、上皮圈1512、設(shè)于前羅拉155前面的集聚羅拉157及與集聚羅拉157對應(yīng)的集聚羅拉上皮輥158。集束器1511設(shè)于集聚羅拉157和前羅拉155之間且與集聚羅拉157和前羅拉155分別貼合,前羅拉155和集聚羅拉157通過齒輪傳動連接,上皮圈1512設(shè)于集聚上皮輥158和前羅拉上皮輥156上。更具體地,中羅拉153與后羅拉151之間設(shè)有摩擦輪159。摩擦輪159與中羅拉151和后羅拉153分別相切設(shè)置。摩擦輪159可將后羅拉151的轉(zhuǎn)動傳動給中羅拉153,從而使中羅拉153與后羅拉151同步轉(zhuǎn)動。更具體地,集聚羅拉157的表面設(shè)有波浪形齒紋。具體地,集聚羅拉157的直徑為25~30mm,集聚羅拉上皮輥156的直徑為21mm。具體地,集聚羅拉157與前羅拉155圓心之間的水平距離為21mm,集聚羅拉157與前羅拉155圓心的垂直距離為20mm。此時的紡紗質(zhì)量最佳。一實施方式的聚酰亞胺纖維與竹纖維混紡紗線加工方法,采用上述聚酰亞胺纖維與竹纖維混紡紗線加工系統(tǒng)100,包括步驟s1~s2。步驟s1:將聚酰亞胺纖維和竹纖維分別采用清梳聯(lián)技術(shù)進(jìn)行開松和梳棉處理,然后分別進(jìn)行預(yù)并處理,得到聚酰亞胺條子和竹條子。竹纖維具有抗菌抑菌、防臭保健性能,其吸濕透氣好,手感滑軟,富有絲質(zhì)感,染色吸收性強(qiáng),滲透性強(qiáng),不易褪色,但纖維強(qiáng)力較低且不穩(wěn)定,濕斷裂強(qiáng)度較低,濕斷裂伸長率卻較大,不耐洗。聚酰亞胺纖維是一種高性能纖維,其具有耐輻射性、耐高溫性、高強(qiáng)度等優(yōu)異綜合性能,在航空航天、環(huán)保放火等領(lǐng)域發(fā)揮重要作用。由于聚酰亞胺纖維和竹纖維性能相差較大,為了減少纖維損傷,發(fā)揮兩者的優(yōu)點,步驟s1將聚酰亞胺纖維和竹纖維分別預(yù)并制成聚酰亞胺條子和竹條子并合。清、梳加工流程是纖維開松和除雜的關(guān)鍵,在此過程中對于聚酰亞胺纖維和竹纖維極易造成損傷導(dǎo)致混紡紗無法成紗或者成紗質(zhì)量差,因此使用短流程、無成卷的清梳聯(lián)處理是十分關(guān)鍵的。而且步驟s1采用清梳聯(lián)技術(shù)將清花和梳棉步驟直接連接,取消了成卷步驟,省去了落卷、搬運和上卷等處理,減輕了工人的勞動強(qiáng)度,提高了勞動生產(chǎn)率,縮短了處理流程,實現(xiàn)了清梳紡紗生產(chǎn)的連續(xù)化、自動化。清花是清梳聯(lián)流程中的主要的開松機(jī)械,有較好、較細(xì)致的松解作用,合理控制梳針輥筒的速度,避免過度開松,造成纖維損傷。優(yōu)選地,梳針輥筒的速度為450~550rpm。更優(yōu)選地,梳針輥筒的速度為500rpm。梳棉是將開松后的纖維梳理成條,第一次梳棉處理和/或第二次梳棉處理時,應(yīng)該控制刺輥速度為600~900rpm,錫林速度為300~400rpm。優(yōu)選地,刺輥速度與錫林速度比為2~3:1。竹纖維包括天然竹纖維和竹漿纖維。優(yōu)選地,竹纖維為竹漿纖維,由于竹漿纖維的橫截面呈不規(guī)則圓形,橫截面內(nèi)布滿了大大小小的空洞,這種結(jié)構(gòu)大大提高了纖維的吸濕能力,使得制成的織物穿著不貼身、不帶濕、具有挺爽舒適感。在其中一個實施例中,聚酰亞胺纖維和竹纖維的旦數(shù)為1~3d;聚酰亞胺纖維和竹纖維的長度為30~40mm。聚酰亞胺纖維和竹纖維性能相差較大,為了減少纖維損傷,更好除雜,采用整齊度較好的聚酰亞胺纖維和竹纖維。優(yōu)選地,聚酰亞胺纖維的旦數(shù)為2d,竹纖維的旦數(shù)為1.5d;聚酰亞胺纖維和竹纖維的長度均為38mm。步驟s2:將聚酰亞胺條子和竹條子進(jìn)行混并處理,然后進(jìn)行粗紗和細(xì)紗處理,得到聚酰亞胺纖維與竹纖維混紡紗線。步驟s2采用條子混并,然后再進(jìn)行粗紗及細(xì)紗處理,得到的聚酰亞胺纖維與竹纖維混紡紗線結(jié)合了兩者的優(yōu)點,其不僅具有良好的抗菌性,而且其濕斷裂強(qiáng)度較高且濕斷裂伸長率較小,具有耐洗的優(yōu)點,避免了竹纖維易脆、不耐洗的問題。此外,上述聚酰亞胺纖維與竹纖維混紡紗線還具有親膚、保暖、遠(yuǎn)紅外能量特性及阻燃作用。其中一個實施例中,在混并處理中,聚酰亞胺條子和竹條子的混紡比為20%~30%:70%~80%。優(yōu)選地,聚酰亞胺條子和竹條子的混紡比為30%:70%。如此以竹纖維為主導(dǎo)作用,以穩(wěn)定成紗強(qiáng)力和條干,保持良好的吸濕透氣性和抗菌抑菌性,以聚酰亞胺纖維作為輔助原料,利用其高強(qiáng)度及阻燃性,得到具有親膚、保暖、抗菌、遠(yuǎn)紅外能量特性及阻燃作用的聚酰亞胺纖維與竹纖維混紡紗線。在其中一個實施例中,混并處理采用三道并道。具體地,第一道并條的輸出定量為18.68g/5m,牽伸倍數(shù)為7,并合數(shù)為6根,羅拉隔距為54×46。第二道并條的輸出定量為18.68g/5m,牽伸倍數(shù)為6,并合數(shù)為6根,羅拉隔距為54×46mm。第三道并條的輸出定量為18.68g/5m,牽伸倍數(shù)為8,并合數(shù)為6根,羅拉隔距為54×46mm。在其中一個實施例中,細(xì)紗處理為緊密紡細(xì)紗處理。采用緊密紡細(xì)紗處理相比傳統(tǒng)環(huán)錠紡細(xì)紗處理時纖維受到的預(yù)張力不均勻?qū)е乱讛嗔?,使得成紗?qiáng)力降低的問題,成紗強(qiáng)力提高了10%,斷頭率下降了40%,而且減少了毛羽,提高了紗光潔度,從而提高了成紗質(zhì)量。在其中一個實施例中,粗紗處理的條件為:羅拉隔距為34×47×38mm,粗紗定量為6g/10m,捻系數(shù)為90,錠速為700~750rpm,總牽伸倍數(shù)為7。在其中一個實施例中,細(xì)紗處理的條件為:羅拉隔距為30×47mm,錠速為10000~12000rpm,總牽伸倍數(shù)為26。在其中一個實施例中,聚酰亞胺纖維與竹纖維混紡紗線的紗線密度為12~16tex。優(yōu)選地,聚酰亞胺纖維與竹纖維混紡紗線的紗線密度為14tex。上述聚酰亞胺纖維與竹纖維混紡紗線加工方法,將聚酰亞胺纖維和竹纖維采用清梳聯(lián)技術(shù)進(jìn)行開松和梳棉,并分別預(yù)并制成聚酰亞胺條子和竹條子混并合,減少了纖維損傷,提高了成紗質(zhì)量,然后通過粗紗和細(xì)紗處理,而且得到的聚酰亞胺纖維與竹纖維混紡紗線結(jié)合了兩者的優(yōu)點,避免了竹纖維易脆、不耐洗的問題,不僅抗菌性良好,且耐洗性能佳。此外,上述聚酰亞胺纖維與竹纖維混紡紗線還具有親膚、保暖、遠(yuǎn)紅外能量特性及阻燃作用。此外還提供了上述聚酰亞胺纖維與竹纖維混紡紗線加工方法得到的聚酰亞胺纖維與竹纖維混紡紗線。此外還提供了上述聚酰亞胺纖維與竹纖維混紡紗線在制備織物中的應(yīng)用。在其中一個實施例中,聚酰亞胺纖維與竹纖維混紡紗線在織物中的質(zhì)量含量不小于30%。在其中一個實施例中,織物為襪子??梢岳斫猓谄渌麑嵤├?,織物也可為圍巾、服裝等。以下為具體實施例。實施例1使用聚酰亞胺纖維與竹纖維混紡紗線加工系統(tǒng)100,將聚酰亞胺纖維加入第一清梳聯(lián)合機(jī)111采用清梳聯(lián)技術(shù)進(jìn)行開松、混合、清花和梳棉處理,再進(jìn)入第一預(yù)并條機(jī)121進(jìn)行預(yù)并條處理,得到聚酰亞胺纖維條子;第一清梳聯(lián)合機(jī)111的梳針輥筒的速度為500rpm。第一清梳聯(lián)合機(jī)111的刺輥速度為700rpm,錫林速度為320rpm;將竹纖維加入第二清梳聯(lián)合機(jī)112采用清梳聯(lián)技術(shù)進(jìn)行開松、混合、清花和梳棉處理,再進(jìn)入第二預(yù)并條機(jī)122進(jìn)行預(yù)并條處理,得到竹條子。第二清梳聯(lián)合機(jī)112的梳針輥筒的速度為450rpm。第二清梳聯(lián)合機(jī)112的刺輥速度為600rpm,錫林速度為300rpm。將聚酰亞胺纖維條子和竹條子在混并條機(jī)130中進(jìn)行三道混并條處理,然后在粗紗機(jī)140中進(jìn)行粗紗處理,再在細(xì)紗機(jī)150中進(jìn)行細(xì)紗處理,得到聚酰亞胺纖維與竹纖維混紡紗線。其中,聚酰亞胺纖維條子和竹條子的混紡比為30%:70%。第一道并條的輸出定量為18.68g/5m,牽伸倍數(shù)為7,并合數(shù)為6根,羅拉隔距為54×46。第二道并條的輸出定量為18.68g/5m,牽伸倍數(shù)為6,并合數(shù)為6根,羅拉隔距為54×46mm。第三道并條的輸出定量為18.68g/5m,牽伸倍數(shù)為8,并合數(shù)為6根,羅拉隔距為54×46mm。粗紗處理的條件為:羅拉隔距為34×47×38mm,粗紗定量為6g/10m,捻系數(shù)為90,錠速為700~750rpm,總牽伸倍數(shù)為7。細(xì)紗處理的條件為:羅拉隔距為30×47mm,錠速為11000rpm,總牽伸倍數(shù)為26。將聚酰亞胺纖維與竹纖維混紡紗線與棉紗線紡織,得到聚酰亞胺纖維與竹纖維混紡紗線織物,且在織物中的質(zhì)量含量為30%。實施例2~3實施例2~3與實施例1基本相同,不同之處在于,在混并處理中,聚酰亞胺條子和竹條子的混紡比分別為20%:80%、25%:75%。對比例1將聚酰亞胺纖維和竹纖維配料,混合,經(jīng)過清花、梳棉、并條、粗紗及細(xì)紗,得到聚酰亞胺纖維與竹纖維混紡紗線。其中,聚酰亞胺纖維和竹纖維的混紡比為30%:70%。將實施例1~3及對比例1得到的聚酰亞胺纖維與竹纖維混紡紗線分別進(jìn)行抗菌測試、濕斷裂強(qiáng)度及濕斷裂伸長率測試、親膚性、保暖性、遠(yuǎn)紅外及阻燃性能測試。其中抗菌性能采用金黃色葡萄球菌和肺炎桿菌進(jìn)行測試,按aatcc100-2004《紡織品材料上耐細(xì)胞整理》標(biāo)準(zhǔn)執(zhí)行。其中抗菌測試的結(jié)果如表1所示;濕斷裂強(qiáng)度及濕斷裂伸長率測試的結(jié)果如表2所示。表1從表1可知,說明實施例1~3得到的紗線優(yōu)于對比例1,且抗菌率達(dá)到99.99%,相當(dāng)于銀離子纖維的抗菌效果,然而銀離子屬于重金屬離子,因此可以替代銀離子抗菌產(chǎn)品,避免重金屬污染以及人體接觸的危害,尤其適用于嬰幼童織物產(chǎn)品,避免細(xì)菌及重金屬污染的危害。表2組別/%原料竹纖維實施例1實施例2實施例3對比例1濕斷裂強(qiáng)度(cn/tex)1.52.22.12.11.4濕斷裂伸長率(%)28.124.324.924.929.0原料竹纖維的干斷裂強(qiáng)度為2.32cn/tex,干斷裂伸長率為23.9%。從表2可知,說明實施例1~3得到的紗線優(yōu)于對比例1,且接近原料竹纖維的干斷裂強(qiáng)度和干斷裂伸長率,因此其洗后穩(wěn)定性提高,耐洗性能提升,其能夠任意水洗,其性能不受影響。親膚性測試:實施例1得到的聚酰亞胺纖維與竹纖維混紡紗線織物通過瑞士紡織科學(xué)研究院oeko-tex100嬰兒級生態(tài)信心紡織品的國際認(rèn)證,并達(dá)到a類嬰兒紡織品級別,可直接接觸嬰兒皮膚。且該織物產(chǎn)品通過了歐盟紡織品sgs皮膚敏感性測試,結(jié)論為最高級,符合制作貼身衣物的標(biāo)準(zhǔn)要求。此外,該織物產(chǎn)品不含有歐盟對紡織品161種高關(guān)注有害物質(zhì),檢測結(jié)果均為小于0.1%。遠(yuǎn)紅外能量特性:實施例1得到的聚酰亞胺纖維與竹纖維混紡紗線織物的法向發(fā)射率可達(dá)88%,可使微循環(huán)增加到114.23%。而微循環(huán)的加快,意味著人體血液循環(huán)加快,同時也提高了人體的免疫力。經(jīng)檢測,聚酰亞胺纖維與竹纖維混紡紗線的遠(yuǎn)紅外線波長范圍4~16um,與人體發(fā)射的波長相同,說明更容易被人體所吸收。保暖性測試:實施例1~3得到的聚酰亞胺纖維與竹纖維混紡紗線,常溫下導(dǎo)熱系數(shù)為0.028,僅比空氣導(dǎo)熱系數(shù)0.02略高。因此人體熱量極難通過纖維傳導(dǎo)到外界,使得其具有良好的保暖性能。而且該聚酰亞胺纖維與竹纖維混紡紗線具備智能調(diào)溫功能,10℃以下低溫環(huán)境中,纖維織物遠(yuǎn)紅外功能產(chǎn)生的升溫效應(yīng)可使體表快速升溫,而在20℃以上的環(huán)境下,升溫相對緩慢。并且在潮濕情況下及衣物沾濕時,也可有效保溫。此外聚酰亞胺纖維與竹纖維混紡紗線還具有原生的遠(yuǎn)紅外功能,在吸收人體和外界熱量后,可輻射可供人體吸收的遠(yuǎn)紅外能量,使得織物能夠蓄熱保暖。經(jīng)過對比檢測:發(fā)現(xiàn)119克重的實施例1~3得到的聚酰亞胺纖維與竹纖維混紡紗線,折算保溫率可達(dá)76.5%,優(yōu)于123克重羊絨絮片的保溫率70.1%,大大優(yōu)于極地科考服123克重滌綸絮片的保溫率64.9%。阻燃性能:實施例1~3得到的聚酰亞胺纖維與竹纖維混紡紗線的極限氧指數(shù)為38,屬于不燃材料的級別。以上所述實施例的各技術(shù)特征可以進(jìn)行任意的組合,為使描述簡潔,未對上述實施例中的各個技術(shù)特征所有可能的組合都進(jìn)行描述,然而,只要這些技術(shù)特征的組合不存在矛盾,都應(yīng)當(dāng)認(rèn)為是本說明書記載的范圍。以上所述實施例僅表達(dá)了本發(fā)明的幾種實施方式,其描述較為具體和詳細(xì),但并不能因此而理解為對發(fā)明專利范圍的限制。應(yīng)當(dāng)指出的是,對于本領(lǐng)域的普通技術(shù)人員來說,在不脫離本發(fā)明構(gòu)思的前提下,還可以做出若干變形和改進(jìn),這些都屬于本發(fā)明的保護(hù)范圍。因此,本發(fā)明專利的保護(hù)范圍應(yīng)以所附權(quán)利要求為準(zhǔn)。當(dāng)前第1頁12