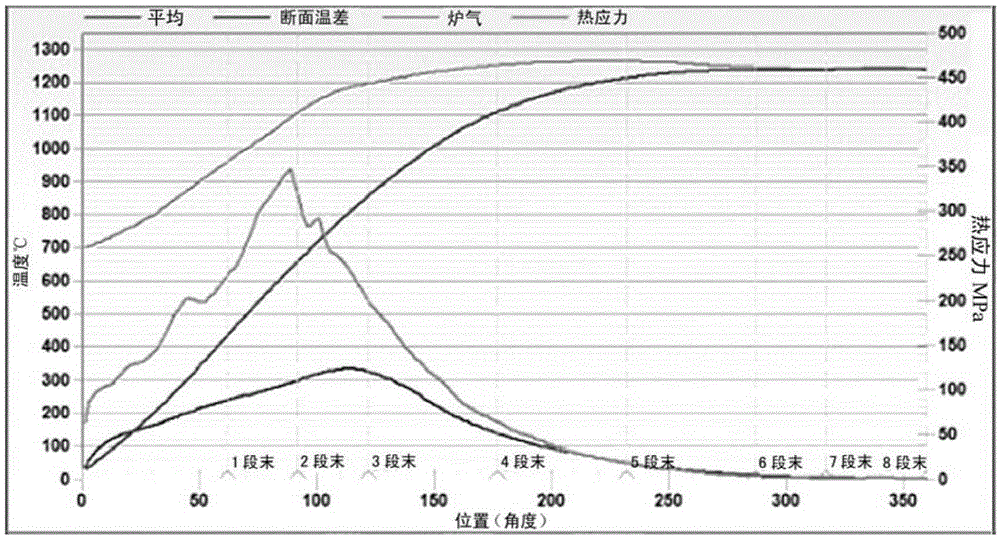
本發(fā)明屬于冶金領(lǐng)域,尤其涉及一種用于金屬熱處理的環(huán)形加熱爐的加熱工藝及控制方法。
背景技術(shù):
:鋼在加熱過程,進(jìn)入奧氏體組織之前,若加熱速度太快時(shí),鋼坯內(nèi)外溫度不均勻,會產(chǎn)生熱應(yīng)力,當(dāng)應(yīng)力難以松弛,且拉應(yīng)力較大時(shí),就可能導(dǎo)致鋼坯開裂。尤其是高合金鋼,熱導(dǎo)率小,導(dǎo)熱性差,熱應(yīng)力相對較大。因此,高合金鋼在低溫加熱階段,加熱速度應(yīng)取較小值。開始奧氏體轉(zhuǎn)變后,雖然會因相變而出現(xiàn)組織應(yīng)力,但這種應(yīng)力由于奧氏體為軟韌相,且由于鋼材塑性變好,因而可松弛應(yīng)力,所以這階段的加熱速度可以快些。事實(shí)上,鋼坯在高溫加熱階段,在實(shí)際生產(chǎn)中難以采用較大升溫速度進(jìn)行加熱,一方面是因?yàn)楦邷囟螤t子散熱增大,另一個(gè)方面是,當(dāng)珠光體轉(zhuǎn)變?yōu)閵W氏體時(shí),需要吸收相變潛熱,從而影響升溫速度。尤其對于環(huán)形加熱爐而言,管坯放置在爐底轉(zhuǎn)盤上,采用上部單側(cè)加熱,管坯單面受熱,同時(shí)受到相鄰管坯和爐底的影響,使得管坯溫度的均勻性不好,這不僅影響到管坯軋制過程的鋼管尺寸精度,還容易導(dǎo)致鋼管內(nèi)外表面出現(xiàn)裂紋等質(zhì)量缺陷。因此,利用環(huán)形爐進(jìn)行高合金鋼管坯加熱時(shí),合理的加熱工藝非常重要,一般的工藝控制思想是,降低其在低溫加熱過程的升溫速率,增加在爐時(shí)間,以確保管坯溫度的均勻性。但是一直以來,因?yàn)槿鄙儆?jì)算手段,高合金鋼的加熱工藝制定還是以生產(chǎn)經(jīng)驗(yàn)為主,往往造成不必要的能源浪費(fèi)。授權(quán)公告日為2011年7月20日,授權(quán)公告號為CN101775475B的中國發(fā)明專利,公開了“一種熱軋管坯的加熱工藝”,針對控制段的脈沖燒嘴,按照設(shè)定的換向周期和換向間隔依次循環(huán)燃燒,通過合理設(shè)置各控制段內(nèi)外側(cè)的爐溫,控制出爐熱管坯的頭部與尾部溫差范圍,使進(jìn)入連軋機(jī)毛管的頭尾溫度較為均勻,為連軋機(jī)的軋制提供更好的條件。該技術(shù)方案主要涉及爐溫的燃燒控制,并給出各控制段工藝爐溫范圍,但不涉及加熱工藝的爐溫、時(shí)間等具體信息的制定規(guī)則。授權(quán)公告日為1998年11月11日,授權(quán)公告號為CN1040662C的中國發(fā)明專利,公開了一種“鋼的最佳加熱速度加熱工藝”,該技術(shù)方案以最小能耗為目標(biāo),通過協(xié)調(diào)加熱溫度和加熱時(shí)間,給出鋼的最佳加熱速度。該方案主要適用于碳鋼,而且根據(jù)其方案所得到的給出爐溫,無法適用于環(huán)形加熱爐。公開日為2011年05月04日,公開號為CN102041372A的中國發(fā)明專利申請,公開了一種“低合金、碳素鋼大管坯在環(huán)形爐中的加熱工藝方法”,該技術(shù)方案通過快速升溫并在高溫段保留一段時(shí)間的加熱方式,提高管坯產(chǎn)能,使加熱溫度能夠更好適應(yīng)不同軋制節(jié)奏。該技術(shù)方案可適用于碳素鋼和低合金鋼,但不適用于高合金鋼。技術(shù)實(shí)現(xiàn)要素:本發(fā)明所要解決的技術(shù)問題是提供一種環(huán)形加熱爐加熱工藝優(yōu)化方法,其主要針對高合金鋼,以控制爐內(nèi)管坯的熱應(yīng)力和出爐溫度為目標(biāo),采用模型計(jì)算,確定管坯在加熱過程中,各控制段的工藝爐溫和工藝在爐時(shí)間。本技術(shù)方案通過合理設(shè)計(jì)管坯在環(huán)形加熱爐中的工藝爐溫和工藝在爐時(shí)間,能夠有效降低管坯在加熱過程中因熱應(yīng)力過高而產(chǎn)生表面裂紋的風(fēng)險(xiǎn),提高產(chǎn)品加熱質(zhì)量,同時(shí)有利于降低加熱爐排煙溫度,減少工序能耗。本發(fā)明的技術(shù)方案是:提供一種環(huán)形加熱爐加熱工藝優(yōu)化方法,其特征所述的工藝優(yōu)化方法包括下列步驟:步驟1、根據(jù)熱傳導(dǎo)偏微分方程和爐內(nèi)熱輻射總括系數(shù)方法,建立環(huán)形爐內(nèi)管坯溫度模型;根據(jù)管坯斷面熱膨脹的差異,建立熱應(yīng)力模型;步驟2、建立加熱工藝的調(diào)整流程和調(diào)整規(guī)則,調(diào)整流程指外環(huán)的工藝在爐時(shí)間調(diào)整和內(nèi)環(huán)的工藝溫度調(diào)整,調(diào)整規(guī)則指模型計(jì)算結(jié)果和加熱工藝調(diào)整細(xì)則的對應(yīng)關(guān)系;步驟3、針對給定加熱工藝,利用步驟1中的管坯溫度模型和熱應(yīng)力模型,計(jì)算對應(yīng)于加熱工藝不同時(shí)刻的管坯溫度和熱應(yīng)力值;步驟4、采用步驟3計(jì)算結(jié)果,判斷當(dāng)前加熱工藝狀態(tài),結(jié)合步驟2建立的加熱工藝調(diào)整流程和加熱工藝調(diào)整規(guī)則,通過迭代計(jì)算實(shí)現(xiàn)加熱工藝調(diào)整,最終輸出符合工藝要求的加熱工藝。其所述步驟1中的管坯溫度模型,忽略長度方向的傳熱,采用二維熱傳導(dǎo)方程,采用常規(guī)的差分解法,在管坯半徑方向和角度方向,迭代計(jì)算管坯的溫度分布。在所述步驟1中管坯溫度模型的表達(dá)形式如下:其中:λ,管坯熱導(dǎo)率,單位W/(m×K);c,管坯比熱,單位J/(kg×K);ρ,管坯密度,單位kg/(m3);T,管坯溫度,單位℃;r,表示管坯截面2維網(wǎng)格在半徑方向的坐標(biāo),r1,rM分別為網(wǎng)格的最小、最大 半徑;為了兼顧計(jì)算的穩(wěn)定性和精度,r1可以取一個(gè)大于0的極小值;θ,表示管坯截面2維網(wǎng)格在角度方向的坐標(biāo),θ1、θN分別為網(wǎng)格的最小、最大角度;所述的管坯表面對應(yīng)于不同角度θ,從加熱爐內(nèi)獲取的熱量,可以通過總括系數(shù)法獲得:其中:α(θ)為角度θ對應(yīng)的綜合輻射系數(shù),可以結(jié)合黑匣子試驗(yàn)或通過有限元模擬計(jì)算獲取;σ為Stefan-Boltzmann常數(shù),取值5.67W/(m2×K4);Tg(t)為對應(yīng)t時(shí)刻的工藝爐溫。具體的,所述的步驟1中的熱應(yīng)力模型可以采用如下公式計(jì)算:F=κ(T)×E(T)×ΔT其中,κ(T)為管坯線膨脹系數(shù),單位1E-6/K;E(T)為管坯彈性模量,MPa;ΔT為管坯不同節(jié)點(diǎn)之間溫差。具體的,在所述步驟2中,建立加熱工藝的調(diào)整流程和加熱工藝的調(diào)整規(guī)則如下:所述加熱工藝的調(diào)整流程包括內(nèi)、外兩個(gè)閉環(huán);其中,外環(huán)調(diào)節(jié)時(shí)間,內(nèi)環(huán)調(diào)節(jié)溫度,因此定義外環(huán)工藝為調(diào)時(shí)工藝,內(nèi)環(huán)工藝為調(diào)溫工藝;在首次進(jìn)行工藝調(diào)節(jié)時(shí),調(diào)時(shí)工藝和調(diào)溫工藝都和初始工藝一致;外環(huán)的時(shí)間調(diào)節(jié)是針對前一次的調(diào)時(shí)工藝進(jìn)行調(diào)節(jié),每次完成時(shí)間調(diào)節(jié)后,需采用調(diào)節(jié)后的調(diào)時(shí)工藝重置內(nèi)環(huán)的調(diào)溫工藝;同樣,內(nèi)環(huán)的溫度調(diào)節(jié)是針對前一次的調(diào)溫工藝進(jìn)行 調(diào)節(jié);所述加熱工藝的調(diào)整規(guī)則具體包括如下:①滿足條件FMax≥FAim,應(yīng)力段降溫;其中,F(xiàn)Max是對應(yīng)于當(dāng)前工藝計(jì)算得到的管坯斷面局部最大熱應(yīng)力,F(xiàn)Aim是加熱過程所允許的最大熱應(yīng)力;其中所述的應(yīng)力段,定義為超出目標(biāo)應(yīng)力的當(dāng)前控制段;②滿足條件Tave-TAim>ΔT1,溫度段降溫;其中,Tave是對應(yīng)于當(dāng)前工藝計(jì)算得到的管坯出爐平均溫度,TAim是工藝給出目標(biāo)出爐溫度,ΔT1是工藝允許最大出爐溫度偏差;溫度段定義為應(yīng)力段到出爐位置之間的所有控溫段,如果不存在應(yīng)力段,則所有的控溫段均為溫度段。③滿足條件Tave-TAim<-ΔT1,溫度段升溫;④滿足條件tcalcu-tAim>Δt,減少工藝在爐時(shí)間;其中,tcalcu是當(dāng)前工藝下,計(jì)算管坯平均溫度達(dá)到TAim后的在爐時(shí)間;tAim是工藝給出保溫時(shí)間;Δt是工藝允許的保溫時(shí)間偏差;⑤滿足條件tcalcu-tAim<-Δt,增加工藝在爐時(shí)間;⑥同時(shí)滿足如下條件,輸出調(diào)整后加熱工藝:進(jìn)一步的,在所述的步驟3中,所述的給定加熱工藝,是指當(dāng)前調(diào)整流程中的調(diào)溫工藝;在進(jìn)行管坯溫度和熱應(yīng)力計(jì)算時(shí),首先需要獲取相關(guān)計(jì)算參數(shù);所述的相關(guān)計(jì)算參數(shù)至少包括工藝溫度、工藝在爐時(shí)間、管坯尺寸、管坯比熱、管坯熱導(dǎo)率、管坯密度、管坯線膨脹系數(shù)、管坯彈性模量。進(jìn)一步的,在所述的步驟3中,將步驟1中建立的管坯溫度模型,采用有限差分方式,進(jìn)行迭代求解,可以獲取對應(yīng)于加熱工藝不同時(shí)刻的管坯溫度;然后,針對不同時(shí)刻的管坯溫度分布,獲取管坯內(nèi)部節(jié)點(diǎn)的局部溫差ΔT,再利用步驟1建立的熱應(yīng)力模型,獲取對應(yīng)于加熱工藝不同時(shí)刻的管坯斷面節(jié)點(diǎn)熱應(yīng)力,并通過比較得到局部最大熱應(yīng)力。進(jìn)一步的,在所述的步驟4中,首先,根據(jù)步驟3輸出的不同時(shí)間、不同位置下的管坯溫度和熱應(yīng)力,判斷計(jì)算值和工藝目標(biāo)值之間的關(guān)系,確定工藝調(diào)節(jié)過程中應(yīng)力段、溫度段所對應(yīng)的具體控制段;其次,根據(jù)步驟2建立的加熱工藝調(diào)整流程和加熱工藝調(diào)整規(guī)則,選擇合適的調(diào)節(jié)溫度和調(diào)節(jié)時(shí)間,實(shí)現(xiàn)工藝的優(yōu)化調(diào)整,并輸出符合工藝要求的加熱工藝。進(jìn)一步的,在所述的步驟4中,假設(shè)當(dāng)前加熱工藝以及對應(yīng)的計(jì)算結(jié)果,包含了如下信息:表示應(yīng)力段的工藝爐溫、表示溫度段的工藝爐溫、t工藝表示工藝在爐時(shí)間,Tstep表示溫度調(diào)節(jié)量,tstep表示時(shí)間調(diào)節(jié)量;則有,滿足步驟2定義調(diào)整規(guī)則①,下次迭代計(jì)算的工藝爐溫調(diào)整為:滿足步驟2定義調(diào)整規(guī)則②,下次迭代計(jì)算的工藝爐溫調(diào)整為:滿足步驟2定義調(diào)整規(guī)則③,下次迭代計(jì)算的工藝爐溫調(diào)整為:滿足步驟2定義調(diào)整規(guī)則④,下次迭代計(jì)算的工藝在爐時(shí)間調(diào)整為:t工藝=t工藝-tstep滿足步驟2定義調(diào)整規(guī)則⑤,下次迭代計(jì)算的工藝在爐時(shí)間調(diào)整為:t工藝=t工藝+tstep滿足步驟2定義調(diào)整規(guī)則⑥,輸出當(dāng)前調(diào)時(shí)工藝為最終優(yōu)化加熱工藝。本技術(shù)方案所述的加熱工藝優(yōu)化方法,以控制爐內(nèi)管坯的熱應(yīng)力和出爐溫度為目標(biāo),采用模型計(jì)算,確定管坯在加熱過程中,各控制段的工藝爐溫和工藝在爐時(shí)間。本技術(shù)方案所述的加熱工藝優(yōu)化方法,通過合理設(shè)計(jì)管坯在環(huán)形加熱爐中的工藝爐溫和工藝在爐時(shí)間,能夠有效降低管坯在加熱過程中因熱應(yīng)力過高而產(chǎn)生表面裂紋的風(fēng)險(xiǎn),提高產(chǎn)品加熱質(zhì)量,同時(shí)有利于降低加熱爐排煙溫度,減少工序能耗。與現(xiàn)有技術(shù)比較,本發(fā)明的優(yōu)點(diǎn)是:1.所述的工藝優(yōu)化方法主要針對高合金鋼,以控制爐內(nèi)管坯的熱應(yīng)力和出爐溫度為目標(biāo),采用管坯溫度模型和管坯熱應(yīng)力模型,確定管坯在加熱過程中,各控制段的工藝爐溫和工藝在爐時(shí)間;2.通過離線計(jì)算,實(shí)現(xiàn)工藝優(yōu)化,對計(jì)算時(shí)間沒有限制,因此溫度調(diào)節(jié)和時(shí)間調(diào)節(jié)均可取很小值;3.通過合理設(shè)計(jì)管坯在環(huán)形加熱爐中的工藝爐溫和工藝在爐時(shí)間,能夠有效降低管坯在加熱過程中因熱應(yīng)力過高而產(chǎn)生表面裂紋的風(fēng)險(xiǎn),提高產(chǎn)品加熱質(zhì)量,同時(shí)有利于降低加熱爐排煙溫度,減少工序能耗。附圖說明圖1是本發(fā)明的工藝優(yōu)化流程示意圖;圖2是本發(fā)明環(huán)形爐應(yīng)力段和溫度段的示意圖;圖3是本發(fā)明對應(yīng)于初始工藝的管坯溫度及熱應(yīng)力的示意圖;圖4是本發(fā)明對應(yīng)于調(diào)整完成后的加熱工藝示意圖。具體實(shí)施方式下面結(jié)合附圖和實(shí)施例對本發(fā)明做進(jìn)一步說明。本發(fā)明的技術(shù)方案提供了一種環(huán)形加熱爐加熱工藝優(yōu)化方法,其發(fā)明點(diǎn)在于所述的工藝優(yōu)化方法包括下列步驟:步驟1、根據(jù)熱傳導(dǎo)偏微分方程和爐內(nèi)熱輻射總括系數(shù)方法,建立環(huán)形爐內(nèi)管坯溫度模型;根據(jù)管坯斷面熱膨脹的差異,建立熱應(yīng)力模型;步驟2、建立加熱工藝的調(diào)整流程和調(diào)整規(guī)則,調(diào)整流程指外環(huán)的工藝在爐時(shí)間調(diào)整和內(nèi)環(huán)的工藝溫度調(diào)整,調(diào)整規(guī)則指模型計(jì)算結(jié)果和加熱工藝調(diào)整細(xì)則的對應(yīng)關(guān)系;步驟3、針對給定加熱工藝,利用步驟1中的管坯溫度模型和熱應(yīng)力模型,計(jì)算對應(yīng)于加熱工藝不同時(shí)刻的管坯溫度和熱應(yīng)力值;步驟4、采用步驟3計(jì)算結(jié)果,判斷當(dāng)前加熱工藝狀態(tài),結(jié)合步驟2建立的加熱工藝調(diào)整流程和加熱工藝調(diào)整規(guī)則,通過迭代計(jì)算實(shí)現(xiàn)加熱工藝調(diào)整,最終輸出符合工藝要求的加熱工藝。本技術(shù)方案的具體內(nèi)容為:根據(jù)步驟1,管坯溫度模型,忽略長度方向的傳熱,采用二維熱傳導(dǎo)方程,采用常規(guī)的差分解法,在管坯半徑方向和角度方向,迭代計(jì)算管坯的溫度分布。形式如下:其中:λ,管坯熱導(dǎo)率,單位W/(m×K);c,管坯比熱,單位J/(kg×K);ρ,管坯密度,單位kg/(m3);T,管坯溫度,單位℃;r,表示管坯截面2維網(wǎng)格在半徑方向的坐標(biāo),r1,rM分別為網(wǎng)格的最小、最大半徑;θ,表示管坯截面2維網(wǎng)格在角度方向的坐標(biāo),θ1、θN分別為網(wǎng)格的最小、最大角度。為了兼顧計(jì)算的穩(wěn)定性和精度,r1可以取一個(gè)大于0的極小值,管坯表面對應(yīng)于不同角度θ,從加熱爐內(nèi)獲取的熱量可以通過總括系數(shù)法計(jì)算:其中:α(θ)為角度θ對應(yīng)的綜合輻射系數(shù),可以結(jié)合黑匣子試驗(yàn)或通過有限元模擬計(jì)算獲??;σ為Stefan-Boltzmann常數(shù),取值5.67W/(m2×K4);Tg(t)為對應(yīng)t時(shí)刻的工藝爐溫。根據(jù)步驟1,熱應(yīng)力模型可以采用如下公式計(jì)算:F=κ(T)×E(T)×ΔT其中,κ(T)為管坯線膨脹系數(shù),單位1E-6/K;E(T)為管坯彈性模量,MPa;ΔT為管坯不同節(jié)點(diǎn)之間溫差。根據(jù)步驟2,建立加熱工藝的調(diào)整流程和調(diào)整規(guī)則如下:加熱工藝的調(diào)整流程包括內(nèi)、外兩個(gè)閉環(huán),外環(huán)調(diào)節(jié)時(shí)間,內(nèi)環(huán)調(diào)節(jié)溫度,因此定義外環(huán)工藝為調(diào)時(shí)工藝,內(nèi)環(huán)工藝為調(diào)溫工藝。具體流程可參考圖1中所示。在首次進(jìn)行工藝調(diào)節(jié)時(shí),調(diào)時(shí)工藝和調(diào)溫工藝都和初始工藝一致;外環(huán)的時(shí)間調(diào)節(jié)是針對前一次的調(diào)時(shí)工藝進(jìn)行調(diào)節(jié),每次完成時(shí)間調(diào)節(jié)后,需采用調(diào)節(jié)后的調(diào) 時(shí)工藝重置內(nèi)環(huán)的調(diào)溫工藝;同樣,內(nèi)環(huán)的溫度調(diào)節(jié)是針對前一次的調(diào)溫工藝進(jìn)行調(diào)節(jié)。加熱工藝的調(diào)整規(guī)則具體包括如下:①滿足條件FMax≥FAim,應(yīng)力段降溫。其中,F(xiàn)Max是對應(yīng)于當(dāng)前工藝計(jì)算得到的管坯斷面局部最大熱應(yīng)力,F(xiàn)Aim是加熱過程所允許的最大熱應(yīng)力;應(yīng)力段定義為超出目標(biāo)應(yīng)力的當(dāng)前控制段;②滿足條件Tave-TAim>ΔT1,溫度段降溫。其中,Tave是對應(yīng)于當(dāng)前工藝計(jì)算得到的管坯出爐平均溫度,TAim是工藝給出目標(biāo)出爐溫度,ΔT1是工藝允許最大出爐溫度偏差;溫度段定義為應(yīng)力段(不包含應(yīng)力段)到出爐位置之間的所有控溫段,如果不存在應(yīng)力段,則所有的控溫段均為溫度段。③滿足條件Tave-TAim<-ΔT1,溫度段升溫。④滿足條件tcalcu-tAim>Δt,減少工藝在爐時(shí)間。其中,tcalcu是當(dāng)前工藝下,計(jì)算管坯平均溫度達(dá)到TAim后的在爐時(shí)間;tAim是工藝給出保溫時(shí)間;Δt是工藝允許的保溫時(shí)間偏差。⑤滿足條件tcalcu-tAim<-Δt,增加工藝在爐時(shí)間。⑥同時(shí)滿足如下條件,輸出調(diào)整后加熱工藝:本技術(shù)方案中所述的應(yīng)力段和溫度段的具體劃分,可參考圖2中所示。該方法通過離線計(jì)算,實(shí)現(xiàn)工藝優(yōu)化,對計(jì)算時(shí)間沒有限制,因此溫度調(diào)節(jié)和時(shí)間調(diào)節(jié)均可取很小值,例如,溫度調(diào)節(jié)量采用1~10℃,時(shí)間調(diào)節(jié)量采用1~10min。根據(jù)步驟3,針對給定加熱工藝,利用步驟1模型,計(jì)算對應(yīng)于不同時(shí)刻的管坯溫度和熱應(yīng)力值。此處涉及的給定加熱工藝,具體來說,是指當(dāng)前調(diào)整流程中的調(diào)溫工藝。在進(jìn)行管坯溫度和熱應(yīng)力計(jì)算時(shí),首先需要獲取相關(guān)計(jì)算參數(shù),具體包括工藝溫度、工藝在爐時(shí)間、管坯尺寸、管坯比熱、管坯熱導(dǎo)率、管坯密度、管坯線膨脹系數(shù)、管坯彈性模量等信息。將步驟1建立的管坯溫度模型,采用有限差分方式,進(jìn)行迭代求解,可以獲取對應(yīng)于加熱工藝不同時(shí)刻的管坯溫度;然后,針對不同時(shí)刻的管坯溫度分布,獲取管坯內(nèi)部節(jié)點(diǎn)的局部溫差ΔT,再利用步驟1建立的熱應(yīng)力模型,獲取對應(yīng)于加熱工藝不同時(shí)刻的管坯斷面節(jié)點(diǎn)熱應(yīng)力,并通過比較得到局部最大熱應(yīng)力。根據(jù)步驟4,采用步驟3計(jì)算結(jié)果,判斷當(dāng)前加熱工藝狀態(tài),利用步驟2建立的流程和規(guī)則,通過迭代計(jì)算實(shí)現(xiàn)加熱工藝調(diào)整,最終輸出符合工藝要求的加熱工藝。具體來說,首先,根據(jù)步驟3輸出的不同時(shí)間、不同位置下的管坯溫度和熱應(yīng)力,判斷計(jì)算值和工藝目標(biāo)值之間的關(guān)系,確定工藝調(diào)節(jié)過程中應(yīng)力段、溫度段所對應(yīng)的具體控制段;其次,根據(jù)步驟2建立的調(diào)整流程和調(diào)整規(guī)則,選擇合適的調(diào)節(jié)溫度和調(diào)節(jié)時(shí)間,實(shí)現(xiàn)工藝的優(yōu)化調(diào)整,并輸出符合工藝要求的加熱工藝。不失一般性,假設(shè)當(dāng)前加熱工藝以及對應(yīng)的計(jì)算結(jié)果,包含了如下信息:表示應(yīng)力段的工藝爐溫、表示溫度段的工藝爐溫、t工藝表示工藝在爐時(shí)間,Tstep表示溫度調(diào)節(jié)量,tstep表示時(shí)間調(diào)節(jié)量。則有,滿足步驟2定義調(diào)整規(guī)則①,下次迭代計(jì)算的工藝爐溫調(diào)整為:滿足步驟2定義調(diào)整規(guī)則②,下次迭代計(jì)算的工藝爐溫調(diào)整為:滿足步驟2定義調(diào)整規(guī)則③,下次迭代計(jì)算的工藝爐溫調(diào)整為:滿足步驟2定義調(diào)整規(guī)則④,下次迭代計(jì)算的工藝在爐時(shí)間調(diào)整為:t工藝=t工藝-tstep滿足步驟2定義調(diào)整規(guī)則⑤,下次迭代計(jì)算的工藝在爐時(shí)間調(diào)整為:t工藝=t工藝+tstep滿足步驟2定義調(diào)整規(guī)則⑥,輸出當(dāng)前調(diào)時(shí)工藝為最終優(yōu)化加熱工藝。實(shí)施例:某環(huán)形加熱爐共分為爐尾段、預(yù)熱1段、預(yù)熱2段、加熱1段、加熱2段、加熱3段、均熱1段、均熱2段等8個(gè)物理段,除爐尾段外,其余7段均為控溫段,各段長度比例關(guān)系為60:30:30:55:55:55:35:35?,F(xiàn)有某合金鋼坯,直徑300mm,工藝要求管坯出爐目標(biāo)溫度為1220±10℃以內(nèi),均熱保溫時(shí)間30min,在低溫快速升溫過程的產(chǎn)生的斷面局部最大熱應(yīng)力低于300Mpa。初始工藝給定在爐加熱時(shí)間210min,各控制段對應(yīng)工藝爐溫見表1:表1初始加熱工藝表控制段預(yù)熱1預(yù)熱2加熱1加熱2加熱3均熱1均熱2工藝爐溫℃1050118012201260126012401240根據(jù)步驟1,管坯溫度模型,忽略長度方向的傳熱,采用二維熱傳導(dǎo)方程,采用常規(guī)的差分解法,在管坯半徑方向和角度方向,迭代計(jì)算管坯的溫度分布。圓坯的2維形式如下:管坯從加熱爐內(nèi)獲取的熱量可以通過總括系數(shù)法計(jì)算:在實(shí)施例中,管坯斷面角度方向θ取值[0,π],半徑方向r取值[0.001,150mm],2個(gè)維度均劃分網(wǎng)格節(jié)點(diǎn)數(shù)量N=5,初始溫度T0(r,θ)取值20;利用總括系數(shù)法計(jì)算管坯表面熱流時(shí),σ取值5.67W/(m2×K4),α(θ)沿不同角度的取值分別為0.3,0.45,0.75,0.85,0.90。管坯對應(yīng)材料參數(shù)λ、c、ρ見表2。根據(jù)步驟1,熱應(yīng)力模型采用如下公式計(jì)算:F=κ(T)×E(T)×ΔTΔT為管坯不同節(jié)點(diǎn)之間溫差,κ、E取值參考表2。表2管坯對應(yīng)物性參數(shù)溫度℃λcρκE025469774511.122310026481772212.121820027523769612.621230028557766713.120540028615763814.119850027703760814.51926002780875751518570026959754215.917880025871751916.717190027653752417.1140100028645746317.6132110029649739718124120030661733118.2116130031678726518.2113根據(jù)步驟2,建立加熱工藝的調(diào)整流程和調(diào)整規(guī)則。加熱工藝調(diào)整流程包括外環(huán)時(shí)間調(diào)節(jié)和內(nèi)環(huán)溫度調(diào)節(jié),具體流程參考圖1中所示。定義工藝在爐時(shí)間調(diào)整后的加熱工藝為調(diào)時(shí)工藝,工藝溫度調(diào)整后的加熱工藝為調(diào)溫工藝。在首次進(jìn)行工藝調(diào)節(jié)時(shí),調(diào)時(shí)工藝和調(diào)溫工藝都和初始工藝一致,在本實(shí)施例中,即采用表1所示初始工藝;在調(diào)整流程中,外環(huán)的調(diào)時(shí)工藝是在初始工藝的基礎(chǔ)上,對工藝在爐時(shí)間進(jìn)行迭代調(diào)整,后一次調(diào)整的初始值采用前一次的調(diào)整結(jié)果;內(nèi)環(huán)的調(diào)溫工藝的初值采用最新的調(diào)時(shí)工藝,然后在此基礎(chǔ)上進(jìn)行工藝溫度的迭代調(diào)整。本實(shí)施例中,不妨定義初始加熱工藝為Craft0,調(diào)時(shí)工藝用M(i)表示,調(diào)溫工藝用N(i)表示,i表示對應(yīng)工藝的第i次調(diào)整。則有如下關(guān)系:M(1)=Craft0;N(1)=M(1)N(2)=N(1)+溫度調(diào)節(jié)量N(i+1)=N(i)+溫度調(diào)節(jié)量……M(2)=M(1)+時(shí)間調(diào)節(jié)量N(k)=M(2)N(k+1)=N(k)+溫度調(diào)節(jié)量……當(dāng)滿足產(chǎn)品工藝要求時(shí),結(jié)束調(diào)整,調(diào)整過程通過程序迭代計(jì)算自動實(shí)現(xiàn)。本實(shí)施例中,加熱工藝的調(diào)整規(guī)則具體包括如下:①滿足條件FMax≥FAim,應(yīng)力段降溫。其中,F(xiàn)Max是對應(yīng)于調(diào)溫工藝N(i),模型計(jì)算管坯斷面局部最大熱應(yīng)力;FAim是加熱過程所允許的最大熱應(yīng)力,本實(shí)施例中取300Mpa;應(yīng)力段定義為超出目標(biāo)應(yīng)力的當(dāng)前控制段;②滿足條件Tave-TAim>ΔT1,溫度段降溫。其中,Tave是對應(yīng)于調(diào)溫工藝N(i),模型計(jì)算管坯出爐平均溫度;TAim是工藝給出目標(biāo)出爐溫度,本實(shí)施例中取值1220℃;ΔT1是工藝允許最大出爐溫度偏差,在本實(shí)施例中取值10℃;溫度段定義為應(yīng)力段(不包含應(yīng)力段)到出爐位置之間的所有控溫段,如果不存在應(yīng)力段,則所有的控溫段均為溫度段。③滿足條件Tave-TAim<-ΔT1,溫度段升溫。④滿足條件tcalcu-tAim>Δt,減少工藝在爐時(shí)間。其中,tcalcu是對應(yīng)于調(diào)溫工藝N(i),計(jì)算管坯平均溫度達(dá)到TAim后,管坯還在加熱爐內(nèi)的停留時(shí)間;tAim是工藝給出保溫時(shí)間,在本實(shí)施例中,取值30min;Δt是工藝允許的保溫時(shí)間偏差,在本實(shí)施例中,取值2min。⑤滿足條件tcalcu-tAim<-Δt,即增加工藝在爐時(shí)間。⑥同時(shí)滿足如下條件,輸出調(diào)整后加熱工藝:在本實(shí)施例中,單步溫度調(diào)整值取5℃,單步時(shí)間調(diào)整值取2min。根據(jù)步驟3,針對給定加熱工藝,利用步驟1模型,計(jì)算對應(yīng)于不同時(shí)刻的管坯溫度和熱應(yīng)力值。此處涉及的給定加熱工藝,具體來說,是指當(dāng)前調(diào)整流程中的調(diào)溫工藝N(i)。以N(1)為例,計(jì)算得到對應(yīng)于初始工藝的管坯溫度及熱應(yīng)力的計(jì)算結(jié)果如圖3中所示。根據(jù)步驟4,采用步驟3計(jì)算結(jié)果,判斷當(dāng)前加熱工藝狀態(tài),利用步驟2建立的流程和規(guī)則,通過迭代計(jì)算實(shí)現(xiàn)加熱工藝調(diào)整,最終輸出符合工藝要求的加熱工藝。以加熱工藝N(1)的計(jì)算結(jié)果為例,在預(yù)熱1段,模型計(jì)算管坯在加熱過程的最大熱應(yīng)力為340Mpa,較目標(biāo)值300Mpa大,因此定義預(yù)熱1段為應(yīng)力段;其余控溫段為溫度段。模型計(jì)算管坯的出爐溫度達(dá)到1235℃,超出管坯出爐目標(biāo)溫度1220±10℃的要求。因此,在本次調(diào)整過程中,取值預(yù)熱1段的工藝爐溫,即:其余各控制段均采用對應(yīng)的工藝溫度表示根據(jù)步驟2建立的調(diào)整流程和調(diào)整規(guī)則,當(dāng)前計(jì)算結(jié)果滿足調(diào)整規(guī)則①,因此,下次迭代計(jì)算的應(yīng)力段爐溫調(diào)整為:當(dāng)前調(diào)整后的加熱工藝N(2)下表,在爐時(shí)間210min:控制段預(yù)熱1預(yù)熱2加熱1加熱2加熱3均熱1均熱2工藝爐溫℃1045118012201260126012401240然后再以N(2)為例,利用步驟3進(jìn)行模型計(jì)算,并根據(jù)步驟4進(jìn)行判斷調(diào)整,通過這樣不斷迭代,直到調(diào)整后的加熱工藝滿足目標(biāo)要求,則停止迭代,輸出調(diào)整后的加熱工藝。在本實(shí)施例中,通過反復(fù)迭代后,最終得到加熱工藝對應(yīng)的加熱時(shí)間為200min,各控制段的工藝爐溫為:控制段預(yù)熱1預(yù)熱2加熱1加熱2加熱3均熱1均熱2工藝爐溫℃1010109012101250125012301230對應(yīng)于調(diào)整完成后的加熱工藝,計(jì)算結(jié)果如圖4中所示。由該圖可知,模型計(jì)算管坯在加熱過程的最大熱應(yīng)力為295Mpa,較目標(biāo)值300Mpa小,滿足加熱過程的管坯斷面熱應(yīng)力限制;模型計(jì)算管坯的出爐溫度達(dá)到1225℃,滿足管坯出爐目標(biāo)溫度1220±10℃的要求;均熱時(shí)間29min,滿足管坯加熱過程的均熱要求。本發(fā)明的技術(shù)方案主要針對高合金鋼,以控制爐內(nèi)管坯的熱應(yīng)力和出爐溫度為目標(biāo),采用管坯溫度模型和管坯熱應(yīng)力模型,確定管坯在加熱過程中,各控制段的工藝爐溫和工藝在爐時(shí)間;該技術(shù)方案通過合理設(shè)計(jì)管坯在環(huán)形加熱爐中的工藝爐溫和工藝在爐時(shí)間,能夠有效降低管坯在加熱過程中因熱應(yīng)力過高而產(chǎn)生表面裂紋的風(fēng)險(xiǎn),提高產(chǎn)品加熱質(zhì)量,同時(shí)有利于降低加熱爐排煙溫度,減少工序能耗。本發(fā)明可廣泛用于高合金管坯在環(huán)形加熱爐加熱時(shí)的加熱工藝及生產(chǎn)控制領(lǐng)域。當(dāng)前第1頁1 2 3