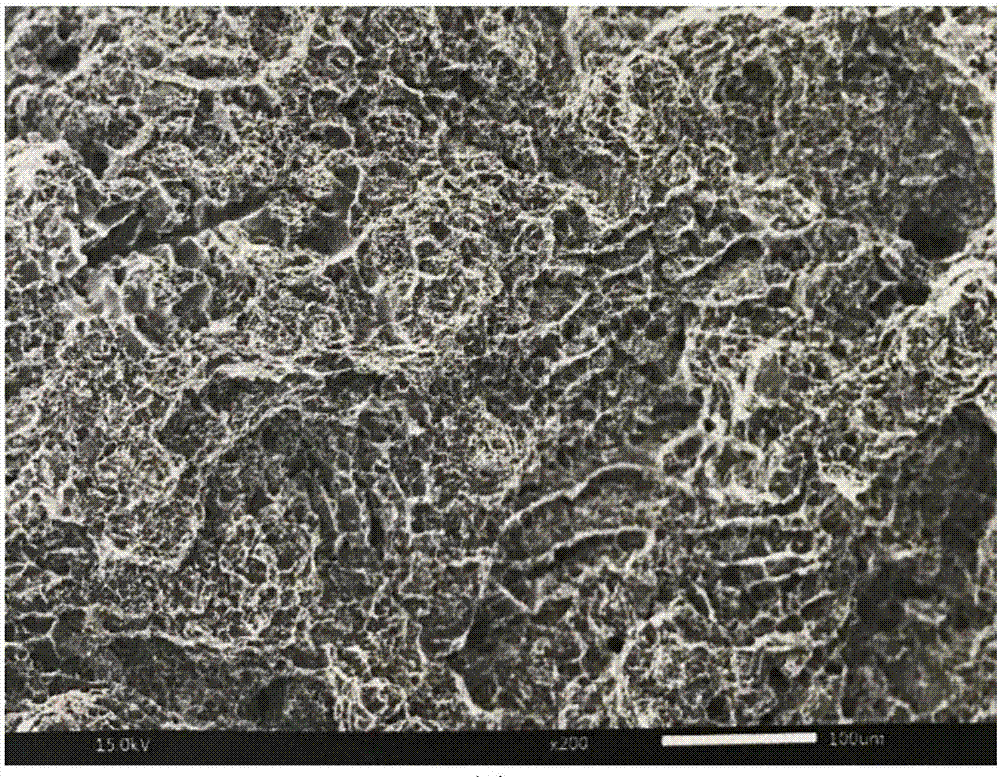
本發(fā)明涉及合金材料領(lǐng)域,尤其涉及一種高強韌耐腐蝕鋁合金材料,還涉及該鋁合金材料的制備方法。
背景技術(shù):
:al-si-cu系鑄造鋁合金是當(dāng)前在工業(yè)中應(yīng)用最多的鑄造鋁合金材料,如國內(nèi)yl102(alsi12)、yl112(alsi8.5cu3.5)和yl113(alsi811cu3),日本adc12(alsi11cu3)、adc10(alsi8.5cu3.5)以及美國a380(alsi8.5cu3.5)等,這些合金具有優(yōu)異的鑄造性能、高的強度和較好的抗腐蝕性,在扶梯電梯、汽車關(guān)鍵零部件(減速器殼體、控制臂)等眾多領(lǐng)域廣泛應(yīng)用,但其韌性、塑性較低,如:y112合金(gb/t15115-94)的強度為240mpa,延伸率僅為1%。如能進一步提高其塑性無疑將提高產(chǎn)品的可靠性和輕量化水平。迄今為止,國內(nèi)外對鑄造成型好、強韌性高、耐腐蝕性好的鑄造鋁合金材料都進行了大量研究,但沖擊韌性≥34.3j/cm2,抗拉強度≥208mpa,斷后延伸率≥6.5%,在3.5%nacl水溶液中浸泡93h的腐蝕速率≤0.049mm/y的鑄造鋁合金材料尚未見報道。如中國專利cn101798649a公開了一種鋯和鍶微合金化的6013型鋁合金,主要由鋁、1.22~1.52%的鎂、0.90~1.15%的硅、0.804~1.04%的銅、0.451~0.661%的錳、0.311~0.135%的鋅、0.0915~0.135%的鋯和0.0157~0.0391%的鍶組成;該合金的制備方法是:將純al融化后加入al-cu中間合金、al-si中間合金、al-mn中間合金、al-zr中間合金、al-sr中間合金、純mg、純zn,待其融化后加入六氯乙烷精煉,靜置保溫5~10min后去渣并澆鑄成錠。該發(fā)明合金硬度為156.0~159.1hv,抗晶間腐蝕性能處于四級,抗剝落腐蝕性能不低于pb級。該發(fā)明提供的微合金化鋁合金的制備方法為本發(fā)明提供了一定的指導(dǎo)思路,但是,相比于本發(fā)明,該發(fā)明制備的鋁合金在強韌性和可塑性方面遠不如本發(fā)明制備的鋁合金。又如中國專利cn103572111a公開了一種高強韌鑄造用鋁合金,其成分按重量百分比為:si:6.5~7.50%、mg:0.3~0.45%、sr:0.1~0.2%、cu≤0.1%、cr:0.02%、ti≤0.2%、mn≤0.5%、zn≤0.05%、fe≤0.12%,余量為al。其制造方法包括以下步驟:首先熔煉鋁材,去掉廢渣;將溫度升至780℃,加入sr;鋁液溫度調(diào)整至740℃除氣30分鐘;將溫度降至澆鑄溫度690℃;倒入模具進行澆鑄;將鋁合金鑄件經(jīng)人工時效處理。該發(fā)明提供的高強韌鑄造鋁合金抗拉強度為250mpa,伸長率為5%,布氏硬度80hbw。而本發(fā)明提供的高強韌耐腐蝕鋁合金材料,其伸長率明顯優(yōu)于該發(fā)明。技術(shù)實現(xiàn)要素:為克服現(xiàn)有技術(shù)中存在的鑄造鋁合金材料韌性和塑性低、耐腐蝕性不高的問題,本發(fā)明提供了一種高強韌耐腐蝕鋁合金材料及其制備方法。一種高強韌耐腐蝕鋁合金材料,包含主合金化元素鋁、硅和銅,微合金化元素錳、鎂和鋅,同時添加微量鋯和鍶元素進行復(fù)合微合金化,其特征在于:所述主合金化元素中硅含量為7.93~8.92wt%,銅含量為1.98~2.11wt%;所述微合金化元素中錳含量為0.001~0.02wt%,鎂含量為0.001~0.02wt%,鋅含量為0.005~0.23wt%,鋯含量為0.182~0.62wt%,鍶含量為0.0346~0.0391wt%或0.0391~0.04wt%,余量為鋁。在一些實施方式中,所述主合金化元素中硅含量為8.21~8.92wt%,銅含量為1.98~2.08wt%;所述微合金化元素中錳含量為0.001~0.02wt%,鎂含量為0.001~0.02wt%,鋅含量為0.005~0.23wt%,鋯含量為0.32~0.62wt%,鍶含量為0.0346~0.0391wt%,余量為鋁。在一些實施方式中,所述主合金化元素中硅含量為8.61~8.92wt%,銅含量為1.98~2.04wt%;所述微合金化元素中錳含量為0.001~0.02wt%、鎂含量為0.001~0.02wt%、鋅含量為0.005~0.23wt%,鋯含量為0.55~0.62wt%,鍶含量為0.0391~0.04wt%,余量為鋁。在一些實施方式中,所述主合金化元素中硅含量為8.92wt%,銅含量為1.98wt%;所述微合金化元素中錳含量為0.001~0.02wt%,鎂含量為0.001~0.02wt%,鋅含量為0.005~0.23wt%,鋯含量為0.62wt%,鍶含量為0.04%,余量為鋁。在一些實施方式中,所述高強韌耐腐蝕鋁合金材料沖擊韌性≥34.3j/cm2,抗拉強度≥208mpa,斷后延伸率≥6.5%,在3.5%nacl水溶液中浸泡93h的腐蝕速率≤0.049mm/y,可應(yīng)用在航天、汽車和自動扶梯的梯級上。一種高強韌耐腐蝕鋁合金材料的制備方法,其特征在于:包括以下步驟:步驟一:高溫融化,使鋁融化成鋁液;步驟二:加入合金化元素si、cu、zr、sr、mn、mg和zn,使其各元素最終含量滿足配比要求;步驟三:去除廢渣,降溫排氣;步驟四:澆鑄成型。在一些實施方式中,所述步驟二中合金化元素的加入方法以鋁基中間合金的方式加入,其中,al-si中間合金含量15.86~17.84wt%,si的質(zhì)量百分比為50%;al-cu中間合金含量5.66~6.03wt%,cu的質(zhì)量百分比為35%;al-zr中間合金含量1.86~6.33wt%,zr的質(zhì)量百分比為9.8%;al-sr中間合金含量0.23~0.257wt%或0.257~0.263wt%,sr的質(zhì)量百分比為15.2%;al-mg中間合金含量0.019~0.39wt%,mg的質(zhì)量百分比為5.1%;al-mn中間合金含量0.016~0.33wt%,mn的質(zhì)量百分比為6%;al-zn中間合金0.065~3.067wt%,zn的質(zhì)量百分比為7.6%。在一些實施方式中,所述步驟一種高溫融化溫度為750~800℃,所述步驟三中降溫排氣溫度為700~750℃,時間為20~30min。在一些實施方式中,所述步驟四種澆鑄成型包括澆鑄凝固和后處理加工,澆鑄溫度為680~740℃,凝固時間控制為1~3min;后處理加工為鋁合金表面瑕疵的處理,依次包括退火和回火處理。與現(xiàn)有技術(shù)相比,本發(fā)明提供的一種高強韌耐腐蝕鋁合金材料及其制備方法產(chǎn)生的有益效果是:一、本發(fā)明提供的一種高強韌耐腐蝕鋁合金材料及其制備方法,在常規(guī)al-si-cu系鑄造鋁合金成分設(shè)計的基礎(chǔ)上,通過調(diào)整硅含量至7.93~8.92wt%,銅含量至1.98~2.11wt%,同時添加0.182~0.62wt%的鋯,0.0346~0.0391wt%或0.0391~0.04wt%的鍶進行復(fù)合微合金化,在不降低鋁合金鑄造性能(流動性)的同時,高效細化了鋁合金中的硅相,使硅尺寸集中在亞微米級,并且長徑比集中在≤2,大幅提高了鋁合金的韌性、塑性和耐腐蝕性,同時,合金的強度也得到提高,具有非常顯著的性能效果。二、本發(fā)明提供的一種高強韌耐腐蝕鋁合金材料及其制備方法,獲得的鑄造鋁合金其性能突破了國際標準規(guī)范,經(jīng)機械工業(yè)材料質(zhì)量檢測中心檢測:其沖擊韌性≥34.3j/cm2,抗拉強度≥208mpa,斷后延伸率≥6.5%,在3.5%nacl水溶液中浸泡93h的腐蝕速率≤0.049mm/y,其中斷后延伸率是其他材料不可比擬的,能顯著提高鋁合金材料的強韌性和可塑性。三、本發(fā)明提供的一種高強韌耐腐蝕鋁合金材料及其制備方法,制備得到的高強韌耐腐蝕鋁合金材料可制備得到更具輕量化的產(chǎn)品,可廣泛應(yīng)用于自動扶梯、汽車、航空等工業(yè)領(lǐng)域,以減輕扶梯、汽車、航天器的重量,從而降低扶梯、汽車、航天器的能耗,并提高其可靠性。四、本發(fā)明提供的一種高強韌耐腐蝕鋁合金材料及其制備方法,通過理論分析、jmatpro材料設(shè)計軟件計算和試驗研究,研究主合金化元素(si、cu)、微合金化元素(zr、sr、mn、mg、zn)及其含量對高強韌耐腐蝕鋁合金鑄造性能(流動性)、組織、力學(xué)性能的影響規(guī)律,為制定實驗方案提供了精確指導(dǎo),為確保獲得硅相細小、合金致密的優(yōu)良鑄態(tài)組織提供了有力的數(shù)據(jù)支持和性能保障。附圖說明圖1是本發(fā)明披露的高強韌耐腐蝕鋁合金的微觀組織;圖2是本發(fā)明披露的高強韌耐腐蝕鋁合金在沖擊韌性時的斷口形貌;圖3是本發(fā)明披露的高強韌耐腐蝕鋁合金在拉伸時的斷口形貌。具體實施方式以下結(jié)合附圖和實施例,對本發(fā)明進行進一步詳細說明。應(yīng)當(dāng)理解,此處所描述的具體實施例僅用以解釋本發(fā)明,并不用于限定本發(fā)明。本發(fā)明披露了一種高強韌耐腐蝕鋁合金,包含主合金化元素鋁、硅和銅,微合金化元素錳、鎂和鋅,同時添加微量鋯和鍶元素進行復(fù)合微合金化。作為本發(fā)明的一個發(fā)明點,所述主合金化元素中硅含量為7.93~8.92wt%,銅含量為1.98~2.11wt%;所述微合金化元素中錳含量為0.001~0.02wt%,鎂含量為0.001~0.02wt%,鋅含量為0.005~0.23wt%,鋯含量為0.182~0.62wt%,鍶含量為0.0346~0.0391wt%或0.0391~0.04wt%,余量為鋁。本發(fā)明在常規(guī)al-si-cu系鑄造鋁合金成分設(shè)計的基礎(chǔ)上,通過調(diào)整硅含量至7.93~8.92wt%,銅含量至1.98~2.11wt%,同時添加0.182~0.62wt%的鋯,0.0346~0.0391wt%或0.0391~0.04wt%的鍶進行復(fù)合微合金化,在不降低鋁合金鑄造性能(流動性)的同時,高效細化了鋁合金中的硅相。對上述實施方式所得到的高強韌耐腐蝕鋁合金進行性能表征和測試,具體如下:通過光學(xué)電鏡,觀察所得高強韌耐腐蝕鋁合金的表面微觀組織,結(jié)果如圖1所示,由圖1可知,硅相尺寸集中在亞微米級,并且長徑比集中在≤2。通過掃面電鏡,觀察所得高強韌耐腐蝕鋁合金在沖擊韌性時的斷口形貌,結(jié)果如圖2所示,由圖2可知,高強韌耐腐蝕鋁合金材料在沖擊韌性時的斷口呈韌窩特征的典型韌性斷裂形貌;觀察所得高強韌耐腐蝕鋁合金在拉伸時的斷口形貌,結(jié)果如圖3所示,由圖3可知,高強韌耐腐蝕鋁合金材料在拉伸時的斷口也呈韌窩特征的典型韌性斷裂形貌;對高強韌耐腐蝕鋁合金進行腐蝕試驗:將試樣放入溫度為(37±2)℃的3.5%氯化鈉溶液中進行93小時浸泡試驗后觀察,發(fā)現(xiàn)試樣表面有白色腐蝕物,去除腐蝕物后稱重,得出試樣的均勻腐蝕速率為0.049mm/y。對高強韌耐腐蝕鋁合金進行拉伸性能測試,測試方法參照gb/t228.1-2010,測試結(jié)果如表1所示,由表1可知,其抗拉強度≥208mpa,斷后延伸率≥6.5%,規(guī)定塑性延伸強度≥88mpa。對高強韌耐腐蝕鋁合金進行沖擊性能測試,測試方法參照gb/t229-2007,測試結(jié)果如表2所示,由表2可知,其沖擊韌性≥34.3j/cm2。表1高強韌耐腐蝕鋁合金拉伸性能測試檢測項目1#2#3#4#5#抗拉強度(mpa)208208211208209斷后延伸率(%)6.76.57.17.86.6規(guī)定塑性延伸強度(mpa)8889909388表2高強韌耐腐蝕鋁合金沖擊性能測試綜上所述,本發(fā)明制備所得的高強韌耐腐蝕鋁合金材料大幅提高了鋁合金的韌性、塑性和耐腐蝕性,具體而言,該高強韌耐腐蝕鋁合金材料沖擊韌性≥34.3j/cm2,抗拉強度≥208mpa,斷后延伸率≥6.5%,在3.5%nacl水溶液中浸泡93h的腐蝕速率≤0.049mm/y,其中斷后延伸率是其他材料不可比擬的,能顯著提高鋁合金材料的強韌性和可塑性,獲得的高強韌耐腐蝕鋁合金其性能突破了國際標準規(guī)范。在上述實施方式的基礎(chǔ)之上,以下通過實施例1-3三個對比實施例具體闡述該高強韌耐腐蝕鋁合金各元素含量對材料性能的影響。實施例1:所述主合金化元素中硅含量為8.21~8.92wt%,銅含量為1.98~2.08wt%;所述微合金化元素中錳含量為0.001~0.02wt%,鎂含量為0.001~0.02wt%,鋅含量為0.005~0.23wt%,鋯含量為0.32~0.62wt%,鍶含量為0.0346~0.0391wt%,余量為鋁。該實施方式獲得的高強韌耐腐蝕鋁合金材料沖擊韌性≥38.4j/cm2,抗拉強度≥210mpa,斷后延伸率≥6.8%,在3.5%nacl水溶液中浸泡93h的腐蝕速率≤0.047mm/y。實施例2:所述主合金化元素中硅含量為8.61~8.92wt%,銅含量為1.98~2.04wt%;所述微合金化元素中錳含量為0.001~0.02wt%、鎂含量為0.001~0.02wt%、鋅含量為0.005~0.23wt%,鋯含量為0.55~0.62wt%,鍶含量為0.0391~0.04wt%,余量為鋁。該實施方式獲得的高強韌耐腐蝕鋁合金材料沖擊韌性≥39.1j/cm2,抗拉強度≥209mpa,斷后延伸率≥7.1%,在3.5%nacl水溶液中浸泡93h的腐蝕速率≤0.045mm/y。實施例3:所述主合金化元素中硅含量為8.92wt%,銅含量為1.98wt%;所述微合金化元素中錳含量為0.001~0.02wt%,鎂含量為0.001~0.02wt%,鋅含量為0.005~0.23wt%,鋯含量為0.62wt%,鍶含量為0.04%,余量為鋁。該實施方式獲得的高強韌耐腐蝕鋁合金材料沖擊韌性≥40.1j/cm2,抗拉強度≥211mpa,斷后延伸率≥7.8%,在3.5%nacl水溶液中浸泡93h的腐蝕速率≤0.042mm/y。以上三種實施方式,對主合金化元素硅和銅的含量進行進一步的優(yōu)化,同時對微合金化元素鋯和鍶的含量也進行進一步的優(yōu)化,經(jīng)過一系列檢測,得到了高強韌耐腐蝕鋁合金材料的沖擊韌性、抗拉強度、斷后延伸率以及在3.5%nacl水溶液中浸泡93h的腐蝕速率。由測試結(jié)果發(fā)現(xiàn),當(dāng)主合金化元素中硅含量為8.92wt%,銅含量為1.98wt%;微合金化元素中錳含量為0.001~0.02wt%,鎂含量為0.001~0.02wt%,鋅含量為0.005~0.23wt%,鋯含量為0.62wt%,鍶含量為0.04%時,所得的高強韌耐腐蝕鋁合金材料擊韌性≥40.1j/cm2,抗拉強度≥211mpa,斷后延伸率≥7.8%,在3.5%nacl水溶液中浸泡93h的腐蝕速率≤0.042mm/y,相比于之前的實施例,具有最佳的實施效果。在實際生產(chǎn)應(yīng)用中,本發(fā)明提供的實施方式:主合金化元素中硅含量為7.93~8.92wt%,銅含量為1.98~2.11wt%;微合金化元素中錳含量為0.001~0.02wt%,鎂含量為0.001~0.02wt%,鋅含量為0.005~0.23wt%,鋯含量為0.182~0.62wt%,鍶含量為0.0346~0.0391wt%或0.0391~0.04wt%已能滿足目標產(chǎn)品需求,但是,為了具備更優(yōu)化的實施效果,可選擇實施例1-3所述的實施方式或在此范圍內(nèi)的其他實施方式,尤其可選擇實施例3所述的實施方式。另外,在理想狀態(tài)下,所述高強韌耐腐蝕鋁合金中雜質(zhì)含量可為0,但是,在實際生產(chǎn)中,為了避免一些不可控的因素,本發(fā)明提供的高強韌耐腐蝕鋁合金材料中不可避免的雜志含量控制在≤0.05wt%的范圍內(nèi)即可達到生產(chǎn)需求。作為進一步優(yōu)選的,在本發(fā)明的此實施方式中,通過理論分析、jmatpro材料設(shè)計軟件計算和試驗研究,研究主合金化元素(si、cu)、微合金化元素(zr、sr、mn、mg、zn)及其含量對高強韌耐腐蝕鋁合金鑄造性能(流動性)、組織、力學(xué)性能的影響規(guī)律。具體的,包括以下研究內(nèi)容:(1)高強韌耐腐蝕鋁合金材料鑄造性能的研究:通過流動性試驗,研究主合金化元素、微合金化元素及其含量對合金液態(tài)流動性能的影響規(guī)律。(2)高強韌耐腐蝕鋁合金材料鑄態(tài)組織的研究:通過光學(xué)顯微鏡和掃面電鏡,研究確立主合金化元素、微合金化元素、熔鑄工藝等因素與合金鑄態(tài)組織之間內(nèi)在聯(lián)系。(3)高強韌耐腐蝕鋁合金材料鑄態(tài)沖擊韌性和多沖疲勞性能的研究:通過擺錘沖擊韌性試驗、多沖疲勞試驗,研究高強韌耐腐蝕鋁合金材料鑄態(tài)韌性和多沖疲勞性能及其關(guān)鍵影響因素(化學(xué)成分、熔鑄工藝、組織等)。(4)高強韌耐腐蝕鋁合金材料鑄態(tài)強度、塑性的研究:通過拉伸試驗,研究合金的化學(xué)成分、熔鑄工藝、微觀組織等關(guān)鍵因素對高強韌耐腐蝕鋁合金材料的強度、延伸率的影響并進行檢測。(5)高強韌耐腐蝕鋁合金材料鑄態(tài)耐腐蝕性能的研究:通過腐蝕試驗,檢測高強韌耐腐蝕鋁合金材料的耐腐蝕性能,進一步優(yōu)化合金的化學(xué)成分、熔鑄工藝和微觀組織。通過以上研究內(nèi)容,高度細化了高強韌耐腐蝕鋁合金制備過程中的實驗數(shù)據(jù),為制定實驗方案提供了精確指導(dǎo),同時也為確保獲得硅相細小、合金致密的優(yōu)良鑄態(tài)鋁合金組織提供了有力的數(shù)據(jù)支持和性能保障。在上述實施方式的基礎(chǔ)之上,本發(fā)明還提供了這種高強韌耐腐蝕鋁合金材料的制備方法,具體包括以下步驟:步驟一:將鋁放入高溫爐內(nèi)進行高溫融化,高溫融化溫度為750~800℃;步驟二:待融化成鋁液后,依次加入合金化元素si、cu、zr、sr、mn、mg和zn,使其各元素最終含量滿足配比要求;步驟三:待充分攪拌融化后,去除廢渣,然后降溫排氣直至沒有氣體溢出,降溫排氣溫度為700~750℃,時間為20~30min;步驟四:最后進行澆鑄成型,具體包括澆鑄凝固和后處理加工,澆鑄溫度為680~740℃,凝固時間控制為1~3min;后處理加工為鋁合金表面瑕疵的處理,依次包括退火和回火處理。進一步優(yōu)化的,所述步驟二中合金化元素的加入方法以鋁基中間合金的方式加入,其中,al-si中間合金含量15.86-17.84wt%,si的質(zhì)量百分比為50%;al-cu中間合金含量5.66~6.03wt%,cu的質(zhì)量百分比為35%;al-zr中間合金含量1.86~6.33wt%,zr的質(zhì)量百分比為9.8%;al-sr中間合金含量0.23~0.257wt%或0.257~0.263wt%,sr的質(zhì)量百分比為15.2%;al-mg中間合金含量0.019~0.39wt%,mg的質(zhì)量百分比為5.1%;al-mn中間合金含量0.016~0.33wt%,mn的質(zhì)量百分比為6%;al-zn中間合金0.065~3.067wt%,zn的質(zhì)量百分比為7.6%。此外,也可選用復(fù)合鋁基中間合金,如以al-si-mg中間合金、al-cu-mn中間合金等中間合金的方式添加進入鋁液中,在保證最終鋁合金材料中各元素配比含量滿足本發(fā)明要求的前提下可以以任意多種鋁基組合中間合金的方式加入。不選用金屬單質(zhì)而使用鋁基中間合金是為了減少燒損,所述中間合金可采用常規(guī)方法:如鋁熱法或溶化合成法,進行自行配置,也可根據(jù)配比在市場進行購買;中間合金的加入方式可以一次性加入也可待前一種中間合金融化后再加入另一種中間合金,優(yōu)選后一種加入方式。本發(fā)明實現(xiàn)了高強韌耐腐蝕鋁合金材料的研究,制備了鑄造性能優(yōu),強韌性高、耐腐蝕性能好的鑄造鋁合金材料。通過該方法制備得到的高強韌耐腐蝕鋁合金材料可制備得到更具輕量化的產(chǎn)品,可廣泛應(yīng)用于自動扶梯、汽車、航空等工業(yè)領(lǐng)域,以減輕扶梯、汽車、航天器的重量,從而降低扶梯、汽車、航天器的能耗,并提高其可靠性。上述說明示出并描述了本發(fā)明的優(yōu)選實施例,如前所述,應(yīng)當(dāng)理解本發(fā)明并非局限于本文所披露的形式,不應(yīng)看作是對其他實施例的排除,而可用于各種其他組合、修改和環(huán)境,并能夠在本文所述發(fā)明構(gòu)想范圍內(nèi),通過上述教導(dǎo)或相關(guān)領(lǐng)域的技術(shù)或知識進行改動。而本領(lǐng)域人員所進行的改動和變化不脫離本發(fā)明的精神和范圍,則都應(yīng)在本發(fā)明所附權(quán)利要求的保護范圍內(nèi)。當(dāng)前第1頁12