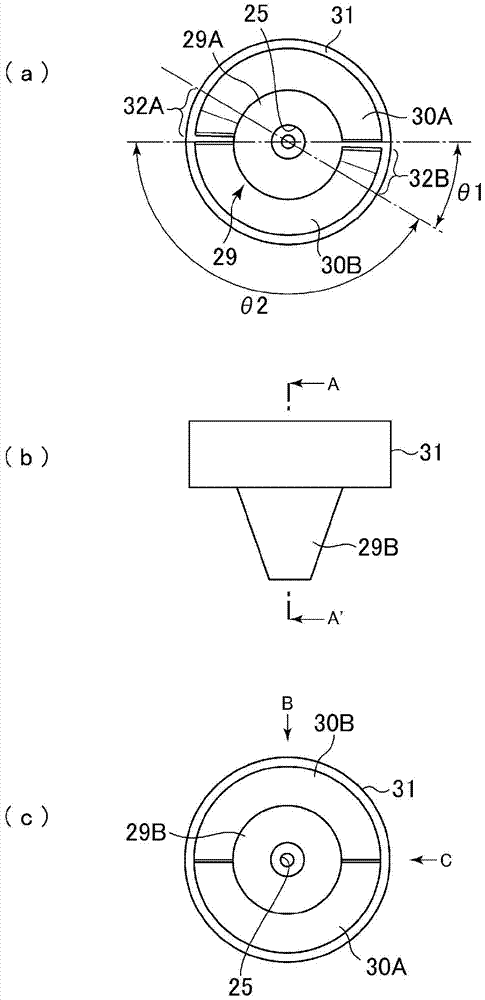
本發(fā)明涉及微氣泡發(fā)生裝置,利用回旋流進(jìn)行氣液混合,使液體中產(chǎn)生微氣泡。
背景技術(shù):作為使液體中產(chǎn)生微小氣泡等微氣泡的方式,已知有氣液二相高速回旋方式。在氣液二相高速回旋方式中,使液體沿噴嘴內(nèi)的圓筒面高速回旋,在噴嘴中心(沿軸心)產(chǎn)生負(fù)壓。而且,利用該負(fù)壓向噴嘴內(nèi)導(dǎo)入氣體,形成高速回旋的氣液二相回旋流。將該回旋流沿軸心縮流,通過從噴嘴出口散開,將氣液二相流體剪斷,產(chǎn)生微氣泡(例如參照專利文獻(xiàn)1、2)。在專利文獻(xiàn)1的微氣泡發(fā)生裝置中,將高壓的液體通過螺旋流路導(dǎo)入噴嘴內(nèi)的氣液混合空間,由此形成沿著氣液混合空間的圓筒內(nèi)周面的螺旋狀的高速回旋流。螺旋流路通過將其外周設(shè)有螺旋狀葉片的圓柱部嵌合于具有與葉片的外徑大致相等的內(nèi)徑的噴嘴主體上設(shè)置的圓筒內(nèi)而形成?,F(xiàn)有技術(shù)文獻(xiàn)專利文獻(xiàn)專利文獻(xiàn)1:日本特開2006-142251號(hào)公報(bào)專利文獻(xiàn)2:日本特許第4376888號(hào)公報(bào)
技術(shù)實(shí)現(xiàn)要素:(發(fā)明要解決的問題)但是,由于螺旋狀的葉片暴露于液體中極高的壓力下,所以專利文獻(xiàn)1、2的結(jié)構(gòu)中,在耐久性上有問題。本發(fā)明的課題在于,在采用了氣液二相高速回旋方式的微氣泡發(fā)生裝置中,提高螺旋流路相對(duì)于高壓流體的耐久性。(解決技術(shù)問題的技術(shù)方案)本發(fā)明的回旋通路形成體,安裝于微氣泡發(fā)生裝置,該微氣泡發(fā)生裝置,將通過螺旋通路加壓的液體向噴嘴內(nèi)供給,使噴嘴內(nèi)產(chǎn)生回旋流,使用利用回旋流產(chǎn)生的負(fù)壓將氣體導(dǎo)入噴嘴內(nèi),形成氣液二相回旋流,通過從噴嘴出口噴出氣液二相回旋流,將氣液二相流體剪斷,產(chǎn)生微氣泡,所述回旋通路形成體的特征在于,具備:主體,其由圓柱部和圓錐梯形部構(gòu)成,沿中心軸形成用于導(dǎo)入氣體的氣體導(dǎo)入孔;螺旋狀的葉片,其沿圓柱部的外周面形成;外側(cè)圓筒部,其形成于葉片的外周緣。優(yōu)選使葉片的入口部立起。由此,降低所供給的液體的壓力損失,提高噴出的液體的流速,從而可以產(chǎn)生強(qiáng)的回旋流。優(yōu)選的是,葉片設(shè)有多個(gè),多個(gè)葉片彼此在中心軸向上不重合。由此,可以通過鑄模一體成形螺旋通路形成體。另外,優(yōu)選多個(gè)葉片由錯(cuò)開180°配置的兩個(gè)葉片構(gòu)成,各葉片遍及外周面的半周形成。更優(yōu)選的是,主體、葉片、外側(cè)圓筒部通過鑄模成形而一體形成。例如,回旋通路形成體由聚苯硫醚(PPS)樹脂形成。本發(fā)明的微氣泡發(fā)生裝置,為使用上述螺旋通路形成體的上述任一個(gè)微氣泡發(fā)生裝置,其特征在于,還具備安裝于噴嘴的液體供給部和設(shè)于液體供給部的氣體供給部,螺旋通路形成體嵌插于噴嘴內(nèi)所形成的圓筒形的收容部,在收容部上設(shè)置承受螺旋通路形成體的外側(cè)圓筒部的臺(tái)階部。液體供給部嵌插于噴嘴并固定于噴嘴,嵌插于噴嘴的液體供給部的前端部與螺旋通路形成體的外側(cè)圓筒部抵接,螺旋通路形成體被保持在臺(tái)階部和前端部之間。沿液體供給部的液體通路內(nèi)配置來自氣體供給部的氣體導(dǎo)入管,氣體導(dǎo)入管與螺旋通路形成體的氣體導(dǎo)入孔連結(jié)。(發(fā)明的效果)根據(jù)本發(fā)明,在采用了氣液二相高速回旋方式的微氣泡發(fā)生裝置中,能夠提高螺旋流路相對(duì)于高壓流體的耐久性。附圖說明圖1是本實(shí)施方式的微氣泡發(fā)生裝置的側(cè)截面圖。圖2是螺旋通路形成體的俯視圖、側(cè)視圖、仰視圖。圖3是螺旋通路形成體的截面圖、向視圖。圖4是螺旋通路形成體的變形例的截面圖。符號(hào)說明10微氣泡發(fā)生裝置11噴嘴12液體供給部13氣體供給部14容器壁面19螺旋通路形成體20收容部20A臺(tái)階部22氣液混合部29螺旋通路形成體主體29A圓柱部29B圓錐梯形部30A、30B螺旋狀的葉片31外側(cè)圓筒部32A、32B螺旋通路入口部。具體實(shí)施方式下面,參照附圖對(duì)本發(fā)明的實(shí)施方式進(jìn)行說明。圖1是表示本發(fā)明一實(shí)施方式的微氣泡發(fā)生裝置的結(jié)構(gòu)的截面圖。微氣泡發(fā)生裝置10具備:使液體中產(chǎn)生微小氣泡等微氣泡的噴嘴11、向噴嘴11供給進(jìn)行了加壓的液體的液體供給部12、向噴嘴11供給氣體的氣體供給部13。噴嘴11例如被固定于貯存液體L的容器的壁面14,且其前端配置于液體L內(nèi)。在本實(shí)施方式中,噴嘴11具備肩部15,噴嘴11其前端被插入形成于壁面14的孔,在噴嘴11的前端螺裝螺母16,且在肩部15和螺母16之間把持壁面14,由此將噴嘴11固定于容器壁面14。在噴嘴11的基部側(cè)氣密地嵌插液體供給部12的一端(前端部12A)。另外,在液體供給部12的另一端設(shè)置氣體供給部13。液體供給部12具備例如L字形的液體通路17,其外形也呈沿著L字形的外形。圖1中,在向側(cè)方延伸的開口端設(shè)置管接頭部18,在管接頭部18上連接與加壓泵等連接的管(未圖示)。即,將由加壓泵加壓的液體向液體通路17供給。另外,液體通路17的另一開口端連接到形成于噴嘴11內(nèi)的旋轉(zhuǎn)對(duì)稱的空間。在該旋轉(zhuǎn)對(duì)稱的空間設(shè)置收容后述的螺旋通路形成體19的大徑的圓筒空間(收容部)20,且在其前端設(shè)置圓錐狀縮徑的縮徑部21。另外,在縮徑部21的前端設(shè)置生成氣液二相回旋流的小徑的圓筒空間(氣液混合部)22。氣液混合部22,在其前端進(jìn)行一端縮徑后,向噴嘴外部開口。在與噴嘴11連接的液體通路17的開口的相反側(cè)(L字狀彎曲的根部)形成小孔23,與來自氣體供給部13的氣體導(dǎo)入管24氣密地相通。延伸到液體通路17內(nèi)的氣體導(dǎo)入管24沿液體通路17的大致中央延伸,其前端部被安裝于在收容部20上裝備的螺旋通路形成體19的氣體導(dǎo)入孔25。在氣體供給部13上形成有流通氣體的L字形的氣體通路26,在向側(cè)方延伸的開口端設(shè)置管接頭27。即,從與管接頭27連接的管(未圖示)向氣體通路26供給所希望的氣體。另外,在氣體通路26的例如L字形彎曲部設(shè)置針型絲桿等流量調(diào)整閥28,進(jìn)行向氣體導(dǎo)入管24供給的氣體流量的調(diào)整。其次,參照?qǐng)D2、圖3說明本實(shí)施方式的螺旋通路形成體19的構(gòu)造。此外,圖2(a)~圖2(c)是本實(shí)施方式的螺旋通路形成體19的俯視圖、側(cè)視圖、仰視圖,圖3(a)是圖2(b)中A-A’截面圖,圖3(b)、(c)是從圖2(c)的B方向、C方向觀察的向視圖(除去外周圓筒部)。如圖2、3所示,螺旋通路形成體19的主體29由圓柱狀的圓柱部29A和從圓柱部29A的下端圓錐梯形狀突出的圓錐梯形部29B構(gòu)成,在圓柱部29A的外周面設(shè)置一對(duì)螺旋狀的葉片30A、30B。另外,在螺旋狀葉片30A、30B的外周緣設(shè)置圓筒狀的外側(cè)圓筒部31。在本實(shí)施方式中,外側(cè)圓筒部31的高度例如與圓柱部29A的高度相等,圓錐梯形部29B的底面的外徑與圓柱部29A的外徑相等。此外,在主體29的中心,沿圓柱軸(圓錐軸)形成氣體導(dǎo)入孔25。在本實(shí)施方式中,螺旋狀的葉片30A、30B從以主體29的中心軸為中心隔開180°的位置起,分別沿圓柱部29A的外周面遍及半周(180°)設(shè)置。即,在本實(shí)施方式中,如2重螺旋那樣,葉片彼此在軸向上不重合。另外,形成螺旋通路的葉片30A、30B在頂面附近立起,形成螺旋通路入口部32A、32B(特別是參照?qǐng)D3(c))。如圖2(a)所示,螺旋通路入口部32A、32B設(shè)于以主體29的軸為中心的角θ1的范圍,剩余的角θ2的范圍作為導(dǎo)程角一定的葉片30A、30B的主體部形成。角度θ1、θ2按例如公差±10°計(jì),分別設(shè)定為約30°、150°,葉片30A、30B的主體部分(角度θ2的范圍)的導(dǎo)程角例如設(shè)定為5°~10°。另外,螺旋通路入口部32A、32B的立起部分的最端部(上游側(cè))為大致90°。其次,參照?qǐng)D1、圖3說明螺旋通路形成體19向收容部20的固定方法。在噴嘴11的收容部20和縮徑部21的連接部形成具有與外側(cè)圓筒部31的厚度大致同一尺寸寬度的臺(tái)階部20A。如果將螺旋通路形成體19安裝于收容部20的話,則外側(cè)圓筒部31的外周面與收容部20的內(nèi)周面密接,外側(cè)圓筒部31的下端部與臺(tái)階部20A抵接。另一方面,液體供給部12的前端部12A呈與外側(cè)圓筒部31大致同一直徑、大致同一厚度的圓筒形狀,在將螺旋通路形成體19安裝于收容部20之后,在噴嘴11上安裝液體供給部12時(shí),前端部12A與外側(cè)圓筒部31的上端部抵接。由此,螺旋通路形成體19的位置在收容部20內(nèi)被固定。此外,在本實(shí)施方式中,此時(shí),螺旋通路形成體19的圓錐部29B的前端位于氣液混合部22的入口高度位置。其次,參照?qǐng)D1對(duì)使用以上結(jié)構(gòu)的氣液二相回旋流體生成過程和微氣泡生成過程的概略進(jìn)行說明。向液體通路17供給的加壓流體從螺旋通路形成體19的入口部(32A、32B)沿著螺旋狀的葉片(30A、30B)被導(dǎo)入縮徑部21,且向周方向下方噴出。液體沿縮徑部21的圓錐面螺旋狀地被導(dǎo)入氣液混合部22,進(jìn)一步被增速,一邊沿氣液混合部22的圓筒內(nèi)周面進(jìn)行高速回旋一邊向噴嘴前端部的開口流動(dòng)。由此,在氣液混合部22的中心產(chǎn)生負(fù)壓,從氣體導(dǎo)入管24沿圓筒軸向氣液混合部22吸引氣體,形成氣液二相回旋流體。該氣液二相回旋流體從縮徑的氣液混合部22的前端開口部向噴嘴外部噴出/散開,在該過程中將氣液二相流體剪斷,產(chǎn)生氣泡。如上,根據(jù)本實(shí)施方式,由于用于微氣泡發(fā)生裝置的螺旋通路形成體上設(shè)置的螺旋狀的葉片的周緣通過圓筒部增強(qiáng),因此,對(duì)于壓力高的液體,也能夠?qū)θ~片賦予足夠的強(qiáng)度。另外,在本實(shí)施方式中,設(shè)置多個(gè)螺旋狀的葉片,并且使它們?cè)谳S向上不重合,因此,可以通過鑄造成形而一體成形螺旋通路形成體。但是,當(dāng)這樣在軸向上不重合時(shí),則如現(xiàn)有例那樣不能采用二重螺旋構(gòu)造,螺旋通路的長度縮短。因此,螺旋流的助起動(dòng)(助走)距離縮短,回旋流的效率降低。雖然考慮通過增大供給的流體壓力對(duì)其補(bǔ)償,但當(dāng)提高壓力且增大螺旋通路的流速時(shí),在螺旋通路入口部分的壓力損失增大。因此,在本實(shí)施方式中,通過立起螺旋通路的入口部分,防止流動(dòng)方向急劇變化,降低損失的發(fā)生。由此,在本實(shí)施方式中,由于使用鑄造成形,所以不僅能夠縮短螺旋通路的長度,而且還能夠產(chǎn)生強(qiáng)的回旋流。此外,在本實(shí)施方式中,螺旋間距在入口部不連續(xù)地變更,但也可以設(shè)為在整個(gè)螺旋通路或入口部,朝向入口連續(xù)增大間距的結(jié)構(gòu)。例如,螺旋通路形成體由聚苯硫醚(PPS)樹脂形成。此外,圖4表示螺旋通路形成體的變形例。在圖4所示的變形例中,將外側(cè)側(cè)壁31和葉片30A、30B、圓柱部29A連接的角部設(shè)為R(形成圓弧等彎曲的形狀),抑制在由這些壁面形成的通路內(nèi)流通的流體在角部產(chǎn)生渦流,降低阻力。