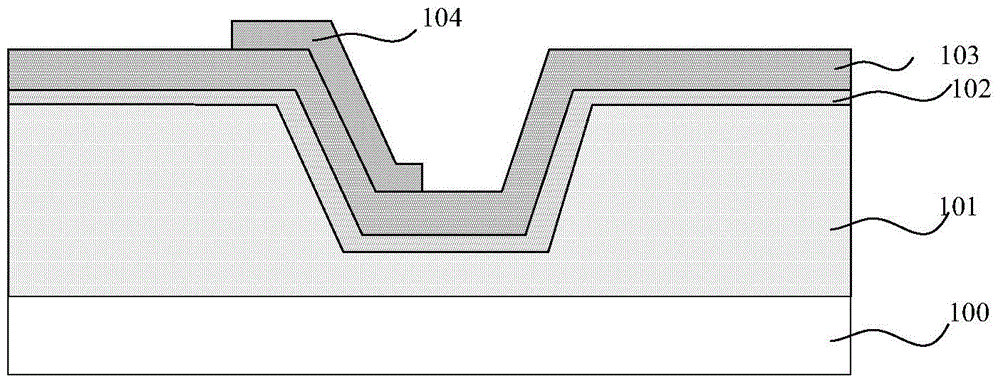
本發(fā)明涉及MEMS器件制造領(lǐng)域,尤其涉及一種三軸磁傳感器的制造方法。
背景技術(shù):微機(jī)電系統(tǒng)(Micro-Electro-MechanicalSystems,簡稱MEMS)是指微細(xì)加工技術(shù)制作的,集微型傳感器、微型構(gòu)件、微型執(zhí)行器、信號處理、控制電路等于一體的微型器件或系統(tǒng),其制造過程是以薄膜沉積、光刻、外延、氧化、擴(kuò)散、注入、濺射、蒸鍍、刻蝕、劃片和封裝等為基本工藝步驟來制造復(fù)雜三維形體的微加工過程,尺寸通常在微米或納米級。其中,磁傳感器是一種MEMS器件,它可以將各種磁場及其變化的量轉(zhuǎn)變成電信號輸出的器件,磁傳感器包括巨磁阻傳感器(GiantMagnetoResistiveSensor,GMR)、各向異性磁阻傳感器(AnisotropicMagnetoResistiveSensor,AMR)等。以各向異性磁阻傳感器為例,鎳鐵合金層作為磁阻層。當(dāng)外界磁場施加到磁阻層上時,磁阻層的磁疇旋轉(zhuǎn),使得磁阻層的電阻發(fā)生改變,磁阻層電阻的變化就反應(yīng)在輸出電壓變化,實現(xiàn)檢測外加磁場的目的。近幾年,各向異性磁阻傳感器技術(shù)的發(fā)展,已經(jīng)歷了單軸磁傳感器、雙軸磁傳感器到三軸(3D)磁傳感器。在現(xiàn)有技術(shù)中,三軸磁傳感器以其可全面檢測空間X、Y、Z三個方向上的磁信號,而得到普遍應(yīng)用。現(xiàn)有技術(shù)的AMR三軸磁傳感器的制程中,X軸和Y軸的磁阻材料形成在平面上,而Z軸的磁阻材料需要和X軸及Y軸形成的平面垂直,因此,要形成一個與平面垂直的溝槽(Trench),以便將Z軸的磁阻材料形成在溝槽的側(cè)壁以及溝槽附近的表面上。具體過程通常包括以下步驟:請參考圖1A,首先在襯底100上形成層間介質(zhì)層101,隨后在層間介質(zhì)層101中形成溝槽(trench),深度大約為3微米;此后在形成溝槽的層間介質(zhì)層101上依次形成氮化硅等擴(kuò)散阻擋層(起擴(kuò)散阻擋作用,未圖示)、鎳鐵合金層102(作為磁性材料層,厚度230埃米左右)和氮化鉭層103(TaN,作為導(dǎo)電材料和掩膜材料,厚度900埃米左右),從而在溝槽中也形成氮化硅層、鎳鐵合金層和氮化鉭層的疊層;此后在氮化鉭層103上形成氮化硅等硬掩膜層104,厚度為400埃米左右;之后填充光刻膠,使光刻膠完全填充深溝槽,并提供平坦表面,對光刻膠進(jìn)行曝光及顯影,形成圖形化的光刻膠層105,圖形化的光刻膠層105定義鎳鐵合金層用于形成Z軸磁阻層的位置,所述Z軸磁阻層包括:所述溝槽一個側(cè)壁上的鎳鐵合金層、與該側(cè)壁接觸的溝槽部分底部上的鎳鐵合金層、與該側(cè)壁接觸的部分層間介質(zhì)層上的鎳鐵合金層。此后,請參考圖1B,以圖形化的光刻膠層為掩模,刻蝕硬掩膜層104,將光刻膠圖案轉(zhuǎn)移到硬掩膜層104,然后以硬掩膜層104為掩膜,依次等離子體干法刻蝕氮化鉭層103以及磁性材料層102,形成Z軸磁阻層;然后請參考圖1C,通過灰化工藝去除光刻膠,并通過刻蝕后殘留物去除液(例如EKC酸)等濕法腐蝕溶液濕法清洗(SolventClean)溝槽表面,以去除刻蝕殘留物,位于磁阻層上的剩余氮化鉭層103用于保護(hù)磁阻層,避免磁阻層直接暴露在空氣中而遭到氧化腐蝕。而上述的這種AMR三軸磁傳感器的制造方法造成磁傳感器性能不佳,主要原因如下:一方面,由于溝槽深度很大,大約為3um,光刻膠填充在溝槽剩余空間內(nèi)后,容易出現(xiàn)溝槽內(nèi)的深紫外光刻膠未完全顯影的情況,還可能出現(xiàn)期望留下光刻膠的溝槽側(cè)壁上沒有光刻膠的情況;另一方面,參照圖2,圖2是現(xiàn)有AMR三軸磁傳感器去除硬掩膜層后的SEM圖譜,對應(yīng)于圖1C虛線圈的位置。由于溝槽深度很大,硬掩膜層、氮化鉭層以及磁性材料層等在溝槽表面的沉積厚度大于溝槽側(cè)壁的沉積厚度,再加上硬掩膜層相對氮化鉭層較薄,所以在等離子體干法刻蝕氮化鉭層以及磁性材料層形成Z軸磁阻層的過程中,溝槽側(cè)壁的硬掩膜層無法阻擋等離子體對溝槽側(cè)壁的氮化鉭層表面的轟擊損害,尤其是溝槽側(cè)壁底部位置;而且刻蝕殘留物通常為含鉭聚合物,比較難去除,所以濕法清洗的清洗溶劑濃度較高,腐蝕力強(qiáng),會穿透氮化硅并進(jìn)一步腐蝕氮化鉭層和磁阻層表面,最終造成表面缺陷,甚至?xí)斐纱抛鑼訑嚅_,最終導(dǎo)致Z軸磁傳感器敏感度降低、不穩(wěn)定甚至失效。因此需要一種新的三軸磁傳感器的制造方法,能夠比較容易的去除刻蝕殘留物,獲得較佳的氮化鉭層以及磁阻層表面形貌,提高器件性能。
技術(shù)實現(xiàn)要素:本發(fā)明的目的在于提供一種三軸磁傳感器的制造方法,能夠比較容易的去除刻蝕殘留物,獲得較佳的氮化鉭層以及磁阻層表面形貌,提高器件性能。為解決上述問題,本發(fā)明提出一種三軸磁傳感器的制造方法,包括以下步驟:提供一半導(dǎo)體襯底,所述半導(dǎo)體襯底中形成有溝槽;在形成溝槽的半導(dǎo)體襯底表面依次形成磁性材料層、氮化鉭層以及硬掩膜層,所述硬掩膜層比所述氮化鉭層厚;在所述硬掩膜層上形成圖案化的光刻膠層,所述圖案化的光刻膠層定義磁阻層的位置;以所述圖案化的光刻膠層為掩膜,刻蝕所述硬掩膜層,保留所述圖案化的光刻膠層下方的硬掩膜層;以所述硬掩膜層為掩膜,依次對所述氮化鉭層和磁性材料層進(jìn)行離子束物理轟擊刻蝕,形成磁阻層,所述磁阻層包括所述溝槽一側(cè)壁上的磁性材料層、與該側(cè)壁接觸的溝槽部分底部上的磁性材料層、與該側(cè)壁接觸的部分半導(dǎo)體襯底表面上的磁性材料層;對形成磁阻層的器件表面進(jìn)行灰化工藝處理;對灰化工藝處理后的器件表面進(jìn)行去離子水清洗。進(jìn)一步的,所述硬掩膜層的厚度是所述氮化鉭的1.5~3倍。進(jìn)一步的,所述磁性材料層為所述氮化鉭層為所述硬掩膜層為進(jìn)一步的,所述磁性材料層為Ni-Fe合金、Ni-Fe-Cr合金、Ni-Fe-Nd合金、Ni-Fe-Cr合金或Fe-Ni-Co合金。進(jìn)一步的,所述硬掩膜層為氮化硅或氮氧化硅。進(jìn)一步的,在所述硬掩膜層上形成圖案化的光刻膠層之間,采用有機(jī)材料填滿溝槽并覆蓋溝槽周圍的硬掩膜層上表面,為所述光刻膠提供平坦工藝表面。進(jìn)一步的,以所述硬掩膜層為掩膜,進(jìn)行離子束物理轟擊刻蝕之前,采用高于200℃的高溫灰化工藝去除包括所述圖案化的光刻膠在內(nèi)的有機(jī)材料。進(jìn)一步的,所述離子束物理轟擊刻蝕的工藝參數(shù)包括:工藝氣體為Ar,氣體流量為10sccm~100sccm,射頻功率為300W~800W。進(jìn)一步的,采用氟基氣體與氧氣的混合氣體進(jìn)行溫度低于200℃的低溫灰化工藝,去除刻蝕過程中反應(yīng)產(chǎn)生的聚合物殘留。進(jìn)一步的,提供一半導(dǎo)體襯底的步驟包括:提供一基底,在所述基底上形成層間介質(zhì)層;刻蝕所述層間介質(zhì)層以在層間介質(zhì)層中形成溝槽。與現(xiàn)有技術(shù)相比,本發(fā)明提供的三軸磁傳感器的制造方法,具有以下有益效果:1、形成比氮化鉭層更厚的硬掩膜層,來保護(hù)溝槽側(cè)壁的氮化鉭層以及磁阻層在后續(xù)刻蝕過程中不受破壞;2、采用離子束物理轟擊刻蝕工藝(IBE)對所述氮化鉭層和磁性材料層進(jìn)行刻蝕,以避免對溝槽側(cè)壁上氮化鉭層和磁性材料層的侵蝕,形成更加精細(xì)的磁阻層,同時去除刻蝕硬掩膜層以及氮化鉭層和磁性材料層過程中產(chǎn)生的含鉭聚合物,僅僅殘留物理轟擊刻蝕后的顆粒,這些顆粒很容易被清洗;3、采用去離子水清洗器件表面,在去除物理轟擊刻蝕后的殘留顆粒的同時,保護(hù)刻蝕后的氮化鉭層和磁阻層的形貌,提高了器件性能;4、在形成磁阻層之后,采用氟基氣體與氧氣的混合氣體的低溫灰化工藝可以進(jìn)一步去除有可能殘留的含鉭聚合物,提高去離子水清洗的效果。附圖說明圖1A至1C是現(xiàn)有的AMR三軸磁傳感器制造過程中的器件剖面結(jié)構(gòu)示意圖;圖2是現(xiàn)有的AMR三軸磁傳感器濕法清洗后的SEM圖譜;圖3是本發(fā)明具體實施例的三軸磁傳感器的制造方法流程圖;圖4A至圖4D是圖3所示的制造過程中的器件結(jié)構(gòu)剖面圖;圖5是本發(fā)明具體實施例的三軸磁傳感器去離子水清洗后的SEM圖譜。具體實施方式為使本發(fā)明的目的、特征更明顯易懂,下面結(jié)合附圖對本發(fā)明的具體實施方式作進(jìn)一步的說明,然而,本發(fā)明可以用不同的形式實現(xiàn),不應(yīng)只是局限在所述的實施例。請參考圖3所示,本發(fā)明提出一種三軸磁傳感器的制造方法,包括以下步驟:S1,提供一半導(dǎo)體襯底,所述半導(dǎo)體襯底中形成有溝槽;S2,在形成溝槽的半導(dǎo)體襯底表面依次形成磁性材料層、氮化鉭層以及硬掩膜層,所述硬掩膜層比所述氮化鉭層厚;S3,在所述硬掩膜層上形成圖案化的光刻膠層,所述圖案化的光刻膠層定義磁阻層的位置;S4,以所述圖案化的光刻膠層為掩膜,刻蝕所述硬掩膜層,保留所述圖案化的光刻膠層下方的硬掩膜層;S5,以所述硬掩膜層為掩膜,依次對所述氮化鉭層和磁性材料層進(jìn)行離子束物理轟擊刻蝕,形成磁阻層,所述磁阻層包括所述溝槽一側(cè)壁上的磁性材料層、與該側(cè)壁接觸的溝槽部分底部上的磁性材料層、與該側(cè)壁接觸的部分半導(dǎo)體襯底表面上的磁性材料層;S6,對形成磁阻層的器件表面進(jìn)行灰化工藝處理;S7,對灰化工藝處理后的器件表面進(jìn)行去離子水清洗。請參考圖4A,在步驟S1中,提供形成有溝槽的半導(dǎo)體襯底的步驟包括:首先,提供一基底400,在具體實施例中,基底400可以為硅襯底、鍺襯底或者絕緣體上硅襯底等,或者還可以包括其它的材料,例如砷化鎵等III-Ⅴ族化合物,然后在所述基底400上形成層間介質(zhì)層401,層間介質(zhì)層401的材料可以為氧化硅、氮氧化硅、TEOS或低K介質(zhì),形成方法為熱氧化生長或化學(xué)氣相沉積工藝,層間介質(zhì)層401起到后續(xù)形成的磁性材料層與基底400之間的絕緣隔離作用;接著,各向異性刻蝕所述層間介質(zhì)層401以在層間介質(zhì)層401中形成溝槽,具體地,先生長一層氮化硅等硬掩膜,然后在硬掩膜上涂布一層光刻膠,并圖形化光刻膠以形成深溝槽光刻窗口,然后,以圖形化光刻膠為掩膜,刻蝕硬掩膜層以及層間介質(zhì)層401形成具有一定傾斜角度的深溝槽,深溝槽的角度需要與后續(xù)的有機(jī)填充材料的厚度和淀積的角度做綜合考量并匹配,典型值是85度至90度,寬度為3μm以上,深度為2μm~4μm,然后通過濕法刻蝕去除硬掩膜,濕法刻蝕液是氫氟酸和硫酸的混合物,溝槽的深度一般小于層間介質(zhì)層401的厚度,也就是溝槽的底部不為基底400的上表面;最后,在形成所述溝槽的層間介質(zhì)層401表面依次形成擴(kuò)散阻擋層(未圖示)。擴(kuò)散阻擋層的材料可以為氮化硅、氮氧化硅或二氧化硅,形成擴(kuò)散阻擋層的方法可以為化學(xué)氣相沉積,擴(kuò)散阻擋層覆蓋層間介質(zhì)層401、溝槽的底部和側(cè)壁,用于阻擋后續(xù)磁性材料向?qū)娱g介質(zhì)層401中擴(kuò)散而引起短路或擊穿,確保層間介質(zhì)層401的絕緣隔離作用。本發(fā)明的磁傳感器為3D磁傳感器,最終形成的磁阻層只形成在位于溝槽的一側(cè)側(cè)壁的擴(kuò)散阻擋層表面、與對應(yīng)側(cè)壁相連的溝槽底部的擴(kuò)散阻擋層部分表面、和位于溝槽外且與對應(yīng)側(cè)壁相連的擴(kuò)散阻擋層頂部部分表面,從而可以分別感應(yīng)X、Y、Z三個方向的磁場信號。請繼續(xù)參考圖4A,在步驟S2中,首選,通過濺射鍍膜工藝或其他物理氣相沉積工藝在形成溝槽的器件表面依次形成磁性材料層402以及氮化鉭TaN層403,并進(jìn)行退火處理,從而形成各向異性磁電阻薄膜。在3D磁傳感器中,所述磁性材料層為Ni-Fe合金、Ni-Fe-Cr合金、Ni-Fe-Nd合金、Ni-Fe-Cr合金或Fe-Ni-Co合金,所述磁性材料層402后續(xù)形成磁傳感器的磁阻層,當(dāng)外界磁場施加到磁阻層上時,磁阻層的磁疇旋轉(zhuǎn),使得磁阻層的電阻發(fā)生改變,磁阻層電阻的變化就反應(yīng)在輸出電壓變化,實現(xiàn)檢測外加磁場的目的。TaN層403作為磁阻層(即刻蝕磁性材料層402形成的)的保護(hù)層,避免磁阻層暴露在空氣中而遭到氧化腐蝕,擴(kuò)散阻擋層阻擋磁性材料向?qū)娱g介質(zhì)層401中擴(kuò)散,磁性材料層402用來形成磁阻層;然后通過化學(xué)氣相沉積工藝在TaN層403的表面形成硬掩膜層404,其中,所述硬掩膜層404的材質(zhì)為氮化硅或氮氧化硅,能夠起到刻蝕阻擋的作用,并且不會與磁性材料發(fā)生反應(yīng),能夠確保后續(xù)形成的各向異性磁阻的性能。所述硬掩膜層的厚度一般是所述氮化鉭的1.5~3倍,例如,所述磁性材料層為所述氮化鉭層為所述硬掩膜層為請繼續(xù)參照圖4A,在步驟S3中,形成的圖案化的光刻膠層405用于定義磁阻層的位置。由于溝槽深度較大,在形成硬掩膜層后,溝槽一般沒有填平,此時可以先經(jīng)過多次旋轉(zhuǎn)涂覆、靜止、烘烤過程,形成平坦表面的光刻膠層,然后經(jīng)過曝光、顯影等工藝形成圖案化的光刻膠層405。為了避免后續(xù)出現(xiàn)溝槽內(nèi)的光刻膠未完全顯影的情況以及期望留下光刻膠的溝槽側(cè)壁上沒有光刻膠的情況,也可以先在硬掩膜層404上形成具有平坦表面的有機(jī)材料層(未圖示),有機(jī)材料層填充滿溝槽,并覆蓋溝槽周圍的硬掩膜層404上表面,為后續(xù)形成光刻膠提供平坦表面,便于后續(xù)光刻膠圖案的形成,確保光刻膠的圖案精細(xì),然后在有機(jī)材料層上形成圖案化的光刻膠層405,之后先等離子體刻蝕有機(jī)材料層,由于溝槽內(nèi)部的填充材料層的厚度明顯大于溝槽周圍表面上的有機(jī)材料層,這樣,溝槽周圍表面上的有機(jī)材料層先遭到去除,繼續(xù)刻蝕溝槽中有機(jī)材料層,在該過程中,等離子體化的刻蝕氣體也轟擊硬掩膜層404,硬掩膜層404阻擋了刻蝕氣體對TaN層403的轟擊,在圖案化的光刻膠層405的上表面和側(cè)面不會沉積含Ta聚合物,最終將圖案化的光刻膠層405的圖案轉(zhuǎn)移到有機(jī)材料層上,然后才能繼續(xù)刻蝕硬掩膜層404。請參考圖4B,在步驟S4中,以圖案化的光刻膠層405為掩模,等離子體干法刻蝕或者反應(yīng)離子干法刻蝕硬掩膜層404,將圖案化的光刻膠層405的圖案轉(zhuǎn)移到硬掩膜層404上,刻蝕后剩余的硬掩膜層404覆蓋于氮化鉭層403表面起到隔離的作用,以避免光刻膠與氮化鉭發(fā)生反應(yīng)產(chǎn)生聚合物。進(jìn)一步的,對硬掩膜層404的干法刻蝕為各向同性的干法刻蝕,既能有效的去除位于溝槽側(cè)壁且未被光刻膠層405覆蓋的部分,同時也不會因為陰影效應(yīng)而使得最終磁傳感器的尺寸不容易控制。硬掩膜層404刻蝕過程中,等離子體在一定程度上會轟擊氮化鉭層403表面,其表面脫離的Ta與光刻膠和有機(jī)填充材料反應(yīng)生成少量的含Ta聚合物405a。優(yōu)選的,采用氯、氧混合等離子體刻蝕所述硬掩膜層404,與現(xiàn)有技術(shù)中的普通干法刻蝕相比,一方面對氮化鉭層403轟擊力量減弱,氮化鉭層403的表面損傷較小,另一方面,可以抑制脫離出來的Ta等導(dǎo)電離子與光刻膠和有機(jī)填充材料的化學(xué)反應(yīng),從而減少了產(chǎn)生的含Ta聚合物的產(chǎn)生。請參考圖4C,在步驟S5中,以剩余的硬掩膜層404為掩膜,采用離子束物理轟擊刻蝕工藝(IBE刻蝕)依次刻蝕氮化鉭層403和磁性材料層402,形成磁阻層,磁阻層形成在位于溝槽的一側(cè)側(cè)壁表面、與對應(yīng)側(cè)壁相連的溝槽底部的部分表面、和位于溝槽外且與對應(yīng)側(cè)壁相連的頂部部分表面,所述離子束物理轟擊刻蝕的工藝參數(shù)包括:工藝氣體為Ar,氣體流量為10sccm~100sccm,射頻功率為300W~800W。由于采用離子束物理轟擊刻蝕工藝,所以當(dāng)以所述硬掩膜層為掩膜,對所述氮化鉭層404和磁性材料層進(jìn)行刻蝕時,不僅能夠很好地控制刻蝕速度和刻蝕深度,在對氮化鉭層403進(jìn)行物理刻蝕的時候,刻蝕停留于所述磁性材料層402,并將之前已堆積于溝槽側(cè)壁上的含鉭聚合物刻蝕掉,提高了溝槽側(cè)壁的平滑垂直性,進(jìn)而提高了器件的可靠性;而且刻蝕用離子束不會同氮化鉭層403發(fā)生化學(xué)反應(yīng),從而避免再次產(chǎn)生大量難以去除的含鉭聚合物。此外,物理轟擊刻蝕過程中,溝槽側(cè)壁受到的側(cè)向刻蝕較少,邊緣平整,硬掩膜層的厚度保護(hù)了其覆蓋部分的氮化鉭層和磁阻層,進(jìn)一步提高了溝槽側(cè)壁的平滑垂直性。再者,硬掩膜層404的厚度能夠保護(hù)氮化鉭層和磁阻層的同時,還不會形成陰影效應(yīng),使得最終形成的氮化鉭層和磁阻層的尺寸與硬掩膜層的尺寸相當(dāng)。該步驟后,圖案化的光刻膠層405及其他有機(jī)填充材料的表面可能僅殘留有較少的含鉭聚合物405a。請參考圖4C和4D,在步驟S6中,可以依次進(jìn)行低溫灰化工藝和高溫灰化工藝兩步灰化工藝去除光刻膠等有機(jī)填充物以及殘留的含鉭聚合物405a。具體地,請參考圖4D,本實施例的步驟S8中,采用氟基氣體與高流量氧氣的混合氣體對器件表面進(jìn)行低溫灰化工藝處理,可以去除步驟S6之前的過程中在圖案化的光刻膠層405等有機(jī)填充材料暴露表面上產(chǎn)生的含鉭聚合物405a,同時避免了對氮化鉭層403的破壞,防止填充的圖案化的光刻膠層405及其他有機(jī)填充材料的硬化,有利于后續(xù)圖案化的光刻膠層405等有機(jī)填充材料的去除。所述低溫灰化工藝的工藝溫度低于200℃,例如85℃或者80℃~150℃中的任意溫度,氧氣流量范圍為100sccm~500sccm。經(jīng)驗證,85℃下低溫灰化工藝后聚合物殘留的去除較為徹底,且氮化鉭層403的表面性能以及圖案化的光刻膠層405等有機(jī)填充材料的硬度最佳;接著,通過高溫灰化工藝去除圖案化的光刻膠層等有機(jī)填充材料,該過程處于工藝溫度高于200℃的高溫氧氣氣氛中,光刻膠等有機(jī)填充材料均與氧氣反應(yīng)生成揮發(fā)性氣體被排出。請參考圖4D,在步驟S7中,由于離子束物理轟擊刻蝕工藝后溝槽內(nèi)部及溝槽周圍表面本身殘留的含鉭聚合物405a較少,所以在步驟S6的灰化工藝后,含鉭聚合物405a基本被去除干凈,而離子束物理轟擊以及灰化工藝后殘留物質(zhì)的成分主要是離子束物理轟擊時產(chǎn)生的氮化鉭、磁性材料顆粒物,通過去離子水沖洗器件表面就可以沖刷掉,同時還可以避免現(xiàn)有技術(shù)中的濕法清洗時高濃度清洗劑對暴露表面造成的腐蝕,保證了溝槽內(nèi)壁以及溝槽周圍的器件表面形貌,提高了器件性能。在本發(fā)明的其他實施例中,還可以在步驟S4之后,步驟S5之前,先去除產(chǎn)生含鉭聚合物的反應(yīng)物之一即硬掩膜層404上方的光刻膠及其他有機(jī)填充材料,在后續(xù)對氮化鉭層403進(jìn)行刻蝕時,沒有光刻膠等的存在,就不會產(chǎn)生含鉭聚合物,即對所述硬掩膜層404表面的圖案化光刻膠層進(jìn)行灰化工藝處理,工藝溫度為80℃~150℃,灰化氣體包括氧氣和CF4、C2F6、C4F8或CHF3等含氟氣體,含氟氣體的流量為10sccm~100sccm,所述氧氣的流量為100sccm~3000sccm,從而使后續(xù)暴露出的氮化鉭層表面較為清潔、光滑,提高了所制造的三軸磁傳感器的性能。請參考圖5,圖5為采用本發(fā)明的去離子水沖洗后溝槽處器件表面的SEM圖譜。將圖5與圖2對比可見,采用本發(fā)明的三軸磁傳感器的制造方法后獲得的溝槽處器件表面較為平滑,尤其是溝槽側(cè)壁及其側(cè)壁底部的表面,由此獲得的Z軸磁性傳感器靈敏度高、穩(wěn)定性好。綜上,本發(fā)明提供的三軸磁傳感器的制造方法,沉積了相對較厚的硬掩膜層,保護(hù)溝槽側(cè)壁的氮化鉭層以及磁阻層在后續(xù)刻蝕過程中不受破壞,且以硬掩膜層為掩膜,采用了離子束物理轟擊刻蝕工藝對所述氮化鉭層和磁性材料層進(jìn)行了刻蝕,在去除多余氮化鉭和磁性材料過程中,主要產(chǎn)生比較好去除的氮化鉭及磁性材料顆粒,不但避免了現(xiàn)有技術(shù)中普通等離子體刻蝕對氮化鉭層表面的損壞,抑制了難以去除的含鉭聚合物的產(chǎn)生以及側(cè)向刻蝕對溝槽側(cè)壁形貌的侵蝕,還去除了先前工藝中產(chǎn)生的含鉭聚合物,保證了氮化鉭層表面的光滑度,之后采用去離子水沖洗去除殘留的氮化鉭及磁性材料顆粒,改善了最終形成的溝槽形貌,從而提高了制造的三軸磁傳感器的性能。顯然,本領(lǐng)域的技術(shù)人員可以對發(fā)明進(jìn)行各種改動和變型而不脫離本發(fā)明的精神和范圍。這樣,倘若本發(fā)明的這些修改和變型屬于本發(fā)明權(quán)利要求及其等同技術(shù)的范圍之內(nèi),則本發(fā)明也意圖包含這些改動和變型在內(nèi)。