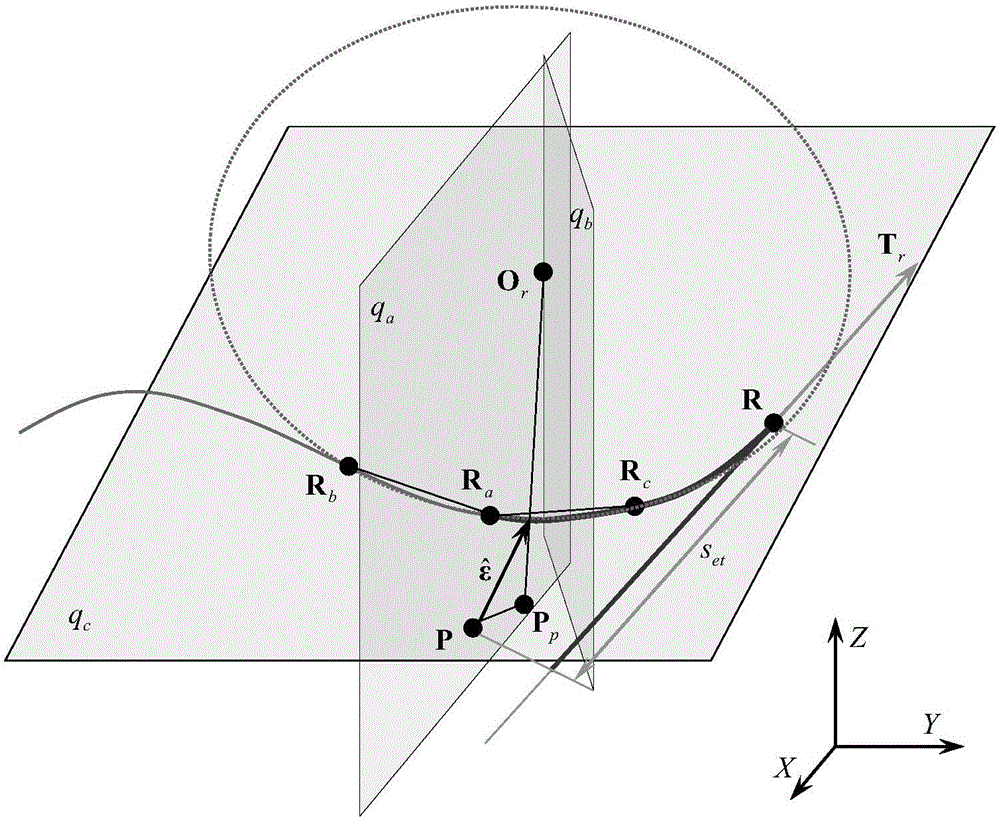
本發(fā)明屬于精密高效數(shù)控加工
技術(shù)領(lǐng)域:
,涉及一種樣條曲線插補(bǔ)加工過程中基于空間圓弧近似的輪廓誤差實(shí)時(shí)估計(jì)方法。
背景技術(shù):
:隨著高端裝備領(lǐng)域的快速發(fā)展,復(fù)雜曲面零件的高速數(shù)控加工技術(shù)應(yīng)用越來越廣。鑒于復(fù)雜曲面零件加工刀軌多為具有復(fù)雜幾何特征的曲線,采用傳統(tǒng)的直線、圓弧插補(bǔ)數(shù)控加工時(shí),由于直線、圓弧段逼近理想曲線時(shí)一階不連續(xù)點(diǎn)的存在,會導(dǎo)致數(shù)控加工過程中進(jìn)給軸的頻繁加減速,影響加工質(zhì)量和加工效率。參數(shù)樣條曲線直接插補(bǔ)技術(shù)可克服傳統(tǒng)直線、圓弧插補(bǔ)加工的缺陷,因此得到了廣泛研究。然而,在參數(shù)曲線直接插補(bǔ)過程中,由于各進(jìn)給軸伺服控制系統(tǒng)的滯后特性及動(dòng)態(tài)性能不匹配等原因,會引起較大的加工軌跡輪廓誤差,且該誤差隨著進(jìn)給速度的增加而增大,從而降低了復(fù)雜曲面零件的加工精度。為解決這一問題,國內(nèi)外學(xué)者提出了一系列先進(jìn)的控制算法,交叉耦合控制是其中的典型代表。交叉耦合控制器主要由輪廓誤差估計(jì)算法和控制律構(gòu)成,因此,高精度的輪廓誤差估計(jì)是保障交叉耦合控制器性能進(jìn)而提高數(shù)控系統(tǒng)輪廓跟蹤精度的前提。綜上,研究參數(shù)樣條曲線插補(bǔ)加工過程中輪廓誤差的實(shí)時(shí)高精度估計(jì)方法對實(shí)現(xiàn)復(fù)雜曲面零件的高效精密數(shù)控加工具有重要意義。文獻(xiàn)“ANovelContourErrorEstimationforPositionLoop-BasedCross-CoupledControl”,Yang等,IEEE/ASMETransactionsonMechatronics,2011,16(4):643-655,該文獻(xiàn)提出一種基于密切圓弧近似的輪廓誤差估計(jì)方法,然而,該方法只適用于二維平面輪廓,且當(dāng)隨動(dòng)誤差較大時(shí)估計(jì)精度較低;文獻(xiàn)“AReal-timecontouringerrorestimationformulti-axismotionsystemsusingthesecond-orderapproximation”,Zhu等,InternationalJournalofMachineToolsandManufacture,2013,68:75-80,該文獻(xiàn)提出一種基于點(diǎn)到曲線距離公式的二階近似空間輪廓誤差實(shí)時(shí)估計(jì)方法,然而該方法當(dāng)隨動(dòng)誤差較大時(shí)估計(jì)精度同樣較低,且估計(jì)算法獲得的為實(shí)際點(diǎn)到理想曲線的距離值,而非輪廓誤差矢量值。技術(shù)實(shí)現(xiàn)要素:本發(fā)明旨在克服現(xiàn)有技術(shù)缺陷,發(fā)明一種適用于參數(shù)樣條曲線插補(bǔ)器的空間輪廓誤差實(shí)時(shí)估計(jì)方法,該方法基于一階泰勒級數(shù)展開法計(jì)算參數(shù)曲線上用于擬合空間圓弧的特征點(diǎn),并構(gòu)造空間圓弧近似替代理想輪廓,從而計(jì)算輪廓誤差矢量值,實(shí)現(xiàn)空間輪廓誤差的高精度估計(jì)。本發(fā)明的技術(shù)方案是一種基于空間圓弧近似的輪廓誤差實(shí)時(shí)估計(jì)方法,其特性在于,該方法基于一階泰勒級數(shù)展開法計(jì)算參數(shù)樣條曲線上用于輪廓誤差估計(jì)的特征點(diǎn),再根據(jù)特征點(diǎn)擬合空間圓弧,并獲得其圓心坐標(biāo);最后,根據(jù)實(shí)際加工點(diǎn)與所擬合空間圓弧的位置關(guān)系,計(jì)算輪廓誤差矢量估計(jì)值;方法的具體步驟如下:第一步計(jì)算特征點(diǎn)設(shè)參數(shù)樣條曲線的方程為C=C(u),其中u為曲線參數(shù),當(dāng)前理想刀位點(diǎn)為R,對應(yīng)的曲線參數(shù)值為ur,實(shí)際刀位點(diǎn)為P,則隨動(dòng)誤差向量Et為:Et=R-P(1)為全面反映實(shí)際刀位點(diǎn)P附近理想曲線形貌,以隨動(dòng)誤差向量在曲線當(dāng)前理想刀位點(diǎn)處的切線方向上的投影長度為基準(zhǔn),根據(jù)一階泰勒級數(shù)展開法,確定參數(shù)曲線上用于空間圓弧擬合的第一個(gè)特征點(diǎn)Ra,以投影長度的1.5倍為基準(zhǔn),確定第二個(gè)特征點(diǎn)Rb,以投影長度的0.5倍為基準(zhǔn),確定第三個(gè)特征點(diǎn)Rc;Ra點(diǎn)處曲線參數(shù)ua的計(jì)算方法為:ua=ur-duds|u=urEt·Tr---(2)]]>其中,s為曲線弧長,Tr為理想刀軌在R點(diǎn)處的單位切失,參數(shù)u對s的導(dǎo)數(shù)為:duds|u=ur=1dsdu|u=ur=1||C′(ur)||---(3)]]>其中,C′(ur)為參數(shù)方程C(u)對參數(shù)u的導(dǎo)矢在ur處的值;Tr為:Tr=C′(ur)||C′(ur)||---(4)]]>將公式(1)、(3)、(4)帶入公式(2)得:ua=ur-(R-P)·C′(ur)||C′(ur)||2---(5)]]>因此Rb點(diǎn)處曲線參數(shù)ub為:ub=ur-32duds|u=urEt·Tr=3ua-ur2---(6)]]>Rc點(diǎn)處曲線參數(shù)uc為:uc=ur-12duds|u=urEt·Tr=ua+ur2---(7)]]>因此Ra、Rb、Rc點(diǎn)分別計(jì)算為Ra=C(ua),Rb=C(ub)及Rc=C(uc);根據(jù)特征點(diǎn)Ra、Rb及Rc實(shí)現(xiàn)空間圓弧的擬合;第二步擬合空間圓弧通過Ra、Rb和Rc三點(diǎn)所確定空間圓的圓心為線段RaRb的中垂面qa、線段RaRc的中垂面qb以及Ra、Rb、Rc三點(diǎn)所確定的平面qc三個(gè)平面的交點(diǎn),其中,平面qa的表達(dá)式為:(Ra-Rb)·xyz=(Ra-Rb)·(Ra+Rb)2---(8)]]>式中,(x,y,z)為平面上任一點(diǎn)的坐標(biāo)值;平面qb的表達(dá)式為:(Rc-Ra)·xyz=(Rc-Ra)·(Rc+Ra)2---(9)]]>平面qc的表達(dá)式為:(Rb-Rc)×(Ra-Rb)·xyz=(Rb-Rc)×(Ra-Rb)·Rc---(10)]]>設(shè)擬合空間圓的圓心為Or=[OxrOyrOzr]T,則其必滿足公式(8)、(9)和(10),因此圓心坐標(biāo)計(jì)算為:Or=12·(Ra-Rb)T(Rc-Ra)T((Rb-Rc)×(Ra-Rb))TT.(Ra-Rb)·(Ra+Rb)(Rc-Ra)·(Rc+Ra)2(Rb-Rc)×(Ra-Rb)·Rc---(11)]]>所構(gòu)造的空間圓弧即為以O(shè)r為圓心,以||Ra-Or||為半徑的在平面qc上的圓;第三步計(jì)算輪廓誤差矢量估計(jì)值令輪廓誤差估計(jì)值為實(shí)際刀位點(diǎn)P到第二步中所構(gòu)造空間圓弧的距離;因空間圓所在平面為qc,設(shè)qc面的單位法矢為nc,則:nc=(Rb-Rc)×(Ra-Rb)||(Rb-Rc)×(Ra-Rb)||---(12)]]>P點(diǎn)在qc平面上的投影點(diǎn)Pp為:Pp=P-(nc·(P-Ra))nc(13)將公式(12)代入(13)得Pp點(diǎn)為:Pp=P-((Rb-Rc)×(Ra-Rb)·(P-Ra))||(Rb-Rc)×(Ra-Rb)||2(Rb-Rc)×(Ra-Rb)---(14)]]>將輪廓誤差矢量的估計(jì)值表示為則根據(jù)實(shí)際刀位點(diǎn)P與擬合空間圓Or的幾何關(guān)系確定其計(jì)算公式為:ϵ^=(||R1-Or||||Pp-Or||-1)(Pp-Or)+Pp-P---(15)]]>在數(shù)控系統(tǒng)的每個(gè)插補(bǔ)周期內(nèi),根據(jù)插補(bǔ)器提供的參數(shù)曲線幾何信息及實(shí)際刀位點(diǎn)坐標(biāo),執(zhí)行上述步驟實(shí)現(xiàn)每一點(diǎn)處輪廓誤差矢量值的實(shí)時(shí)估計(jì)。本發(fā)明的有益效果是:建立了基于空間圓弧近似的輪廓誤差估計(jì)模型,為參數(shù)曲線插補(bǔ)空間軌跡加工輪廓誤差的實(shí)時(shí)高精度估計(jì)提供了有效途徑;在估計(jì)輪廓誤差時(shí)充分考慮了實(shí)際刀位點(diǎn)附近的理想刀軌形貌,在隨動(dòng)誤差較大時(shí)亦可保證輪廓誤差的估計(jì)精度。附圖說明圖1—空間刀軌輪廓幾何模型圖。圖2—輪廓誤差估計(jì)方法示意圖,其中,R為理想刀位點(diǎn),P為實(shí)際刀位點(diǎn),Tr為理想刀軌在R點(diǎn)處的單位切失,set為隨動(dòng)誤差在Tr方向上的投影長度,Ra為第一個(gè)特征點(diǎn),Rb為第二個(gè)特征點(diǎn),Rc為第三個(gè)特征點(diǎn),qa為線段RaRb的中垂面,qb為線段RaRb的中垂面,qc為Ra、Rb、Rc三點(diǎn)確定的平面,Or為擬合空間圓的圓心,Pp為P點(diǎn)在qc平面上的投影點(diǎn),為輪廓誤差矢量的估計(jì)值。圖3—本方法估計(jì)輪廓誤差與實(shí)際輪廓誤差的偏差圖,其中,X軸表示插補(bǔ)周期序號,Y軸表示偏差值,單位為mm。圖4—Zhu等人方法估計(jì)輪廓誤差與實(shí)際輪廓誤差的偏差圖;其中,X軸表示插補(bǔ)周期序號,Y軸表示偏差值,單位為mm。具體實(shí)施方式結(jié)合技術(shù)方案與附圖詳細(xì)說明本發(fā)明的具體實(shí)施方式。在參數(shù)樣條曲線直接插補(bǔ)過程中,由于各進(jìn)給軸伺服控制系統(tǒng)的滯后特性及動(dòng)態(tài)性能不匹配等原因,會引起較大的加工軌跡輪廓誤差,為提高加工輪廓精度,需在實(shí)時(shí)估計(jì)輪廓誤差的基礎(chǔ)上,進(jìn)行輪廓控制。據(jù)此,發(fā)明一種基于空間圓弧近似的高精度輪廓誤差實(shí)時(shí)估計(jì)方法。附圖1為空間刀軌輪廓幾何模型圖,以附圖1所示的非均勻有理B樣條空間刀軌輪廓為例,詳細(xì)說明本發(fā)明具體實(shí)施過程,該空間刀軌輪廓的非均勻有理B樣條參數(shù)為:階數(shù):2;控制點(diǎn):{(0,0,0);(-8,-20,0);(30,-5,-5);(60,-20,0);(47,0,0);(60,20,0);(30,5,-5);(-8,20,0);(0,0,0)};權(quán)因子:{1,0.9,0.75,1.5,6,3.5,1.8,1.5,1};節(jié)點(diǎn)向量:{0,0,0,0.15,0.3,0.45,0.6,0.75,0.85,1,1,1}。借助MATLAB/SIMULINK數(shù)值仿真平臺,建立三軸數(shù)控機(jī)床進(jìn)給伺服控制系統(tǒng)模型,X軸進(jìn)給控制系統(tǒng)的傳遞函數(shù)Gx(s)為:Gx(s)=6751.8S2+91.24s+6751.8---(16)]]>Y軸進(jìn)給控制系統(tǒng)的傳遞函數(shù)Gy(s)為:Gy(s)=6478.1S2+91.24s+6478.1---(17)]]>Z軸進(jìn)給控制系統(tǒng)的傳遞函數(shù)Gz(s)為:Gz(s)=7116.8S2+91.24s+7116.8---(18)]]>根據(jù)二階泰勒級數(shù)展開法對附圖1所示空間刀軌輪廓進(jìn)行曲線插補(bǔ),并在每一個(gè)插補(bǔ)周期內(nèi)依據(jù)理想刀位點(diǎn)R、實(shí)際刀位點(diǎn)P以及輪廓曲線參數(shù)信息,利用本方法實(shí)時(shí)估計(jì)輪廓誤差;附圖2為輪廓誤差估計(jì)方法示意圖,實(shí)施的具體過程如下:第一步,計(jì)算特征點(diǎn):根據(jù)公式(5)、(6)、(7)計(jì)算特征點(diǎn)參數(shù)ua、ub、uc,進(jìn)而獲得三個(gè)特征點(diǎn)Ra、Rb和Rc;第二步,擬合空間圓?。焊鶕?jù)第一步中獲得的特征點(diǎn)Ra、Rb和Rc,利用公式(8)、(9)、(10)獲得線段RaRb的中垂面qa、線段RaRc的中垂面qb以及Ra、Rb、Rc三點(diǎn)所確定平面qc,進(jìn)而利用公式(11)計(jì)算通過三個(gè)特征點(diǎn)的空間圓弧圓心Or坐標(biāo);第三步,計(jì)算輪廓誤差矢量估計(jì)值:根據(jù)公式(14)計(jì)算實(shí)際刀位點(diǎn)P在圓弧所在平面qc上的投影Pp,進(jìn)而利用公式(15)獲得輪廓誤差矢量的估計(jì)值在每個(gè)插補(bǔ)周期內(nèi)重復(fù)上述步驟,即可得到每個(gè)插補(bǔ)點(diǎn)處的輪廓誤差估計(jì)值,另外,利用離線非實(shí)時(shí)方法計(jì)算實(shí)際輪廓誤差真值,將本方法估計(jì)的輪廓誤差值與實(shí)際誤差值對比,得到二者偏差如附圖3所示;為說明本發(fā)明在輪廓誤差估計(jì)精度方面的優(yōu)勢,同樣采用Zhu等人在文獻(xiàn)“AReal-timecontouringerrorestimationformulti-axismotionsystemsusingthesecond-orderapproximation”,Zhu等,InternationalJournalofMachineToolsandManufacture,2013,68:75-80,中提出的基于點(diǎn)到曲線距離公式的二階空間輪廓誤差估計(jì)方法進(jìn)行輪廓誤差估計(jì),并將該方法的估計(jì)值與實(shí)際誤差值對比,得到偏差如附圖4所示;對比附圖3和附圖4可見,本方法的估計(jì)偏差最大值為0.0093mm,Zhu等人方法的估計(jì)偏差最大值為0.0899mm,說明了采用本方法可有效提高輪廓誤差估計(jì)精度,具有良好的輪廓誤差估計(jì)效果。本發(fā)明面向參數(shù)樣條曲線插補(bǔ)實(shí)際加工中對產(chǎn)生的輪廓誤差進(jìn)行補(bǔ)償與控制時(shí)高精度估計(jì)輪廓誤差的重大需求,發(fā)明了基于空間圓弧近似的輪廓誤差實(shí)時(shí)估計(jì)方法,對數(shù)控機(jī)床進(jìn)給伺服系統(tǒng)輪廓跟蹤精度的提高具有重大意義。當(dāng)前第1頁1 2 3