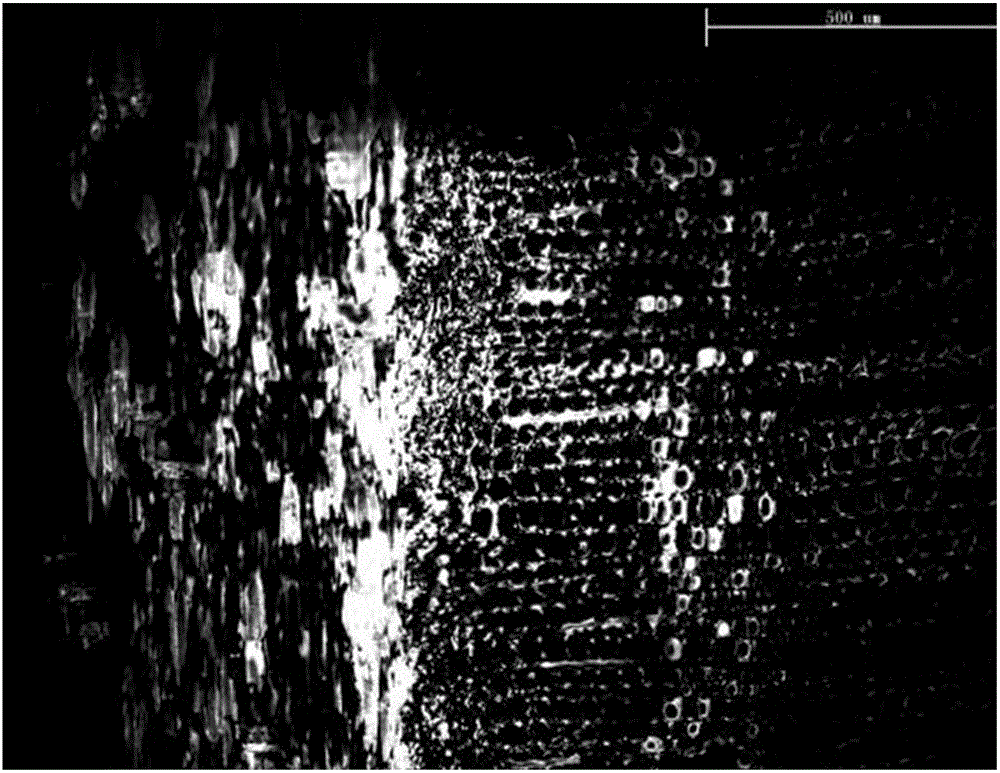
本發(fā)明涉及一種提高膠合強(qiáng)度的方法,特別涉及一種提高木質(zhì)材料膠合強(qiáng)度的方法及膠合板制備方法。
背景技術(shù):
:常規(guī)膠合板制造工藝包括原木截斷、蒸煮、旋切或者刨切、干燥、施膠、鋪裝、熱壓、冷卻、裁切和分選等工序。其中膠黏劑對膠合強(qiáng)度起著重要作用。在綜合考慮生產(chǎn)成本和膠合強(qiáng)度的因素下,膠合板生產(chǎn)一般使用脲醛樹脂膠黏劑。由于脲醛樹脂本身性能的影響,如低摩爾比、低游離醛樹脂和較低的固含量等因素都會導(dǎo)致膠合板的耐水性差和膠合強(qiáng)度(濕強(qiáng)度)的下降。同時,在常規(guī)制造工藝中,若采用膠黏劑的黏度不高,尤其不脫水膠粘劑,膠黏劑容易滲透到木質(zhì)單板中,且木材是多孔性材料,從而導(dǎo)致在膠層處的膠黏劑量明顯減少,不利于膠合。另一方面,熱固性膠粘劑通常在熱壓過程中,起初隨著溫度提高,膠粘劑粘度降低,X.Lu和A.Pizzi指出:當(dāng)膠層溫度達(dá)到60-80℃時,粘度最小,分散性達(dá)到最大,之后膠粘劑粘度急劇增加。粘度降低加大膠粘劑通過木材中的木射線或裂隙滲透[參考:X.LuandA.Pizzi,SubstrateInfluenceonTTTandCHTCuringDiagramsofWoodAdhesives,HolzalsRoh-undWerkstoff.56(5)(1998):339-346],導(dǎo)致膠合性能顯著降低。一些國內(nèi)外研究表明,如[作者為錢俊等,文獻(xiàn)名稱為:《電場對楊木膠合效應(yīng)之初探》,來自《浙江林學(xué)院學(xué)報》,1999,16(2):109-113;作者為錢俊等,文獻(xiàn)名稱為:《電場對楊木膠合效應(yīng)之再探》,來自《浙江林學(xué)院學(xué)報》,1999,16(2):293-296],其研究使用低壓條件制備膠合板,且膠黏劑是聚醋酸乙烯乳液,是非通用制備膠合板的膠黏劑,且膠合板的膠合強(qiáng)度提高效果不是很明顯;同時也未完全解決現(xiàn)有技術(shù)中存在的膠黏劑的粘度低、摩爾比低、木材多孔性導(dǎo)致的滲膠量大,木質(zhì)膠合材料的膠合強(qiáng)度不高,甲醛釋放量高等問題;尤其對于國內(nèi)采用的膠黏劑是未經(jīng)過脫水的,上述問題更加嚴(yán)重。技術(shù)實(shí)現(xiàn)要素:1.發(fā)明要解決的技術(shù)問題針對現(xiàn)有技術(shù)中存在的膠黏劑的粘度低、摩爾比低、木材多孔性導(dǎo)致的滲膠量大、木質(zhì)膠合材料的膠合強(qiáng)度低、甲醛釋放量和工作環(huán)境是否安全等技術(shù)問題,本發(fā)明公開了一種提高木質(zhì)材料膠合強(qiáng)度的方法及膠合板制備方法,通過在熱壓過程中利用高壓靜電場處理涂膠后的木質(zhì)材料,使木質(zhì)材料的兩側(cè)形成強(qiáng)大的靜電電壓,即使采用的膠黏劑是未經(jīng)過脫水的(固含量為等于或小于50%),處理后木質(zhì)膠合材料的膠合強(qiáng)度完全滿足要求,與采用普通膠合方法制備的木質(zhì)膠合材料相比膠合強(qiáng)度提高了一倍以上。2.技術(shù)方案發(fā)明原理:基于庫倫定律、靜電理論Vanutian規(guī)則和集聚原則,微小帶電粒子上若混有反極性的大粒子時,會使凝聚速度加快。在木質(zhì)材料膠合過程,進(jìn)行冷壓或熱壓,當(dāng)其溫度達(dá)到60℃~80℃時,膠黏劑的黏度達(dá)到最低,加高壓靜電,在高壓靜電場的作用下,甲醛與尿素反應(yīng)進(jìn)一步完善(見圖3),由紅外圖譜得出:在低波數(shù)區(qū)段,1500-1575cm-1為酰胺ΙΙ帶,其特征峰逐漸移向低波數(shù),說明反應(yīng)強(qiáng)度變大,反應(yīng)更加完全;在985-1035cm-1內(nèi),波峰強(qiáng)度逐漸增強(qiáng),說明了羥甲基含量增加,使固化后的膠黏劑交聯(lián)密度上升。再之,在高壓靜電條件下,膠黏劑分子極性化和取向化,從而獲得了更多的化學(xué)鍵,增加了尿素與甲醛的反應(yīng)幾率。最終,膠黏劑發(fā)生集聚現(xiàn)象,并于木質(zhì)材料膠接面上凝聚,從而提高木質(zhì)材料的膠合強(qiáng)度,降低了甲醛釋放量;而低壓靜電無法促使膠黏劑取向化和集聚,且未完全解決現(xiàn)有技術(shù)中存在的膠黏劑的粘度低、摩爾比低、木材多孔性導(dǎo)致的滲膠量大、木質(zhì)膠合材料的膠合強(qiáng)度不高和甲醛釋放量等問題;尤其對于國內(nèi)采用的膠黏劑是未經(jīng)過脫水的,上述問題更加嚴(yán)重。因此,對于膠合強(qiáng)度沒有明顯的作用。為解決上述技術(shù)問題,本發(fā)明通過下述實(shí)施方案來實(shí)現(xiàn):一種提高木質(zhì)材料膠合強(qiáng)度的方法,其步驟包括:涂膠后的木質(zhì)材料在其加壓過程中,對涂膠后的木質(zhì)材料兩側(cè)加高壓靜電,形成最終木質(zhì)膠合材料。優(yōu)選的在加壓過程中,在熱壓過程中對涂膠后的木質(zhì)材料沿?zé)釅悍较虻膬蓚?cè)加高壓靜電。優(yōu)選的高壓靜電,即接電后,涂膠后的木質(zhì)材料兩側(cè)的電壓差至少為1kV。如,通過高壓靜電發(fā)生器接負(fù)極板于涂膠后的木質(zhì)材料上側(cè),負(fù)壓為至少1kV(千伏)以上;接地極板為0kV于涂膠后的木質(zhì)材料下側(cè)。優(yōu)選的對涂膠后的木質(zhì)材料兩側(cè)加高壓靜電,其處理時間至少為200s以上;且通過高壓靜電發(fā)生器接負(fù)極板于涂膠后的木質(zhì)材料上側(cè),接地極板于涂膠后的木質(zhì)材料下側(cè)。優(yōu)選的木質(zhì)材料的含水率為8±3%;高壓靜電處理時間為300s至500s。優(yōu)選的所述涂膠后的木質(zhì)材料,其采用的膠黏劑是未經(jīng)脫水的,固含量等于或小于50%。一種膠合板制備方法,包括以下步驟:(1)將木材旋切或者刨切成木質(zhì)單板;(2)對步驟(1)中處理后的木質(zhì)單板進(jìn)行干燥;(3)對步驟(2)中處理后的木質(zhì)單板進(jìn)行涂飾膠黏劑,且在膠黏劑中加入固化劑氯化銨;(4)對步驟(3)中處理后的木質(zhì)單板進(jìn)行組坯;(5)對步驟(4)中處理后的板坯進(jìn)行熱壓,沿?zé)釅悍较驅(qū)Π迮鲀蓚?cè)加高壓靜電,將高壓靜電發(fā)生器接負(fù)極板于板坯上側(cè),負(fù)壓為1-15kV以上;接地極板為0kV于板坯下側(cè);(6)對步驟(5)中處理的板坯,達(dá)到靜電處理時間后立即關(guān)靜電;(7)對步驟(6)中處理后的板坯,達(dá)到熱壓時間后,卸壓、冷卻、裁邊和砂光處理,制得膠合板。優(yōu)選的,所述的步驟(1)中木質(zhì)單板的厚度為2.6-2.8mm;所述步驟(2)的干燥,在干燥箱中進(jìn)行的,干燥溫度為50℃,時間為12h,終含水率為8±3%。優(yōu)選的,所述的步驟(3)處所述的膠黏劑為脲醛樹脂,不經(jīng)過脫水處理,固含量為小于等于50%,甲醛與尿素的摩爾比為1.5,氯化銨是脲醛樹脂的重量的0.5-1.5%,雙面施膠量為200-300g/m2。優(yōu)選的,步驟(4)中所述板坯為縱-橫-縱三層或奇數(shù)層組坯方式,其熱壓條件為95℃-110℃,單位壓力為1MPa,熱壓時間20-60s/mm;步驟(6)高壓靜電處理時間為300s-500s。3.有益效果通過利用高壓靜電場處理木質(zhì)材料膠合,影響膠黏劑的分布、定向和運(yùn)動,從而使木質(zhì)材料兩側(cè)的膠黏劑產(chǎn)生集聚現(xiàn)象,解決了低摩爾比膠黏劑對于木質(zhì)材料膠合性能差和耐水性差的問題,以及減少了木材自身多孔性缺陷的影響,獲得了木質(zhì)膠合材料膠合強(qiáng)度倍增的效果,大大減少了膠黏劑和木材本身對木質(zhì)膠合材料的不利影響,顯著地提高了膠合強(qiáng)度,得到了高性能的木質(zhì)膠合材料。同時利用高壓靜電條件處理熱壓過程中的木質(zhì)材料,不僅提高木質(zhì)膠合材料的膠合強(qiáng)度,而且高壓靜電法消耗功率小,從而實(shí)現(xiàn)了低成本、高性能木質(zhì)膠合材料的制備。附圖說明:圖1(a)為未加靜電處理制備的膠合板縱向和橫向單板(無裂隙度)膠接層處微觀構(gòu)造圖,其中,1—縱向單板,2—膠接層,3—橫向單板;圖1(b)為未加靜電處理制備的膠合板縱向和橫向單板(無裂隙度)膠接層處的膠黏劑在兩單板中分布狀態(tài)的微觀構(gòu)造圖(不含木材部分),其中白色部分為膠黏劑的分布形態(tài),圖片背景為黑色;圖2(a)為靜電處理500s后所制備的膠合板縱向和橫向單板(無裂隙度)膠接層處微觀構(gòu)造圖,其中,1—縱向單板,2—膠接層,3—橫向單板;圖2(b)為靜電處理500s后所制備的膠合板縱向和橫向單板(無裂隙度)膠接層處的膠黏劑在兩單板中分布狀態(tài)的微觀構(gòu)造圖(不含木材部分),其中白色部分為膠黏劑的分布形態(tài),圖片背景為黑色;圖3(a)為未加靜電處理制備的膠合板縱向和橫向單板(裂隙度38%)膠接層處微觀構(gòu)造圖,其中,1—縱向單板,2—膠接層,3—橫向單板;圖3(b)為未加靜電處理制備的膠合板縱向和橫向單板(裂隙度38%)膠接層處的膠黏劑在兩單板中分布狀態(tài)的微觀構(gòu)造圖(不含木材部分),其中白色部分為膠黏劑的分布形態(tài),圖片背景為黑色;圖4(a)為靜電處理500s后所制備的膠合板縱向和橫向單板(裂隙度38%)膠接層處微觀構(gòu)造圖,其中,1—縱向單板,2—膠接層,3—橫向單板;圖4(b)為靜電處理500s后所制備的膠合板縱向和橫向單板(裂隙度38%)膠接層處的膠黏劑在兩單板中分布狀態(tài)的微觀構(gòu)造圖(不含木材部分),其中白色部分為膠黏劑的分布形態(tài),圖片背景為黑色;圖5為未加靜電處理和靜電處理500s后制備的膠合板(裂隙度38%)中的脲醛樹脂的傅里葉變換紅外光譜圖。具體實(shí)施方式:實(shí)施例1:一種利用高壓靜電高效提高木質(zhì)膠合材料膠合強(qiáng)度的制造方法,包括如下步驟:1)刨切:刨切好的南方松單板(無裂隙度),其厚度為2.6-2.8mm的木質(zhì)單板,在干燥箱中進(jìn)行的,干燥溫度為50℃,時間為12h,終含水率為7%。2)涂膠:將干燥后的木質(zhì)單板進(jìn)行涂飾膠黏劑,且在膠黏劑中加入固化劑氯化銨,膠黏劑為脲醛樹脂,甲醛與尿素摩爾比為F/U=1.5,氯化銨是脲醛樹脂重量的1%,雙面施膠量為300g/m2,固含量為50%。3)組坯:按照膠合板的縱-橫-縱三層組坯方式,制備三層結(jié)構(gòu)膠合板的板坯。4)熱壓并加高壓靜電:將板坯放入壓機(jī)后,將高壓靜電發(fā)生器接負(fù)極板于板坯上側(cè),負(fù)壓為10kV;接地極板為0kV于板坯下側(cè),立即打開高壓靜電發(fā)生器,靜電處理時間分別為0s(未處理)、200s、300s和500s。熱壓條件為110℃,板坯壓力為1.0MPa,熱壓時間60s/mm(秒每毫米)。5)關(guān)閉靜電發(fā)生器:達(dá)到高壓靜電處理時間后關(guān)閉靜電發(fā)生器。6)卸壓:達(dá)到熱壓時間后,熱壓結(jié)束,卸壓取出板坯,然后冷卻、裁邊、和砂光處理,制的膠合板。按照實(shí)施例1的工序得到的木質(zhì)材料的膠合板檢測數(shù)據(jù)(GB/T17657-2013),如表1和表2所示;圖1(a)為未加靜電處理制備的膠合板縱向和橫向單板膠接層處微觀構(gòu)造圖,其中,縱向單板1,膠接層2,橫向單板3;以及圖1(b)為未加靜電處理制備的膠合板縱向和橫向單板膠接層處的膠黏劑在兩單板中分布狀態(tài)的微觀構(gòu)造圖(不含木材部分),其中白色部分為膠黏劑的分布形態(tài),圖片背景為黑色。而圖2(a)為靜電處理500s后所制備的膠合板縱向和橫向單板膠接層處微觀構(gòu)造圖,其中,縱向單板1,膠接層2,橫向單板3;圖2(b)為靜電處理500s后所制備的膠合板縱向和橫向單板膠接層處的膠黏劑在兩單板中分布狀態(tài)的微觀構(gòu)造圖(不含木材部分),其中白色部分為膠黏劑的分布形態(tài),圖片背景為黑色。從上述圖中反映出通過利用高壓靜電場處理木質(zhì)材料膠合,影響膠黏劑的分布、定向和運(yùn)動,從而使木質(zhì)材料兩側(cè)的膠黏劑產(chǎn)生集聚現(xiàn)象,解決了低摩爾比膠黏劑對于木質(zhì)材料膠合性能差和耐水性差的問題,以及減少了木材自身多孔性缺陷的影響,獲得了木質(zhì)膠合材料膠合強(qiáng)度倍增的效果,大大減少了膠黏劑和木材本身對木質(zhì)膠合材料的不利影響,顯著地提高了膠合強(qiáng)度。表1木質(zhì)材料膠合板的膠合強(qiáng)度檢測數(shù)據(jù)表2木質(zhì)材料的膠合板甲醛釋放量檢測數(shù)據(jù)靜電處理時間(s)甲醛釋放量(mg/L)035002.7實(shí)施例2:一種利用高壓靜電高效提高木質(zhì)膠合材料膠合強(qiáng)度的制造方法,包括如下步驟:實(shí)施步驟同實(shí)施例1,不同在于,1)旋切:旋切好的木質(zhì)單板(裂隙度38%),其厚度為2.6-2.8mm的單板,含水率為7%。2)涂膠:膠黏劑為脲醛樹脂,甲醛與尿素摩爾比為F/U=1.5,氯化銨是脲醛樹脂重量的1.5%,雙面施膠量為300g/m2,固含量為47%。3)組坯:按照膠合板的組坯方式,制備三層結(jié)構(gòu)膠合板。4)熱壓并加高壓靜電:將高壓靜電發(fā)生器接負(fù)極板于板坯上側(cè),負(fù)壓為10kV;接地極板為0kV于板坯下側(cè)。將板坯放入壓機(jī)后,立即打開靜電發(fā)生器,靜電處理時間分別為0s、300s和500s。熱壓條件為110℃,板坯壓力為1.0MPa,熱壓時間60s/mm。5)關(guān)閉靜電發(fā)生器:達(dá)到高壓靜電處理時間后關(guān)閉靜電發(fā)生器6)卸壓:熱壓結(jié)束后,卸壓取出板坯,然后冷卻、裁邊、砂光處理,制的膠合板。按照實(shí)施例2的工序得到的木質(zhì)材料膠合板的檢測數(shù)據(jù)(GB/T17657-2013),如表3所示;圖3(a)為未加靜電處理制備的膠合板縱向和橫向單板膠接層處微觀構(gòu)造圖,其中,縱向單板1,膠接層2,橫向單板3;圖3(b)為未加靜電處理制備的膠合板縱向和橫向單板膠接層處的膠黏劑在兩單板中分布狀態(tài)的微觀構(gòu)造圖(不含木材部分),其中白色部分為膠黏劑的分布形態(tài),圖片背景為黑色。圖4(a)為靜電處理500s后所制備的膠合板縱向和橫向單板膠接層處微觀構(gòu)造圖,其中,縱向單板1,膠接層2,橫向單板3;圖4(b)為靜電處理500s后所制備的膠合板縱向和橫向單板膠接層處的膠黏劑在兩單板中分布狀態(tài)的微觀構(gòu)造圖(不含木材部分),其中白色部分為膠黏劑的分布形態(tài),圖片背景為黑色;圖5為未加靜電處理和靜電處理500s后制備的膠合板中的脲醛樹脂的傅里葉變換紅外光譜圖。從上述圖中反映出,在高壓靜電條件下,膠黏劑分子極性化和取向化,從而獲得了更多的化學(xué)鍵,增加了尿素與甲醛的反應(yīng)幾率。最終,膠黏劑發(fā)生集聚現(xiàn)象,并于木質(zhì)材料膠接面上凝聚,從而提高木質(zhì)材料的膠合強(qiáng)度。由紅外圖譜得出:在高壓靜電場的作用下,甲醛與尿素反應(yīng)進(jìn)一步完善,在低波數(shù)區(qū)段,1500-1575cm-1為酰胺ΙΙ帶,其特征峰逐漸移向低波數(shù),說明反應(yīng)強(qiáng)度變大,反應(yīng)更加完全;在985-1035cm-1內(nèi),波峰強(qiáng)度逐漸增強(qiáng),說明了羥甲基含量增加,使固化后的膠黏劑交聯(lián)密度上升。表3木質(zhì)材料膠合板的膠合強(qiáng)度檢測數(shù)據(jù)由于實(shí)施例1的表1中的單板選用的是南方松單板,即無裂隙度;而實(shí)施例2中的板坯材料選用的是旋切單板,有裂隙度,裂隙度為38%。一部分膠黏劑會遺留在裂隙中,因此膠合強(qiáng)度提高率會降低,但都高于現(xiàn)有的試驗(yàn)數(shù)據(jù)。實(shí)施例3:步驟同實(shí)施例2,在干燥箱中進(jìn)行的,干燥溫度為50℃,時間為12h,終含水率為8%。區(qū)別在于膠黏劑的固含量50%,甲醛與尿素摩爾比為F/U=1.5,氯化銨是脲醛樹脂重量的0.5%,雙面施膠量為200g/m2。按照實(shí)施例3的工序得到的木質(zhì)材料的檢測數(shù)據(jù)(GB/T17657-2013),如表4所示:表4木質(zhì)材料膠合板的膠合強(qiáng)度檢測數(shù)據(jù)實(shí)施例4:步驟同實(shí)施例2,區(qū)別在于膠黏劑的固含量50%,甲醛與尿素摩爾比為F/U=1.5,氯化銨是脲醛樹脂重量的1%,熱壓溫度為95℃。按照實(shí)施例4的工序得到的木質(zhì)材料的檢測數(shù)據(jù)(GB/T17657-2013),如表5所示:表5木質(zhì)材料膠合板的膠合強(qiáng)度檢測數(shù)據(jù)實(shí)施例5:步驟同實(shí)施例2,在干燥箱中進(jìn)行的,干燥溫度為50℃,時間為12h,終含水率為5%。區(qū)別在于膠黏劑的固含量50%,甲醛與尿素摩爾比為F/U=1.5,氯化銨是脲醛樹脂重量的1%,奇數(shù)層組坯方式為五層結(jié)構(gòu)膠合板,熱壓溫度為100℃。按照實(shí)施例5的工序得到的木質(zhì)材料的檢測數(shù)據(jù)(GB/T17657-2013),如表6所示:表6木質(zhì)材料膠合板的膠合強(qiáng)度檢測數(shù)據(jù)實(shí)施例6:步驟同實(shí)施例2,區(qū)別在于膠黏劑的固含量50%,高壓靜電發(fā)生器接負(fù)極板于板坯上側(cè),負(fù)壓為1kV;接地極板為0kV于板坯下側(cè)。得到的板坯均按照GB/T17657-2013進(jìn)行檢測。高壓靜電處理后的膠合板的膠合強(qiáng)度高于未加靜電的板坯強(qiáng)度,且高壓靜電處理后的膠合板膠合強(qiáng)度均符合標(biāo)準(zhǔn)要求。實(shí)施例7:步驟同實(shí)施例2,區(qū)別在于,在干燥箱中進(jìn)行的,干燥溫度為50℃,時間為12h,終含水率為11%。膠黏劑的固含量50%,高壓靜電發(fā)生器接負(fù)極板于板坯上側(cè),負(fù)壓為15kV;接地極板為0kV于板坯下側(cè)。得到的板坯均按照GB/T17657-2013進(jìn)行檢測。高壓靜電處理后的膠合板的膠合強(qiáng)度高于未加靜電的板坯強(qiáng)度,且高壓靜電處理后的膠合板膠合強(qiáng)度均符合標(biāo)準(zhǔn)要求。實(shí)施例8:步驟同實(shí)施例2,區(qū)別在于,膠黏劑的固含量為50%,對板坯左側(cè)、右側(cè)加壓,高壓靜電發(fā)生器接負(fù)極板于板坯左側(cè),接負(fù)極板與板坯右側(cè)。得到的板坯均按照GB/T17657-2013進(jìn)行檢測。高壓靜電處理后的膠合板的膠合強(qiáng)度高于未加靜電的板坯強(qiáng)度,且高壓靜電處理后的膠合板膠合強(qiáng)度均符合標(biāo)準(zhǔn)要求。實(shí)施例9:步驟同實(shí)施例2,區(qū)別在于,膠黏劑的固含量為30%,得到的板坯均按照GB/T17657-2013進(jìn)行檢測。高壓靜電處理后的膠合板的膠合強(qiáng)度高于未加靜電的板坯強(qiáng)度,且高壓靜電處理后的膠合板膠合強(qiáng)度均符合標(biāo)準(zhǔn)要求。實(shí)施例10:步驟同實(shí)施例2,區(qū)別在于,膠黏劑的固含量為40%,得到的板坯均按照GB/T17657-2013進(jìn)行檢測。高壓靜電處理后的膠合板的膠合強(qiáng)度高于未加靜電的板坯強(qiáng)度,且高壓靜電處理后的膠合板膠合強(qiáng)度均符合標(biāo)準(zhǔn)要求。實(shí)施例11:一種利用高壓靜電高效提高木質(zhì)材料膠合強(qiáng)度的制造方法,包括如下步驟:1)旋切:旋切好的木質(zhì)單板(裂隙度38%),其厚度為2.6-2.8mm的單板,含水率為7%。2)涂膠:膠黏劑為酚醛樹脂,固含量50%,雙面施膠量為250g/m2。3)組坯:按照單板層積材的組坯方式,制備九層結(jié)構(gòu)單板層積材。4)熱壓并加高壓靜電:將高壓靜電發(fā)生器接負(fù)極板于板坯上側(cè),負(fù)壓為10kV;接地極板為0kV于板坯下側(cè)。將板坯放入壓機(jī)后,立即打開靜電發(fā)生器。熱壓條件為145℃,板坯單位壓力為1.0MPa,熱壓時間60s/mm。5)關(guān)閉靜電發(fā)生器:達(dá)到高壓靜電處理時間后關(guān)閉靜電發(fā)生器6)卸壓:熱壓結(jié)束后,卸壓取出板坯,然后冷卻、裁邊、分選。按照實(shí)施例11的工序得到的木質(zhì)材料的檢測數(shù)據(jù)(GB/T20241-2006),如表7所示:表7木質(zhì)材料的浸漬剝離率檢測數(shù)據(jù)實(shí)施例12:提高木質(zhì)材料膠合木膠合強(qiáng)度的制造方法,包括如下步驟:1)制材:鋸制好的南方松鋸材,其厚度和寬度分別為16mm和140mm,含水率為10%。2)涂膠:膠黏劑為間苯二酚-苯酚-甲醛共聚樹脂,固含量50%,雙面施膠量為250g/m2。3)組坯:按照膠合木的組坯方式,制備三層結(jié)構(gòu)膠合木的板坯。4)熱壓并加高壓靜電:將高壓靜電發(fā)生器接負(fù)極板于板坯上側(cè),負(fù)壓為10kV;接地極板為0kV于板坯下側(cè)。將板坯放入壓機(jī)后,立即打開靜電發(fā)生器。熱壓條件為145℃,板坯單位壓力為1.0MPa,熱壓時間60s/mm。5)關(guān)閉靜電發(fā)生器:達(dá)到高壓靜電處理時間后關(guān)閉靜電發(fā)生器6)卸壓:熱壓結(jié)束后,卸壓取出材料,然后冷卻、裁邊和分選,制備三層結(jié)構(gòu)膠合木。按照實(shí)施例12的工序得到的木質(zhì)材料的檢測數(shù)據(jù)(GB/T26899-2011)。高壓靜電處理后的木質(zhì)材料膠合木的膠合強(qiáng)度高于未加靜電的膠合木強(qiáng)度,且高壓靜電處理后的膠合強(qiáng)度均符合標(biāo)準(zhǔn)要求。當(dāng)前第1頁1 2 3