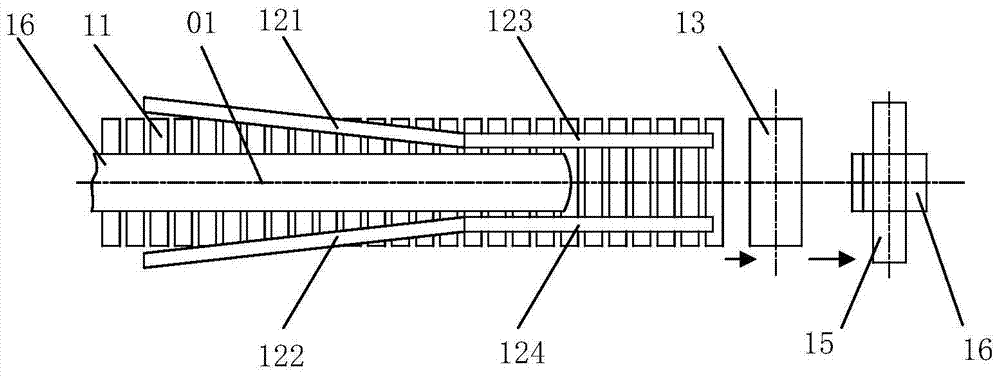
本發(fā)明涉及鋼帶熱連軋產(chǎn)線的卷取機控制工藝,尤其是指一種對熱軋卷取擦傷缺陷的控制方法,適用于立式運輸?shù)臒彳埳a(chǎn)線。
背景技術:卷取機是熱軋生產(chǎn)線的重要設備,用于將軋制的成品熱軋帶鋼卷成鋼卷。卷取機位于精軋機組后,為熱連軋生產(chǎn)線的最后一道工序。請參照圖1a-圖1b,卷取機主要包括輥道11,側導板12,夾送輥13,三根助卷輥14及卷筒15等主要設備。其中輥道11主要負責將帶鋼16由精軋機組輸送至卷取機;側導板12主要作用是對中帶鋼16;夾送輥13的主要作用是在頭部咬鋼階段對帶鋼16施加一定的夾緊力,同時對其實施第一次彎曲變形,在尾部卷取階段對帶鋼16施加穩(wěn)定的張力,以保證良好的卷形質(zhì)量;助卷輥14幫助彎曲帶鋼16,并使帶鋼16緊緊纏繞上卷筒15;卷筒15是卷取機的核心設備,在帶鋼16纏繞上后,對其施加前向張力,以確保帶鋼卷形質(zhì)量合格。現(xiàn)有的側導板12包含傳動側側導板及操作側側導板,傳動側側導板由傳動側斜導板121及傳動側平行導板123組成,操作側側導板由操作側斜導板122、及操作側平行導板124組成。圖1b中的標記01是指軋制中心線,圖1a-圖1b中箭頭所示帶鋼16的走向(以下有關附圖的箭頭一樣所示)?,F(xiàn)有技術在任何情況下,操作側和傳動側的側導板都采用對稱的開度設定。卷取機設備生產(chǎn)中一般存在塔形缺陷及卷取擦傷缺陷。參見圖2a-圖2c,卷取機塔形缺陷是指帶鋼16卷成鋼卷(圖2a所示)后其內(nèi)圈卷層向一側凸出的外觀缺陷,向操作側凸出稱操作側塔形鋼卷161(圖2b所示),向傳動側凸出稱傳動側塔形鋼卷162(圖2c所示)。參見圖3,在采用立式運輸?shù)臒彳埳a(chǎn)線上,鋼卷在卷取完畢以后,需要向操作側翻轉(zhuǎn)90度,卷取機擦傷缺陷是指存在操作側塔形的鋼卷在向操作側翻轉(zhuǎn)過程中,操作側塔形161會在鋼卷自重的作用下被壓入鋼卷內(nèi)圈(圖3中箭頭所示的是翻轉(zhuǎn)過程),在此過程中,鋼卷內(nèi)圈各層的表面會產(chǎn)生相互摩擦,產(chǎn)生相互擦傷的缺陷。目前,操作側和傳動側的側導板都采用對稱的開度設定方式:所述開度是指一側的平行導板邊與軋制中心線之間的距離。參見圖4a-圖4b,在帶鋼16的頭部到達側導板出口前,傳動側側導板和操作側側導板被對稱地設定在相同的開度上,即,傳動側側導板的開度=(帶鋼寬度/2)+S1,其中,S1為傳動側平行導板邊與軋制中心線之間的距離減去帶鋼寬度/2);操作側側導板的開度=(帶鋼寬度/2)+S2,其中,S2為操作側平行導板邊與軋制中心線之間的距離減去帶鋼寬度/2。一般,S1=S2=S(該″S″一般為40mm)。當帶鋼頭部通過側導板出口時,如圖4b所示,操作側和傳動側的側導板同時快速關閉(S=0),當帶鋼尾部通過側導板后(圖4a),操作側和傳動側的側導板同時打開。也就是說現(xiàn)有技術中,傳動側的側導板和操作側的側導板始終與軋制中心線01保持相等的距離,即采用對稱側導板控制方法。該對稱側導板控制方法存在以下問題:1)在帶鋼頭部到達側導板出口以前,側導板的開度大于帶鋼的寬度,帶鋼在側導板開度范圍內(nèi)處于自由狀態(tài)。帶鋼會向任意一側游動,游動至操作側時,就產(chǎn)生了操作側塔形;游動至傳動側時,就產(chǎn)生了傳動側塔形。請參見圖5a-圖5b,圖5a為帶鋼游動至操作側(A側)時就產(chǎn)生了操作側塔形161;圖5b為帶鋼游動至傳動側(B側)時就產(chǎn)生了傳動側塔形162。2)上述控制方法不可避免產(chǎn)生操作側塔形,帶鋼一旦游動至操作側產(chǎn)生了操作側塔形,操作側塔形就會在鋼卷自重的作用下被壓入鋼卷內(nèi)圈并產(chǎn)生卷取擦傷缺陷。為減少鋼卷在翻轉(zhuǎn)過程中產(chǎn)生的卷取擦傷缺陷,目前業(yè)內(nèi)熱軋產(chǎn)線多數(shù)采用改造運輸方式的辦法,即鋼卷運輸方式由立式改為臥式,鋼卷不需要經(jīng)過翻轉(zhuǎn),也就減少了翻轉(zhuǎn)過程中產(chǎn)生的卷取擦傷。但改變運輸方式需要對設備進行大規(guī)模改造,投資大、時間長。
技術實現(xiàn)要素:本發(fā)明的目的是為了解決現(xiàn)有技術存在的問題,提供一種對熱軋卷取擦傷缺陷的控制方法,通過對側導板的控制,達到減少操作側塔形缺陷,進而減少鋼卷翻轉(zhuǎn)過程中產(chǎn)生卷取擦傷缺陷的目的。本發(fā)明的目的是通過以下技術方案實現(xiàn)的:一種對熱軋卷取擦傷缺陷的控制方法,其包含以下步驟:S1,帶鋼咬入精軋機組的F1機架,檢測F1機架軋制力變化,判斷F1機架的機架軋制力是否達到限幅,如果沒有達到,繼續(xù)等待,直至F1機架的機架軋制力達到限幅;S2,判斷F1機架是否已咬鋼,如果沒有咬鋼繼續(xù)等待,直至F1機架已咬鋼;S3,將咬鋼信號上傳至上位機,上位機得到F1機架的咬鋼信號后,根據(jù)帶鋼的目標厚度和卷取溫度下發(fā)給卷取機組;S4,判斷帶鋼是否滿足以下條件:帶鋼卷取的目標厚度≤6mm且卷取溫度≥680℃;S5,如果上述步驟S4中,滿足帶鋼卷取的目標厚度≤6mm且卷取溫度≥680℃的條件時,采用對熱軋卷取擦傷缺陷的控制方法,其包含:S51,在帶鋼頭部到達側導板出口前,傳動側側導板的開度=(帶鋼寬度/2)+2S,操作側側導板的開度=帶鋼寬度/2,其中2S是指傳動側平行導板邊與軋制中心線之間的距離減去帶鋼寬度/2,2S=80mm;S52,等待到帶鋼檢測裝置檢測到帶鋼頭部通過側導板出口的信號后進行下面步驟;S53,傳動側側導板的開度=帶鋼寬度/2,操作側側導板的開度還是為帶鋼寬度/2;S54,等待到帶鋼檢測裝置檢測到帶鋼尾部通過側導板出口的信號后進行下面步驟;S55,傳動側側導板的開度=(帶鋼寬度)/2+2S,操作側側導板的開度還是為帶鋼寬度/2,流程結束,等待下一塊帶鋼到達;S6,如果上述步驟S4中,不滿足帶鋼卷取的目標厚度≤6mm且卷取溫度≥680℃的條件時,采用熱軋卷取方法。所述步驟S2及步驟S3中,均由精軋基礎自動化計算機判斷F1機架是否已咬鋼,并將咬鋼信號上傳至上位機。所述步驟S3及步驟S4中,均由卷取機組的卷取基礎自動化計算機接收上位機下發(fā)的帶鋼目標厚度和卷取溫度的信號,并判斷帶鋼卷取的目標厚度≤6mm且卷取溫度≥680℃的條件是否滿足。所述熱軋卷取方法包含:S61,在帶鋼頭部到達側導板出口前,傳動側側導板的開度=(帶鋼寬度/2)+S1,其中,S1為傳動側平行導板邊與軋制中心線之間的距離減去帶鋼寬度/2;操作側側導板的開度=(帶鋼寬度/2)+S2,其中,S2為操作側平行導板邊與軋制中心線之間的距離減去帶鋼寬度/2);S1=S2=S,S取值40mm。S62,等待到帶鋼檢測裝置檢測到帶鋼頭部通過側導板出口的信號后進行下面步驟;S63,傳動側側導板的開度=帶鋼寬度/2,操作側側導板的開度=帶鋼寬度/2;S64,等待到帶鋼檢測裝置檢測到帶鋼尾部通過側導板出口的信號后進行下面步驟;S65,傳動側側導板的開度=(帶鋼寬度/2)+S,操作側的側導板開度=(帶鋼寬度/2)+S,流程結束,等待下一塊帶鋼到達。所述傳動側側導板的開度及操作側側導板的開度由卷取基礎自動化計算機控制。本發(fā)明的有益效果:本發(fā)明的方法是一種非對稱的側導板控制方法,應用于立式運輸?shù)臒彳埳a(chǎn)線,具有以下優(yōu)點:可以減少操作側塔形產(chǎn)生的幾率,進而減少鋼卷翻轉(zhuǎn)過程中產(chǎn)生卷取擦傷的缺陷;本方法對設備硬件改造的投入少,改造需用時間少,減少了改造投資成本。為進一步說明本發(fā)明的上述目的、結構特點和效果,以下將結合附圖對本發(fā)明進行詳細說明。附圖說明圖1a為卷取機結構示意圖;圖1b為圖1a的俯視圖;圖2a為圖1a中帶鋼卷成鋼卷后的示意圖;圖2b為圖2a的鋼卷出現(xiàn)向操作側凸出的操作側塔形鋼卷的右視圖;圖2c為圖2a的鋼卷出現(xiàn)向傳動側凸出的傳動側塔形鋼卷的右視圖;圖3為操作側塔形鋼卷翻轉(zhuǎn)90度被壓入鋼卷內(nèi)圈的狀態(tài)圖;圖4a為現(xiàn)有對稱側導板中帶鋼頭部到側導板出口前示意圖;圖4b為圖4a中帶鋼頭部通過側導板出口后的示意圖;圖5a為操作側塔形產(chǎn)生原因的示意圖;圖5b為傳動側塔形產(chǎn)生原因的示意圖;圖6a為本發(fā)明控制方法中帶鋼游動至操作側(A側)到達側導板出口前示意圖;圖6b為帶鋼游動至傳動側(B側)到達側導板出口前示意圖;圖7為本發(fā)明控制方法的工藝流程示意圖;圖8為本發(fā)明對熱軋卷取擦傷缺陷的控制方法的步驟圖。具體實施方式下面結合實施例的附圖對本發(fā)明的具體實施方式進行詳細說明。要防止出現(xiàn)操作側塔形,就必須限制帶鋼向操作側的自由游動。為此可以通過減小操作側的側導板的開度就可以限制帶鋼向操作側游動的范圍,當操作側的側導板的開度減小到只有帶鋼寬度的1/2時,就可以有效地防止操作側塔形的產(chǎn)生。要保證帶鋼頭部被側導板順利導入卷取機,在帶鋼頭部到達前,側導板必須保持一個足夠的開度。所以,在減小操作側的側導板的開度的同時,必須適當增加傳動側的側導板的開度。參見圖6a-圖6b,帶鋼頭部到達側導板出口前(圖6a),傳動側側導板的開度=(帶鋼寬度/2)+2S,操作側側導板的開度=帶鋼寬度/2,其中2S是指傳動側平行導板邊與軋制中心線之間的距離減去帶鋼寬度/2,2S=80mm(以下相同)。當帶鋼頭部通過側導板出口時,傳動側的側導板快速關閉2S,傳動側的側導板的開度維持不變。當帶鋼尾部通過側導板出口后,傳動側側導板打開2S,操作側側導板的開度維持不變。因本發(fā)明的控制方法會增加傳動側塔形的程度,并且卷取擦傷通常只發(fā)生在厚度較薄,卷取溫度較高的帶鋼上,所以本發(fā)明的控制方法只在薄規(guī)格,高卷取溫度的帶鋼上使用,一般當卷取帶鋼的厚度≤6mm且卷取溫度≥680℃時采用本方法。請參見圖7,本發(fā)明控制方法的具體工藝流程如下:帶鋼16咬入精軋機組20的F1機架21,壓力檢測設備22檢測到F1機架21軋制力變化,精軋基礎自動化計算機23判斷F1機架21咬鋼,并將咬鋼信號上傳至上位機30;上位機30得到F1機架21的咬鋼信號以后,根據(jù)帶鋼的目標厚度和卷取溫度下發(fā)給卷取機組10的卷取基礎自動化計算機17;卷取基礎自動化計算機17根據(jù)帶鋼的厚度和卷取溫度進行判斷,當滿足卷取帶鋼的目標厚度≤6mm且卷取溫度≥680℃時,采用對熱軋卷取擦傷缺陷的控制方法;當不滿足卷取帶鋼的目標厚度≤6mm且卷取溫度≥680℃時,采用傳統(tǒng)熱軋卷取方法(如背景技術中采用的方法);卷取基礎自動化計算機17根據(jù)帶鋼寬度,計算傳動側平行導板123的開度設定值=(帶鋼寬度/2)+2S(S=40mm),通過傳動側側導板伺服閥系統(tǒng)127控制傳動側側導板油缸125,使傳動側平行導板123的實際開度到達設定值;內(nèi)置于傳動側側導板油缸125內(nèi)的傳動側側導板位置傳感器129檢測傳動側平行導板123的實際位置并反饋給卷取基礎自動化計算機17。卷取基礎自動化計算機17根據(jù)帶鋼寬度計算操作側平行導板124的開度設定值=帶鋼寬度/2,通過操作側側導板伺服閥系統(tǒng)128控制操作側側導板油缸126,使操作側平行導板124的實際開度到達設定值;內(nèi)置于操作側側導板油缸126內(nèi)的操作側側導板位置傳感器130檢測操作側平行導板124的實際位置并反饋給基礎自動化計算機17。當安裝于側導板出口的帶鋼檢測裝置18檢測到帶鋼頭部時,卷取基礎自動化計算機17判斷帶鋼頭部通過側導板出口,傳動側平行導板123的開度設定值=帶鋼寬度/2(帶鋼檢測裝置18位于側導板出口,如果檢測到帶鋼,說明帶鋼已經(jīng)到達側導板的出口了),通過傳動側側導板伺服閥系統(tǒng)127控制傳動側側導板油缸125,使傳動側平行導板123的實際開度到達設定值,即傳動側的側導板快速關閉2S。操作側的平行導板124的開度設定值=帶鋼寬度/2,保持不動。當安裝于側導板出口的帶鋼檢測裝置18檢測到帶鋼尾部時,卷取基礎自動化計算機17判斷帶鋼尾部是否通過側導板出口,根據(jù)帶鋼寬度計算傳動側平行導板123的開度設定值=帶鋼寬度/2+2S,通過傳動側側導板伺服閥系統(tǒng)127控制傳動側側導板油缸125,使傳動側側平行導板123的實際開度到達設定值,即傳動側的側導板快速打開2S。卷取基礎自動化計算機17根據(jù)帶鋼寬度計算操作側的側導板124的開度設定值=帶鋼寬度/2,所以操作側的側導板123的開度不動。根據(jù)上述描述的本發(fā)明的工藝流程,參見圖8,本發(fā)明對熱軋卷取擦傷缺陷的控制方法的步驟包含:S1,帶鋼咬入精軋機組的F1機架,檢測F1機架軋制力變化,判斷F1機架的機架軋制力是否達到限幅,如果沒有達到,繼續(xù)等待,直至F1機架的機架軋制力達到限幅。S2,由精軋基礎自動化計算機判斷F1機架是否已咬鋼,如果沒有咬鋼繼續(xù)等待,直至F1機架已咬鋼。S3,由精軋基礎自動化計算機將咬鋼信號上傳至上位機,上位機得到F1機架的咬鋼信號后,根據(jù)帶鋼的目標厚度和卷取溫度下發(fā)給卷取機組的卷取基礎自動化計算機。S4,卷取基礎自動化計算機接收到帶鋼的目標厚度和卷取溫度信號后判斷是否滿足帶鋼卷取的目標厚度≤6mm且卷取溫度≥680℃的條件。S5,如果上述步驟S4中,滿足帶鋼卷取的目標厚度≤6mm且卷取溫度≥680℃的條件時,采用對熱軋卷取擦傷缺陷的控制方法,其包含:S51,由卷取基礎自動化計算機控制,在帶鋼頭部到達側導板出口前,傳動側側導板的開度=(帶鋼寬度/2)+2S,操作側側導板的開度=帶鋼寬度/2,其中2S是指傳動側平行導板邊與軋制中心線之間的距離減去帶鋼寬度/2,一般,2S=80mm(以下相同)。S52,等待到帶鋼檢測裝置檢測到帶鋼頭部通過側導板出口的信號后進行下面步驟。S53,由卷取基礎自動化計算機控制,使傳動側側導板的開度=帶鋼寬度/2,操作側側導板的開度還是為帶鋼寬度/2。S54,等待到帶鋼檢測裝置檢測到帶鋼尾部通過側導板出口的信號后進行下面步驟;S55,由卷取基礎自動化計算機控制,使傳動側側導板的開度=(帶鋼寬度)/2+2S,操作側側導板的開度還是為帶鋼寬度/2,流程結束(卷取結束,傳動側側導板2S還開著,等待下一塊帶鋼到達)。S6,如果上述步驟S4中,不滿足帶鋼卷取的目標厚度≤6mm且卷取溫度≥680℃的條件時,采用熱軋卷取方法,其包含:S61,由卷取基礎自動化計算機控制,在帶鋼頭部到達側導板出口前,傳動側側導板的開度=(帶鋼寬度/2)+S1,其中,S1為傳動側平行導板邊與軋制中心線之間的距離減去帶鋼寬度/2;操作側側導板的開度=(帶鋼寬度/2)+S2其中,S2為操作側平行導板邊與軋制中心線之間的距離減去帶鋼寬度/2);一般,S1=S2=S(該S取值40mm,下相同)。S62,等待到帶鋼檢測裝置檢測到帶鋼頭部通過側導板出口的信號后進行下面步驟。S63,由卷取基礎自動化計算機控制,使傳動側側導板的開度=帶鋼寬度/2,操作側側導板的開度=帶鋼寬度/2。S64,等待到帶鋼檢測裝置檢測到帶鋼尾部通過側導板出口的信號后進行下面步驟。S65,由卷取基礎自動化計算機控制,使傳動側側導板的開度=(帶鋼寬度/2)+S1,操作側的側導板開度=(帶鋼寬度/2)+S2,流程結束,等待下一塊帶鋼到達。本技術領域中的普通技術人員應當認識到,以上的實施例僅是用來說明本發(fā)明的目的,而并非用作對本發(fā)明的限定,只要在本發(fā)明的實質(zhì)范圍內(nèi),對以上所述實施例的變化、變型都將落在本發(fā)明的權利要求的范圍內(nèi)。