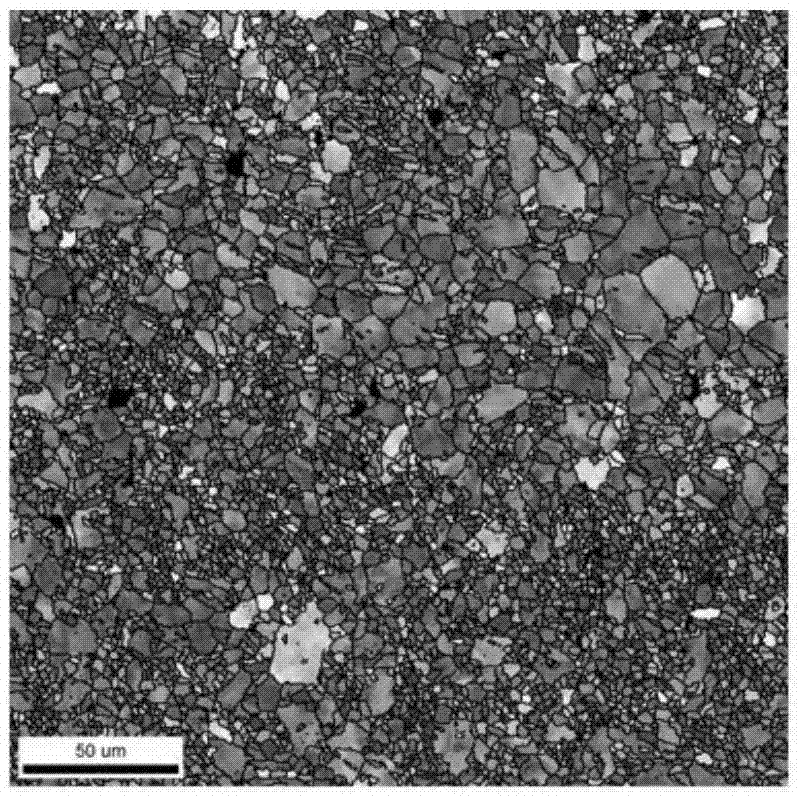
本發(fā)明涉及一種有色金屬加工工藝,尤其涉及一種用于鎂合金板材的軋制工藝。
背景技術(shù):
:鎂是迄今為止發(fā)現(xiàn)的最輕金屬結(jié)構(gòu)材料,為此,鎂合金作為一種新興的金屬結(jié)構(gòu)材料,在世界范圍內(nèi)有著豐富的資源。鎂的密度僅為1.74g/cm3,其僅為鋁密度的2/3,鋼密度的1/4。這一特性使得鎂合金在汽車、航空航天、國(guó)防軍事、電子通信、家電領(lǐng)域有著非常廣泛的應(yīng)用前景。軋制作為一種金屬材料塑性變形加工的重要手段得到了長(zhǎng)足的發(fā)展。然而,現(xiàn)有的鎂合金板材的應(yīng)用仍然受到很大的限制,其生產(chǎn)量和使用量遠(yuǎn)不及鋼鐵和其他有色金屬(例如鋁和銅)。如何克服各種制約因素將其廣泛地推廣至相關(guān)領(lǐng)域用于生產(chǎn)制造是鎂合金進(jìn)一步發(fā)展所要面臨的重大課題。制約鎂合金板材的發(fā)展的因素主要有以下幾點(diǎn):首先,鎂合金屬于密排六方晶體結(jié)構(gòu),獨(dú)立滑移系少,室溫加工性能較差,因此,現(xiàn)有技術(shù)中的鎂合金板材的生產(chǎn)制造均采用多道次且小壓下量的方式在高溫下(熱軋)進(jìn)行,在現(xiàn)有的常規(guī)工序生產(chǎn)中軋制鎂合金中厚板就要多達(dá)十余道次。其次,軋制鎂合金板材的單道次壓下量一般較小(單道次壓下量通常小于30%),其遠(yuǎn)遠(yuǎn)小于鋼鐵及鋁、銅等有色金屬的單道次壓下量,由此使得軋制工序多、生產(chǎn)成本高、生產(chǎn)效率低下。再者,一般認(rèn)為鎂合金的塑性會(huì)隨著應(yīng)變速率的提高而下降,因此軋制時(shí)通常采用的軋制速度(軋制速度通常小于5m/min),其也遠(yuǎn)遠(yuǎn)小于鋼鐵及鋁、銅等有色金屬,因此也會(huì)提高鎂合金板材的生產(chǎn)成本,并降低鎂合金板材的生產(chǎn)效率。最后,鎂合金板材的力學(xué)性能較差,尤其是需要進(jìn)一步地改進(jìn)鎂合金板材的強(qiáng)度和延展性。公開號(hào)為CN101648210A,公開日為2010年2月17日,名稱為“低溫高速大加工量軋制變形鎂合金板材的加工方法”的中國(guó)專利文獻(xiàn)公開了一種用于鎂合金板材的加工方法。該加工方法包括步驟如下:在傳統(tǒng)的鑄錠(扁坯)→銑面(銑邊)→探傷→均勻化處理→加熱→熱軋→矯直→鋸切→表面處理→檢測(cè)→涂油包裝的扁錠加熱-熱軋生產(chǎn)中厚板的工藝基礎(chǔ)上,針對(duì)工藝中的熱軋工藝采用控制軋制溫度、軋制速度(尤其是終軋溫度及速度)及每道次的壓下量、道次控制在8~10之間,各道次變形之間的間隔時(shí)間以及冷卻速度的方法來控制鎂合金熱軋板的晶粒度達(dá)到提高其綜合力學(xué)性能的目的。然而,該加工方法的工藝步驟較為復(fù)雜,并且軋制速度高達(dá)180m/min,使得其很難廣泛地應(yīng)用于實(shí)際生產(chǎn)中。同時(shí),軋制單道次加工率最大時(shí)也僅為30~42%,單道次壓下量較小,道次加工效率并不高。此外,公開號(hào)為CN103316915A,公開日為2013年9月25日,名稱為“一種寬幅鎂合金板材的制備方法”的中國(guó)專利文獻(xiàn)公開了一種寬幅鎂合金板材高效制備方法。該制備方法的步驟包括:將細(xì)晶、均質(zhì)、低內(nèi)應(yīng)力的鎂合金板坯經(jīng)均勻化處理后進(jìn)行可逆高速熱軋,在可逆高速熱軋過程中多次采用中間道次高溫預(yù)退火以及與立輥軋制和預(yù)拉伸相結(jié)合的方式對(duì)板材進(jìn)行超大壓下變形,經(jīng)過數(shù)道次熱軋后即可獲得鎂合金中厚度板,利用上述方法獲得中厚板經(jīng)切頭尾和剪邊處理后,對(duì)表面進(jìn)行打磨拋光處理后,經(jīng)加熱退火后精軋,在精軋程過中多次采用中間道次高溫預(yù)退火以及與反復(fù)彎曲變形和高速異步軋制相結(jié)合對(duì)板材進(jìn)行超大壓下變形,獲得高精度的鎂合金板材。然而,該中國(guó)專利文獻(xiàn)所公開的加工方法中的軋制速度過快,存在著一定的安全隱患。與此同時(shí),該加工方法的工藝步驟較為復(fù)雜,也很難廣泛地應(yīng)用于實(shí)際生產(chǎn)中。綜上所述,現(xiàn)有的鎂合金板材制備方法并不能有效地兼顧提高生產(chǎn)效率、降低生產(chǎn)成本及改善力學(xué)性能等諸多方面。同時(shí),由于現(xiàn)有的鎂合金板材制備方法要么軋制速度過高,要么軋制速度過低,并且工序復(fù)雜,因此其并不具有大規(guī)模工業(yè)化生產(chǎn)的可行性。為此,企業(yè)亟需獲得一種軋制加工工藝,其能夠滿足市場(chǎng)對(duì)于鎂合金板材應(yīng)用需求的增長(zhǎng)。技術(shù)實(shí)現(xiàn)要素:本發(fā)明的目的在于提供一種高強(qiáng)度高延展性鎂合金板材的高效率軋制工藝。該軋制工藝的軋制速度及道次壓下量適當(dāng),能夠廣泛地推廣至相關(guān)生產(chǎn)制造領(lǐng)域。另外,該軋制工藝的軋制總道次控制得當(dāng),有利地提高了軋制效率。此外,采用本發(fā)明所述的軋制工藝后還能有效地改善板材的力學(xué)性能水平,尤其是能夠大幅度地提高板材的強(qiáng)度和延展性。為了實(shí)現(xiàn)上述目的,本發(fā)明提出了一種高強(qiáng)度高延展性鎂合金板材的高效率軋制工藝,其為對(duì)軋制坯料進(jìn)行軋制的工藝,該軋制工藝的參數(shù)控制為:各軋制道次的軋制速度為10~50m/min,各軋制道次的壓下量控制在40~90%,在各軋制道次軋制前預(yù)熱坯料,并控制各軋制道次軋制前的預(yù)熱溫度和軋制溫度均為250-450℃。需要說明的是,在本技術(shù)方案中,各軋制道次的壓下量在上述范圍內(nèi)可以相同,也可以不同。鎂合金材料通過晶粒細(xì)化可以獲得更為優(yōu)良的力學(xué)性能,也就是說,通過晶粒細(xì)化不僅能提高鎂合金材料的加工塑性,而且還能提高鎂合金材料的強(qiáng)度,并降低其力學(xué)性能的各向異性。相較于鐵、鋁等其它合金材料,因?yàn)殒V合金材料具有更大的Hall-Petch關(guān)系的K系數(shù),所以晶粒細(xì)化作用對(duì)于提高鎂合金材料的強(qiáng)度的貢獻(xiàn)更加明顯。為了進(jìn)一步提高鎂合金的強(qiáng)度和韌度及其它力學(xué)性能,就需要得到更加細(xì)小的晶粒組織。在擠壓、軋制、鍛造等變形加工過程中,鑄態(tài)組織中粗大晶粒和粗大的第二相逐漸得到破碎細(xì)化,使得第二相彌散分布于鎂基體中,從而令鎂合金的力學(xué)性能得到進(jìn)一步地提高,進(jìn)而獲得更高的強(qiáng)度和更好的塑性。經(jīng)軋制后的鎂合金板材的組織特征,如晶粒尺寸、織構(gòu)等與軋制工藝中的軋制速度、單道次壓下量(尤其是終軋壓下量)、軋制溫度、退火溫度和退火時(shí)間都有著密切的關(guān)系。一方面,當(dāng)鎂合金材料軋制速度較快時(shí),變形所產(chǎn)生的變形熱以及軋件與軋輥接觸所產(chǎn)生的摩擦熱會(huì)導(dǎo)致軋件實(shí)際溫度的上升,啟動(dòng)更多的變形模式,以提高合金的變形能力,從而在鎂合金板材的微觀組織中引入更多的位錯(cuò),誘發(fā)動(dòng)態(tài)再結(jié)晶,細(xì)化變形晶粒,進(jìn)而獲得組織晶粒更為細(xì)小的鎂合金板材。另一方面,提高軋制變形應(yīng)變量也有利于軋制變形過程中獲得更加細(xì)化的微觀組織。變形是促使板材發(fā)生再結(jié)晶驅(qū)動(dòng)力的來源。與此同時(shí),壓下量又決定了變形程度和變形儲(chǔ)能大小,從而影響靜態(tài)再結(jié)晶的形核速率,進(jìn)而最終決定靜態(tài)再結(jié)晶晶粒的尺寸大小。較大的變形量能夠在鎂合金的組織中引入更多的畸變能量,以降低動(dòng)態(tài)再結(jié)晶的起始溫度,以此更加有利于鎂合金板材中獲得更加細(xì)化的組織結(jié)構(gòu)。鑒于此,采用較快軋制速度與較大的軋制壓下量相結(jié)合的軋制工藝,不僅能夠有效地獲得細(xì)晶組織,以提高鎂合金板材的力學(xué)性能,而且還能夠有利地提高軋制的工作效率?;诒景l(fā)明的技術(shù)方案,采用適當(dāng)較高的軋制速度并且匹配較大的軋制變形量,有望在鎂合金板材中獲得細(xì)小的變形組織。對(duì)軋制鎂合金板材來說,軋制速度主要會(huì)影響其變形速率。變形速率對(duì)軋制速度的影響主要表現(xiàn)在兩方面:一方面是變形速率將影響變形過程中軋件的實(shí)際軋制溫度;另一方面是變形速率會(huì)影響軋制過程中可啟動(dòng)的變形模式。這兩個(gè)方面將綜合性地決定特定軋制溫度下軋件的最終可軋制能力。發(fā)明人發(fā)現(xiàn),在實(shí)際生產(chǎn)過程中,當(dāng)軋制速度為12.1m/min時(shí),在適當(dāng)?shù)能堉茰囟认聠蔚来螇合铝靠梢赃_(dá)到60%,并且伴隨著動(dòng)態(tài)再結(jié)晶的發(fā)生,為此,提高軋制速度既可以有效地改善鎂合金板材的軋制能力,也實(shí)現(xiàn)了較大壓下量軋制的應(yīng)用。然而,如果軋制速度過快,變形所產(chǎn)生的變形熱以及軋件與軋輥接觸所產(chǎn)生的摩擦熱會(huì)導(dǎo)致軋件實(shí)際溫度的大幅度上升,由于軋件的軋制溫度(即動(dòng)態(tài)再結(jié)晶溫度)在實(shí)際生產(chǎn)過程中很難控制,從而會(huì)誘發(fā)動(dòng)態(tài)再結(jié)晶并可使晶粒長(zhǎng)大,使得鎂合金板材組織再結(jié)晶不完全或者再結(jié)晶晶粒相對(duì)粗大,進(jìn)而導(dǎo)致鎂合金板材的最終力學(xué)性能較差。為此,軋制速度不宜超過50m/min。但是,如果軋制速度過慢,變形所產(chǎn)生的變形熱和軋件與軋輥接觸所產(chǎn)生的摩擦熱又不足以引起軋件實(shí)際溫度的提高,反而會(huì)因預(yù)熱軋件與常溫軋輥的接觸而失去了軋件的部分熱量,由此慢速軋制也不能實(shí)現(xiàn)較大壓下量的軋制。由于壓下量小會(huì)使得變形儲(chǔ)能和位錯(cuò)密度降低,在靜態(tài)再結(jié)晶過程中,不具有充足的形核驅(qū)動(dòng)力,不利于細(xì)化晶粒,會(huì)影響鎂合金板材的強(qiáng)度提高。鑒于此,需要將各軋制道次的軋制速度控制在10~50m/min范圍之間。另外,提高軋制壓下量有利于增加板材中儲(chǔ)存的變形能,使得鎂合金板材中具有較高的位錯(cuò)密度,為靜態(tài)再結(jié)晶形核提供更大的驅(qū)動(dòng)力,從而可以有效地細(xì)化晶粒,提高板材的強(qiáng)度和延展性。發(fā)明人還發(fā)現(xiàn),各道次的壓下量對(duì)鎂合金板材的微觀組織有著重要的影響。隨著壓下量的增大,鎂合金板材的晶粒內(nèi)位錯(cuò)密度增加,晶格畸變加劇,再結(jié)晶晶粒形核數(shù)目增多,由此使得板材內(nèi)的晶粒得以大幅度地細(xì)化。但是,若單道次壓下量過大,也會(huì)導(dǎo)致軋件開裂的可能傾向顯著增加,故而單道次壓下量不宜大于90%。相反,若單道次壓下量過小,則變形儲(chǔ)能和位錯(cuò)密度低,在靜態(tài)再結(jié)晶過程中,形核不具有充足的驅(qū)動(dòng)力,形核點(diǎn)少,不利于鎂合金板材的晶粒細(xì)化。因此,在本發(fā)明所述的高強(qiáng)度高延展性鎂合金板材的高效率軋制工藝中的各軋制道次的單道次壓下量不得小于40%且不得大于90%。由于上述技術(shù)方案中的各軋制道次的壓下量控制在40~90%之間,每一道次的壓下量變得更大了,因此,相較于現(xiàn)有的軋制工序中所需的道次,本發(fā)明所述的軋制工藝中所經(jīng)歷的軋制道次更少,工序步驟更為簡(jiǎn)單,所需的軋制時(shí)間更省,工作效率更高。此外,在通過控制軋制速度及軋制單道次壓下量的基礎(chǔ)上,控制軋制溫度能夠有效地改善鎂合金板材的力學(xué)性能。在本發(fā)明的技術(shù)方案中,將各軋制道次的軋制前的預(yù)熱溫度和軋制溫度都控制在250~450℃之間的原因在于:溫度過高,軋制前后晶粒在高溫下快速長(zhǎng)大,降低了通過軋制變形來細(xì)化晶粒的效果;如溫度過低,則材料的塑性變形能力較低,軋制板材容易開裂、甚至原料發(fā)生斷裂。進(jìn)一步地,在本發(fā)明所述的高強(qiáng)度高延展性鎂合金板材的高效率軋制工藝中,控制各軋制道次軋制前的預(yù)熱時(shí)間為1~15min。本發(fā)明的另一目的在于提供一種高強(qiáng)度高延展性鎂合金板材的制備方法。通過該制備方法可以獲得強(qiáng)度高且延展性好的鎂合金板材。另外,該制備方法的工序步驟簡(jiǎn)單,所耗時(shí)間少,生產(chǎn)效率高。此外,本發(fā)明所述的高強(qiáng)度高延展性鎂合金板材的制備方法的生產(chǎn)成本低,能夠大規(guī)模地推廣至相關(guān)生產(chǎn)制造領(lǐng)域。為了達(dá)到上述發(fā)明目的,本發(fā)明提出了一種高強(qiáng)度高延展性鎂合金板材的制備方法,其包括步驟:(1)制備軋制坯料;(2)將坯料高效熱軋到目標(biāo)值:各軋制道次的軋制速度為10-50m/min,各軋制道次的壓下量控制在40-90%,在各軋制道次軋制前預(yù)熱坯料,并控制各軋制道次軋制前的預(yù)熱溫度和軋制溫度均為250-450℃;(3)退火。進(jìn)一步地,在本發(fā)明所述的制備方法中,在步驟(2)中,控制各軋制道次軋制前的預(yù)熱時(shí)間為1~15min。通過控制在高效熱軋過程中的軋制速度、軋制單道次壓下量和軋制溫度不僅能夠有效地改善鎂合金板材的力學(xué)性能,而且能夠有利地提高鎂合金板材的軋制效率。由于上文已經(jīng)對(duì)于控制軋制工藝參數(shù)的設(shè)計(jì)原理進(jìn)行了詳細(xì)的描述,在此,就不再針對(duì)上述熱軋工藝的參數(shù)控制的設(shè)計(jì)原理進(jìn)行贅述了。需要說明的是,由于高效熱軋中的各軋制道次的壓下量控制在40~90%之間,也就是說,較之于現(xiàn)有技術(shù)中所采用的軋制的壓下量,每一道次的壓下量變得更大了,因此,相較于現(xiàn)有的軋制工序中的道次,本發(fā)明所述的制備方法中所經(jīng)歷的熱軋軋制道次就會(huì)變得更少,熱軋工序步驟更為簡(jiǎn)單,所需的熱軋軋制時(shí)間更省,工作效率則更高。進(jìn)一步地,在上述步驟(3)中,退火溫度為150~400℃,退火時(shí)間為10~300s。退火溫度和退火時(shí)間對(duì)板材的靜態(tài)再結(jié)晶晶粒大小也有著極為重要的影響。如果退火溫度太高,靜態(tài)再結(jié)晶晶粒長(zhǎng)大速率過快,故而很難得到細(xì)小的再結(jié)晶晶粒。如果退火溫度太低,那么變形儲(chǔ)能則達(dá)不到該溫度下靜態(tài)再結(jié)晶所需的能量,故而不會(huì)產(chǎn)生靜態(tài)再結(jié)晶,無(wú)法進(jìn)一步地細(xì)化晶粒。同時(shí),在一定退火溫度下,隨著退火時(shí)間的增加,變形晶粒將通過靜態(tài)再結(jié)晶形成細(xì)小的晶粒并且逐漸長(zhǎng)大。同時(shí),一旦保溫時(shí)間過長(zhǎng),又將導(dǎo)致再結(jié)晶晶粒變得粗大,由此不利于提高鎂合金板材的強(qiáng)度。反之,保溫時(shí)間過短,則有可能尚未發(fā)生靜態(tài)再結(jié)晶,也無(wú)法通過再結(jié)晶進(jìn)一步細(xì)化晶粒。為此,根據(jù)鎂合金板材的成分和變形情況,退火溫度應(yīng)當(dāng)控制在150~400℃范圍之間,并將退火時(shí)間應(yīng)控制在10~300s范圍之間,以有效地細(xì)化鎂合金板材的晶粒尺寸,從而大幅度地提高鎂合金板材的室溫強(qiáng)度與延伸率。在某些實(shí)施方式中,本發(fā)明所述的制備方法的步驟1)制備軋制坯料的步驟包括熔煉、鑄造鑄錠、均勻化處理、鋸切鑄錠和粗軋。更進(jìn)一步地,在上述步驟(1)中,控制粗軋各道次的軋制速度為10~50m/min。更進(jìn)一步地,在上述步驟(1)中,控制粗軋各道次的壓下量為10~30%??紤]扁錠咬入板材的條件,較之于步驟(2),在步驟(1)中的各軋制道次采用相對(duì)較小的軋制壓下量,因此,在粗軋過程中控制各道次的壓下量為10~30%,其小于高效熱軋過程中的各道次的軋制壓下量。更進(jìn)一步地,在上述步驟(1)中,在粗軋各道次前預(yù)熱坯料,并控制預(yù)熱溫度和粗軋各道次的軋制溫度為250~450℃。在步驟(1)中,控制預(yù)熱溫度和粗軋各道次的軋制溫度在250~450℃范圍之間的原因在于:溫度過高,軋制前后晶粒在高溫下快速長(zhǎng)大,減低了通過軋制變形來細(xì)化晶粒的效果;如溫度過低,則材料的塑性變形能力較低,軋制板材容易開裂、甚至材料發(fā)生斷裂。在另外一些實(shí)施方式中,本發(fā)明所述的制備方法的步驟1)中,還可以采用雙輥鑄軋方法制備軋制坯料。該方法為本領(lǐng)域內(nèi)的常規(guī)工藝,故在此不再進(jìn)行贅述。本發(fā)明所述的高強(qiáng)度高延展性鎂合金板材的制備方法采用了較快的軋制速度及較大的軋制壓下量,使得變形儲(chǔ)能高但尚未發(fā)生動(dòng)態(tài)再結(jié)晶的鎂合金板材,在隨后的較低的退火溫度下進(jìn)行短時(shí)間退火,以在鎂合金板材中獲得由靜態(tài)再結(jié)晶導(dǎo)致的細(xì)小晶粒,從而得到強(qiáng)度更高且塑性更好的鎂合金板材。此外,在該高強(qiáng)度高延展性鎂合金板材的制備方法中,僅需要對(duì)于軋制工藝參數(shù)和退火工藝參數(shù)進(jìn)行控制即可獲得具有強(qiáng)度高且塑性好的鎂合金板材,工藝步驟簡(jiǎn)單便捷,生產(chǎn)效率高,在提高鎂合金板材的力學(xué)性能指標(biāo)的前提下,還降低了鎂合金板材的生產(chǎn)成本,其具有較高的實(shí)際應(yīng)用價(jià)值,可以廣泛地推廣至相關(guān)生產(chǎn)制造領(lǐng)域。本發(fā)明所述的高強(qiáng)度高延展性鎂合金板材的高效率軋制工藝的軋制速度和道次壓下量適當(dāng),能夠廣泛地推廣至相關(guān)生產(chǎn)制造領(lǐng)域。另外,該高強(qiáng)度高延展性鎂合金板材的高效率軋制工藝的軋制總道次控制得當(dāng),有利地提高了軋制效率。此外,采用本發(fā)明所述的高強(qiáng)度高延展性鎂合金板材的高效率軋制工藝后還能有效地改善板材的力學(xué)性能指標(biāo),尤其是能夠大幅度地提高板材的強(qiáng)度和延展性。通過本發(fā)明所述的高強(qiáng)度高延展性鎂合金板材的制備方法可以改善鎂合金板材的強(qiáng)度和塑性。另外,該高強(qiáng)度高延展性鎂合金板材的制備方法的可軋性好。此外,該高強(qiáng)度高延展性鎂合金板材的制備方法可以大幅度地減少軋制道次,從而有效地減少生產(chǎn)制備所需的時(shí)間,提高生產(chǎn)效率高,進(jìn)而降低生產(chǎn)成本。同時(shí),該高強(qiáng)度高延展性鎂合金板材的制備方法的工序步驟簡(jiǎn)單,能夠大規(guī)模地推廣至相關(guān)生產(chǎn)制造領(lǐng)域。附圖說明圖1為對(duì)比例B1經(jīng)退火步驟后的微觀組織圖。圖2為對(duì)比例B2經(jīng)退火步驟后的微觀組織圖。圖3為實(shí)施例A1經(jīng)退火步驟后的微觀組織圖。圖4為實(shí)施例A1、對(duì)比例B1和對(duì)比例B2所采用的壓下量和其室溫拉伸曲線的關(guān)系圖。圖5為對(duì)比例B3經(jīng)退火步驟后的微觀組織圖。圖6為對(duì)比例B4經(jīng)退火步驟后的微觀組織圖。圖7為實(shí)施例A2經(jīng)退火步驟后的微觀組織圖。圖8為實(shí)施例A2、對(duì)比例B3和對(duì)比例B4所采用的壓下量和其室溫拉伸曲線的關(guān)系圖。圖9為對(duì)比例B5經(jīng)退火步驟后的微觀組織圖。圖10為對(duì)比例B6經(jīng)退火步驟后的微觀組織圖。圖11為實(shí)施例A3經(jīng)退火步驟后的微觀組織圖。圖12為實(shí)施例A3、對(duì)比例B5和對(duì)比例B6所采用的壓下量和其室溫拉伸曲線的關(guān)系圖。具體實(shí)施方式下面將結(jié)合附圖說明和具體的實(shí)施例對(duì)本發(fā)明所述的高強(qiáng)度高延展性鎂合金板材的高效率軋制工藝及高強(qiáng)度高延展性鎂合金板材的制備方法做進(jìn)一步的解釋和說明,然而該解釋和說明并不對(duì)本發(fā)明的技術(shù)方案構(gòu)成不當(dāng)限定。實(shí)施例A1-A6和對(duì)比例B1-B9通過本發(fā)明的高強(qiáng)度高延展性鎂合金板材的制備方法來獲得上述實(shí)施例A1-A6,其包括步驟:(1)制備軋制坯料:其中,實(shí)施例A1-A2,A4,A5中軋制坯料的制備工藝如下:(1a)熔煉:將原材料放置在鋼坩堝中混合,隨后將坩堝及原材料放置在感應(yīng)爐中加熱至760℃熔煉,在熔煉過程中,向感應(yīng)爐中注入氬氣作為保護(hù)氣氛,防止燃燒;(1b)鑄造鑄錠:熔煉完畢后,將熔融的鎂合金液體澆鑄于200℃的預(yù)熱鋼模具中,鑄錠尺寸為55mm(長(zhǎng))*30mm(寬)*120mm(高);(1c)均勻化處理:先在300℃溫度下均勻化處理12hr,然后在430℃的溫度下均勻化處理4hr;(1d)鋸切鑄錠:均勻化處理后根據(jù)厚度要求將鑄錠鋸切成5mm厚度的板坯;(1e)粗軋:該軋制工藝的參數(shù)控制為:軋輥直徑為75mm,各道次的軋制速度為10~50m/min,各道次的壓下量為10~30%,各道次軋制前預(yù)熱坯料,預(yù)熱溫度和軋制溫度均為250~450℃,預(yù)熱保溫時(shí)間為1~15min。實(shí)施例A3、A6的軋制坯料通過雙輥鑄軋制備的得到的AZ31合金坯料,其初始厚度為2mm。(2)高效熱軋:軋輥直徑為75mm,控制各軋制道次的軋制速度為10~50m/min,各軋制道次的壓下量為40~90%,各軋制道次在軋制前預(yù)熱坯料,控制預(yù)熱溫度和和軋制的溫度為250~450℃,預(yù)熱保溫時(shí)間為1~15min。(3)退火:控制退火溫度為150~400℃,退火時(shí)間為10~300s。需要說明的是,對(duì)比例B5、B6、B9的軋制坯料也是通過雙輥鑄軋制備的得到的。而對(duì)比例B1-B4,B7,B8是通過熔煉、鑄造鑄錠、均勻化處理、鋸切鑄錠和粗軋步驟獲得的。表1列出了實(shí)施例A1-A6和對(duì)比例B1-B9的具體工藝參數(shù)。表1.*注:對(duì)于表中的多道次軋制,如果單道次壓下量只有一個(gè)值,則表示每一個(gè)道次的壓下量均是相同的。對(duì)實(shí)施例A1-A6和對(duì)比例B1-B9的鎂合金板材取樣,截取樣品中間部分以觀察板材的微觀組織,相關(guān)板材的微觀組織如以下附圖所示:相關(guān)力學(xué)性能通過常規(guī)的拉伸實(shí)驗(yàn)測(cè)試方法來測(cè)定;其中,拉伸應(yīng)變速率為10-3/s,標(biāo)距長(zhǎng)度10mm,將經(jīng)過測(cè)試后所獲得的結(jié)果列于表2中。表2列出了實(shí)施例A1-A6和對(duì)比例B1-B9的力學(xué)性能參數(shù)。表2.序號(hào)*屈服強(qiáng)度(MPa)抗拉強(qiáng)度(MPa)均勻延伸率(%)延伸率(%)A12433001324A2244265829A32633041020A42453082026A52342551631A62653181524B1221270915B22352801120B3215236714B4238259718B5255291816B6261303813B71192301523B8141212930B91952641222從表2所示的內(nèi)容可以看出,實(shí)施例A1-A6的屈服強(qiáng)度均≥234MPa,抗拉強(qiáng)度≥255MPa,說明實(shí)施例的鎂合金板材具有較高的強(qiáng)度;實(shí)施例A1-A6的均勻延伸率≥8%且延伸率≥20%,由此說明實(shí)施例的鎂合金板材具有較高的延展性,具備良好的塑性。實(shí)施例A1-A6的屈服強(qiáng)度、抗拉強(qiáng)度、均勻延伸率、延伸率均高于其所對(duì)應(yīng)的對(duì)比例的屈服強(qiáng)度、抗拉強(qiáng)度、均勻延伸率、延伸率。尤其是,實(shí)施例的鎂合金板材的屈服強(qiáng)度得到大幅度地提高,例如,較之于對(duì)比例B9的屈服強(qiáng)度(195MPa),實(shí)施例A6的屈服強(qiáng)度(265MPa)提高了35.9%,相較于對(duì)比例B8的屈服強(qiáng)度(141MPa),實(shí)施例A5的屈服強(qiáng)度(234MPa)的升幅達(dá)到了66%左右,與對(duì)比例B7的屈服強(qiáng)度(119MPa)相比較,實(shí)施例A4的屈服強(qiáng)度(245MPa)甚至提升了約106%。圖1、圖2和圖3分別顯示了對(duì)比例B1、對(duì)比例B2和實(shí)施例A1經(jīng)退火步驟后的微觀組織。如圖1所示,必要時(shí)可以參見表1,對(duì)比例B1的單道次壓下量為10%,由于壓下量小導(dǎo)致鎂合金板材的變形量小,因此,使得板材的再結(jié)晶不完全,其再結(jié)晶晶粒分?jǐn)?shù)僅為22%,并且其晶粒比較粗大,平均晶粒尺寸在9μm左右。如圖2所示,必要時(shí)可以參見表1,對(duì)比例B2的單道次壓下量為30%,由于較之于對(duì)比例B1所采用的單道次壓下量大,鎂合金板材的變形量也相對(duì)較大,盡管鎂合金板材的再結(jié)晶仍不完全,但是其再結(jié)晶晶粒分?jǐn)?shù)要高于對(duì)比例B1的再結(jié)晶晶粒分?jǐn)?shù),其再結(jié)晶晶粒分?jǐn)?shù)為40%左右,平均晶粒尺寸更小,其約為6μm。如圖3所示,必要時(shí)可以參見表1,實(shí)施例A1采用的單道次壓下量為50%,由于較之于對(duì)比例B1和B2所采用的單道次壓下量更大,鎂合金板材的變形量更大,鎂合金板材的晶粒組織明顯得到細(xì)化,大尺寸變形晶粒大幅度地減少。較之于圖1和圖2所示的對(duì)比例B1和B2的鎂合金板材的晶粒尺寸,圖3所示的實(shí)施例A1的晶粒尺寸更小,晶粒大小較為均勻,平均晶粒尺寸在4μm左右,再結(jié)晶晶粒分?jǐn)?shù)達(dá)到了68%左右。如圖1和圖2所示,并結(jié)合表1所示內(nèi)容可以獲知,由于對(duì)比例B1和對(duì)比例B2采用了相對(duì)較低的單道次壓下量,因此,對(duì)比例B1和對(duì)比例B2經(jīng)退火步驟后所呈現(xiàn)的微觀組織中的再結(jié)晶晶粒尺寸較大,再結(jié)晶細(xì)化晶粒效果并不明顯。如圖3所示,并結(jié)合表1所示內(nèi)容可以獲知,由于實(shí)施例A1采用了較高的單道次壓下量,因此,實(shí)施例A1的微觀組織中的再結(jié)晶程度非常明顯,晶粒尺寸小且晶粒大小均勻。圖4顯示了實(shí)施例A1、對(duì)比例B1和對(duì)比例B2所采用的單道次壓下量和其室溫拉伸曲線之間的關(guān)系。如圖4所示,并結(jié)合表1和表2,對(duì)比例B1采用的單道次壓下量為10%,對(duì)比例B2采用的單道次壓下量為30%,而實(shí)施例A1采用的單道次壓下量為50%,隨著單道次壓下量的增大,鎂合金板材的力學(xué)性能指標(biāo)隨之提升。具體地,實(shí)施例A1的屈服強(qiáng)度、抗拉強(qiáng)度、均勻延伸率、延伸率均高于對(duì)比例B1和B2的屈服強(qiáng)度、抗拉強(qiáng)度、均勻延伸率、延伸率。圖5、圖6和圖7分別顯示了對(duì)比例B3、對(duì)比例B4和實(shí)施例A2經(jīng)退火步驟后的微觀組織。如圖5所示,必要時(shí)可以參見表1,對(duì)比例B3的單道次壓下量為10%,由于壓下量小導(dǎo)致鎂合金板材的變形量小,因此,使得板材的再結(jié)晶不完全,其再結(jié)晶晶粒分?jǐn)?shù)僅為30%,并且從圖5中看到的晶粒較為粗大,平均晶粒尺寸在7μm左右。如圖6所示,必要時(shí)可以參見表1,對(duì)比例B4的單道次壓下量為30%,由于較之于對(duì)比例B3所采用的單道次壓下量要來的大,鎂合金板材的變形量更大,雖然鎂合金板材的再結(jié)晶仍不完全,但是其再結(jié)晶晶粒分?jǐn)?shù)要高于對(duì)比例B3的再結(jié)晶晶粒分?jǐn)?shù),其再結(jié)晶晶粒分?jǐn)?shù)為48%左右,平均晶粒尺寸更小,其約為4μm。如圖7所示,必要時(shí)可以參見表1,實(shí)施例A2采用單道次壓下量為50%,由于較之于對(duì)比例B3和B4所采用的單道次壓下量更大,鎂合金板材的變形量更大,鎂合金板材的晶粒組織明顯得到細(xì)化,大尺寸變形晶粒大幅度地減少。較之于圖5和圖6所示的對(duì)比例B3和B4的鎂合金板材的晶粒尺寸,圖7所示的實(shí)施例A2的晶粒尺寸更加地細(xì)小,晶粒大小更為均勻,平均晶粒尺寸在3μm左右,再結(jié)晶晶粒分?jǐn)?shù)達(dá)到了66%左右。如圖5和圖6所示,并結(jié)合表1所示內(nèi)容可以獲知,由于對(duì)比例B3和對(duì)比例B4采用了相對(duì)較低的單道次壓下量,因此,對(duì)比例B3和對(duì)比例B4經(jīng)退火步驟后所呈現(xiàn)的微觀組織中的再結(jié)晶晶粒尺寸相對(duì)較大,再結(jié)晶細(xì)化晶粒效果并不明顯。如圖7所示,并結(jié)合表1所示內(nèi)容可以獲知,由于實(shí)施例A2采用了較高的單道次壓下量,因此,實(shí)施例A2的微觀組織中的再結(jié)晶效果明顯,晶粒尺寸小且晶粒大小均勻。圖8顯示了實(shí)施例A2、對(duì)比例B3和對(duì)比例B4所采用的單道次壓下量和其室溫拉伸曲線之間的關(guān)系。如圖8所示,并結(jié)合表1和表2,對(duì)比例B3采用的單道次壓下量為10%,對(duì)比例B4采用的單道次壓下量為30%,而實(shí)施例A2采用的單道次壓下量為50%,隨著單道次壓下量的增大,鎂合金板材的應(yīng)力和應(yīng)變指數(shù)也隨之提升。具體地,實(shí)施例2的屈服強(qiáng)度、抗拉強(qiáng)度、均勻延伸率、延伸率均高于對(duì)比例B3和B4的屈服強(qiáng)度、抗拉強(qiáng)度、均勻延伸率、延伸率。圖9、圖10和圖11分別顯示了對(duì)比例B5、對(duì)比例B6和實(shí)施例A3經(jīng)退火步驟后的微觀組織。如圖9所示,必要時(shí)可以參見表1,對(duì)比例B5的單道次壓下量為10%,由于壓下量小導(dǎo)致鎂合金板材的變形量小,因此,使得板材的再結(jié)晶不完全,其再結(jié)晶晶粒分?jǐn)?shù)僅為28%,并且從圖9中看到的晶粒較為粗大,平均晶粒尺寸在12μm左右。如圖10所示,必要時(shí)可以參見表1,對(duì)比例B6的單道次壓下量為30%,由于較之于對(duì)比例B5所采用的單道次壓下量要來的大,鎂合金板材的變形量更大,雖然鎂合金板材的再結(jié)晶仍不完全,但是其再結(jié)晶晶粒分?jǐn)?shù)要高于對(duì)比例B5的再結(jié)晶晶粒分?jǐn)?shù),其再結(jié)晶晶粒分?jǐn)?shù)為48%左右,平均晶粒尺寸更小,其約為7μm。如圖11所示,必要時(shí)可以參見表1,實(shí)施例A3采用單道次壓下量為50%,由于較之于對(duì)比例B5和B6所采用的單道次壓下量更大,鎂合金板材的變形量更大,鎂合金板材的晶粒組織明顯得到細(xì)化,大尺寸變形晶粒大幅度地減少。較之于圖9和圖10所示的對(duì)比例B5和B6的鎂合金板材的晶粒尺寸,圖11所示的實(shí)施例A3的晶粒尺寸更加地細(xì)小,晶粒大小更為均勻,平均晶粒尺寸在4μm左右,再結(jié)晶晶粒分?jǐn)?shù)達(dá)到了67%左右。如圖9和圖10所示,并結(jié)合表1所示內(nèi)容可以獲知,由于對(duì)比例B5和對(duì)比例B6采用了相對(duì)較低的單道次壓下量,因此,對(duì)比例B5和對(duì)比例B6經(jīng)退火步驟后所呈現(xiàn)的微觀組織中的再結(jié)晶晶粒尺寸較大,再結(jié)晶細(xì)化晶粒效果并不明顯。如圖11所示,并結(jié)合表1所示內(nèi)容可以獲知,由于實(shí)施例A3采用了較高的單道次壓下量,因此,實(shí)施例A3的微觀組織中的再結(jié)晶效果明顯,晶粒尺寸小且晶粒大小均勻。圖12顯示了實(shí)施例A3、對(duì)比例B5和對(duì)比例B6所采用的單道次壓下量和其室溫拉伸曲線之間的關(guān)系。如圖12所示,并結(jié)合表1和表2,對(duì)比例B5采用的單道次壓下量為10%,對(duì)比例B6采用的單道次壓下量為30%,而實(shí)施例A3采用的單道次壓下量為50%,隨著單道次壓下量的增大,鎂合金板材的應(yīng)力和應(yīng)變指數(shù)也隨之提升。具體地,實(shí)施例A3的屈服強(qiáng)度、抗拉強(qiáng)度、均勻延伸率、延伸率均高于對(duì)比例B5和B6的屈服強(qiáng)度、抗拉強(qiáng)度、均勻延伸率、延伸率。需要注意的是,以上列舉的僅為本發(fā)明的具體實(shí)施例,顯然本發(fā)明不限于以上實(shí)施例,隨之有著許多的類似變化。本領(lǐng)域的技術(shù)人員如果從本發(fā)明公開的內(nèi)容直接導(dǎo)出或聯(lián)想到的所有變形,均應(yīng)屬于本發(fā)明的保護(hù)范圍。當(dāng)前第1頁(yè)1 2 3