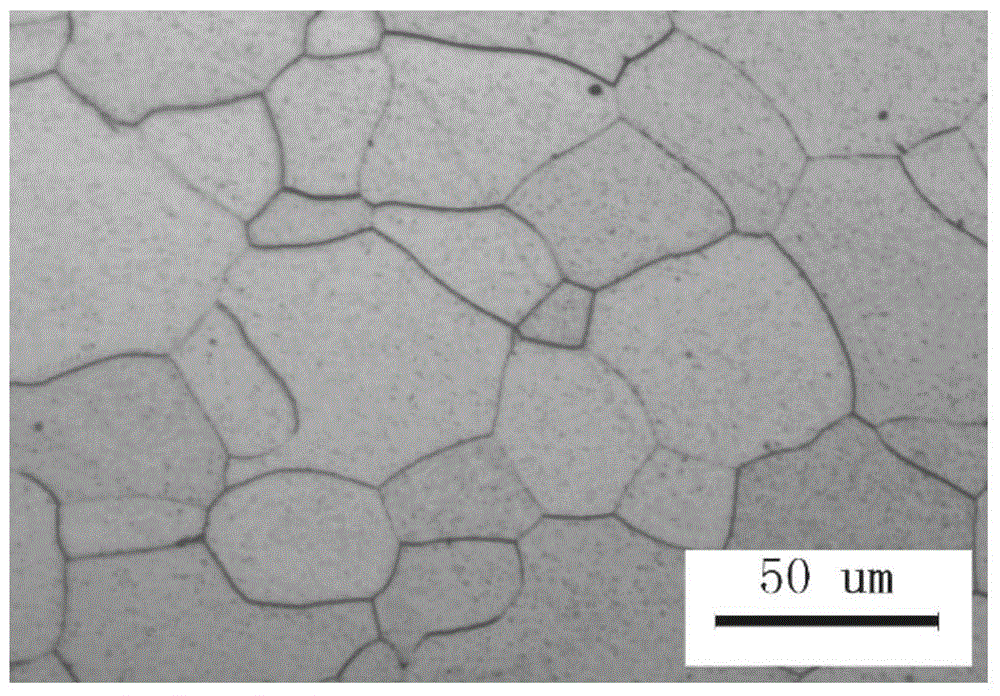
本發(fā)明涉及一種汽車用高強(qiáng)度冷軋鋼板及其制造方法,特別涉及一種超低碳含銅汽車用高強(qiáng)度冷軋鋼板及其熱處理方法。
背景技術(shù):
:隨著環(huán)境保護(hù)日益受到重視,汽車行業(yè)面臨越來越嚴(yán)峻的技術(shù)和成本競爭。作為汽車行業(yè)主要的材料供應(yīng)商的鋼鐵生產(chǎn)企業(yè),也面臨著同樣的問題。提供環(huán)境友好、性能優(yōu)良、成本低廉的鋼鐵產(chǎn)品是各鋼鐵企業(yè)共同的追求。為了保證一定的耐蝕性能,冷軋板熱鍍鋅是目前廣泛采用的方式。但是熱鍍鋅對環(huán)境有不利的影響,在發(fā)達(dá)國家甚至在國內(nèi)的一些城市也受到了限制。以上海為例,從2013年開始,就不再審批新的熱鍍鋅線。因此,能否從鋼種成分設(shè)計著手,設(shè)計出具有一定的耐蝕性、性能優(yōu)良且成本經(jīng)濟(jì)的冷軋鋼板,無疑具有廣闊的市場前景。銅,作為析出強(qiáng)化和提高耐蝕性元素很早就被使用。但銅由于熔點較低,容易在熱軋過程產(chǎn)生“熱脆”,而不得不在成分中加入昂貴的鎳元素,以抵消銅的不利作用。鋼中加入1%銅的同時要加入差不多等量甚至更高的鎳,致使鋼的成本大幅提高,缺乏市場競爭力。該發(fā)明采用含銅無鎳的設(shè)計方案并配合一定的軋制工藝,不僅規(guī)避了銅在熱軋過程中的危害,還在保證鋼力學(xué)性能的同時,提高了鋼的耐蝕性,在一定范圍內(nèi)具備了替代鍍鋅板的條件,并具有更低的成本。尹桂全等人的“含銅鋼的時效硬化”(《鋼鐵研究學(xué)報》2004年8月16卷第4期)研究了銅的時效強(qiáng)化作用,鋼中銅含量為1.19%, 但鋼中同時添加了0.85%的鎳;劉錕等人的“低鎳/銅比鋼中銅的富集行為”(《金屬熱處理》,2012年5月第37卷第5期),研究了降低銅的危害的方法,但在鋼中仍然加入了一定量的鎳;李闖等人的“組織對含銅鋼中析出行為的影響”(《材料科學(xué)與工藝》,2011年8月第19卷第4期),研究是熱軋板,含銅量為1.95%,但加入了2%的鎳。上述文獻(xiàn)中的含銅鋼中都無一例外地加入了昂貴的鎳、鈮、鉬元素或者其中一種,增加了鋼的成本,與本專利的成分設(shè)計有著本質(zhì)的區(qū)別。技術(shù)實現(xiàn)要素:本發(fā)明的目的在于提供一種無鎳復(fù)合加入、低成本低廉、耐蝕性能優(yōu)良的超低碳含銅汽車用高強(qiáng)冷軋鋼板及其制造方法。本發(fā)明以超低C、低Si、Mn成分為基礎(chǔ),添加1.2%~2.4%的Cu,采用普低溫?zé)彳?普通冷軋+退火+時效的工藝,開發(fā)出抗拉強(qiáng)度在450~650MPa、延伸率不低于30%的冷軋汽車用鋼板。其組織為多邊形鐵素體。鐵素體中有起強(qiáng)化作用的大量銅的析出相。本發(fā)明中鋼的化學(xué)成分(質(zhì)量百分?jǐn)?shù))為:C:0.004%~0.006%、N:0.001%~0.003%、Si:0.2%~1.0%、Mn:0.2%~1.0%、P≤0.015%、S≤0.015%、Als:0.02%~0.04%,Cu:1.2%~2.4%,余量為Fe和不可避免的雜質(zhì)。本發(fā)明中高氮高強(qiáng)汽車用鋼的成分設(shè)計說明:C:為保證鋼顯微組織中無碳化物相及充分避開包晶反應(yīng),同時不惡化鋼板的成形性和焊接性能,采取較低的碳含量。因為鋼中沒有加入Nb、Ti等強(qiáng)碳化物形成元素,為降低對塑性不利的間隙原子含量,必須選擇超低碳設(shè)計。但碳還有開啟奧氏體相區(qū)、固溶強(qiáng)化、促進(jìn)奧氏體再結(jié)晶的有益作用。因此,將C控制在0.004%~0.006%。Si:在鋼中硅是有效的固溶強(qiáng)化元素,根據(jù)強(qiáng)度需要進(jìn)行添加。 另外,Si防止碳化物生成。但若其量超過1.0%則會惡化鋼板的成形性、焊接性和塑性,因此,選在0.2%~1.0%之間。Mn:能細(xì)化晶粒并降低Ar3,擴(kuò)大奧氏體相區(qū),推遲珠光體轉(zhuǎn)變,抑制鐵素體的生成,同時錳也有固溶強(qiáng)化的作用,但過高的錳則使鋼材難于加工。錳容易偏析并造成混晶,故選在0.2%~1.0%之間。Als:若小于0.02%,會導(dǎo)致鋼中氧含量增加,大于0.04%容易導(dǎo)致連鑄水口堵塞。Al也能有效降低固溶N的含量,一定程度細(xì)化晶粒。因此將Als的含量控制在0.02%~0.04%。N:作為隙間原子,可以擴(kuò)大奧氏體相區(qū),與C相比有更好的固溶強(qiáng)化效果,但會降低鋼的塑性。因此將N控制在0.001%~0.003%。P、S是鋼中不可避免的雜質(zhì),惡化了鋼板的成形性,因此在冶煉能力允許的條件下,將P控制在≤0.015%、S控制在≤0.015%。Cu:作為本發(fā)明鋼中最重要的合金元素,不僅具有開啟奧氏體相區(qū)的作用,同時具有固溶強(qiáng)化、析出強(qiáng)化的作用。另外,銅還能顯著提高鋼的耐蝕性。由于銅在鐵素體中也有較高的溶解度,因此為保證析出強(qiáng)化銅的含量不能太低;過高的銅含量容易造成軋制缺陷。因此本發(fā)明中將銅含量選擇在1.2%~2.4%。本發(fā)明超低碳含銅汽車用鋼的生產(chǎn)方法及實施具體實施步驟如下:(1)冶煉:按設(shè)計成分冶煉,無特殊要求;連鑄坯厚度要控制在350mm以下;(2)熱軋:980~1050℃保溫30~60min,開軋溫度950~1000℃,終軋溫度820~880℃,500~550℃卷取;(3)冷軋:壓下率不低于65%;(4)退火:加熱溫度890~920℃,保溫20~40min,以不低于20 ℃/s速度冷至室溫。然后根據(jù)強(qiáng)度級別在550~680℃時效30~60min。本發(fā)明可以獲得如下有益效果:(1)不用添加Nb、Ti、Mo等貴重金屬,僅加入銅從而降低冶煉成本和冶煉難度;(2)采用較低的軋制溫度和較短的均熱時間,節(jié)省燃?xì)獬杀荆?3)由于Cu含量較高,其耐蝕性遠(yuǎn)遠(yuǎn)優(yōu)于普通高強(qiáng)汽車用鋼;(4)該鋼板阻尼性能也遠(yuǎn)優(yōu)于其它同級別鋼種。附圖說明圖1典型退火工藝曲線圖;圖2含銅鋼的金相組織;圖3含銅鋼析出相。具體實施方式本發(fā)明超低碳含銅汽車用高強(qiáng)冷軋鋼板的化學(xué)成分為:C:0.004%~0.006%、N:0.001%~0.003%、Si:0.2%~1.0%、Mn:0.2%~1.0%、P≤0.015%、S≤0.015%、Als:0.02%~0.04%,Cu:1.2%~2.4%,余量為Fe和不可避免的雜質(zhì)。連鑄坯厚度控制在350mm以下;熱軋加熱溫度為980~1050℃,保溫30~60min,開軋溫度為950~1000℃,終軋溫度為820~880℃,卷取溫度為500~550℃;冷軋壓下率不低于65%;退火加熱溫度為890~920℃,保溫20~40min,以不低于20℃/s速度冷至室溫,然后在550~680℃時效30~60min。以下實施例用于具體說明本
發(fā)明內(nèi)容,體現(xiàn)獲得的效果。這些實施例僅為本
發(fā)明內(nèi)容的一般描述,并不對本
發(fā)明內(nèi)容進(jìn)行限制。表1為本發(fā)明實施例的具體鋼種成分。表2為本發(fā)明實施例工藝參數(shù)。表3為實施例鋼板的力學(xué)性能指標(biāo)。表4為實施例鋼板的耐蝕性能。表1發(fā)明鋼的熔煉成分(mass%)實施例CSiMnPSCuAlsN10.0040.210.550.0080.0051.300.0300.00220.0060.460.360.0070.0031.330.0280.00130.0041.001.000.0080.0031.800.0360.00340.0060.800.800.0090.0041.800.0310.00250.0050.800.800.0060.0032.400.0380.002表2實施例工藝參數(shù)表3實施例鋼板的力學(xué)性能實施例ReL/MPaRm/MPaA50/%n值(平均)1240520380.212230490390.203260570350.224270550360.225320650320.24表4實施例鋼板的耐蝕性能對比(mm/年)通過本發(fā)明得到的鋼板,抗拉強(qiáng)度達(dá)到490MPa以上,延伸率不低于30%且耐蝕性能優(yōu)良。當(dāng)前第1頁1 2 3