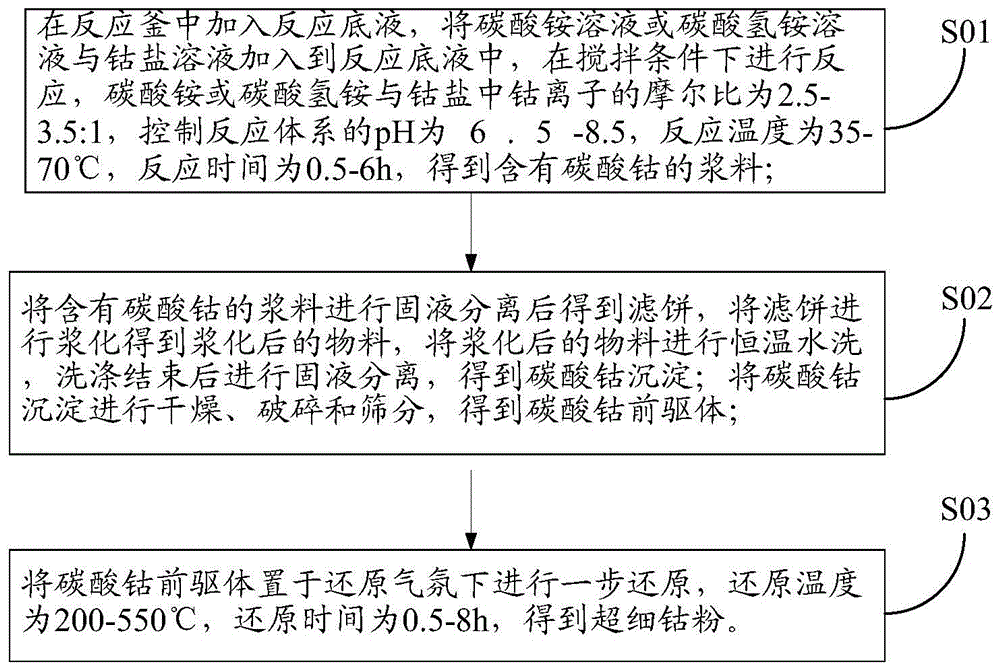
本發(fā)明屬于金屬微粒制備
技術(shù)領(lǐng)域:
,尤其涉及一種低成本制備超細(xì)鈷粉的方法。
背景技術(shù):
:作為一種優(yōu)良的粘結(jié)劑,鈷粉在硬質(zhì)合金、金剛石工具和粉末冶金等領(lǐng)域有重要作用。隨著鈷粉粒徑減小,可以顯著降低硬質(zhì)合金粉末混料的研磨時(shí)間、燒結(jié)溫度,增強(qiáng)硬質(zhì)合金抗彎強(qiáng)度、耐磨性和抗裂性等性能,減少鈷池和孔隙的出現(xiàn),因此,目前國內(nèi)外都把超細(xì)鈷粉作為硬質(zhì)合金和金剛石工具等領(lǐng)域的發(fā)展方向。由于對(duì)超細(xì)鈷粉的前驅(qū)體制備、鈷粉還原及后處理等過程要求程度很高,導(dǎo)致超細(xì)鈷粉的生產(chǎn)成本相對(duì)較高,主要體現(xiàn)在以下幾方面:(1)、部分工藝采用氫氧化鈉、氫氧化鉀等堿液作為沉淀劑,會(huì)引入較多的金屬陽離子雜質(zhì),增加了除雜成本。如公開號(hào)為CN103624251A、CN103128304A的發(fā)明通過氫氧化鈉沉淀鈷離子,沉淀劑用量為鈷離子8倍以上,導(dǎo)致后續(xù)除Na較難;(2)、前驅(qū)體合成pH低,造成產(chǎn)品收率低。如公開號(hào)為CN101829786A的發(fā)明在pH5.5-6.8條件下沉鈷,反應(yīng)結(jié)束后母液仍呈紅色,鈷離子含量大于1g/L,在工業(yè)大規(guī)模生產(chǎn)情況下,鈷的損失量大;(3)、前驅(qū)體制備中引入添加劑,增加輔料成本的同時(shí),增加了除雜成本。如公開號(hào)為CN102689020A的發(fā)明中往鈷鹽中加表面活性劑和鋁粉,導(dǎo)致后續(xù)除雜成本較高;(4)、前驅(qū)體先經(jīng)過高溫煅燒,再高溫還原制備鈷粉,生產(chǎn)能耗大。如公開號(hào)為CN102560100A的發(fā)明先經(jīng)過350-580℃高溫煅燒后再還原。公開號(hào)為CN101829786A的發(fā)明同樣經(jīng)過400-800℃ 煅燒2-8h后得到氧化鈷粉末,再經(jīng)400-550℃還原4-6h;(5)、制備工序繁雜、流程長,增加處理成本。如公開號(hào)為CN103028735A的發(fā)明先合成碳酸鈷,然后利用草酸將碳酸鈷轉(zhuǎn)化為小粒徑草酸鈷,再進(jìn)行干燥還原,工藝復(fù)雜。綜上所述,目前生產(chǎn)超細(xì)鈷粉的工藝普遍存在成本高的問題,若通過合理的工藝,降低除雜、能耗和工藝流程過長等帶來的成本,將更有利于超細(xì)鈷粉的規(guī)?;a(chǎn),推動(dòng)超細(xì)晶粒硬質(zhì)合金及金剛石工具等行業(yè)更好的發(fā)展。技術(shù)實(shí)現(xiàn)要素:為解決上述問題,本發(fā)明提供了一種低成本制備超細(xì)鈷粉的方法,該制備方法工藝簡單,制備成本較低,解決了現(xiàn)有技術(shù)制備超細(xì)鈷粉成本較高的問題。本發(fā)明所述超細(xì)鈷粉指的是Fsss粒度為0.4-1.0μm的鈷粉。本發(fā)明提供了一種低成本制備超細(xì)鈷粉的方法,包括以下步驟:(1)在反應(yīng)釜中加入反應(yīng)底液,將碳酸銨溶液或碳酸氫銨溶液與鈷鹽溶液加入到所述反應(yīng)底液中,在攪拌條件下進(jìn)行反應(yīng),所述碳酸銨或所述碳酸氫銨與所述鈷鹽中鈷離子的摩爾比為2.5-3.5:1,反應(yīng)體系的pH為6.5-8.5,反應(yīng)溫度為35-70℃,反應(yīng)時(shí)間為0.5-6h,得到含有碳酸鈷的漿料;(2)將所述含有碳酸鈷的漿料進(jìn)行固液分離后得到濾餅,將所述濾餅進(jìn)行漿化得到漿化后的物料,將所述漿化后的物料進(jìn)行恒溫水洗,洗滌結(jié)束后進(jìn)行固液分離,得到碳酸鈷沉淀;將所述碳酸鈷沉淀進(jìn)行干燥、破碎和篩分,得到碳酸鈷前驅(qū)體;(3)將所述碳酸鈷前驅(qū)體置于還原氣氛下進(jìn)行一步還原,所述還原溫度為200-550℃,所述還原時(shí)間為0.5-8h,得到超細(xì)鈷粉。優(yōu)選地,步驟(1)中所述反應(yīng)底液為純水、碳酸鹽溶液或碳酸氫鹽溶液。更優(yōu)選地,步驟(1)中當(dāng)所述反應(yīng)底液為碳酸鹽溶液或碳酸氫鹽溶液時(shí),所述反應(yīng)底液中碳酸鹽或碳酸氫鹽的濃度大于0g/L小于250g/L。更優(yōu)選地,所述碳酸鹽為碳酸銨,所述碳酸氫鹽為碳酸氫銨。優(yōu)選地,步驟(1)中所述鈷鹽為氯化鈷、醋酸鈷、硫酸鈷和硝酸鈷中的至 少一種。本發(fā)明的沉淀劑選用碳酸銨或碳酸氫銨,沒有引入金屬陽離子雜質(zhì),降低了后續(xù)的除雜成本。優(yōu)選地,步驟(1)中,將所述碳酸銨溶液或所述碳酸氫銨溶液與所述鈷鹽溶液并流加入到所述反應(yīng)底液中。根據(jù)反應(yīng)實(shí)際情況通過改變碳酸銨或碳酸氫銨的流量來調(diào)節(jié)反應(yīng)pH。本發(fā)明采用并流加料的方式合成碳酸鈷時(shí),通過調(diào)節(jié)所述碳酸銨溶液或所述碳酸氫銨溶液的流量來調(diào)節(jié)加料過程中pH值,可以避免正流法和逆流法加料過程中pH值的大幅度變化和局部濃度過高現(xiàn)象,有助于產(chǎn)品質(zhì)量的穩(wěn)定和連續(xù)化生產(chǎn)。優(yōu)選地,步驟(1)中,所述鈷鹽溶液中鈷離子濃度為50-160g/L。優(yōu)選地,步驟(1)中,所述碳酸銨溶液或碳酸氫銨溶液的濃度為120-260g/L。步驟(1)中的反應(yīng)體系的pH為6.5-8.5,在該pH范圍內(nèi)可以制備出粒徑更小的碳酸鈷,同時(shí)可以降低生產(chǎn)成本。優(yōu)選地,步驟(1)中,所述反應(yīng)體系的pH為7.0-8.5。優(yōu)選地,步驟(1)中所述攪拌速度為100-400rpm。本發(fā)明在制備碳酸鈷前驅(qū)體過程中,采用不含金屬元素的碳酸銨或碳酸氫銨作為沉淀劑,同時(shí)制備過程中沒有引入添加劑,降低了原料成本和后續(xù)的除雜成本。另外,合成的pH相對(duì)于現(xiàn)有技術(shù)較高,可以提高鈷的產(chǎn)量,降低生產(chǎn)成本。本發(fā)明在一定的反應(yīng)溫度和反應(yīng)時(shí)間范圍內(nèi),可以得到粒徑小、比表面積大和分散性好的碳酸鈷前驅(qū)體,反應(yīng)充分,后續(xù)不需進(jìn)行陳化工藝,在縮短工藝流程、降低加工成本的同時(shí),產(chǎn)品的性能也得到了更好地控制。優(yōu)選地,步驟(2)中,采用板框壓濾機(jī)和微孔過濾器中的至少一種固液分離設(shè)備進(jìn)行所述固液分離。更優(yōu)選地,利用所述板框壓濾機(jī)進(jìn)行固液分離時(shí),壓強(qiáng)為18-22MPa。更優(yōu)選地,利用所述微孔過濾器進(jìn)行固液分離時(shí),壓強(qiáng)為0.1-0.25MPa。固液分離后得到的母液可進(jìn)入回收系統(tǒng)進(jìn)行重復(fù)利用,得到的濾餅進(jìn)行漿 化洗滌。本發(fā)明所使用固液分離設(shè)備是板框壓濾機(jī)或微孔過濾器、或兩種洗滌設(shè)備的組合,在固液分離后得到濾餅,無需對(duì)濾餅進(jìn)行洗滌,直接卸料進(jìn)行后續(xù)的漿化洗滌操作。更優(yōu)選地,步驟(2)中,將所述含有碳酸鈷的漿料采用板框壓濾機(jī)進(jìn)行固液分離得到濾餅。采用板框壓濾機(jī)時(shí),壓力更大,可以提高固液分離速度,即提升了生產(chǎn)效率。優(yōu)選地,步驟(2)中,將所述含有碳酸鈷的漿料進(jìn)行固液分離后得到濾餅,將所述濾餅卸料至漏斗式下料槽,然后用純水沖洗至漿化槽中進(jìn)行漿化,漿化后,得到漿化后的物料,將所述漿化后的物料通過泵輸送至漿洗槽中進(jìn)行恒溫水洗,洗滌結(jié)束后進(jìn)行固液分離。更優(yōu)選地,所述漿化時(shí)間為20min-40min,通過漿化工藝將濾餅分散均勻,有助于將物料通過泵直接輸送至漿洗槽進(jìn)行洗滌,同時(shí),有利于后續(xù)除雜洗滌操作。更優(yōu)選地,步驟(2)中,所述水洗的溫度為0-80℃。進(jìn)一步優(yōu)選地,步驟(2)中,所述水洗的溫度為25-80℃。更優(yōu)選地,步驟(2)中,所述水洗的時(shí)間為0.5-10h。更優(yōu)選地,所述恒溫水洗時(shí)進(jìn)行攪拌,所述攪拌速度為30-200rpm。優(yōu)選地,所述恒溫水洗的次數(shù)為1-4次。每次恒溫水洗后,都要進(jìn)行固液分離,然后進(jìn)行第二次水洗或進(jìn)入后續(xù)工藝。所述水洗溫度、洗滌水量、水洗時(shí)間以及洗滌次數(shù)根據(jù)洗滌過程中物料中的Cl-、NO3-、SO42-或CH3COO-等雜質(zhì)的含量水平?jīng)Q定。優(yōu)選地,第一次洗滌結(jié)束時(shí),以Cl-為例,物料中Cl含量應(yīng)不高于0.8%,若Cl-含量較高則加大水量、延長洗滌時(shí)間;第二次洗滌結(jié)束時(shí),物料中Cl-含量應(yīng)不高于0.08%,若含量高于0.08%,則加大洗水量、延長洗滌時(shí)間;若第二次洗滌結(jié)束后Cl-含量高于0.1%,則進(jìn)行第三次洗滌,直至物料中Cl-含量小于0.08%,進(jìn)入下一個(gè)工序。優(yōu)選地,本發(fā)明還可以根據(jù)漿料中Cl-含量調(diào)整洗滌過程溫度,如果Cl-含量高于控制標(biāo)準(zhǔn),則升高洗滌溫度,Cl-含量較低,則適當(dāng)調(diào)低洗滌溫度。通過控制洗滌過程溫度,在一定程度上可以維持相同洗滌用水量的情況下,增強(qiáng)洗滌效果,進(jìn)而節(jié)約洗滌用水量?,F(xiàn)有技術(shù)的洗滌方式主要是固液分離后,直接將過濾得到的濾餅或?yàn)V渣進(jìn)行簡單地淋洗,或者將濾餅或?yàn)V渣漿化后,進(jìn)行固液分離得到濾餅后再次洗滌濾餅。這些洗滌的方式由于洗滌方式單一、洗滌條件固定,都難以將產(chǎn)物中的雜質(zhì)完全去除。同時(shí)會(huì)造成產(chǎn)品顆粒分布不均勻,一致性差,不利于產(chǎn)品質(zhì)量的穩(wěn)定。與現(xiàn)有技術(shù)中通過檢測(cè)濾液中雜質(zhì)(如Cl-)含量以及洗滌時(shí)間、洗滌水量固定的方式不同。本發(fā)明優(yōu)選地根據(jù)洗滌后物料中的Cl-含量情況控制水洗溫度、洗滌水量和水洗時(shí)間等因素,在優(yōu)選的洗滌溫度下、洗滌水量下、洗滌時(shí)間下以及洗滌次數(shù)下可以得到更好的洗滌效果,因此,本發(fā)明提供的洗滌方法更有利于節(jié)約生產(chǎn)用水及生產(chǎn)時(shí)間,同時(shí),可以達(dá)到更好的除雜效果,最終顯著降低物料中的雜質(zhì)含量。本發(fā)明通過固液分離和洗滌操作可以顯著地降低碳酸鈷中的雜質(zhì)含量,同時(shí)固液分離和漿化洗滌操作連續(xù)化程度高,可以根據(jù)含有碳酸鈷的漿料中的雜質(zhì)含量調(diào)節(jié)洗滌參數(shù),降低產(chǎn)能消耗,增強(qiáng)洗滌效果,有利于規(guī)?;a(chǎn)。優(yōu)選地,步驟(2)中,所述干燥的方法為離心噴霧干燥、閃蒸干燥或鼓風(fēng)干燥。更優(yōu)選地,步驟(2)中,所述離心噴霧干燥的條件為:進(jìn)料口溫度為160-250℃,出料口溫度為70-105℃。進(jìn)一步優(yōu)選地,所述離心噴霧干燥的條件為:進(jìn)料口溫度為180-220℃,出料口溫度為80-100℃。更優(yōu)選地,所述閃蒸干燥條件為:進(jìn)料口溫度為170-230℃,出料口溫度為90-120℃。進(jìn)一步優(yōu)選地,步驟(2)中,所述閃蒸干燥條件為:進(jìn)料口溫度為180-220℃, 出料口溫度為100-110℃。采用所述離心噴霧干燥或所述閃蒸干燥方法時(shí),物料干燥時(shí)間小于5min,相比于現(xiàn)有技術(shù)的干燥方式,大大縮短了干燥時(shí)間,減少干燥過程對(duì)產(chǎn)品性能的影響。優(yōu)選地,所述鼓風(fēng)干燥的條件為:干燥溫度75-140℃,干燥時(shí)間為6-12h。更優(yōu)選干燥溫度為80-120℃。優(yōu)選地,步驟(2)中,在將所述碳酸鈷沉淀干燥后,碳酸鈷中的含水量為小于3.0%。步驟(2)中,在將所述碳酸鈷沉淀干燥后,當(dāng)所述碳酸鈷的粒徑D50>4.5μm時(shí),需要進(jìn)行破碎操作。優(yōu)選地,所述破碎的方法為氣流破碎和機(jī)械破碎中的至少一種。更優(yōu)選地,步驟(2)中,破碎后,對(duì)所述碳酸鈷采用200目篩網(wǎng)進(jìn)行篩分。本發(fā)明制得的碳酸鈷前驅(qū)體的粒徑較小,純度較高。優(yōu)選地,所述碳酸鈷前驅(qū)體的D50粒徑為0.5-3.0μm,松裝密度為0.2-0.5g/cm3,比表面積為40-150m2/g。優(yōu)選地,所述碳酸鈷前驅(qū)體中Cl含量小于等于100ppm,Ca、Na、Mg、Fe元素含量小于等于20ppm,Cu、Zn、Al元素含量小于等于10ppm。超細(xì)顆粒的合成需要在溶液過飽和條件下進(jìn)行,在過飽和溶液中,沉淀劑的加入會(huì)導(dǎo)致碳酸鈷爆炸性成核,形成的碳酸鈷顆粒小、比表面積大,難以進(jìn)行固液分離和除雜。本發(fā)明在沉淀反應(yīng)結(jié)束后,將含有碳酸鈷的漿料通過固液分離后,使得母液去除完全,減少了雜質(zhì)殘留。之后在一定溫度下進(jìn)行高強(qiáng)度的漿化洗滌,促使吸附在碳酸鈷顆粒表面的雜質(zhì)離子脫附,再經(jīng)過固液分離,再次去除部分雜質(zhì)。固液分離和漿化洗滌結(jié)束后,物料經(jīng)過合適條件下的干燥、破碎得到粒徑小、純度高的碳酸鈷顆粒。本發(fā)明采用鈷鹽為原料,碳酸銨或碳酸氫銨為沉淀劑,在一定原料和沉淀劑摩爾比、pH、溫度范圍內(nèi),合成含有碳酸鈷的漿料。然后將所述含碳酸鈷的漿料經(jīng)過固液分離及漿化洗滌后,進(jìn)行干燥、破碎、篩分,最終得到雜質(zhì)含量低、粒徑小、比表面積大的碳酸鈷粉末。相比其他制備方法,本發(fā)明制備碳酸 鈷過程中并未引入任何其他添加劑,生產(chǎn)成本低,流程簡單,且所得產(chǎn)品中金屬元素雜質(zhì)及陰離子雜質(zhì)含量均很低,有利于得到粒徑小、純度高的鈷粉。優(yōu)選地,步驟(3)中,將所述碳酸鈷前驅(qū)體置于多溫區(qū)管式爐或鋼帶式還原爐中進(jìn)行一步還原。更優(yōu)選地,采用所述多溫區(qū)管式爐進(jìn)行一步還原時(shí),還原溫度為200-450℃,還原時(shí)間為5-8h。進(jìn)一步優(yōu)選地,采用所述多溫區(qū)管式爐進(jìn)行一步還原時(shí),還原溫度控制模式采用非線性控制模式,所述非線性控制模式為梯形溫控模式或平臺(tái)溫控模式。進(jìn)一步優(yōu)選地,所述非線性控制模式為梯形溫控模式時(shí),所述還原過程中在所述多溫區(qū)管式爐中分為三個(gè)溫區(qū)分別為進(jìn)爐區(qū)、中間區(qū)和出爐區(qū),所述進(jìn)爐區(qū)和所述出爐區(qū)溫度低于所述中間區(qū)溫度,所述進(jìn)爐區(qū)溫度為200-320℃,所述中間溫區(qū)溫度為320-450℃,所述出爐區(qū)溫度250-350℃,在所述進(jìn)爐區(qū)停留時(shí)間為2-4h,在所述中間溫區(qū)的停留時(shí)間為4-6h,在所述出爐區(qū)中的停留時(shí)間為2-4h。進(jìn)一步優(yōu)選地,所述非線性控制模式為平臺(tái)溫控模式時(shí),所述還原過程中在所述多溫區(qū)管式爐中分為2或3個(gè)溫區(qū),所述2個(gè)溫區(qū)分別為低溫區(qū)和高溫區(qū),所述3個(gè)溫區(qū)分別為第一低溫區(qū)、第二低溫區(qū)和高溫區(qū),所述低溫區(qū)、第一低溫區(qū)或第二低溫區(qū)的溫度各為200-350℃,停留時(shí)間各為3-5h,所述高溫區(qū)的溫度350-450℃,停留時(shí)間為2-4h。更優(yōu)選地,采用所述鋼帶式還原爐進(jìn)行一步還原時(shí),還原溫度為250-550℃,還原時(shí)間為0.5-4h。進(jìn)一步優(yōu)選地,采用所述鋼帶式還原爐進(jìn)行一步還原時(shí),還原溫度控制模式采用非線性控制模式,所述非線性控制模式為梯形溫控模式或平臺(tái)溫控模式。進(jìn)一步優(yōu)選地,所述非線性控制模式為梯形溫控模式時(shí),所述還原過程中在所述多溫區(qū)管式爐中分為三個(gè)溫區(qū)分別為進(jìn)爐區(qū)、中間區(qū)和出爐區(qū),所述進(jìn)爐區(qū)和所述出爐區(qū)溫度低于所述中間區(qū)溫度,所述進(jìn)爐區(qū)溫度為250-450℃,所述中間溫區(qū)溫度為350-550℃,所述出爐區(qū)溫度250-400℃,在所述進(jìn)爐區(qū)停留 時(shí)間為0.1-2h,在所述中間溫區(qū)的停留時(shí)間為0.3-2h,在所述出爐區(qū)中的停留時(shí)間為0.1-2h。進(jìn)一步優(yōu)選地,所述非線性控制模式為平臺(tái)溫控模式時(shí),所述還原過程中在所述多溫區(qū)管式爐中分為2或3個(gè)溫區(qū),所述2個(gè)溫區(qū)分別為低溫區(qū)和高溫區(qū),所述3個(gè)溫區(qū)分別為第一低溫區(qū)、第二低溫區(qū)和高溫區(qū),所述低溫區(qū)、第一低溫區(qū)或第二低溫區(qū)的溫度各為250-400℃,停留時(shí)間分別為0.3-3h,所述高溫區(qū)的溫度350-550℃,停留時(shí)間為0.2-1h。優(yōu)選地,步驟(3)中,所述還原氣氛為氫氣氣氛。優(yōu)選地,步驟(3)中,在所述還原過程中加入氫氣,所述氫氣的流量是4-50m3/h。本發(fā)明在采用非線性溫控模式進(jìn)行一步還原,相對(duì)于現(xiàn)有技術(shù)的先高溫煅燒再還原的技術(shù),降低了氫氣的消耗量,生產(chǎn)能耗大大降低。相對(duì)于線性溫控模式一步還原法,本發(fā)明設(shè)置了低溫段,為物料進(jìn)入還原階段提供了一定的過渡期,在較低溫度下還原時(shí),有利于保持物料的形貌及還原過程樣的均一性,有利于得到性能更均一的鈷粉。后期的高溫段還原,則保證了鈷粉的還原完全,保證了產(chǎn)品質(zhì)量。優(yōu)選地,步驟(3)中,將所述碳酸鈷還原后,進(jìn)行破碎、篩分和混料包裝,得到超細(xì)鈷粉。優(yōu)選地,所述超細(xì)鈷粉的Fsss粒度為0.4-1.0μm。更優(yōu)選地,所述超細(xì)鈷粉的Fsss粒度為0.5-0.8μm。本發(fā)明超細(xì)鈷粉的制備包括前驅(qū)體的合成與前驅(qū)體的還原。所述前驅(qū)體合成過程為液相沉淀法,前驅(qū)體的合成過程中未引入添加劑,減少了原料的雜質(zhì)元素引入量,同時(shí)工藝流程簡單,大大降低了生產(chǎn)成本,制得了粒徑較小、純度較高的碳酸鈷前驅(qū)體。所述前驅(qū)體的還原采用一步還原法,通過采用合理的溫控模式,一步還原制得鈷粉,能耗成本及工藝成本都得到有效控制,最終實(shí)現(xiàn)了低成本條件下規(guī)?;a(chǎn)超細(xì)鈷粉的目的。本發(fā)明提供的低成本制備超細(xì)鈷粉的方法,具有如下有益效果:本發(fā)明采用液相沉淀—一步還原法制備超細(xì)鈷粉,通過優(yōu)化工藝、簡化過程,多途徑縮減生產(chǎn)成本,最終實(shí)現(xiàn)了低成本條件下生產(chǎn)超細(xì)鈷粉的目的。附圖說明圖1是本發(fā)明一實(shí)施例中低成本制備超細(xì)鈷粉方法的流程示意圖;圖2為本發(fā)明實(shí)施例1制備的超細(xì)鈷粉的掃描電鏡(SEM)圖;圖3為本發(fā)明實(shí)施例2制備的超細(xì)鈷粉的掃描電鏡(SEM)圖;圖4為本發(fā)明實(shí)施例3制備的超細(xì)鈷粉的掃描電鏡(SEM)圖。具體實(shí)施方式以下所述是本發(fā)明的優(yōu)選實(shí)施方式,應(yīng)當(dāng)指出,對(duì)于本
技術(shù)領(lǐng)域:
的普通技術(shù)人員來說,在不脫離本發(fā)明原理的前提下,還可以做出若干改進(jìn)和潤飾,這些改進(jìn)和潤飾也視為本發(fā)明的保護(hù)范圍。請(qǐng)參考圖1,圖1是本發(fā)明一實(shí)施例中低成本制備超細(xì)鈷粉方法的流程示意圖,包括以下步驟:S01、在反應(yīng)釜中加入反應(yīng)底液,將碳酸銨溶液或碳酸氫銨溶液與鈷鹽溶液加入到反應(yīng)底液中,在攪拌條件下進(jìn)行反應(yīng),碳酸銨或碳酸氫銨與鈷鹽中鈷離子的摩爾比為2.5-3.5:1,控制反應(yīng)體系的pH為6.5-8.5,反應(yīng)溫度為35-70℃,反應(yīng)時(shí)間為0.5-6h,得到含有碳酸鈷的漿料;S02、將含有碳酸鈷的漿料進(jìn)行固液分離后得到濾餅,將濾餅進(jìn)行漿化得到漿化后的物料,將漿化后的物料進(jìn)行恒溫水洗,洗滌結(jié)束后進(jìn)行固液分離,得到碳酸鈷沉淀;將碳酸鈷沉淀進(jìn)行干燥、破碎和篩分,得到碳酸鈷前驅(qū)體;S03、將碳酸鈷前驅(qū)體置于還原氣氛下進(jìn)行一步還原,還原溫度為200-550℃,還原時(shí)間為0.5-8h,得到超細(xì)鈷粉。本發(fā)明超細(xì)鈷粉的制備包括前驅(qū)體的合成與前驅(qū)體的還原。所述前驅(qū)體合成過程為液相沉淀法,前驅(qū)體的合成過程中未引入添加劑,減少了原料的雜質(zhì) 元素引入量,同時(shí)工藝流程簡單,大大降低了生產(chǎn)成本,制得了粒徑較小、純度較高的碳酸鈷前驅(qū)體。所述前驅(qū)體的還原采用一步還原法,通過采用合理的溫控模式,一步還原制得鈷粉,能耗成本及工藝成本都得到有效控制,最終實(shí)現(xiàn)了低成本條件下生產(chǎn)超細(xì)鈷粉的目的。實(shí)施例1一種低成本制備超細(xì)鈷粉的方法,包括以下步驟:(1)、向合成反應(yīng)釜中加入純水(反應(yīng)底液)至攪拌槳處,升高反應(yīng)釜溫度至55℃后,啟動(dòng)攪拌槳,控制轉(zhuǎn)速為220rpm,同時(shí)并流加入氯化鈷溶液和碳酸氫銨溶液,其中氯化鈷溶液中鈷離子濃度為80g/L,碳酸氫銨溶液濃度為180g/L,通過碳酸氫銨流量調(diào)節(jié)pH,控制反應(yīng)pH在7.5-8.2之間,反應(yīng)溫度為55℃±2℃。反應(yīng)2.5h后停止加料,得到含有碳酸鈷的漿料;碳酸氫銨與氯化鈷中鈷離子的摩爾比為2.6:1;(2)將含有碳酸鈷的漿料輸送至板框壓濾機(jī)進(jìn)行固液分離,壓強(qiáng)為19Mpa,得到母液和濾餅,母液進(jìn)入回收系統(tǒng),濾餅卸料至漏斗式下料槽,然后用純水沖洗至帶攪拌漿的漿化槽中,漿化20min后得到漿化后的物料,將漿化后的物料通過泵輸送至帶攪拌漿的漿洗槽中進(jìn)行恒溫水洗,啟動(dòng)攪拌,攪拌速度為30rpm保持洗滌溫度為60℃,洗滌2.5h。重復(fù)進(jìn)行上述固液分離與漿化洗滌1次,洗滌結(jié)束后將物料經(jīng)板框壓濾機(jī)壓干,得到碳酸鈷沉淀;將碳酸鈷沉淀轉(zhuǎn)移至閃蒸干燥機(jī),進(jìn)料口溫度為210℃,出料口溫度為85℃,使得干燥后粉末水分含量<3%,干燥后物料經(jīng)過氣流破碎、篩分后得到碳酸鈷前驅(qū)體;(3)將碳酸鈷前驅(qū)體送至還原工段的多溫區(qū)鋼帶式還原爐,還原爐中依次設(shè)置三個(gè)溫區(qū),分別為進(jìn)爐區(qū)、中間區(qū)和出爐區(qū),進(jìn)爐區(qū)溫度為450℃,中間溫區(qū)溫度為550℃,出爐區(qū)溫度400℃,在進(jìn)爐區(qū)停留時(shí)間為0.1h,在中間溫區(qū)的停留時(shí)間為0.3h,在所述出爐區(qū)中的停留時(shí)間為0.1h。鋼帶速度為200mm/min,還原后所得鈷粉依次經(jīng)氣流破碎機(jī)、篩分機(jī)、混料包裝等設(shè)備后得到超細(xì)鈷粉,超細(xì)鈷粉的Fsss粒度為0.56μm。實(shí)施例1制得的碳酸鈷前驅(qū)體的D50粒徑為2.8μm,松裝密度為0.45g/cm3,比表面積為87m2/g;碳酸鈷前驅(qū)體中Ca、Na、Fe、Mg含量小于15ppm,Cl含量小于60ppm,雜質(zhì)含量具體參見表1。從表1中可以看出,本實(shí)施例1制得的碳酸鈷前驅(qū)體雜質(zhì)含量小,純度高。表1實(shí)施例1制得的碳酸鈷前驅(qū)體中的雜質(zhì)含量NiCuFeCaMgMnZnPb0.0007%0.0001%0.0008%0.0011%0.0008%0.0002%0.0001%0.0002%CdNaAlSiCrSAsCl0.0001%0.0015%0.0001%0.0005%0.0005%0.0020%0.0001%0.0052%圖2為本發(fā)明實(shí)施例1制備的超細(xì)鈷粉的掃描電鏡(SEM)圖;從圖2中可以看出,實(shí)施例1制得的超細(xì)鈷粉粒徑較小,粒徑均勻分布。實(shí)施例2一種低成本制備超細(xì)鈷粉的方法,包括以下步驟:(1)向合成反應(yīng)釜中加入純水(反應(yīng)底液)至攪拌槳處,升高反應(yīng)釜溫度至65℃后,啟動(dòng)攪拌槳,控制轉(zhuǎn)速為220rpm,同時(shí)并流加入醋酸鈷溶液和碳酸銨溶液,其中醋酸鈷溶液中鈷離子濃度為140g/L,碳酸銨溶液濃度為240g/L。通過碳酸銨流量調(diào)節(jié)pH,控制反應(yīng)pH在7.0-8.0之間,反應(yīng)溫度65℃±2℃。反應(yīng)1h后停止加料,得到含有碳酸鈷的漿料;碳酸銨和醋酸鈷中鈷離子的摩爾比為3.0:1;(2)將含有碳酸鈷的漿料輸送至微孔過濾器進(jìn)行固液分離,壓強(qiáng)為0.2Mpa,得到母液和濾餅,母液進(jìn)入回收系統(tǒng),濾餅卸料至漏斗式下料槽,然后用純水沖洗至帶攪拌漿的漿化槽中,漿化30min后得到漿化后的物料,將漿化后的物料通過泵輸送至帶攪拌漿的漿洗槽中進(jìn)行恒溫水洗,啟動(dòng)攪拌,攪拌速度為200rpm,保持洗滌溫度為45℃,洗滌5h。重復(fù)進(jìn)行上述固液分離與漿化洗滌3次,洗滌結(jié)束后物料經(jīng)微孔過濾器壓干,得到碳酸鈷沉淀;將碳酸鈷沉淀利用閃蒸干燥機(jī)進(jìn)行干燥。進(jìn)料口溫度為195℃,出料口溫度為95℃,使得干燥后粉末水分含量<3%,干燥后物料經(jīng)過氣流破碎、篩分后得到碳酸鈷前驅(qū)體;(3)將碳酸鈷前驅(qū)體送至還原工段的多溫區(qū)管式還原爐,還原爐中依次設(shè)置三個(gè)溫區(qū),分別為進(jìn)爐區(qū)、中間區(qū)和出爐區(qū),進(jìn)爐區(qū)溫度為320℃,中間溫區(qū)溫度為450℃,出爐區(qū)溫度350℃,在進(jìn)爐區(qū)停留時(shí)間為2h,在中間溫區(qū)的停留時(shí)間為4h,在出爐區(qū)中的停留時(shí)間為2h。還原后所得鈷粉依次經(jīng)氣流破碎機(jī)、篩分機(jī)、混料包裝等設(shè)備后得到超細(xì)鈷粉,超細(xì)鈷粉的Fsss粒度為0.65μm。實(shí)施例2制得的碳酸鈷前驅(qū)體的D50粒徑為3.9μm,松裝密度為0.49g/cm3,比表面積為56m2/g;碳酸鈷前驅(qū)體中Ca、Na、Fe、Mg含量小于17ppm,Cl含量小于75ppm,雜質(zhì)含量具體參見表2。從表2中可以看出,本實(shí)施例2制得的碳酸鈷前驅(qū)體雜質(zhì)含量小,純度高。表2實(shí)施例2制得的碳酸鈷前驅(qū)體中的雜質(zhì)含量NiCuFeCaMgMnZnPb0.0010%0.0001%0.0006%0.0013%0.0006%0.0001%0.0001%0.0001%CdNaAlSiCrSAsCl0.0001%0.0014%0.0002%0.0003%0.0004%0.0018%0.0001%0.072%圖3為本發(fā)明實(shí)施例2制備的超細(xì)鈷粉的掃描電鏡(SEM)圖;從圖3中可以看出,實(shí)施例2制得的超細(xì)鈷粉粒徑較小,粒徑均勻分布。實(shí)施例3一種低成本制備超細(xì)鈷粉的方法,包括以下步驟:(1)、向合成反應(yīng)釜中加入純水(反應(yīng)底液)至攪拌槳處,升高反應(yīng)釜溫度至35℃后,啟動(dòng)攪拌槳,控制轉(zhuǎn)速為400rpm,同時(shí)并流加入硫酸鈷溶液和碳酸銨溶液,其中硫酸鈷溶液中鈷離子濃度為100g/L,碳酸銨溶液濃度為200g/L。通過碳銨流量調(diào)節(jié)pH,控制反應(yīng)pH在7.2-8.5之間,反應(yīng)溫度35℃±2℃。反應(yīng)6h后停止加料,得到含有碳酸鈷的漿料;碳酸銨和硫酸鈷中鈷離子的摩爾比為2.5:1;(2)將含有碳酸鈷的漿料輸送至板框壓濾機(jī)進(jìn)行固液分離,壓強(qiáng)為20Mpa,得到母液和濾餅,母液進(jìn)入回收系統(tǒng),濾餅卸料至漏斗式下料槽,然后用純水沖洗至帶攪拌漿的漿化槽中,漿化30min后得到漿化后的物料,將漿化后的物 料通過泵輸送至帶攪拌漿的漿洗槽中進(jìn)行恒溫水洗,啟動(dòng)攪拌,攪拌速度為100rpm,保持洗滌溫度為75℃,洗滌0.5h。重復(fù)進(jìn)行上述固液分離與漿化洗滌2次,洗滌結(jié)束后將物料經(jīng)微孔過濾器壓干,得到碳酸鈷沉淀;將碳酸鈷沉淀利用離心噴霧機(jī)進(jìn)行干燥,進(jìn)料口溫度為220℃,出料口溫度為80℃,使得干燥后粉末水分含量<3%,干燥后物料經(jīng)過渦輪破碎、篩分后得到碳酸鈷前驅(qū)體;(3)將碳酸鈷前驅(qū)體送至還原工段的多溫區(qū)鋼帶式還原爐,還原爐中依次設(shè)置三個(gè)溫區(qū),分別為第一低溫區(qū)、第二低溫區(qū)和高溫區(qū),第一低溫區(qū)和第二低溫區(qū)的溫度為400℃,停留時(shí)間各為0.3h,高溫區(qū)的溫度550℃,停留時(shí)間為1h,鋼帶速度為250mm/min,還原后所得鈷粉依次經(jīng)氣流破碎機(jī)、篩分機(jī)、混料包裝等設(shè)備后得到超細(xì)鈷粉,超細(xì)鈷粉的Fsss粒度為0.45μm。實(shí)施例3制得的碳酸鈷前驅(qū)體的D50粒徑為1.6μm,松裝密度為0.40g/cm3,比表面積為98m2/g;碳酸鈷前驅(qū)體中Ca、Na、Fe、Mg含量小于20ppm,Cl含量小于105ppm,雜質(zhì)含量具體參見表3。從表3中可以看出,本實(shí)施例3制得的碳酸鈷前驅(qū)體雜質(zhì)含量小,純度高。表3實(shí)施例3制得的碳酸鈷前驅(qū)體中的雜質(zhì)含量NiCuFeCaMgMnZnPb0.0013%0.0001%0.0008%0.0015%0.0007%0.0001%0.0002%0.0001%CdNaAlSiCrSAsCl0.0001%0.0015%0.0003%0.0002%0.0003%0.0016%0.0001%0.0103%圖4為本發(fā)明實(shí)施例3制備的超細(xì)鈷粉的掃描電鏡(SEM)圖;從圖4中可以看出,實(shí)施例3制得的超細(xì)鈷粉粒徑較小,粒徑均勻分布。實(shí)施例4一種低成本制備超細(xì)鈷粉的方法,包括以下步驟:(1)向合成反應(yīng)釜中加入純水(反應(yīng)底液)至攪拌槳處,升高反應(yīng)釜溫度至45℃后,啟動(dòng)攪拌槳,控制轉(zhuǎn)速為250rpm,同時(shí)并流加入硝酸鈷溶液和碳酸氫銨溶液,其中硝酸鈷溶液中鈷離子濃度為160g/L,碳酸氫銨溶液濃度為260g/L。通過碳酸氫銨流量調(diào)節(jié)pH,控制反應(yīng)pH在6.5-8.0之間,反應(yīng)溫度為45℃±2℃。 反應(yīng)3.5h后停止加料,得到含有碳酸鈷的漿料;碳酸氫銨和硝酸鈷中鈷離子的摩爾比為3.5:1;(2)將含有碳酸鈷的漿料輸送至微孔過濾器進(jìn)行固液分離,壓強(qiáng)為0.18Mpa,得到母液和濾餅,母液進(jìn)入回收系統(tǒng),濾餅卸料至漏斗式下料槽,然后用純水沖洗至帶攪拌漿的漿化槽中,漿化30min后得到漿化后的物料,將漿化后的物料通過泵輸送至帶攪拌漿的漿洗槽中進(jìn)行恒溫水洗,啟動(dòng)攪拌,攪拌速度為100rpm,保持洗滌溫度為25℃,洗滌6h。重復(fù)進(jìn)行上述固液分離與漿化洗滌2次,洗滌結(jié)束后物料經(jīng)板框壓濾機(jī)壓干,得到碳酸鈷沉淀。將碳酸鈷沉淀轉(zhuǎn)移至閃蒸干燥機(jī),進(jìn)料口溫度為200℃,出料口溫度為85℃,使得干燥后粉末水分含量<3%,干燥后物料經(jīng)過氣流破碎、篩分后得到碳酸鈷前驅(qū)體;(3)將碳酸鈷前驅(qū)體送至還原工段的多溫區(qū)鋼帶式還原爐,還原爐中依次設(shè)置三個(gè)溫區(qū),分別為進(jìn)爐區(qū)、中間區(qū)和出爐區(qū),進(jìn)爐區(qū)溫度為250℃,中間溫區(qū)溫度為350℃,出爐區(qū)溫度250℃,在進(jìn)爐區(qū)停留時(shí)間為2h,在中間溫區(qū)的停留時(shí)間為1h,在出爐區(qū)中的停留時(shí)間為1h。鋼帶速度為160mm/min,還原后所得鈷粉依次經(jīng)氣流破碎機(jī)、篩分機(jī)、混料包裝等設(shè)備后得到超細(xì)鈷粉,超細(xì)鈷粉的Fsss粒度為0.59μm。實(shí)施例4制得的碳酸鈷前驅(qū)體的D50粒徑為3.4μm,松裝密度為0.48g/cm3,比表面積為65m2/g;碳酸鈷前驅(qū)體中Ca、Na、Fe、Mg含量小于16ppm,Cl含量小于76ppm,雜質(zhì)含量具體參見表4,從表4中可以看出,本實(shí)施例4制得的碳酸鈷前驅(qū)體雜質(zhì)含量小,純度高。表4實(shí)施例4制得的碳酸鈷前驅(qū)體中的雜質(zhì)含量NiCuFeCaMgMnZnPb0.0009%0.0002%0.0005%0.0010%0.0003%0.0002%0.0001%0.0001%CdNaAlSiCrSAsCl0.0001%0.0011%0.0002%0.0002%0.0002%0.0015%0.0001%0.0065%實(shí)施例5一種低成本制備超細(xì)鈷粉的方法,包括以下步驟:(1)向合成反應(yīng)釜中加入純水(反應(yīng)底液)至攪拌槳處,升高反應(yīng)釜溫度 至70℃后,啟動(dòng)攪拌槳,控制轉(zhuǎn)速為100rpm,同時(shí)并流加入氯化鈷溶液和碳銨溶液,其中氯化鈷溶液中鈷離子濃度為135g/L,碳酸銨溶液濃度為260g/L。通過碳酸銨流量調(diào)節(jié)pH,控制反應(yīng)pH在7.1-8.3之間,反應(yīng)溫度為70℃±2℃。反應(yīng)0.5h后停止加料,得到含有碳酸鈷的漿料;碳酸銨和氯化鈷中鈷離子的摩爾比為2.8:1;(2)將含有碳酸鈷的漿料輸送至板框壓濾機(jī)進(jìn)行固液分離,壓強(qiáng)為19Mpa,得到母液和濾餅,母液進(jìn)入回收系統(tǒng),濾餅卸料至漏斗式下料槽,然后用純水沖洗至帶攪拌漿的漿化槽中,漿化40min后得到漿化后的物料,將漿化后的物料通過泵輸送至帶攪拌漿的漿洗槽中進(jìn)行恒溫水洗,啟動(dòng)攪拌,攪拌速度為200rpm,保持洗滌溫度為55℃,洗滌3.0h。重復(fù)進(jìn)行上述固液分離與漿化洗滌1次,洗滌結(jié)束后物料經(jīng)板框壓濾機(jī)壓干,得到碳酸鈷沉淀;將碳酸鈷沉淀轉(zhuǎn)移至閃蒸干燥機(jī),進(jìn)料口溫度為210℃,出料口溫度為92℃,使得干燥后粉末水分含量<3%,干燥后物料經(jīng)過氣流破碎、篩分后得到碳酸鈷前驅(qū)體;(3)將碳酸鈷前驅(qū)體送至還原工段的多溫區(qū)管式還原爐,還原爐中依次設(shè)置兩個(gè)溫區(qū),分別為低溫區(qū)和高溫區(qū),低溫區(qū)的溫度為200℃,停留時(shí)間為4h,高溫區(qū)的溫度350℃,停留時(shí)間為4h。還原后所得鈷粉依次經(jīng)氣流破碎機(jī)、篩分機(jī)、混料包裝等設(shè)備后得到超細(xì)鈷粉,超細(xì)鈷粉的Fsss粒度為0.96μm。實(shí)施例5制得的碳酸鈷前驅(qū)體的D50粒徑為4.4μm,松裝密度為0.49g/cm3,比表面積為52m2/g;碳酸鈷前驅(qū)體中Ca、Na、Fe、Mg含量小于18ppm,Cl含量小于65ppm,雜質(zhì)含量具體參見表5。從表5中可以看出,本實(shí)施例5制得的碳酸鈷前驅(qū)體雜質(zhì)含量小,純度高。表5實(shí)施例5制得的碳酸鈷前驅(qū)體中的雜質(zhì)含量NiCuFeCaMgMnZnPb0.0012%0.0001%0.0007%0.0013%0.0005%0.0001%0.0001%0.0001%CdNaAlSiCrSAsCl0.0001%0.0016%0.0001%0.0002%0.0003%0.0017%0.0001%0.060%本發(fā)明采用液相沉淀-一步還原法制備超細(xì)鈷粉,通過優(yōu)化工藝、簡化過程,多途徑縮減生產(chǎn)成本,最終實(shí)現(xiàn)了低成本條件下規(guī)?;a(chǎn)超細(xì)鈷粉的目的。以上所述是本發(fā)明的優(yōu)選實(shí)施方式,應(yīng)當(dāng)指出,對(duì)于本
技術(shù)領(lǐng)域:
的普通技術(shù)人員來說,在不脫離本發(fā)明原理的前提下,還可以做出若干改進(jìn)和潤飾,這些改進(jìn)和潤飾也視為本發(fā)明的保護(hù)范圍。當(dāng)前第1頁1 2 3