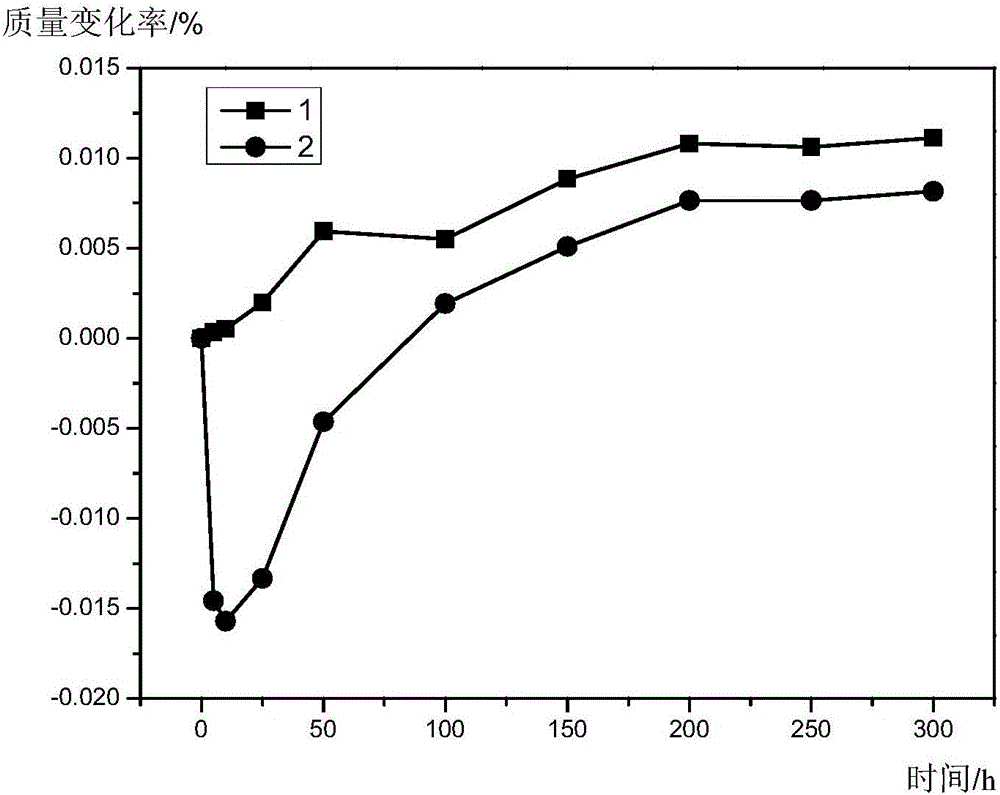
本發(fā)明涉及復(fù)合材料
技術(shù)領(lǐng)域:
,尤其涉及一種超高溫?zé)峤Y(jié)構(gòu)復(fù)合材料界面層的制備方法。
背景技術(shù):
:碳化硅具有優(yōu)良的高溫強(qiáng)度、高溫穩(wěn)定性而得到廣泛關(guān)注,但單體碳化硅陶瓷韌性低,易導(dǎo)致材料災(zāi)難性破壞。以連續(xù)碳化硅纖維增韌碳化硅制備碳化硅纖維增強(qiáng)碳化硅復(fù)合材料可以明顯改善單體陶瓷韌性,在高溫結(jié)構(gòu)材料、熔融反應(yīng)堆以及高溫結(jié)構(gòu)吸波材料等領(lǐng)域具有廣闊的應(yīng)用前景。界面相是碳化硅纖維增強(qiáng)碳化硅復(fù)合材料力學(xué)性能及其他性能的實(shí)現(xiàn)的關(guān)鍵因素之一,合適的界面相、適當(dāng)?shù)慕缑嫦嗪穸饶苡行У恼T導(dǎo)基體微裂紋偏轉(zhuǎn),使纖維橋聯(lián)、纖維拔出等增韌機(jī)制得以發(fā)揮。碳化硅纖維增強(qiáng)碳化硅復(fù)合材料通常采用熱解碳和六方氮化硼作為界面相。其中,熱解碳具有特殊的層狀晶體結(jié)構(gòu),制備來源廣泛,與纖維和基體的相容性好,具有良好的力學(xué)性能。但是熱解碳極易氧化,在高溫下,當(dāng)界面層全部被氧化后,纖維和基體就會被氧化形成氧化硅層,從而最終將纖維和基體粘結(jié)在一起,界面的強(qiáng)結(jié)合會阻止纖維的滑移和拔出,致材料表現(xiàn)為脆性,影響了碳化硅纖維增強(qiáng)碳化硅復(fù)合材料高溫力學(xué)性能的發(fā)揮。此外,采用具有與熱解碳相似晶體結(jié)構(gòu)的六方氮化硼作為界面層,與熱解碳相比,其具有較好的抗氧化性能,氧化后形成的玻璃態(tài)氧化硼能夠彌補(bǔ)纖維基體間的間隙,阻礙氧的擴(kuò)散,因此復(fù)合材料表現(xiàn)出較好的抗氧化性。但是六方氮化硼作界面層存在以下問題:(1)制備通常采用的氣源(三氟化硼、氨)對碳化硅纖維具有腐蝕性,會導(dǎo)致纖維的損傷;(2)氮化硼界面相內(nèi)部及其與纖維之間的結(jié)合較弱,往往需要后繼高溫?zé)崽幚韥砀纳破浣Y(jié)合,但高溫?zé)崽幚頃μ蓟枥w維,特別是會對高氧含量的碳化硅纖維造成損傷;(3)氮化硼氧化產(chǎn)物氧化硼在高溫,特別是在高于1300℃時容易揮發(fā)損失,喪失其對氧的阻礙作用,同時液態(tài)的氧化硼會溶解碳化硅氧化形成的氧化硅,形成低熔點(diǎn)硅硼化合物,增加氧的擴(kuò)散能力,促進(jìn)碳化硅的消耗;(4)玻璃態(tài)的氧化硼或硅硼玻璃會與纖維及基體形成強(qiáng)結(jié)合,破壞復(fù)合材料的弱結(jié)合界面,降低復(fù)合材料的韌性。熱解碳和六方氮化硼界面層均存在高溫抗氧化性差的問題,嚴(yán)重制約了碳化硅纖維增強(qiáng)碳化硅復(fù)合材料高溫力學(xué)性能的發(fā)揮,因此,開發(fā)抗氧化的界面相,提高碳化硅纖維增強(qiáng)碳化硅復(fù)合材料高溫力學(xué)性能是非常有意義的。技術(shù)實(shí)現(xiàn)要素:本發(fā)明的目的是提供一種超高溫?zé)峤Y(jié)構(gòu)復(fù)合材料界面層的制備方法,旨在解決現(xiàn)有技術(shù)的超高溫?zé)峤Y(jié)構(gòu)復(fù)合材料其高溫抗氧化性差,制約高溫力學(xué)性能發(fā)揮的問題。本發(fā)明解決其技術(shù)問題所采用的技術(shù)方案是:一種超高溫?zé)峤Y(jié)構(gòu)復(fù)合材料界面層的制備方法,包括:在初始纖維預(yù)制體的表面制備碳化硅層,制備一級纖維預(yù)制體;在所述一級纖維預(yù)制體的表面制備多孔莫來石層,制備二級纖維預(yù)制體;在所述二級纖維預(yù)制體的表面制備碳化硅層。在此基礎(chǔ)上,進(jìn)一步地,在所述一級纖維預(yù)制體的表面制備多孔莫來石層,制備二級纖維預(yù)制體的步驟,具體為:采用仲丁醇鋁作為鋁源,正硅酸乙酯作為硅源,乙酰乙酸乙酯作為螯合劑,將質(zhì)量比為第一預(yù)定比值的仲丁醇鋁、正硅酸乙酯、乙酰乙酸乙酯溶解于乙醇中,攪拌均勻,制備第一混合液;將與仲丁醇鋁的質(zhì)量比為第二預(yù)定比值的水加入到所述第一混合液中,攪拌均勻,制備第二混合液;將所述一級纖維預(yù)制體在所述第二混合液中進(jìn)行真空浸漬,保溫使其凝膠化,制備凝膠化的纖維預(yù)制體;采用高溫裂解的工藝,在所述凝膠化的纖維預(yù)制體的表面制備莫來石層,制備二級纖維預(yù)制體。在此基礎(chǔ)上,進(jìn)一步地,所述第一預(yù)定比值為50:1:26?;蛘?,進(jìn)一步地,所述第二預(yù)定比值為1:2。在上述任意實(shí)施例的基礎(chǔ)上,進(jìn)一步地,所述在初始纖維預(yù)制體的表面制備碳化硅層,制備一級纖維預(yù)制體的步驟中,采用氣相滲積工藝制備碳化硅層。在此基礎(chǔ)上,進(jìn)一步地,所述氣相滲積工藝中,以三氯甲基硅烷為硅源?;蛘?,進(jìn)一步地,所述氣相滲積工藝中,以氬氣為稀釋氣體?;蛘?,進(jìn)一步地,所述氣相滲積工藝中,滲積溫度為1000℃。在上述任意實(shí)施例的基礎(chǔ)上,進(jìn)一步地,所述在所述二級纖維預(yù)制體的表面制備碳化硅層的步驟中,采用氣相滲積工藝制備碳化硅層。在上述任意實(shí)施例的基礎(chǔ)上,進(jìn)一步地,所述初始纖維預(yù)制體為Hi-Nicalon纖維或Hi-NicalontypeS纖維。本發(fā)明的有益效果是:本發(fā)明提供了一種超高溫?zé)峤Y(jié)構(gòu)復(fù)合材料界面層的制備方法,該方法在超高溫?zé)峤Y(jié)構(gòu)復(fù)合材料的纖維和基體之間設(shè)有三層結(jié)構(gòu)的復(fù)合材料界面層,自纖維向外分別為碳化硅層、多孔莫來石層、碳化硅層。碳化硅層可以防止元素擴(kuò)散,保護(hù)基體與纖維性能不損失;多孔莫來石層具有優(yōu)異的高溫抗氧化能力,高溫穩(wěn)定性好,多孔結(jié)構(gòu)起到誘導(dǎo)微裂紋偏轉(zhuǎn)的作用,有效保障了纖維橋聯(lián)、纖維拔出等增韌機(jī)制的發(fā)揮;多層復(fù)合界面層有利于微裂紋偏轉(zhuǎn)。因此具有該界面層的超高溫?zé)峤Y(jié)構(gòu)復(fù)合材料具有優(yōu)異的高溫抗氧化能力和優(yōu)異的高溫力學(xué)性能。附圖說明下面結(jié)合附圖和實(shí)施例對本發(fā)明進(jìn)一步說明。圖1示出了本發(fā)明實(shí)施例提供的一種超高溫?zé)峤Y(jié)構(gòu)復(fù)合材料界面層的制備方法的流程圖;圖2示出了本發(fā)明實(shí)施例提供的一種復(fù)合材料氧化質(zhì)量與時間的關(guān)系圖。具體實(shí)施方式為了使本發(fā)明的目的、技術(shù)方案及優(yōu)點(diǎn)更加清楚明白,以下結(jié)合附圖及實(shí)施例,對本發(fā)明進(jìn)行進(jìn)一步詳細(xì)說明。應(yīng)當(dāng)理解,此處所描述的具體實(shí)施例僅用以解釋本發(fā)明,并不限定本發(fā)明。具體實(shí)施例一如圖1所示,本發(fā)明實(shí)施例提供了一種超高溫?zé)峤Y(jié)構(gòu)復(fù)合材料界面層的制備方法,包括:步驟S101,在初始纖維預(yù)制體的表面制備碳化硅層,制備一級纖維預(yù)制體;步驟S102,在一級纖維預(yù)制體的表面制備多孔莫來石層,制備二級纖維預(yù)制體;步驟S103,在二級纖維預(yù)制體的表面制備碳化硅層。本發(fā)明實(shí)施例在超高溫?zé)峤Y(jié)構(gòu)復(fù)合材料的纖維和基體之間設(shè)有三層結(jié)構(gòu)的復(fù)合材料界面層,自纖維向外分別為碳化硅層、多孔莫來石層、碳化硅層。碳化硅層可以防止元素擴(kuò)散,保護(hù)基體與纖維性能不損失;多孔莫來石層具有優(yōu)異的高溫抗氧化能力,高溫穩(wěn)定性好,多孔結(jié)構(gòu)起到誘導(dǎo)微裂紋偏轉(zhuǎn)的作用,有效保障了纖維橋聯(lián)、纖維拔出等增韌機(jī)制的發(fā)揮;多層復(fù)合界面層有利于微裂紋偏轉(zhuǎn)。因此具有該界面層的超高溫?zé)峤Y(jié)構(gòu)復(fù)合材料具有優(yōu)異的高溫抗氧化能力和優(yōu)異的高溫力學(xué)性能。本發(fā)明實(shí)施例對溶膠凝膠法制備多孔莫來石層的原料和方式不做限定,優(yōu)選的,制備多孔莫來石層的方式可以具體為:采用仲丁醇鋁作為鋁源,正硅酸乙酯作為硅源,乙酰乙酸乙酯作為螯合劑,將質(zhì)量比為第一預(yù)定比值的仲丁醇鋁、正硅酸乙酯、乙酰乙酸乙酯溶解于乙醇中,攪拌均勻,制備第一混合液;將與仲丁醇鋁的質(zhì)量比為第二預(yù)定比值的水加入到第一混合液中,攪拌均勻,制備第二混合液;將一級纖維預(yù)制體在第二混合液中進(jìn)行真空浸漬,加熱使其凝膠化,而后采用高溫裂解的工藝,在一級纖維預(yù)制體的表面制備莫來石層,制備二級纖維預(yù)制體。本發(fā)明實(shí)施例對鋁源仲丁醇鋁、硅源正硅酸乙酯、螯合劑乙酰乙酸乙酯的質(zhì)量比不做限定,優(yōu)選的,仲丁醇鋁、正硅酸乙酯、乙酰乙酸乙酯的質(zhì)量比可以為50:1:26。本發(fā)明實(shí)施例對用于制備第二混合液的水的質(zhì)量不做限定,優(yōu)選的,水和仲丁醇鋁的質(zhì)量比可以為1:2。本發(fā)明實(shí)施例對步驟S101和步驟S103中制備碳化硅層的工藝不做限定,優(yōu)選的,可以采用氣相滲積工藝制備碳化硅層。本發(fā)明實(shí)施例對氣相滲積工藝參數(shù)不做限定,優(yōu)選的,可以采用三氯甲基硅烷作為硅源。采用三氯甲基硅烷作為硅源的好處是,三氯甲基硅烷分子中Si和C等原子數(shù),易得到化學(xué)分子計(jì)量的SiC,并且滲積溫度較寬,工藝易于控制,因此成為最常用的氣相滲積SiC的氣體。本發(fā)明實(shí)施例對氣相滲積工藝參數(shù)不做限定,優(yōu)選的,可以采用氬氣作為稀釋氣體。采用氬氣作為稀釋氣體的好處是,氬氣作為稀有氣體,化學(xué)性質(zhì)穩(wěn)定,不參與氣相滲積反應(yīng),價格低廉,作為稀釋氣體能有效的起到減緩反應(yīng)速率,增加氣體分子自由程的作用,有利于得到均勻、致密的SiC界面相。本發(fā)明實(shí)施例對氣相滲積工藝參數(shù)不做限定,優(yōu)選的,滲積溫度可以為1000℃。表1滲積溫度與彎曲強(qiáng)度的關(guān)系滲積溫度(℃)彎曲強(qiáng)度(MPa)900329950573100086010506831100554如表1所示,復(fù)合材料的彎曲強(qiáng)度隨滲積溫度發(fā)生變化。本發(fā)明實(shí)施例中的方法對所適用的纖維預(yù)制體的類型不做限定,優(yōu)選的,初始纖維預(yù)制體為Hi-Nicalon纖維或Hi-NicalontypeS纖維。作為第2代碳化硅纖維的Hi-Nicalon纖維,其氧的質(zhì)量分?jǐn)?shù)降低,自由碳的質(zhì)量分?jǐn)?shù)相對較高,碳化硅晶粒的尺寸較第1代大,纖維的耐熱性有一定提高,保持最大抗拉強(qiáng)度的溫度從第1代的1200℃提高到1300℃;Hi-NicalontypeS纖維由亞微米β-SiC晶粒、少量碳和痕量氧組成,體現(xiàn)出高的楊氏模量,高的抗蠕變和抗氧化性能及1600℃下好的熱穩(wěn)定性。在上述任意實(shí)施例的基礎(chǔ)上,本發(fā)明實(shí)施例還可以包括:對所述三級纖維預(yù)制體進(jìn)行致密化,制備超高溫?zé)峤Y(jié)構(gòu)復(fù)合材料。本發(fā)明實(shí)施例對三級纖維預(yù)制體致密化的方式不做限定,優(yōu)選的,其可以具體為:對三級纖維預(yù)制體進(jìn)行真空浸漬和高溫裂解,制備超高溫?zé)峤Y(jié)構(gòu)中間產(chǎn)物;對超高溫?zé)峤Y(jié)構(gòu)中間產(chǎn)物進(jìn)行稱重,當(dāng)超高溫?zé)峤Y(jié)構(gòu)中間產(chǎn)物相對于三級纖維預(yù)制體的增重大于或等于預(yù)定比值時,重復(fù)對超高溫?zé)峤Y(jié)構(gòu)中間產(chǎn)物進(jìn)行真空浸漬和高溫裂解;當(dāng)超高溫?zé)峤Y(jié)構(gòu)中間產(chǎn)物相對于三級纖維預(yù)制體的增重小于預(yù)定比值時,選用該超高溫?zé)峤Y(jié)構(gòu)中間產(chǎn)物作為超高溫?zé)峤Y(jié)構(gòu)復(fù)合材料。采用多次真空浸漬和高溫裂解的方式制備超高溫?zé)峤Y(jié)構(gòu)復(fù)合材料,其工藝成熟,效率高。本發(fā)明實(shí)施例對真空浸漬和高溫裂解后所制備的超高溫?zé)峤Y(jié)構(gòu)中間產(chǎn)物相對于三級纖維預(yù)制體的增重不做限定,優(yōu)選的,超高溫?zé)峤Y(jié)構(gòu)中間產(chǎn)物相對于三級纖維預(yù)制體的增重的預(yù)定比值為1%。本發(fā)明實(shí)施例中,在對三級纖維預(yù)制體進(jìn)行真空浸漬的步驟里,對所選用的浸漬劑不做限定,優(yōu)選的,可以采用聚碳硅烷的二甲苯溶液作為浸漬劑。本發(fā)明實(shí)施例對聚碳硅烷的二甲苯溶液的溶質(zhì)質(zhì)量分?jǐn)?shù)不做限定,聚碳硅烷的二甲苯溶液質(zhì)量分?jǐn)?shù)越高,熱解所得陶瓷產(chǎn)率越高,同時,考慮到浸漬效果,聚碳硅烷的二甲苯溶液的質(zhì)量分?jǐn)?shù)應(yīng)越低越好,以保證粘度盡可能的低,因此,優(yōu)選的,聚碳硅烷的二甲苯溶液的溶質(zhì)質(zhì)量分?jǐn)?shù)為50%。如表2所示,當(dāng)聚碳硅烷的二甲苯溶液的溶質(zhì)質(zhì)量分?jǐn)?shù)為50%~70%時,復(fù)合材料黏度為83~1027mPa·s。表2聚碳硅烷的二甲苯溶液的溶質(zhì)質(zhì)量分?jǐn)?shù)與粘度的關(guān)系聚碳硅烷的二甲苯溶液的溶質(zhì)質(zhì)量分?jǐn)?shù)(%)粘度(mPa·s)701027605255083本發(fā)明實(shí)施例對氣相滲積工藝參數(shù)不做限定,優(yōu)選的,氣相滲積工藝中,可以采用三氯甲基硅烷為硅源,氬氣為稀釋氣體,氫氣為載氣。其具體工藝參數(shù)可以如下:以三氯甲基硅烷為硅源,氬氣為稀釋氣體,氣流速度為50~80cm3/min,稀釋比為9~11,氫氣為載氣,氣流速度為150~200cm3/min,爐內(nèi)壓強(qiáng)為5~10kPa,滲積溫度為900℃~1100℃,滲積時間為2h。表3氣相滲積工藝參數(shù)與復(fù)合材料彎曲強(qiáng)度的關(guān)系如表3所示,隨著氣相滲積工藝參數(shù)的變化,復(fù)合材料的彎曲強(qiáng)度也隨之改變。具體實(shí)施例二本發(fā)明實(shí)施例提供了一種超高溫?zé)峤Y(jié)構(gòu)復(fù)合材料界面層的制備方法,并在此基礎(chǔ)上對具有該界面層的復(fù)合材料其性能做了測試,流程如下:步驟1,在3DHi-Nicalon纖維預(yù)制體上制備SiC層:對3DHi-Nicalon纖維預(yù)制體進(jìn)行清潔,放入氣相沉積爐內(nèi)進(jìn)行氣相滲積。滲積工藝為:以三氯甲基硅烷(MTS)為硅源,置于60℃鼓泡罐中,以氫氣(H2)為載氣,氣流速度為200cm3/min,氬氣(Ar)為稀釋氣體,氣流速度為70cm3/min,混合氣體壓強(qiáng)為5kPa,滲積溫度為1000℃,滲積時間為2h;步驟2,在步驟1所得纖維上制備多孔3Al2O33·2SiO22層:1)將仲丁醇鋁(ASB)作為鋁源,正硅酸乙酯(TEO)作為硅源,乙酰乙酸乙酯(EAcAc)作為螯合劑,按照質(zhì)量比(ASB:TEO:EAcAc)為50:1:26,溶解于乙醇中,攪拌均勻,得到質(zhì)量分?jǐn)?shù)為20%的溶液。2)按照質(zhì)量比(H2O:ASB)為1:2向混合液中加入蒸餾水,并攪拌使之均勻水解。3)將步驟1所得纖維置于在真空浸漬罐中浸漬,并在70℃保溫5h,使之凝膠化。4)通N2保護(hù),在沉積爐中加熱至100℃保溫1h,揮發(fā)凝膠中游離的有機(jī)單質(zhì),隨后以5℃/min升溫至500℃保溫1h,使有機(jī)物裂解轉(zhuǎn)化為無機(jī)物,隨后以1℃/min升溫至1200℃保溫1h,使Al2O3和SiO2反應(yīng)產(chǎn)生莫來石,再以1℃/min降溫至室溫,得到多孔3Al2O3·2SiO2層;步驟3,在步驟2所得纖維上制備SiC層:以三氯甲基硅烷(MTS)為硅源,置于60℃鼓泡罐中,以氫氣(H2)為載氣,氣流速度為200cm3/min,氬氣(Ar)為稀釋氣體,氣流速度為70cm3/min,混合氣體壓強(qiáng)為5kPa,滲積溫度為1000℃,滲積時間為2h;步驟4,利用PIP法在步驟3所得預(yù)制體上制備SiCf/SiC復(fù)合材料:1)將質(zhì)量分?jǐn)?shù)為50%的聚碳硅烷的二甲苯溶液,與步驟3所得預(yù)制體放入真空浸漬機(jī)中,真空浸漬。2)將1)所得預(yù)制體放入氣相沉積爐中加熱裂解,裂解工藝為:在氬氣保護(hù)下,以5℃/min升溫至1200℃并保溫1h后,以5℃/min降溫至室溫;3)重復(fù)1)、2)過程,直到材料增重小于1%為止。步驟5,對步驟4所制得的復(fù)合材料進(jìn)行在管式爐內(nèi)進(jìn)行靜態(tài)空氣高溫抗氧化考核:考核條件為:管式爐內(nèi)溫度為1100℃,空氣流速4.4cm/s,總時長為300h。分別在0、5h、10h、25h、50h、100h、150h、200h、250h、300h測量試樣重量,考核結(jié)果如圖2所示,曲線1為本發(fā)明實(shí)施例提供的熱段復(fù)合材料氧化質(zhì)量變化,曲線2為具有碳界面的熱端復(fù)合材料氧化質(zhì)量變化。對比發(fā)現(xiàn),曲線1與曲線2前期質(zhì)量變化差異明顯,曲線2在氧化前期迅速失重,抗氧化能力差,與之相比曲線1隨著時間的延長略有增重,且后期質(zhì)量變化與曲線2趨勢相同,這是由于基體SiC氧化所致。步驟6,對步驟4所得SiCf/SiC復(fù)合材料進(jìn)行彎曲強(qiáng)度測試:試樣尺寸為45*4*3mm,跨距為30mm,加載速度為0.5mm/min,測試其1100℃氧化10h前后的彎曲強(qiáng)度。并與PyC界面的SiCf/SiC復(fù)合材料進(jìn)行對比。如表4所示,編號1為本發(fā)明實(shí)施例提及的熱段復(fù)合材料,編號2為具有碳界面的熱段復(fù)合材料。對比發(fā)現(xiàn)編號1在為氧化時的彎曲強(qiáng)度略低于編號2,但是經(jīng)10h氧化后,編號2的彎曲強(qiáng)度損失54%,而編號1的彎曲強(qiáng)度無明顯變化,表明本發(fā)明實(shí)施例提及的熱端復(fù)合材料具有優(yōu)良的常溫和高溫力學(xué)性能、具有良好的抗氧化能力。表4氧化前后復(fù)合材料的彎曲強(qiáng)度本發(fā)明提供了一種超高溫?zé)峤Y(jié)構(gòu)復(fù)合材料界面層的制備方法,該方法在超高溫?zé)峤Y(jié)構(gòu)復(fù)合材料的纖維和基體之間設(shè)有三層結(jié)構(gòu)的復(fù)合材料界面層,自纖維向外分別為碳化硅層、多孔莫來石層、碳化硅層。碳化硅層可以防止元素擴(kuò)散,保護(hù)基體與纖維性能不損失;多孔莫來石層具有優(yōu)異的高溫抗氧化能力,高溫穩(wěn)定性好,多孔結(jié)構(gòu)起到誘導(dǎo)微裂紋偏轉(zhuǎn)的作用,有效保障了纖維橋聯(lián)、纖維拔出等增韌機(jī)制的發(fā)揮;多層復(fù)合界面層有利于微裂紋偏轉(zhuǎn)。因此該方法制備的超高溫?zé)峤Y(jié)構(gòu)復(fù)合材料具有優(yōu)異的高溫抗氧化能力和優(yōu)異的高溫力學(xué)性能。盡管本發(fā)明已進(jìn)行了一定程度的描述,明顯地,在不脫離本發(fā)明的精神和范圍的條件下,可進(jìn)行各個條件的適當(dāng)變化。可以理解,本發(fā)明不限于所述實(shí)施方案,而歸于權(quán)利要求的范圍,其包括所述每個因素的等同替換。當(dāng)前第1頁1 2 3