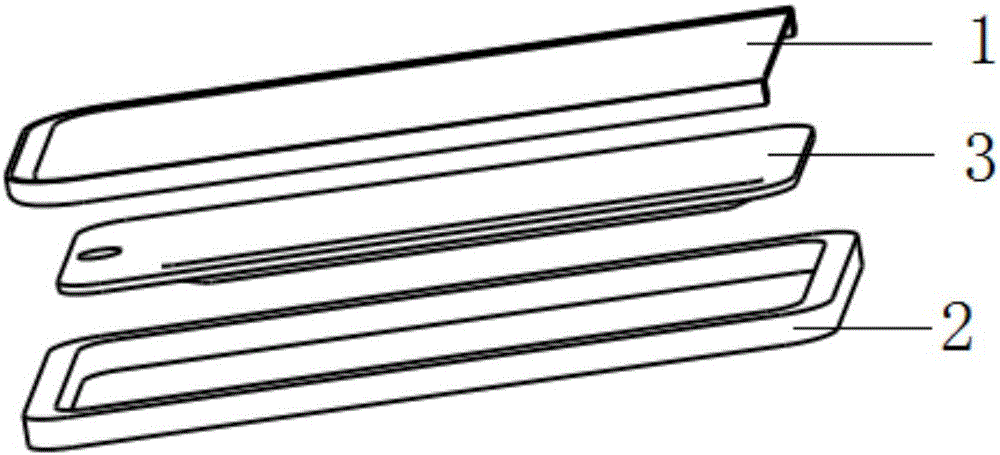
本發(fā)明屬于動鐵受話器
技術領域:
,具體涉及一種振膜成型方法。
背景技術:
:振膜一直是揚聲器、受話器設計中的核心部件,通過振膜振動完成電聲轉換的過程。目前,動鐵受話器的振膜主要由三個部分組成(見圖1):薄膜(圖1中1所示)、支架(圖1中2所示)以及振動板(圖1中3所示)。由于產品性能要求,在制備振膜時,需要用熱熔膠將上述三個部分(即薄膜、支架、振動板)接合并且具有較好的粘接強度,而熱熔膠需要冷卻到一定溫度才能固化,因此模具所在的加熱平臺在高溫之后還需要恢復到初始溫度以便熱熔膠固化。上述技術方案更具體為(請參照圖2所示):將模具置于加熱平臺(工作臺)后,壓合模具,加熱平臺開始從冷卻脫模點(35℃)升溫并加入成型氣壓(即常規(guī)成型氣壓為0.6Mpa),加熱平臺持續(xù)升溫到達高溫設定點(即170℃)后,平臺停止加熱,此時平臺保持高溫并且PLC計時器開始計時,經(jīng)過一段保持時間(12-15s,即圖2中的“保溫時間”),然后加熱平臺通水冷卻到低溫設定點(該過程約需30S,低溫設定點為35℃),取出模具。一般情況下,上述技術方案是在一個密閉的環(huán)境中實施的,將氣壓作用于加溫軟化中的薄膜,使其在模具中成型的過程,即所謂的振膜成型工藝。但是上述振膜成型工藝具有如下缺陷:1.生產周期長(降溫時間約占整個過程周期的1/3),生產效率低;2.通水冷卻容易產生冷凝水,會造成設備安全隱患以及產品的質量隱患;3.“振動板→薄膜→支架”的上料順序產生的累計誤差大,氣泡多,導致良率低。技術實現(xiàn)要素:針對上述現(xiàn)有技術的缺陷,本發(fā)明的目的是提供一種振膜成型方法。本發(fā)明的上述目的是通過以下技術方案實現(xiàn)的:本發(fā)明提供一種振膜成型方法,包括:對工作平臺加熱并使其保持恒溫的步驟,將已上料至模具的振動板、支架、薄膜移入所述保持恒溫的工作平臺進行振膜成型的步驟,將帶有所述成型獲得振膜的模具移出所述保持恒溫的工作平臺進行冷卻的步驟。優(yōu)選地,所述保持恒溫的溫度范圍為:165-175℃。優(yōu)選地,所述保持恒溫的時間范圍為:振膜生產流程的自始至終。優(yōu)選地,所述上料的順序為:先振動板,再支架,最后為薄膜。優(yōu)選地,所述成型包括先采用低于常規(guī)成型氣壓的氣壓進行預成型的階段及再采用常規(guī)成型氣壓進行成型的階段;其中,常規(guī)氣壓為0.6Mpa。優(yōu)選地,所述預成型的氣壓為0.1-0.15Mpa。優(yōu)選地,所述預成型的時間為5-7秒。優(yōu)選地,所述成型的階段的時間為25-33秒。優(yōu)選地,所述冷卻具體是將模具溫度降至上料時涂于支架上的熱熔膠的固化溫度。優(yōu)選地,所述冷卻具體是將溫度降至35℃。與現(xiàn)有技術相比,本發(fā)明具備如下有益效果:本發(fā)明的成型方法自始溫度保持一致,與現(xiàn)有技術的先升溫、保溫、降溫的成型技術相比提高了振膜的成型率,避免了上料模具隨工作平臺同步加熱的步驟,上料后的模具直接進入溫度設定好的工作平臺,提高成型效率,縮短了成型周期;省略了單批次成型均需對工作平臺進行水冷降溫的步驟,避免了冷凝水造成的安全以及質量隱患、提高了冷卻效率。附圖說明一個或多個實施例通過與之對應的附圖中的圖片進行示例性說明,這些示例性說明并不構成對實施例的限定,附圖中具有相同參考數(shù)字標號的元件表示為類似的元件,除非有特別申明,附圖中的圖不構成比例限制。圖1為動鐵受話器的振膜組成示意圖;圖2為現(xiàn)有振膜成型相關參數(shù)特征圖。具體實施方式下面結合具體實施例對本發(fā)明進行詳細說明。以下實施例將有助于本領域的技術人員進一步理解本發(fā)明,但不以任何形式限制本發(fā)明。應當指出的是,對本領域的普通技術人員來說,在不脫離本發(fā)明構思的前提下,還可以做出若干變形和改進。這些都屬于本發(fā)明的保護范圍。實施例1-3實施例1-3分別提供了一種振膜成型方法,包括如下步驟:步驟1,對工作平臺加熱并使其保持恒溫的步驟;步驟2,將已上料至模具的振動板、支架、薄膜移入所述保持恒溫的工作平臺進行振膜成型的步驟;步驟3,將帶有所述成型獲得振膜的模具移出所述保持恒溫的工作平臺進行冷卻的步驟。針對上述步驟1,具體說明如下:將工作平臺預熱至設定溫度并保持恒溫不變,保持恒溫具體為生產開始后自始至終平臺都是同一溫度,直至關機。這樣就省去了對工作平臺的冷卻時間,縮短成型周期。針對上述步驟2,具體說明如下:(1)將現(xiàn)有技術的“振動板→薄膜→支架”的上料順序改為“振動板→支架→薄膜”,即改變支架的定位方式。使材料定位累計誤差減少,由于振膜成品本身的尺寸精度要求較高(約+/-0.0005),改善之前的良品率約85%,更改上料方式使得累計誤差減少,良率至少提高了5%。需要說明的是,根據(jù)本領域的常規(guī)操作,在上料時,支架上涂覆有熱熔膠。(2)在現(xiàn)有成型技術中加入預成型階段,即在上料完成后先通入0.1-0.15Mpa強度的氣壓持續(xù)5-7秒進行預成型,當薄膜遇熱軟化后,由于此時的模具正處于熱傳遞階段,表面熱量還不均勻,因此薄膜附著于模具表面后,在不同區(qū)域(尤其是中間區(qū)域)的薄膜與模具之間會產生氣泡,此時如果直接通入高氣壓會將導致薄膜瞬間緊貼模具,導致內部空氣無法向外排出,最終將會造成成品出現(xiàn)氣泡,不成形等現(xiàn)象。因此,預成型氣壓的加入,使薄膜在軟化的同時從中間區(qū)域慢慢向外側延伸,是薄膜與模具表面實現(xiàn)無空氣接觸。針對上述步驟3,具體說明如下:成型后取出模具,冷卻,即可。該步驟與現(xiàn)有技術的先工作臺冷卻再取出模具的操作是不同的,這樣省略了對工作平臺進行水冷降溫的步驟,避免了冷凝水造成的安全以及質量隱患;取出模具后再對模具冷卻,這樣的操作對振膜生產不會造成影響。通過上述成型方法,可在恒溫工作平臺上同時操作多套上料模具,實現(xiàn)振膜的高效、持續(xù)、批量生產。上述實施例1-3的振膜成型步驟相同,不同之處僅在于如下表1所示的參數(shù):表1需要說明的是,將步驟2中的成型的時間控制在25-33秒范圍內均可實現(xiàn)本發(fā)明的效果。對比例1-4在本發(fā)明的實施中,發(fā)明人還為實施例2設置了對比例,具體為:對比例1:為采用圖2所示的現(xiàn)有技術,即將已上料(“振動板→薄膜→支架”)至模具的振動板、支架(涂有熱熔膠)、薄膜移入工作平臺,加熱平臺開始從冷卻脫模點(35℃)升溫,升溫至80℃加入成型氣壓(即常規(guī)成型氣壓為0.6Mpa),加熱工作平臺持續(xù)升溫到達高溫設定點(即170℃)后,工作平臺停止加熱,此時工作平臺保持高溫并且PLC計時器開始計時,經(jīng)過一段保持時間(12-15s,即圖2中的“保溫時間”),然后加熱平臺通水冷卻到低溫設定點(冷卻過程約需30S,低溫設定點為35℃),取出模具,整個過程耗時60-70秒。對比例2:與實施2的區(qū)別僅在于步驟2中上料順序采用“振動板→薄膜→支架”。對比例3:與實施2的區(qū)別僅在于步驟2中不存在預成型,成型為恒壓成型,成型氣壓為0.6Mpa。對比例4:與實施例2的區(qū)別在于預成型的條件為0.05Mpa。性能測試為了體現(xiàn)本發(fā)明上述實施例的優(yōu)勢效果、突出創(chuàng)造性,發(fā)明人對采用實施例2、對比例1、對比例2、對比例3、對比例4所示方法成型的振膜進行隨機抽檢,每例抽檢100件,抽檢次數(shù)大于等于3次作為重復,對抽檢振膜的成型率、良品率、成型時間進行了統(tǒng)計,具體如下:成型率及其檢測方法:通過顯微鏡下目檢,判斷薄膜成型是否充分,成型充分的振膜數(shù)量在振膜總量中的比例記作成型率;良品率及其檢測方法:通過工具顯微鏡測量以及目檢,不存在缺陷的振膜數(shù)量在振膜總量中的比例記作良品率;成型過程耗時檢測方法:采用普通計時裝置,現(xiàn)有技術耗時60-70秒,改善后的本發(fā)明耗時30-40秒。檢測結果見表2。表2實施例2對比例1對比例2對比例3對比例4成型率98-100%40-50%88-90%88-90%90-92%良品率90-92%80-85%78-85%80-85%89-91%成型耗時30-40秒60-70秒36-40秒36-40秒36-40秒根據(jù)表2所示的結果,分析如下:對比例1與實施例2的區(qū)別在于,對比文件1所示的技術方案是實施例2針對的現(xiàn)有技術,即對比例1為改進前的技術方案,實施例2為改進后的技術方案,根據(jù)表2可知,改進后的實施例2在成型率、良品率、成型時間上均有顯著優(yōu)于現(xiàn)有成型技術對比例1,特別是成型率,保持高溫不變的成型率比對比例1先升溫再保溫最后冷卻的技術方案提高了2-3倍;且實施例2取消了對工作平臺采用通水冷卻的過程,避免了冷凝水造成的安全以及質量隱患,模具取出后再冷卻對生產也不會造成影響;加入預成型氣壓的設計,良品率從原來的80%提高到92%;實施例2的整體改進縮短了成型流程耗時,降低了生產成本。實施例2相對于對比例1的改進點是目前所沒有公開的,產生的優(yōu)勢效果也是本領域技術人員難以預料的,特別是在成型率、良品率、成型耗時方面的改進程度,也是目前其他振膜成型技術所難以達到的,相對于現(xiàn)有技術效果屬質的飛躍。對比例2與實施例2的區(qū)別僅在于其上料的順序為“振動板→薄膜→支架”,即采用了現(xiàn)有技術常用的上料順序。通過表2的測試結果可知,對比例2的效果優(yōu)于對比例1且劣于實施例2,由此可知,上料的順序對振膜的成型率、良品率存在影響,如果不對上料順序進行改進,那么即便采用更長的成型時間也無法實現(xiàn)實施例2給出的優(yōu)勢效果??梢?,上料的順序對本發(fā)明的實現(xiàn)效果做出了重要貢獻,盡管上料屬于本領域技術人員熟知的技術,但是對其進行順序調換的操作打破了本領域技術人員的常規(guī)認識,順序調換的上料手段所產生的效果也是現(xiàn)有技術沒有公開的,更是本領域技術人員不能預測的,該技術手段的改進具備突出的實質性特點和顯著的進步。對比例3與實施例2的區(qū)別僅在于步驟2中不存在預成型,成型為恒壓成型,成型氣壓為0.6Mpa。通過表2的測試結果可知,對比例3的效果優(yōu)于對比例1且劣于實施例2,由此可知,預成型對振膜的成型率、良品率存在影響,如果不對增加預成型這一技術特征,那么即便采用更長的成型時間也無法實現(xiàn)實施例2給出的優(yōu)勢效果??梢?,預成型對本發(fā)明的實現(xiàn)效果做出了重要貢獻,起到了協(xié)同作用,盡管成型屬于本領域技術人員熟知的技術,但是對其進行氣壓調整的操作打破了本領域技術人員的常規(guī)認識,預成型所產生的效果也是現(xiàn)有技術沒有公開的,更是本領域技術人員不能預測的,該技術手段的改進具備突出的實質性特點和顯著的進步。對比例4與實施例2的區(qū)別在于預成型的條件為0.05Mpa,即超出了本發(fā)明限定的預成型氣壓范圍?;谏隙侮P于對比例3與實施例2比較分析可知,預成型技術手段的設定使得本發(fā)明具有創(chuàng)造性。進一步地,對比例4和實施例2對預成型條件設置范圍的重要性進行佐證。通過表2可知,對比例4的效果稍差于對比例3和實施例2,同時顯著優(yōu)于對比例1和對比例2。這說明,即便對比例4參照本發(fā)明的改進點進行改進,但是如果改進點對應的參數(shù)超范圍,那么也無法實現(xiàn)與本發(fā)明實施例相當?shù)男Ч?,突出反映了參?shù)范圍即預成型氣壓限定對振膜性能的關鍵作用。盡管成型氣壓極可能成為本領域技術人員對成型工藝的改進點,或者已經(jīng)成為改進點,但是將氣壓限制為0.1-0.15Mpa且對振膜的成型率、良品率起到積極協(xié)同作用是本領域技術人員所沒有公開的,也不可能從現(xiàn)有技術中得到技術啟示,即本發(fā)明對預成型氣壓的限制屬于發(fā)明人創(chuàng)造性選擇的結果,因此該技術點的改進具備創(chuàng)造性。需要說明的是,本發(fā)明的說明書中給出了本發(fā)明的較佳的實施例,但是,本發(fā)明可以通過許多不同的形式來實現(xiàn),并不限于本說明書所描述的實施例,這些實施例不作為對本
發(fā)明內容的額外限制,提供這些實施例的目的是使對本發(fā)明的公開內容的理解更加透徹全面。并且,上述各技術特征繼續(xù)相互組合,形成未在上面列舉的各種實施例,均視為本發(fā)明說明書記載的范圍;進一步地,對本領域普通技術人員來說,可以根據(jù)上述說明加以改進或變換,而所有這些改進和變換都應屬于本發(fā)明所附權利要求的保護范圍。當前第1頁1 2 3