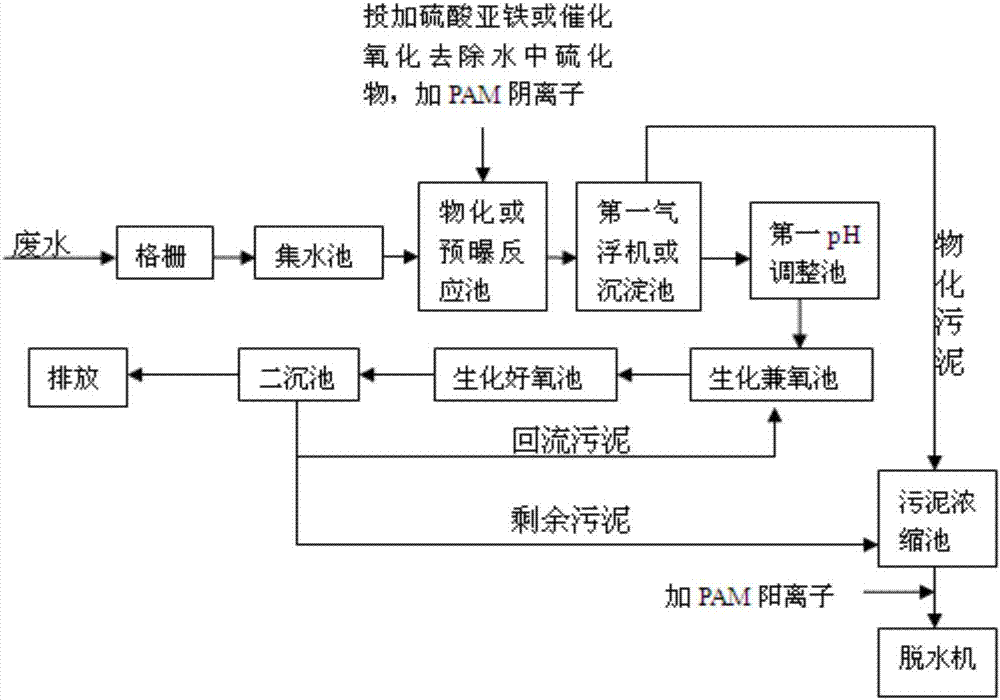
本發(fā)明屬于污水治理領域,具體涉及一種皮革廢水處理系統(tǒng)及方法。
背景技術:
:目前,皮革制造行業(yè)中的生產(chǎn)過程中產(chǎn)生廢水,該廢水通常含有大量的硫化物、鉻、鹽類、表面活性劑、染料、生物廢料等多種污染物質(zhì)和有毒物質(zhì)等,是一種典型的含鹽量高,含氨氮量高的工業(yè)廢水,具有濃度高,水量少的特點。國內(nèi)外的皮革廢水處理基本是結(jié)合物化和生化結(jié)合的工藝流程?,F(xiàn)有皮革廢水的物化處理工藝基本是通過投加亞鐵對水中s2-進行沉淀或投加硫酸錳對s2-進行催化氧化,再投加pam陰離子進行絮凝沉淀,污泥沉于泥斗,經(jīng)排泥管道排入污泥濃縮池。其中,pam全名為聚丙烯酰胺,包括pam陽離子和pam陰離子,有該產(chǎn)品的分子能與分散于溶液中的懸浮粒子架橋吸附,有著極強的絮凝作用。皮革廢水的生化處理工藝是靠生化兼氧池和生化好氧池。物化沉淀后的出水經(jīng)調(diào)整ph到7-8后進入生化兼氧池,利用兼性微生物將難生物降解的大分子有機物水解成易降解小分子有機物,再通過好氧微生物對水中易降解的有機物、nh3—n等污染物進行分解。微生物自身得到生長繁殖,最后進入二沉池進行泥水分離,上清液排放。96%的活性污泥回流至生化系統(tǒng),4%的剩余污泥排入污泥濃縮池。濃縮池污泥進行脫水后外運?,F(xiàn)有工藝存在的問題:(1)水中s2-需要投加大量藥劑進行沉淀或氧化,產(chǎn)生大量污泥,為污泥的脫水和處置帶來很大負擔;(2)廢水原本含鹽量高,物化投加大量藥劑,進一步增加廢水含鹽量,過高的含鹽量對生化曝氣系統(tǒng)腐蝕嚴重;(3)物化段為了去除s2-加入了大量的so42-,兼氧段如水中溶解氧(do)控制不好,so42-容易被厭氧還原,產(chǎn)生h2s惡臭氣體,h2s對好氧微生物造成毀滅性打擊;(4)由于皮革廢水氨氮含量較高(200-300mg/l),生化處理很難達標,出水氨氮超標嚴重;(5)廢水中還有較多染料,再加上物化階段投加了大量鐵鹽等,導致出水色度超標(色度>30倍)。技術實現(xiàn)要素:本發(fā)明的目的在于針對現(xiàn)有技術的不足,使排放的廢水的氨氮含量、色度、硫化物含量達標,同時減少污水處理過程中污泥的排放量,延長廢水物化生化處理系統(tǒng)使用壽命。本發(fā)明利用皮革廢水含鹽量和氯化物含量高,導電性好,用電解裝置對二沉池的生化出水進行電解。本發(fā)明的目的通過以下技術方案實現(xiàn):一種皮革廢水處理系統(tǒng),包括一級廢水處理系統(tǒng),所述一級廢水處理系統(tǒng),包括格柵、集水池、預曝反應池、第一固液分離裝置、第一ph調(diào)整池、生化兼氧池、生化好氧池、二沉池依次管路連接;還包括二級廢水處理系統(tǒng),所述二級廢水處理系統(tǒng),包括電解裝置、第二ph調(diào)整池、第二固液分離裝置依次管路連接;所述電解裝置的陽極設有氯氣收集器,該收集器與集水池管路連通;陰極設有氫氣收集器,該收集器與第二固液分離裝置管路連通。所述的第一固液分離裝置是第一氣浮機或沉降池;所述的第二固液分離裝置是第二氣浮機。所述的電解裝置的正負電極均為鈦金屬電極。所述的氯氣收集器通過射流曝氣裝置與集水池連通。所述電解裝置用低壓直流電,所用電壓10-15v,電流密度為2-7a/dm2,電解時間為20-40min。優(yōu)選的,所述電解裝置用低壓直流電,所用電壓12v,電流密度為3a/dm2,電解時間為30min。所述的第一固液分離裝置和第二固液分離裝置的污泥出口與污泥濃縮池管路連通,所述的污泥濃縮池與脫水機管路相連;所述二沉池分別與生化兼氧池和污泥濃縮池管路連通。利用上述系統(tǒng)處理廢水的方法,包括一級廢水處理和二級廢水處理,所述一級廢水處理包括如下步驟:(1)廢水進行絮凝沉降反應處理,反應用的處理劑是pam陰離子絮凝劑;經(jīng)固液分離后,調(diào)節(jié)ph為7.5-8.5;進行微生物降解處理后沉淀;所述二級廢水處理包括如下步驟:(2)一級廢水處理后的水,進行電解反應處理,電解產(chǎn)生的氯氣通入集水池,電解產(chǎn)生的氫氣通入第二氣浮機,調(diào)節(jié)電解出水的ph為7.5-8.5;最后將出水進行氣浮處理,氣浮反應所用處理劑是pam陰離子絮凝劑;步驟(1)中所述的微生物降解處理后沉淀的污泥中96%w/w回流到生化兼氧池,4%w/w排入污泥濃縮池。步驟(1)中所述的固液分離反應和沉淀和步驟(2)中所述的氣浮反應排出的污泥均進入污泥濃縮池,向濃縮污泥加入pam陽離子絮凝劑,再脫水處理。與現(xiàn)有技術相比,本發(fā)明具有以下優(yōu)點和有益效果:1、電解裝置產(chǎn)生的cl2和集水池中的廢水進行充分接觸和反應,直接將水中s2-氧化成s,水中懸浮物減少50%-60%,從而減少污泥的產(chǎn)生,污泥脫水用的pam陽離子大幅減少60%,降低污泥處置費用;減少除硫藥劑對生化曝氣系統(tǒng)的中好氧微生物的侵害。2、電解裝置產(chǎn)生的氫氣通入氣浮機,利用氫氣的浮力,更好的去除因電解分解有機物而產(chǎn)生的沉淀污泥,促進氣浮機下部的水達標排放,同時使電解效率最大化。3、二沉池中未被生物降解的cod、nh3—n以及有色污染物在電極表面直接被氧化分解,或被電解生成的強氧化物間接氧化得以去除,進而保證出水的氨氮量、出水色度排放達標。4、電解電極采用鈦金屬電極,在電解過程中不會被氧化消耗,這樣的電解效果穩(wěn)定,電流分布均勻,電解效率高。5、電解只產(chǎn)生極少量的有機物分解后的沉淀污泥。6、利用電解裝置處理皮革廢水方法對場地要求不高、成本低、操作簡單。附圖說明圖1原皮革廢水的處理工藝示意圖。圖2本發(fā)明皮革廢水的處理工藝示意圖。具體實施方式下面結(jié)合實施例及附圖對本發(fā)明做進一步詳細的描述。實施例1:廢水先經(jīng)過格柵,由細格柵攔截去除較大垃圾(皮碎、肉碎、毛),減少提升泵的磨損和堵塞。再進入收集池,電解生產(chǎn)的cl2在集水池和原水進行充分混合反應。將水中s2-氧化。由提升泵提升至預曝反應池,進一步氧化水中s2-,再投加pam進行絮凝沉淀,污泥沉于泥斗,經(jīng)排泥管道排入污泥濃縮池。沉淀出水經(jīng)ph調(diào)整到7.5-8.5后進入生化兼氧池,利用兼性微生物將難降解的大分子有機物水解成易生物降解的小分子有機物,再通過好氧微生物對水中易降解的有機物、nh3—n等污染物進行分解。微生物自身得到生長繁殖,最后進入二沉池進行泥水分離,96%活性污泥回流至生化系統(tǒng),4%剩余污泥排入污泥濃縮池。上清液進入電解裝置,利用皮革廢水含鹽量高、氯化物含量高的特點,對生化出水進行電解。未處理的皮革廢水的含鹽量以固含量法測得為20000mg/l。在電場的作用下,水中cl-、oh-向陽極移動,在陽極失去電子,被氧化成cl2、·oh、o2、h2o2、·o等強氧化性物質(zhì),水中未被生物降解的cod、nh3—n以及發(fā)色污染物10%在電極表面直接被氧化分解,90%被電解生成的強氧化性物質(zhì)間接氧化得以去除。水中h+向陰極移動,在陰極得到電子,被還原成h2。水中cl-向陽極移動,在陽極失去電子,被氧化成cl2。由于氯氣易溶于水,電解過程中產(chǎn)生的cl2中80%重新溶于水,20%未溶解于水的cl2和陽極電解生成的o2利用射流裝置進入集水池,和原水進行充分接觸和反應,將原水中的s2-進行氧化。減少除硫藥劑的投加,從而減少污泥的產(chǎn)生,降低污泥處置費用。電解出水經(jīng)ph調(diào)整至7.5—8.5后進入氣浮機,電解生成的h2通過增壓泵進入溶氣罐,和水中懸浮物質(zhì)充分結(jié)合,利用氫氣的浮力更好的去除因電解分解有機物而產(chǎn)生的污泥,氣浮機下部的水達標排放。上面的污泥經(jīng)刮泥機排入污泥濃縮池。濃縮池污泥進行脫水后外運。表1比較沒有電解裝置的原工藝和本發(fā)明的污泥產(chǎn)生量。表1原工藝和本發(fā)明污泥產(chǎn)生量比較按處理1噸污泥花費280元計算,本發(fā)明節(jié)省1747.2元。本發(fā)明采用低壓直流電解裝置,所用電壓12v,電流密度為3a/dm2,電解時間為30min。電極間距10~15mm,電解陰、陽電極均采用鈦金屬電極,電解產(chǎn)生cl2、o2和h2分別利用負壓管道收集,cl2、o2充入原水中,h2充入電解后經(jīng)調(diào)整ph的氣浮進水中。通過調(diào)節(jié)電流密度和電解時間可控制電解速度和出水水質(zhì)。表2原工藝和本發(fā)明出水水質(zhì)比較見表2,通過在出水段加入電解工藝后,出水水質(zhì)有了根本的好轉(zhuǎn),各項指標優(yōu)于國家排放標準。通過將電解產(chǎn)生的氧化性氣體充入原水,使得原水硫化物含量大幅減低,變化情況如表3所示:表3原工藝和本發(fā)明中硫化物含量比較原水硫化物含量mg/l充入電解陽極氣體后硫化物含量mg/l2051.81890.41990.9原工藝由于投加了大量的硫酸亞鐵,根據(jù)反應方程式:feso4+s2-→fes↓+so42-亞鐵離子和水中硫離子反應后生產(chǎn)大量硫化亞鐵沉淀,需要大量pam陰離子進行絮凝沉淀。因為pam陰離子的用量和水中懸浮物成正比,水中所含懸浮物越多,進行絮凝沉淀時所用pam陰離子越多。本發(fā)明通過將氯氣充入原水,直接將水中s2-氧化成s,水中懸浮物減少50%-60%,所以物化段pam陰離子同比減少50%-60%,由于本發(fā)明在電解后端增加了氣浮處理,為了提高氣浮處理效果,廢水在進入氣浮機之前需要投加pam陰離子進行絮凝,所以pam陰離子的用量沒有變化。pam陽離子用于污泥脫水,pam陽離子的用量和污泥產(chǎn)生量成正比,原工藝采用硫酸亞鐵進行脫硫,產(chǎn)生大量硫化亞鐵沉淀,由于硫化亞鐵沉淀的顆粒比較細,很容易堵塞濾布,所以必須投加大量pam陽離子改善污泥脫水性能,本發(fā)明通過充入電解產(chǎn)生的氧化性氣體進行脫硫,泥量較少38%,由于污泥中不存在顆粒細小的硫化亞鐵沉淀,污泥脫水性能提高30%,因此污泥脫水用pam陽離子大幅減少60%。表4比較了原工藝和本發(fā)明的加藥量。表4原工藝和本發(fā)明的加藥量比較本發(fā)明采用充入電解氧化性氣體的方式進行脫硫、沉淀,節(jié)省了大量藥劑費用,降低了操作人員的勞動強度,不增加生化進水的鹽度,提高了生化系統(tǒng)的穩(wěn)定性和對污染物的去除率。上述實施例為本發(fā)明較佳的實施方式,但本發(fā)明的實施方式并不受上述實施例的限制,其他的任何未背離本發(fā)明的精神實質(zhì)與原理下所作的改變、修飾、替代、組合、簡化,均應為等效的置換方式,都包含在本發(fā)明的保護范圍之內(nèi)。當前第1頁12