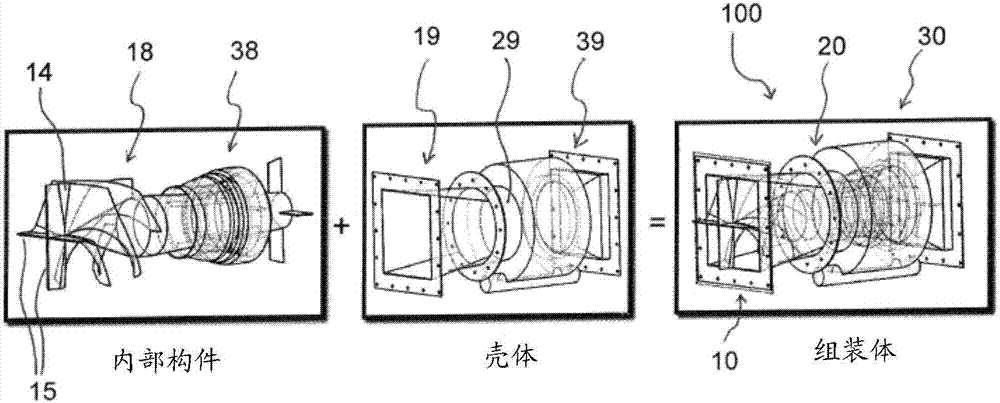
本發(fā)明涉及一種用于從大氣層空氣中去除大氣顆粒物質(zhì)的顆粒物去除器。
背景技術(shù):
:霧霾定義為通常由大氣水分,灰塵,煙霧和水蒸氣等能降低可見度的細(xì)小懸浮顆粒引起的輕微低層大氣遮蔽。空氣攜帶的顆粒(氣溶膠)及微粒的組成通常取決于其來源,而且甚至可包括由風(fēng)從陸地刮起的礦物質(zhì)氧化物(灰塵),以及從海鹽中刮起的氯化鈉、鎂、硫酸鹽、鈣、鉀等礦物質(zhì)氧化物。森林火災(zāi)將硫和氮的氧化物等原生氣體氧化成硫酸(液態(tài))和硝酸(氣態(tài)),這些硫酸和硝酸通常以銨鹽的形式(硫酸銨和硝酸銨)存在。森林燃燒還將有機(jī)物質(zhì)(源自生物或人)以及元素碳(炭黑)引入空氣中。霧霾還可歸因于嚴(yán)重的城市污染和工業(yè)污染。燃?xì)鉁u輪機(jī)在運(yùn)行期間攝取大量的環(huán)境空氣。因此,進(jìn)入燃?xì)鉁u輪機(jī)的空氣質(zhì)量對(duì)該渦輪機(jī)的性能和壽命具有顯著影響。在空氣中因上述原因存在大量顆粒物的重度污染環(huán)境中,迫切需要開發(fā)一種實(shí)用的解決方案,以在被污染環(huán)境中使用的動(dòng)力燃?xì)鉁u輪機(jī)的當(dāng)?shù)丨h(huán)境空氣進(jìn)入其配有工業(yè)級(jí)空氣過濾器的進(jìn)氣室之前,對(duì)該空氣進(jìn)行凈化。發(fā)電廠燃?xì)鉁u輪機(jī)依靠其空氣過濾器部件阻止顆粒物進(jìn)入其燃燒路徑。一旦這些過濾器部件根據(jù)運(yùn)行過程中流經(jīng)其內(nèi)部的空氣壓降測(cè)定的阻塞程度超出某些可接受水平時(shí),則須對(duì)其進(jìn)行周期性更換(例如每12個(gè)月)。這些工業(yè)過濾器無法篩除pm1(或更小)顆粒,而且此類顆粒與pm10顆粒不同的是其可能對(duì)旋轉(zhuǎn)部件不造成任何明顯影響。這便是當(dāng)前技術(shù)的現(xiàn)狀,其目的在于在清潔環(huán)境空氣條件中運(yùn)行動(dòng)力燃?xì)鉁u輪機(jī)。目前,燃?xì)獍l(fā)電廠通常通過一系列綜合過濾器進(jìn)行顆粒物去除。對(duì)于較小的發(fā)電廠,采用壓縮空氣凈化系統(tǒng)對(duì)過濾器進(jìn)行周期性除塵。然而,該凈化系統(tǒng)僅延長(zhǎng)過濾器部件的使用壽命,并不能防止灰塵觸及過濾器。雖然已有通過電暈放電場(chǎng)使灰塵顆粒帶電的嘗試做法,但這些做法不太經(jīng)濟(jì),一方面原因在于運(yùn)行期間的巨大電力消耗,另一方面原因在于大規(guī)模應(yīng)用時(shí)所需的資金成本。因此,需要提供一種無需使用過濾器便可將大氣層空氣中的霧霾和灰塵顆粒,尤其在該空氣被動(dòng)力燃?xì)鉁u輪機(jī)等現(xiàn)代大型空氣呼吸系統(tǒng)消耗之前去除的高性價(jià)比顆粒物去除器。技術(shù)實(shí)現(xiàn)要素:本發(fā)明顆粒物去除器利用動(dòng)量原理從空氣流中分離微粒(尤其是pm5及以上尺寸)。通過增強(qiáng)空氣流的切向和徑向速度分量并因此賦予空氣流中顆粒相應(yīng)的動(dòng)量,可輔助所述顆粒徑向向外遷移并集中于所述氣流的外側(cè)圈層中,以供下游收集。為了促進(jìn)顆粒的遷移和凝結(jié),在本發(fā)明入口處將蒸汽注入空氣流內(nèi),從而使得:(一)顆粒表面發(fā)生的水氣冷凝增加了顆粒的質(zhì)量和尺寸;(二)冷凝水將包有所述顆粒的污染物洗去;(三)冷凝水總體促進(jìn)顆粒的凝結(jié),尤其促進(jìn)較小顆粒(<pm2.5)的凝結(jié);(四)所述蒸汽冷凝過程因相(和容積)變化而產(chǎn)生負(fù)壓,從而部分恢復(fù)本發(fā)明導(dǎo)致的壓降;(五)分離后的微粒易于收集和去除,并且無空氣流泄出。所述顆粒物去除器可在現(xiàn)有過濾器部件之前裝配至渦輪機(jī)燃燒空氣過濾器室,以使得灰塵顆粒在到達(dá)該空氣過濾器室之前即被分離和收集。所述顆粒物去除器還可裝配至商業(yè)建筑內(nèi)的大型空調(diào)系統(tǒng)等任何呼吸大氣層空氣的大型設(shè)備。所述顆粒物去除器利用進(jìn)入系統(tǒng)空氣過濾器的流動(dòng)空氣(以及所攜帶的灰塵)的動(dòng)能實(shí)現(xiàn)顆粒分離。該顆粒物去除器所消耗的能量?jī)H為該顆粒物去除器內(nèi)的氣壓降以及少量低等級(jí)飽和蒸汽(任何現(xiàn)代發(fā)電廠均有大量此類蒸汽可供使用)。與其他現(xiàn)有技術(shù)相比,所述顆粒物去除器可替代整個(gè)系統(tǒng)的至少部分(乃至全部)傳統(tǒng)織物或纖維過濾器。所述顆粒物去除器無任何需要維護(hù)的移動(dòng)部件,可由常用低碳鋼材料制造,而且內(nèi)部涂覆不粘材料。所述顆粒物去除器為模塊化設(shè)計(jì),以供通過復(fù)制進(jìn)行放大。所述顆粒物去除器排出的流出物(冷凝水)質(zhì)量:(一)與被過濾的空氣相比相對(duì)較小(占所述空氣的質(zhì)量百分比為2%~3%);(二)易于處理,(三)所述冷凝水可通過廉價(jià)的沉降和ph校正方法回收再利用。根據(jù)第一方面,提供一種從大氣層空氣中去除顆粒物質(zhì)的顆粒物去除器,該顆粒物去除器包括:軸向旋流器,該軸向旋流器包括設(shè)于其內(nèi)的數(shù)個(gè)螺葉,所述螺葉在以與所述顆粒物去除器的縱軸同軸的方式攝入所述軸向旋流器內(nèi)的空氣中產(chǎn)生軸向、切向和徑向速度分量,其中,所述軸向旋流器的入口處的橫截氣流面積大于該軸向旋流器的出口處的橫截氣流面積;與所述軸向旋流器流體連接的分流區(qū),該分流區(qū)包括環(huán)形通道,該環(huán)形通道為離開所述軸向旋流器的空氣形成恒速流動(dòng)部分;以及與所述分流區(qū)流體連接的顆粒收集區(qū),該顆粒收集區(qū)包括:外殼,該外殼包括殼鼓,該殼鼓的外徑大于所述分流區(qū)的環(huán)形通道的外徑;以及內(nèi)部組裝體,該內(nèi)部組裝體在所述殼鼓內(nèi)限定出擴(kuò)散部件,該擴(kuò)散部件用于所述顆粒物去除器內(nèi)的壓力恢復(fù),以及限定出一個(gè)或多個(gè)與所述擴(kuò)散部件流體連接的空氣泄放通道,以將清潔空氣引出所述顆粒物去除器之外。所述顆粒物去除器可還包括至少一個(gè)蒸汽注入口,該蒸汽注入口設(shè)于所述軸向旋流器的入口處,以將蒸汽注入所述顆粒物去除器內(nèi)。所述至少一個(gè)蒸汽注入口可設(shè)于進(jìn)氣管道處,該進(jìn)氣管道設(shè)于所述軸向旋流器入口的上游。所述內(nèi)部組裝體可包括:內(nèi)錐體,該內(nèi)錐體的直徑朝該內(nèi)錐體下游端方向減?。灰约爸辽賰蓚€(gè)環(huán)形圈,該環(huán)形圈彼此間隔分離并與所述內(nèi)錐體間隔分離,所述至少兩個(gè)環(huán)形圈沿所述內(nèi)錐體同心設(shè)置,其中,所述至少兩個(gè)環(huán)形圈中的各相鄰對(duì)之間的空間限定出所述空氣泄放通道。所述至少兩個(gè)環(huán)形圈可由設(shè)于所述內(nèi)錐體上的第一組肋件彼此間隔分離并與所述內(nèi)錐體間隔分離。所述第一組肋件中的每個(gè)肋件可均相對(duì)于垂直平面朝向預(yù)定的角度,以用作所述顆粒收集區(qū)內(nèi)的渦流破壞部件。所述內(nèi)部組裝體可還包括第二組肋件,該第二組肋件設(shè)于所述內(nèi)錐體的下游端,以將所述內(nèi)部組裝體接合于所述外殼。附圖說明為使本發(fā)明可被完全理解并易于付諸實(shí)踐,以下僅通過非限制性舉例的方式對(duì)本發(fā)明例示實(shí)施方式進(jìn)行描述,該描述參考以下說明性附圖。圖1a為本發(fā)明顆粒物去除器的示意圖。圖1b為例示顆粒物去除器的內(nèi)部構(gòu)件和殼體分解組裝圖以及該例示顆粒物去除器的組裝圖。圖2a為所述例示顆粒物去除器的軸向旋流器內(nèi)部結(jié)構(gòu)的入口端視圖。圖2b為圖2a內(nèi)部結(jié)構(gòu)側(cè)視圖。圖2c為圖2a和圖2b內(nèi)部結(jié)構(gòu)的出口視圖。圖2d為所述例示顆粒物去除器的軸向旋流器殼體的入口視圖。圖2e為圖2d殼體側(cè)視圖。圖2f為圖2d和圖2e殼體出口的端視圖。圖3a為所述例示顆粒物去除器氣流線路(僅示出四分之一)的計(jì)算流體動(dòng)力學(xué)(cfd)模擬視圖。圖3b為所述例示顆粒物去除器分流區(qū)的三個(gè)環(huán)形氣流區(qū)域的分離效率圖,該圖顯示了距所述例示顆粒物去除器入口280mm處的所述環(huán)形氣流區(qū)域的最佳橫截面上的pm10顆粒分布。圖3c為所述三個(gè)環(huán)形氣流區(qū)域距所述入口的不同距離處該三個(gè)環(huán)形氣流區(qū)域內(nèi)的pm10顆粒的遷移圖。圖4a為所述例示顆粒物去除器的分流區(qū)的入口視圖。圖4b為圖4a分流區(qū)的橫截面圖。圖5a為所述例示顆粒物去除器的顆粒收集區(qū)的外殼側(cè)視圖。圖5b為所述例示顆粒物去除器的顆粒收集區(qū)的內(nèi)部組裝體后視圖。圖5c為圖5a外殼的分解組裝圖。圖5d為圖5b內(nèi)部的組裝體分解組裝圖。圖6為所述例示顆粒物去除器的顆粒收集區(qū)的橫截面?zhèn)纫晥D。圖7為所述例示顆粒物去除器的顆粒收集區(qū)的立體及端視示意圖。圖8為所述例示顆粒物去除器原型的照片側(cè)視圖。圖9為設(shè)有蒸汽注入口的所述例示顆粒物去除器的示意圖。具體實(shí)施方式以下,結(jié)合圖1至圖9,對(duì)顆粒物去除器100的例示實(shí)施方式進(jìn)行描述。顆粒物去除器100的部件設(shè)置方式和流路圖示于圖1a和圖1b。顆粒物去除器100包括三個(gè)區(qū),這些區(qū)包括:(一)軸向旋流器10;(二)由與軸向旋流器10流體連接的分流器定義的分流區(qū)20;以及(三)由與分流器流體連接的集粒器定義的顆粒(帶冷凝水)收集區(qū)30。如圖1a和圖1b所示,軸向旋流器10,分流區(qū)20中的分流器和收集區(qū)30中的集粒器優(yōu)選沿顆粒物去除器100的縱向中心軸線lc同軸設(shè)置。如圖1a所示,含塵空氣(下文以空氣流90表示)可由燃?xì)鉁u輪機(jī)(未圖示)等空氣呼吸系統(tǒng)在軸向旋流器10的入口11處被吸入顆粒物去除器100內(nèi)部,并通過顆粒物去除器100。入口11處的進(jìn)氣方向與顆粒物去除器100的縱向中心軸線lc為同軸關(guān)系。在軸向旋流器區(qū)內(nèi)部,空氣被加速并向內(nèi)旋轉(zhuǎn),以使空氣具有三個(gè)速度分量,即用于流動(dòng)連續(xù)性的軸向分量,切向分量,以及用于使空氣中的顆粒具有相應(yīng)動(dòng)量的徑向分量。優(yōu)選地,在旋流器10的入口11處,或者在該旋流器的出口12處,在空氣流90中注入蒸汽88,以填充空氣中顆粒之間的自由空間??諝庵械幕覊m顆粒提供成核表面,從而使蒸汽在該顆粒上凝結(jié),以增加其重量。為了利用旋流器區(qū)實(shí)現(xiàn)更高效或更大的蒸汽凝結(jié)效果,如圖9所示,旋流器入口11為優(yōu)選蒸汽注入點(diǎn)。優(yōu)選地,在旋流器入口11上游設(shè)有進(jìn)氣管道80,該進(jìn)氣管道上設(shè)有用于將蒸汽88注入空氣流中的蒸汽注入口82。注入口82具有噴嘴,優(yōu)選地,該噴嘴的尺寸設(shè)置為蒸汽88提供的噴出速度與位于管道80中及進(jìn)入旋流器10的空氣流的速度相同。優(yōu)選地,所注入的蒸汽88的干燥飽和壓力為1巴(g)。所述蒸汽的質(zhì)量流量可以為空氣質(zhì)量流量的2~3%。蒸汽注入的方向優(yōu)選與管道80內(nèi)的空氣流90方向垂直(交叉),在此之后,已注入的蒸汽88將與所述空氣流90同方向流動(dòng)。在優(yōu)選實(shí)施方式中,蒸汽88在離旋流器入口11距離x處被注入且該距離與進(jìn)氣管道80的寬度或直徑x相等。其為上述優(yōu)選條件下的上游最佳距離,該距離可保證已注入的蒸汽88與空氣流90充分混合,并為蒸汽88在灰塵顆粒上的凝結(jié)提供額外行進(jìn)距離。在旋流器區(qū)下游,灰塵顆粒朝流道外壁徑向向外遷移,并在到達(dá)分流區(qū)20之前,集中于空氣流的最外側(cè)圈層。所注入的蒸汽同樣凝結(jié)于旋流器10和分流區(qū)20的流道內(nèi)壁上。從氣相向液相轉(zhuǎn)變時(shí)的巨大體積縮小(約800倍)產(chǎn)生負(fù)壓或真空。冷凝水與包入該冷凝水內(nèi)的灰塵顆粒一道聚集于顆粒收集區(qū)30內(nèi)。所述冷凝水通過聚水器43被去除,而所含灰塵量極大減少后的空氣流91繼續(xù)流至渦輪機(jī)(未圖示)。以下對(duì)顆粒物去除器100的一種例示實(shí)施方式的軸向旋流器10,分流區(qū)20和顆粒收集區(qū)30進(jìn)行更加詳細(xì)的描述,該例示實(shí)施方式按照行業(yè)伙伴大士發(fā)電有限公司(tuaspowergenerationltd)提供的要求實(shí)施,該公司提供了其燃?xì)鉁u輪機(jī)當(dāng)中一種燃?xì)鉁u輪機(jī)的運(yùn)行數(shù)據(jù),以及相應(yīng)空氣過濾器和空氣過濾器殼體的物理尺寸。該公司還提供了霧霾期間被污染的過濾器,從該過濾器中提取灰塵顆粒用于分析。從上述數(shù)據(jù)中,推導(dǎo)出可附接上述例示顆粒物去除器100的渦輪機(jī)過濾器入口處的空氣流速為3.372m/s,該值為所述燃?xì)鉁u輪機(jī)以最大容量運(yùn)行且消耗空氣量最大時(shí)的平均值。所述顆粒尺寸為10μm,而且所述顆粒的濃度和密度給定為1,900kg/m3。軸向旋流器目前已有成熟的經(jīng)驗(yàn)公式利用已知切向旋流器設(shè)計(jì)實(shí)現(xiàn)給定大小和密度顆粒的至少50%的分離[3]。利用這些已知關(guān)系式,對(duì)于分別為10μm的顆粒尺寸和1900kg/m3的密度,為了實(shí)現(xiàn)90%的分離效率,例示顆粒物去除器100內(nèi)所需的空氣流切向流速估計(jì)為12m/s。針對(duì)其他尺寸和密度已知的顆粒,也可做出與此相同的估計(jì)。利用上述顆粒尺寸和密度數(shù)據(jù)以及3.372m/s的空氣流速,設(shè)計(jì)一種例示軸向旋流器10(圖2),以對(duì)從該軸向旋流器區(qū)的入口11流至其出口12的空氣流進(jìn)行加速和成漩。軸向旋流器10可包括殼體19,該殼體19與螺葉13的內(nèi)部結(jié)構(gòu)18組裝于一起。軸向旋流器10具有200mm×200mm的正方形入口11(圖2b),以和用于流動(dòng)測(cè)試的羽流通道40(示于圖8)的形狀和尺寸相匹配。然而,還可選擇其他幾何橫截面,無論其是否與所述羽流通道的橫截面相同。如圖2b所示,軸向旋流器10的氣流出口12優(yōu)選為圓形,以避免易于在非圓形管道的尖角處發(fā)生的不必要的渦流。入口11和出口12可由殼體19限定。出口12的圓形面積計(jì)算為可將總速度從3.372m/s加速至11.20m/s,其中,3.372m/s為旋流器入口11處的場(chǎng)所的特定速度(相當(dāng)于以上給出的所述行業(yè)伙伴渦輪機(jī)過濾器入口處空氣流速),而11.2m/s為所需的旋流器出口12處的最小速度(以接近以上給出的所需12m/s切向流估值)。可通過僅使外表面逐漸內(nèi)縮(即通過減小殼體19在空氣流動(dòng)方向上的內(nèi)部橫截面積),或通過僅使內(nèi)表面逐漸外擴(kuò)(即通過增大內(nèi)部結(jié)構(gòu)18在所述空氣流方向上的直徑),或通過以上兩者(例如在例示顆粒物去除器100中),實(shí)現(xiàn)從旋流器10的入口11至其出口12的氣流面積變化(縮減)。在入口11處,所述3.372m/s的流速純粹為軸向流速。相反,在出口12處,所述氣流具有三個(gè)速度分量:(一)用于流動(dòng)連續(xù)性的軸向分量(8.42m/s);(二)用于生成徑向分量的切向分量(解為5.89m/s);以及(三)用于使顆粒因牽引力和離心力而向外遷移的徑向分量(0.145m/s)。此三個(gè)速度分量通過在軸向旋流器10內(nèi)設(shè)置螺葉13的內(nèi)部結(jié)構(gòu)18以及通過選擇螺葉13的數(shù)量和螺葉13在旋流器區(qū)的長(zhǎng)度上的扭轉(zhuǎn)角度而實(shí)現(xiàn)。在圖2所示例示顆粒物去除器10中,螺葉13的數(shù)量選為4,所述扭轉(zhuǎn)角度設(shè)為180°,所述旋流器的長(zhǎng)度設(shè)為160mm。螺葉13的數(shù)量取決于旋流器10入口11處產(chǎn)生的等流面積數(shù),例如,對(duì)于正方形的例示旋流器10的入口橫截面,該數(shù)量為4。所述螺葉數(shù)對(duì)于六邊形入口橫截面為6,對(duì)于八邊形入口橫截面為8,而且在圓形入口的情況下可以為大于1的任何數(shù)。螺葉13的所述扭曲角度和行進(jìn)距離(對(duì)于圖2所示實(shí)施方式為180°和160mm)均確定為可產(chǎn)生所需軸向、切向和徑向速度分量以及導(dǎo)致氣流中產(chǎn)生最小壓降的最小值。這通過以計(jì)算流體動(dòng)力學(xué)(cfd)模擬實(shí)施多次試驗(yàn)后實(shí)現(xiàn)。上述包括(一)螺葉13的數(shù)量,(二)分離氣流成漩的長(zhǎng)度以及(三)螺葉13的扭轉(zhuǎn)角度在內(nèi)的所有三個(gè)特征還在當(dāng)蒸汽注入旋流器入口11時(shí)促進(jìn)蒸汽與空氣的混合。最終所得的例示軸向旋流器區(qū)的構(gòu)造如圖2所示。此外,如圖1b和圖2b所示,可在螺葉13的起始位置采用圓角14和平板15(如40mm寬),以使可能會(huì)降低流動(dòng)性的渦流成為直流。當(dāng)設(shè)置平板15時(shí),平板15的平面應(yīng)平行于所述軸向空氣流的方向,而且在平板15的邊緣和螺葉13之間的連接處設(shè)置圓角14,以消除該連接處的尖角。分流區(qū)當(dāng)空氣從例示顆粒物去除器100的軸向旋流器區(qū)排出時(shí),其作為四股螺旋形渦流從兩兩相隔90°的螺葉13之間的流動(dòng)路徑流出。如圖3a所示,在軸向旋流器10的出口處,顆粒仍然處于向分流區(qū)20的外壁29遷移的過程中。分流區(qū)20包括新的恒速管道,該管道同心同軸附接于軸向旋流器10的出口12,以允許顆粒在所述各股渦流從所述軸向旋流器的出口流出時(shí)獲得向該管道外壁29遷移的時(shí)間。該區(qū)域20包括環(huán)形通道28,如圖3b~圖3c所示,該通道可被虛擬地切分為各段均為40mm的切段24,以及三個(gè)同心環(huán)形的等流面積區(qū)域(圈層)。最靠?jī)?nèi)的環(huán)形區(qū)域?yàn)榫哂械谝粴饬鞯牡谝粎^(qū)域21,最靠外的環(huán)形區(qū)域23為具有第三氣流的第三區(qū)域23,第一和第三區(qū)域21,23之間的區(qū)域?yàn)橹虚g環(huán)形區(qū)域22。所述第一環(huán)形區(qū)域,第二環(huán)形區(qū)域和第三環(huán)形區(qū)域21,22,23形成分流區(qū)20內(nèi)的恒速部分。在上述cfd模擬中,對(duì)流經(jīng)各個(gè)40mm的切段24及各個(gè)環(huán)形區(qū)域21,22,23內(nèi)的顆粒數(shù)進(jìn)行計(jì)數(shù),以精確找出外壁29附近顆粒濃度最大的橫截面或點(diǎn)70。如圖3c所示,對(duì)于例示顆粒物去除器100,該點(diǎn)位于距螺葉13末端的120mm處,或距軸向旋流器10入口11的280mm處。此橫截面或點(diǎn)70限定了下一區(qū)30(即顆粒收集區(qū)30)的起始的橫截面或點(diǎn)70,而且取決于離開軸向旋流器10時(shí)的速度分量。如圖4b所示,分離套筒25(在例示顆粒物去除器100中,長(zhǎng)度為20mm)自所述最大濃度點(diǎn)70處開始,從下游的顆粒收集區(qū)30延伸入分流區(qū)20,延伸距離等于前一切段環(huán)形區(qū)域?qū)挾鹊囊话搿L淄?5將最靠?jī)?nèi)的氣流或環(huán)形區(qū)域21與外側(cè)氣流或環(huán)形區(qū)域22,23物理分離。圖4b中顆粒濃度最小的最內(nèi)側(cè)環(huán)形區(qū)域21內(nèi)的氣流被允許繼續(xù)流向顆粒物去除器100的出口。顆粒收集區(qū)如圖5所示,顆粒收集區(qū)30包括外殼39和內(nèi)部組裝體38。外殼39包括中心連接于分流區(qū)20的殼鼓36。外殼39的外徑大于含有分流區(qū)20的三個(gè)環(huán)形區(qū)域21,22,23的所述環(huán)形通道的外徑。因此,如圖6所示,來自分流區(qū)20的外側(cè)環(huán)形區(qū)域22和23(圖4b)的空氣流(如上所述,含最大顆粒濃度)徑向朝外轉(zhuǎn)向,從而降低速度,以允許對(duì)凝結(jié)顆粒(與冷凝水混合)進(jìn)行收集,并允許氣流中任何剩余的蒸汽在外殼39內(nèi)進(jìn)一步冷凝。所述氣流的徑向向外方向變化使得顆粒獲得進(jìn)一步的動(dòng)量,從而使得其朝外殼39的加粗環(huán)形殼鼓36的鼓壁36-9徑向向外遷移。如圖1a,圖5和圖7所示,已經(jīng)朝鼓壁36-9徑向遷移的凝結(jié)顆粒和冷凝水在重力的作用下沿殼鼓36的彎曲的鼓壁36-9向下流至殼鼓36的最低點(diǎn),以待排入設(shè)于殼鼓36下方的濕料收集排水管43中。相比之下,低密度的空氣在進(jìn)入顆粒收集區(qū)30時(shí)在徑向方向上所經(jīng)受的動(dòng)量變化小得多,因此其相對(duì)于顆粒收集區(qū)30內(nèi)的顆粒繼續(xù)沿軸向方向流動(dòng)。這有助于將顆粒(更多以徑向移動(dòng))從所述空氣流(更多以軸向移動(dòng))中分離,并因此促進(jìn)顆粒收集。外殼39還可包括截頭正方錐體34,該錐體通過其較小端中心附接至殼鼓36的下游端。截頭正方錐體34用于接合下文中進(jìn)一步詳細(xì)描述的內(nèi)部組裝體38。在例示顆粒物去除器100中,內(nèi)部組裝體38包括中心內(nèi)錐體37和三個(gè)環(huán)形圈31,32,33。內(nèi)錐體37的直徑朝其下游端逐漸減小。所述三個(gè)環(huán)形圈31,32,33彼此間隔分離,并與內(nèi)錐體37間隔分離。環(huán)形圈31,32,33沿內(nèi)錐體37同心設(shè)置。第一環(huán)形圈31最靠近分流區(qū)20設(shè)置,第三環(huán)形圈33最靠近截頭正方錐體34設(shè)置,第二環(huán)形圈32設(shè)置于第一環(huán)形圈31和第三環(huán)形圈33之間。從圖6可知,所述三個(gè)環(huán)形圈31,32,33構(gòu)造為在該三個(gè)環(huán)形圈31,32,33的相鄰各對(duì)(31和32,32和33)之間限定出泄放通道40,因此其可具有不同的形狀和尺寸。在外殼39內(nèi),可在殼鼓36下游端鄰近截頭正方錐體34處,設(shè)置短的圓形套筒35。該短的圓形套筒35與所述殼鼓的外壁36-9限定出環(huán)形空間,該空間用于將凝結(jié)顆粒和冷凝水存于其內(nèi)。在第三環(huán)形圈33的外表面和所述短的圓形套筒35之間還可限定出另一泄放通道41。泄放通道40和41位于所述空氣流內(nèi),以實(shí)現(xiàn)清潔空氣的三級(jí)泄放以及與來自分流區(qū)20的第一環(huán)形區(qū)域21的氣流的混合。第一環(huán)形區(qū)域21下游的氣流橫截面形成擴(kuò)散部件44,以向泄放通道40,41提供文丘里效應(yīng)并恢復(fù)部分壓力落差。如圖6所示,這可通過將所述三個(gè)環(huán)形圈31,32,33的內(nèi)表面構(gòu)造為相對(duì)于內(nèi)錐體37限定出18.8°的橫截面角的方式實(shí)現(xiàn)。所述三個(gè)環(huán)形圈31,32,33通過結(jié)合于內(nèi)錐體37和該環(huán)形圈31,32,33之間的第一組(組1)四個(gè)肋件51彼此間隔分離并與內(nèi)錐體37間隔分離,肋件51起始于內(nèi)錐體37上的最大顆粒濃度橫截面(即離軸向旋流器10的入口11的280mm距離處),并且其高度沿內(nèi)錐體37的長(zhǎng)度朝下游方向逐漸增大。組1肋件51不僅用作所述三個(gè)環(huán)形圈31,32,33的支撐件和間隔件,而且還用作流經(jīng)第一環(huán)形區(qū)域21的氣流的渦流破壞部件。空氣泄放通道40,41與擴(kuò)散部件44流體連接。上述部分伸入分流區(qū)20內(nèi)且將第一環(huán)形區(qū)域21與第二環(huán)形區(qū)域和第三環(huán)形區(qū)域22,23分離的套筒25可設(shè)于第一環(huán)形圈31的上游端。從所述軸向旋流器出口12排出的渦流在通過分流區(qū)20的同時(shí)繞其扭轉(zhuǎn)。在例示顆粒物去除器100中,如圖7所示,在與所述渦流扭轉(zhuǎn)相同的方向上,此角度相對(duì)于垂直平面v為30°,其中,垂直平面v為垂直于內(nèi)錐體37表面的平面。因此,組1肋件51設(shè)置為與垂直平面v形成30°角。上述形成18.8°擴(kuò)散部件的內(nèi)部組裝體38的下游部分用于氣流混合,壓力恢復(fù)及支撐。在例示顆粒物去除器100中,內(nèi)錐體37由徑向支撐件52連接至外殼39,該徑向支撐件52在顆粒收集區(qū)30的出口55處與截頭方錐34的內(nèi)表面接合。此外,內(nèi)錐體37連接至分流區(qū)20的圓形內(nèi)壁27(示于圖4),該內(nèi)壁與所述分流區(qū)的外壁29限定出所述環(huán)形通道。徑向支撐件52可設(shè)置為內(nèi)錐體37上的第二組(組2)四個(gè)肋件52。微粒旋流分離收集器原型圖8所示為不銹鋼材料制成的例示顆粒物去除器100原型(根據(jù)圖2所示設(shè)計(jì)),該原型用于在特別設(shè)計(jì)和構(gòu)造的羽流通道測(cè)試臺(tái)內(nèi)實(shí)施測(cè)試。在所述羽流通道中,以相應(yīng)cfd模擬中所使用的所有氣流和灰塵含量條件,對(duì)所述微粒旋流分離收集器設(shè)計(jì)(顆粒物去除器100)的功能進(jìn)行了評(píng)價(jià)。所述羽流通道結(jié)果作為評(píng)價(jià)所述cfd結(jié)果的標(biāo)準(zhǔn)。所述原型的尺寸為:入口11為200mm×200mm的正方形;原型長(zhǎng)度為500mm。根據(jù)羽流通道試驗(yàn)結(jié)果及后續(xù)基標(biāo)評(píng)價(jià),制造了按1:6比例增大的商用規(guī)模裝置。該按比例放大的裝置由鋁制成,并用于在發(fā)電廠或其他商業(yè)場(chǎng)所的燃?xì)鉁u輪機(jī)上實(shí)施現(xiàn)場(chǎng)試點(diǎn)測(cè)試。羽流通道內(nèi)的原型測(cè)試通過在羽流通道內(nèi)對(duì)顆粒物去除器100原型進(jìn)行實(shí)驗(yàn),驗(yàn)證了上述基于動(dòng)量原理從大空氣流中去除顆粒物質(zhì)(pm)的概念。在三種不同流量(1m/s,2m/s和3m/s),兩種不同空氣入口溫度(32℃和大氣溫度)以及帶或不帶蒸汽注入的條件下,對(duì)顆粒物去除器100的收集效率(η)進(jìn)行了12次試驗(yàn)。6次試驗(yàn)的空氣入口溫度保持于32℃,以模擬日間時(shí)間;而另6次試驗(yàn)的空氣入口溫度為試驗(yàn)當(dāng)天接近夜間時(shí)間的溫度。共研究了12種不同測(cè)試條件,該12種條件在下表1中給出。試驗(yàn)編號(hào)流速(m/s)溫度(℃)蒸汽注入1a132無1b132有1c1大氣無1d1大氣有2a232無2b232有2c2大氣無2d2大氣有3a332無3b332有3c3大氣無3d3大氣有表1羽流通道試驗(yàn)結(jié)果上述試驗(yàn)所使用的顆粒大小為2.5μm~12μmpm,濃度為0~300μg/m3,并使用了三種速度,即1m/s,2m/s和3m/s。顆粒物去除器100依據(jù)動(dòng)量原理設(shè)計(jì),以利用空氣中懸浮顆粒的質(zhì)量,尤其對(duì)3m/s下10μm(及以上)pm顆粒的質(zhì)量,對(duì)其進(jìn)行分離和收集。主要結(jié)果如下:·≥10μmpm顆粒帶蒸汽注入時(shí)的收集效率η(目標(biāo)值為>90%):83.9%(最小)和95.2%(最大)·≥4μmpm顆粒帶蒸汽注入時(shí)的收集效率η(目標(biāo)值為>70%):72.5%(最小)和79.5%(最大)·≥2.5μmpm顆粒帶蒸汽注入時(shí)的收集效率η(目標(biāo)值為>50%):71.5%(最小)和77.9%(最大)所述軸向旋流器的壓降(目標(biāo)值為約100pa)如下表2所示。速度(m/s)最大壓降(pa)平均壓降(pa)最小壓降(pa)1.021.019.518.02.054.051.048.03.0101.083.566.0表2·顆粒物去除器100以體積流量計(jì)算的空氣泄放率(目標(biāo)值為≤2%):1.98%(12次試驗(yàn)的平均值)·以質(zhì)量流量計(jì)算的蒸汽注入率(目標(biāo)值為≤2%):1.12%(6次試驗(yàn)的平均值)·蒸汽注入導(dǎo)致的出口空氣溫度上升(目標(biāo)值為≤6℃):5.31℃(6次試驗(yàn)的平均值)雖然在以上內(nèi)容中對(duì)本發(fā)明的例示實(shí)施方式進(jìn)行了描述,但是本領(lǐng)域技術(shù)人員可理解的是,在不脫離本發(fā)明的前提下,可對(duì)設(shè)計(jì),構(gòu)造和/或運(yùn)行的細(xì)節(jié)進(jìn)行多種修改和組合。例如,雖然所述擴(kuò)散部件描述為18.8°擴(kuò)散部件,但是還可使用其他角度。所述截頭方錐可設(shè)置為截頭圓錐。所述顆粒收集區(qū)的內(nèi)部組裝體的環(huán)形圈的數(shù)量可從上述三個(gè)修改為兩個(gè)或更多個(gè)。組1肋件可相對(duì)所述垂直平面均朝向一個(gè)不同角度或分別朝向不同角度,而非上述的30°。參考文獻(xiàn)1.wang,l.,旋流器設(shè)計(jì)的理論研究。2004,德克薩斯農(nóng)工大學(xué)。2.vieira,l.g.m.等,過濾用水力旋流器的性能分析和設(shè)計(jì)。巴西化學(xué)工程雜志,2005.22(1):143~152頁(yè)。3.氣體排放控制技術(shù)(空氣質(zhì)量技術(shù))。4.分離設(shè)備:旋流分離器,離心機(jī)和分離設(shè)備的一般設(shè)計(jì)注意事項(xiàng)5.elsayed,k.,利用rans和les方法的旋流分離器幾何結(jié)構(gòu)分析及優(yōu)化。2011,布魯塞爾自由大學(xué)機(jī)械工程系。6.hoffmann,a.c.及l(fā).e.stein,氣體旋流器和旋流管:原理,設(shè)計(jì)和操作(第二版),紐約:施普林格出版社。7.maynard,a.d.,層流條件下軸向旋流器性能的簡(jiǎn)單模型。氣溶膠科學(xué)雜志,2000.31(2):151~167頁(yè)。8.hsiao,t.-c.等,幾何構(gòu)造對(duì)軸向旋流器收集效率的影響。氣溶膠科學(xué)雜志,2011.42:78~86頁(yè)。9.tsai,c.-j.等,在真空條件下去除微粒的軸向旋流器的理論和試驗(yàn)研究。氣溶膠科學(xué)雜志,2004.35:1105~1118。當(dāng)前第1頁(yè)12