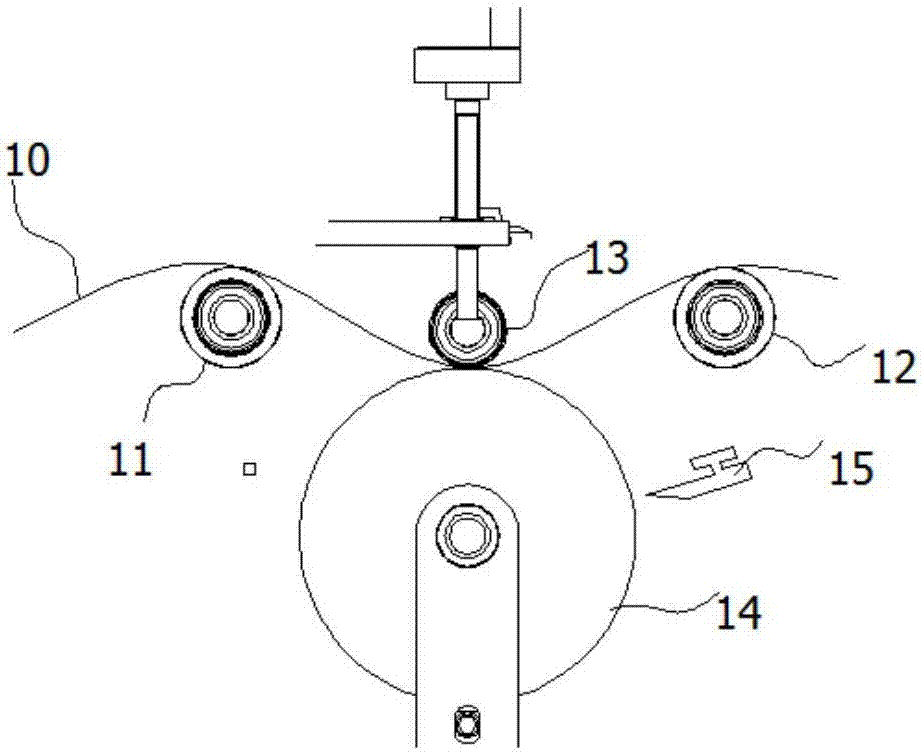
本發(fā)明涉及高溫超導(dǎo)材料的制備領(lǐng)域,尤其是涉及一種高溫超導(dǎo)用哈氏合金基帶的復(fù)合表面處理方法。
背景技術(shù):
:bscco(bismuthstrontiumcalciumcopperoxide,鉍鍶鈣銅氧化物,為一種bi系高溫超導(dǎo)材料)一般被稱為第一代高溫超導(dǎo)體。為了與bscco相區(qū)別,人們把ybco(yttriumbariumcopperoxide,氧化釔鋇銅,為一種y系高溫超導(dǎo)材料)稱為第二代高溫超導(dǎo)體或根據(jù)其制備工藝稱為第二代涂層導(dǎo)體。近年來(lái),美、日、德等技術(shù)發(fā)達(dá)國(guó)家都將第二代涂層導(dǎo)體的實(shí)用化研究作為21世紀(jì)超導(dǎo)材料研究和發(fā)展的熱點(diǎn),并取得了一系列突破性進(jìn)展。與bi系高溫超導(dǎo)材料相比,y系超導(dǎo)體的釘扎力更強(qiáng),超導(dǎo)臨界電流密度要比bi系高出兩個(gè)數(shù)量級(jí),在液氮溫度(77k)下具有高達(dá)7t的不可逆場(chǎng)(bi系在相同條件下的不可逆場(chǎng)僅有0.2t),因此,y系比bi系具有更好的磁場(chǎng)特性。采用廉價(jià)的金屬基帶,使得制備y系超導(dǎo)體的成本低于bi系超導(dǎo)體,規(guī)?;苽湫詢r(jià)比(價(jià)格/ka·m)甚至可以低于金屬銅導(dǎo)線,具有極高的應(yīng)用價(jià)值和廣闊的市場(chǎng)前景。由于ybco超導(dǎo)層是硬、脆的氧化物,晶體流動(dòng)變形性差,難以通過(guò)粉末裝管拉拔工藝或者先涂敷再進(jìn)行后處理的方法實(shí)現(xiàn)高性能長(zhǎng)帶的制備,必須將超導(dǎo)材料沉積在柔性的金屬基帶上,所以,涂層導(dǎo)體的最底層為金屬基帶層。目前用于制備第二代高溫超導(dǎo)帶材的金屬基帶主要有c-276哈氏合金,不銹鋼和鎳-鎢合金。金屬基帶的厚度在50-100微米之間,寬度在1-10厘米之間。為了避免超導(dǎo)層與金屬基帶層之間的互擴(kuò)散,并提供具有高臨界電流密度(jc)的ybco雙軸織構(gòu)生長(zhǎng)所需的模板,需要在超導(dǎo)層與金屬基帶層之間加入過(guò)渡層。過(guò)渡層的作用不僅是阻止基帶與超導(dǎo)層之間的互擴(kuò)散,還要將基帶的雙軸織構(gòu)順延至超導(dǎo)層?;鶐Э棙?gòu)以及表面狀況的好壞是制備涂層導(dǎo)體的關(guān)鍵。目前主要有三種工藝路線來(lái)制備這樣的基帶:軋制輔助雙軸織構(gòu)基帶(rolling-assistedbiaxiallytexturedsubstrates,rabits)技術(shù)、傾斜襯底沉積(inclinedsubstratedeposition,isd)技術(shù)、離子束輔助沉積(ion-beam-assisteddeposition,ibad)技術(shù)。rabits技術(shù)是由oakridge國(guó)家實(shí)驗(yàn)室發(fā)明的,即在一定的形變速率下使金屬材料經(jīng)受軋制的變形作用,總變形量一般為原材料厚度的95%,并且通常以每次軋制10%的變形量經(jīng)多道軋制完成,每道軋制后要經(jīng)過(guò)退火處理,軋制完成后還要進(jìn)行再結(jié)晶處理,以獲得理想的{001}<100>織構(gòu)。rabits法制備雙軸織構(gòu)的金屬基帶的工藝流程簡(jiǎn)單,但制備過(guò)程中連續(xù)的形變熱處理操作使得其制造成本難以下降,已逐漸被日益成熟的ibad技術(shù)所取代。ibad技術(shù)與isd技術(shù)類似,都是在無(wú)織構(gòu)的金屬基帶上沉積一層具有立方織構(gòu)的mgo種子層。但是mgo織構(gòu)的好壞嚴(yán)重依賴基底的光滑度。研究表明,采用ibad工藝制備具有雙軸定向生長(zhǎng)結(jié)構(gòu)的mgo薄膜晶體的首要條件是必須采用均方根表面粗糙度(rms)小于1納米(原子力顯微鏡掃描面積為5×5平方微米)的襯底。然而,由于受到軋機(jī)精度、軋輥光潔度及軋制環(huán)境清潔度的限制,目前市售的高規(guī)格金屬基帶的表面粗糙度大約在75納米左右,更一般的則大于100納米,遠(yuǎn)遠(yuǎn)不能滿足高溫超導(dǎo)帶材功能層制備的要求。2003年以前,主要采用連續(xù)化機(jī)械拋光方法來(lái)提高金屬基帶的表面質(zhì)量。傳統(tǒng)的機(jī)械拋光不能有效去除樣品表面的變形層,即使經(jīng)過(guò)反復(fù)的研磨,也會(huì)出現(xiàn)再次變形的可能,即伴隨著消除嚴(yán)重變形層又有形成新的變形層的可能。此外,機(jī)械拋光方法的拋光速度慢,而且拋光后的表面質(zhì)量很難達(dá)到要求。美國(guó)專利us7811972中闡述了一種機(jī)械拋光方法。采用粗拋和精拋的兩步處理,可以得到表面粗糙度rms<1納米的金屬基帶。但由于拋光速度只有5m/h,遠(yuǎn)遠(yuǎn)低于后續(xù)的ibad工藝(鍍膜速度>100m/h)和mocvd工藝(鍍膜速度>60m/h),不適合大規(guī)模生產(chǎn)應(yīng)用。電化學(xué)拋光也稱電解拋光,在電化學(xué)拋光工藝中,將被拋光金屬工件作為陽(yáng)極,不溶性金屬板作為陰極,兩極同時(shí)浸入到電解槽中,通以直流電而產(chǎn)生有選擇性的陽(yáng)極溶解,從而達(dá)到工件表面光亮度增大的效果。電化學(xué)拋光可以非常有效的去除表面的氧化層和應(yīng)力層。與傳統(tǒng)的機(jī)械拋光相比,電化學(xué)拋光具有生產(chǎn)效率高、成本低廉和均勻性好等優(yōu)點(diǎn)。電解液的成分與被拋光金屬部件的化學(xué)組分相關(guān),需要進(jìn)行大量的試驗(yàn),才能找到理想的拋光參數(shù)和合適的電解液。另外,使用電化學(xué)拋光對(duì)金屬基帶的原始表面粗糙度也有一定要求。美國(guó)專利us7,169,286中描述了電化學(xué)拋光的方法。實(shí)踐證明,原始金屬基帶的表面粗糙度必須低于50納米,才能有效地獲得rms<1納米的金屬基帶。金屬有機(jī)沉積(metalorganicdeposition,mod)工藝,是通過(guò)在原始金屬基帶表面涂布金屬有機(jī)溶液,干燥后在金屬基帶表面沉積金屬氧化物薄膜,使表面粗糙度達(dá)到制備要求。為了達(dá)到表面粗糙度rms<1納米的水平,往往需要進(jìn)行多次沉積。例如,為了使表面粗糙度從30納米下降到1納米往往就需要20至30次以上的薄膜沉積,大大影響了生產(chǎn)效率。如上所述,現(xiàn)有涂層導(dǎo)體用超導(dǎo)基帶表面粗糙度的處理工藝中,或工藝處理時(shí)間長(zhǎng),單位時(shí)間產(chǎn)能低下,無(wú)法滿足后續(xù)超導(dǎo)材料的制備需求;或工藝穩(wěn)定性差,工藝的精確度得不到保證,影響超導(dǎo)材料的制備良率,是影響高溫超導(dǎo)基帶批量生產(chǎn)的關(guān)鍵因素。國(guó)產(chǎn)哈氏合金基帶受軋制水平限制,表面粗糙度一般在200納米左右,不能滿足電化學(xué)拋光工藝對(duì)輸入基帶原始表面粗糙度的要求。技術(shù)實(shí)現(xiàn)要素:目前,第二代高溫超導(dǎo)帶材用哈氏合金基帶的最后一道表面平整工藝大都采用電化學(xué)拋光工藝處理,為了滿足電化學(xué)拋光工藝對(duì)輸入基帶表面粗糙度的要求,本發(fā)明提供一種高溫超導(dǎo)帶材用哈氏合金基帶的復(fù)合表面處理方法。本發(fā)明采用機(jī)械拋光工藝,選用合適的拋光液配比和拋光參數(shù)組合,可快速完成對(duì)基帶表面粗糙度的預(yù)處理,達(dá)到電化學(xué)拋光工藝對(duì)原始基帶表面粗糙度的要求。本發(fā)明的目的可以通過(guò)以下技術(shù)方案來(lái)實(shí)現(xiàn):一種高溫超導(dǎo)帶材用哈氏合金基帶的復(fù)合表面處理方法,該復(fù)合表面處理方法用以降低哈氏合金基帶的表面粗糙度,使哈氏合金基帶均方根表面粗糙度小于1納米,該復(fù)合表面處理方法包括兩個(gè)處理階段,第一階段采用機(jī)械拋光方法,使哈氏合金基帶的表面粗糙度降低至50納米以下;第二階段對(duì)機(jī)械拋光后的合金基帶進(jìn)行電化學(xué)拋光處理,使哈氏合金基帶的均方根表面粗糙度進(jìn)一步降至低于1納米,滿足第二代高溫超導(dǎo)體對(duì)基帶表面粗糙度的要求。第一階段的機(jī)械拋光方法采用粗拋和精拋兩個(gè)拋光單元。粗拋和精拋選用的拋光液均為氧化鋁拋光液,但配方組成不同。粗拋單元拋光液的各組分質(zhì)量份配比范圍為:研磨顆粒11~500g、次亞磷酸或次亞磷酸鹽1~50g、表面活性劑50~500mg、加水至1l;精拋單元拋光液制備方法是將各組分混合到去離子水中。精拋單元拋光液各組分質(zhì)量份配比范圍為:研磨顆粒1~300g、水溶性含氮聚合物0.1~30g、加水至1l。粗拋單元拋光液制備方法是將各組分混合到去離子水中。粗拋單元拋光液中研磨顆粒粒徑為200nm,精拋單元拋光液中研磨顆粒粒徑為30nm;粗拋單元拋光液中表面活性劑優(yōu)選為peg400。用堿性ph調(diào)節(jié)劑(如koh)和酸性ph調(diào)節(jié)劑(如hno3)調(diào)節(jié)粗拋單元拋光液的ph值為9~14,較佳地為10~12。用堿性ph調(diào)節(jié)劑(如koh)和酸性ph調(diào)節(jié)劑(如hno3)調(diào)節(jié)精拋單元拋光液ph值范圍為8~12。本發(fā)明粗拋和精拋選用的拋光液中氧化鋁具有很高的硬度(莫氏硬度9.1),不宜破碎且顆粒均勻,具有良好的磨削性能。本發(fā)明粗拋和精拋選用的拋光液的ph值對(duì)拋光元件表面粗糙度有較明顯的影響。拋光過(guò)程中,當(dāng)保持拋光液處于微堿狀態(tài)時(shí),拋光元件表面具有較小的粗糙度。粗拋單元的拋光輪的旋轉(zhuǎn)方向與哈氏合金基帶前進(jìn)的方向相反,精拋單元的拋光輪的旋轉(zhuǎn)方向與哈氏合金基帶前進(jìn)的方向相同。拋光輪的旋轉(zhuǎn)方向可以抵消拋光輪對(duì)薄帶的作用力,保證整個(gè)拋光系統(tǒng)穩(wěn)定運(yùn)行。粗拋單元的拋光輪與精拋單元的拋光輪均為羊毛材質(zhì)的短毛類毛氈輪。本發(fā)明在機(jī)械拋光過(guò)程中機(jī)械拋光工藝采用常規(guī)工藝即可,優(yōu)選的機(jī)械拋光的工藝條件如下:1、精拋單元的拋光工藝條件:拋光輪轉(zhuǎn)速:600~1000r/min拋光輪直徑:100~150mm拋光液流量:10~30ml/min外加壓力:8kg基帶走線速度:20~40m/h。2、粗拋單元的拋光工藝條件:拋光輪轉(zhuǎn)速:400~800r/min拋光輪直徑:100~150mm拋光液流量:10~30ml/min外加壓力:5kg基帶走線速度:20~40m/h。第二階段的電化學(xué)拋光處理使用的電化學(xué)拋光液的成分與重量份為:目前從理論上還不能確定某種金屬或合金最適宜的拋光液組成和比例,大多采用反復(fù)試驗(yàn)來(lái)確定合適的拋光液成分。本發(fā)明通過(guò)大量實(shí)驗(yàn)確定了以硫酸-磷酸及添加劑體系作為電解拋光液,改善了哈氏合金c276基帶的表面質(zhì)量,取得了較好的拋光效果。第二階段的電化學(xué)拋光處理的工藝條件為:控制拋光電流密度為15-40a·cm-2,拋光時(shí)間為30-90s,電化學(xué)拋光液用真空泵打入拋光池,控制拋光液溫度為50-60℃,陽(yáng)極與陰極之間的間距為10-30mm,拋光完畢,使用0.5mol/l的碳酸鈉溶液中和并在無(wú)水乙醇和去離子水中進(jìn)行超聲清洗。第二階段的電化學(xué)拋光處理工藝采用卷對(duì)卷工藝模式,包括步驟:放卷、粗洗、漂洗、電拋、漂洗、中和、漂洗、精洗、烘干、收卷。以上步驟為常規(guī)步驟,工藝條件根據(jù)實(shí)際情況調(diào)整。本發(fā)明所述的哈氏合金基帶優(yōu)選為c-276哈氏合金。與現(xiàn)有技術(shù)相比,本發(fā)明所配制的機(jī)械拋光液和電化學(xué)拋光液均不需要攪拌,通過(guò)機(jī)械拋光和電化學(xué)拋光復(fù)合使用的方法,可快速完成金屬基帶的表面平整要求,使得金屬基帶的表面粗糙度降低至1納米以下,滿足涂層導(dǎo)體用金屬基帶的使用要求。附圖說(shuō)明圖1是本發(fā)明的表面處理方法的流程示意圖;圖2是本發(fā)明的第一階段機(jī)械拋光工藝的結(jié)構(gòu)圖;圖3是本發(fā)明的第二階段電化學(xué)拋光工藝的流程示意圖。具體實(shí)施方式本發(fā)明提出的一種尤其適用于第二代高溫超導(dǎo)材料用哈氏合金基帶的復(fù)合表面處理方法,能夠?qū)⒔饘倩鶐У谋砻娲植诙冉档椭?納米以下。該復(fù)合表面處理方法針對(duì)目前市場(chǎng)上供應(yīng)的原始金屬基帶,通過(guò)兩個(gè)階段的表面平整工藝,分別在第一階段采用機(jī)械拋光工藝將哈氏合金基帶的表面粗糙度降至50納米以下,第二階段以電化學(xué)拋光工藝作為表面平整處理手段,使得金屬基帶的表面粗糙度進(jìn)一步降低至1納米以下。所述第一階段的表面平整處理工藝為機(jī)械拋光工藝,其目的是將哈氏合金基帶的表面粗糙度降至50納米以下,因此相比較原本1納米的苛刻要求,可降低或適當(dāng)修改第一階段中采用的表面平整處理技術(shù)的工藝要求,以提高整個(gè)工藝效率。所述第二階段的表面平整處理工藝,采用電化學(xué)拋光方法,能夠穩(wěn)定地將哈氏合金基帶表面粗糙度降低至1納米以下。下面結(jié)合附圖對(duì)本發(fā)明的具體實(shí)施方式做詳細(xì)說(shuō)明。附圖1是本發(fā)明的表面處理方法的流程示意圖。如圖1所示,該方法包括以下步驟:對(duì)原始未經(jīng)過(guò)任何表面處理的哈氏合金基帶(可以承受900℃高溫的合金材料),進(jìn)行表面粗糙度測(cè)量。一般選用表面粗糙度測(cè)量?jī)x或原子力顯微鏡(afm)等測(cè)量手段進(jìn)行。測(cè)量的目的在于,對(duì)于不同表面粗糙度的原始金屬基帶,選擇對(duì)應(yīng)的表面平整工藝參數(shù)。根據(jù)上述測(cè)量結(jié)果,對(duì)于原始表面粗糙度低于50納米的金屬基帶,可以縮短第一階段機(jī)械拋光工藝的處理時(shí)間或者直接跳過(guò)此階段;對(duì)于表面粗糙度在50納米以上的金屬基帶,選擇機(jī)械拋光工藝和電化學(xué)拋光工藝聯(lián)用的工藝路線進(jìn)行表面平整處理。下面再以兩個(gè)具體實(shí)施例對(duì)本發(fā)明做進(jìn)一步說(shuō)明實(shí)施例1選取的原始金屬基帶是c-276哈氏合金基帶,寬度為10毫米,厚度為100微米,長(zhǎng)度為100米。經(jīng)afm測(cè)定,基帶表面均方根粗糙度rms=45納米,故,跳過(guò)第一階段機(jī)械拋光過(guò)程,直接選擇第二階段的電化學(xué)拋光工藝為表面平整處理工藝。該電化學(xué)拋光工藝的步驟如表1所示:表1電化學(xué)拋光工藝的步驟放料粗洗漂洗電化學(xué)拋光漂洗中和漂洗精洗烘干收料首先,選用卷對(duì)卷(reeltoreel)工藝模式,布置整個(gè)電化學(xué)工藝的機(jī)臺(tái),在圖3所示的放料卷20和收料卷27之間,設(shè)置了預(yù)清洗機(jī)臺(tái)21、電解拋光機(jī)臺(tái)22、清洗機(jī)臺(tái)23、中和機(jī)臺(tái)24、精細(xì)機(jī)臺(tái)25和干燥機(jī)臺(tái)26。預(yù)清洗機(jī)臺(tái)21采用堿溶液以及熱水對(duì)原始金屬基帶實(shí)施預(yù)清洗,以去除原始金屬基帶上可能存在的自然氧化物及其他雜質(zhì)。電解拋光機(jī)臺(tái)22采用配制好的電化學(xué)拋光液,使金屬基帶浸沒(méi)于該電化學(xué)拋光液中,然后以該金屬基帶為陽(yáng)極、以鉛板為陰極接入拋光電壓。電化學(xué)拋光液的成分由體積分?jǐn)?shù)80%-85%的濃磷酸、體積分?jǐn)?shù)95%-98%的濃硫酸、甘油和丁二酮肟粉組成。其重量份數(shù)分別為:濃磷酸:85份;濃硫酸:15份;甘油:3份;丁二酮肟粉:8份??刂茠伖怆娏髅芏葹?0a·cm-2,拋光時(shí)間為45s。拋光液用真空泵打入拋光池,控制拋光液溫度為55℃。陽(yáng)極與陰極之間的間距為20mm。拋光完畢,使用0.5mol/l的碳酸鈉溶液中和并在無(wú)水乙醇和去離子水中進(jìn)行超聲清洗。電解拋光完成后金屬基帶連續(xù)進(jìn)入清洗機(jī)臺(tái)23、中和機(jī)臺(tái)24、精細(xì)機(jī)臺(tái)25中,以去除拋光過(guò)程中可能存在的拋光液殘余物質(zhì)。最后將金屬基帶導(dǎo)入干燥機(jī)臺(tái)26中進(jìn)行干燥處理,并通過(guò)收料卷27收料,完成第二階段的表面平整處理工藝。第二階段表面處理工藝完成后,金屬基帶的表面粗糙度經(jīng)afm測(cè)定,其粗糙度值ra<1納米。實(shí)施例2選取的原始金屬基帶是c-276哈氏合金基帶,寬度為10mm,厚度為0.1mm,長(zhǎng)度為100m。表面粗糙度ra=176納米。本實(shí)施例第一階段采用機(jī)械拋光工藝對(duì)基帶表面進(jìn)行平整處理,見(jiàn)附圖2?;鶐?0穿過(guò)導(dǎo)輪11和導(dǎo)輪12,在上部輪13的作用力下,通過(guò)機(jī)械拋光輪14進(jìn)行拋光,拋光液通過(guò)噴嘴15加入到機(jī)械拋光輪14中。只要合理調(diào)節(jié)機(jī)械拋光輪14的轉(zhuǎn)速,上部輪13的作用力,拋光液的組成和加入量,以及基帶10的運(yùn)行速度后,一次拋光可以達(dá)到的表面粗糙度低于50納米。粗拋單元拋光液的原料配比如下(質(zhì)量份):三氧化二鋁(200nm)次亞磷酸鉀表面活性劑(peg400)去離子水400.1200mg/kg加至100精拋單元拋光液的原料配比如下(質(zhì)量份):三氧化二鋁(30nm)聚丙烯酰胺(相對(duì)分子質(zhì)量200000)去離子水82加至100然后實(shí)施第二階段的表面平整處理,本實(shí)施例采用與實(shí)施例1相同的第二階段處理工藝,在此不再贅述。第二階段表面處理工藝完成后,金屬基帶的表面粗糙度經(jīng)afm測(cè)定,其粗糙度值ra<1納米。相比于現(xiàn)有技術(shù),本發(fā)明的復(fù)合表面處理方法降低了對(duì)金屬基帶的表面粗糙度要求,避免了單獨(dú)使用機(jī)械拋光工藝效率低,效果差的不良現(xiàn)象,為涂層導(dǎo)體用哈氏合金基帶的規(guī)?;?yīng)提供了一種解決方案。上述的對(duì)實(shí)施例的描述是為便于該
技術(shù)領(lǐng)域:
的普通技術(shù)人員能理解和使用發(fā)明。熟悉本領(lǐng)域技術(shù)的人員顯然可以容易地對(duì)這些實(shí)施例做出各種修改,并把在此說(shuō)明的一般原理應(yīng)用到其他實(shí)施例中而不必經(jīng)過(guò)創(chuàng)造性的勞動(dòng)。因此,本發(fā)明不限于上述實(shí)施例,本領(lǐng)域技術(shù)人員根據(jù)本發(fā)明的揭示,不脫離本發(fā)明范疇所做出的改進(jìn)和修改都應(yīng)該在本發(fā)明的保護(hù)范圍之內(nèi)。當(dāng)前第1頁(yè)12