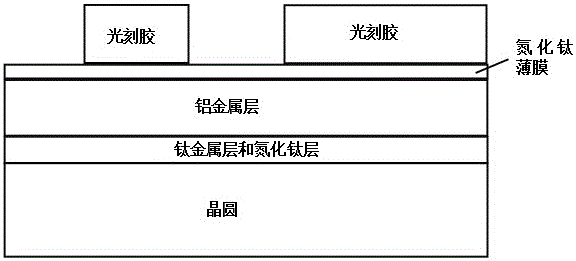
本發(fā)明涉及一種半導(dǎo)體領(lǐng)域的蝕刻工藝,具體涉及一種無金屬線切口問題的金屬濕法蝕刻方法。
背景技術(shù):目前,在濕法蝕刻工藝中,由于金屬表面粗糙不平,使得光刻膠(PR)與金屬之間的附著力不理想,導(dǎo)致在濕法蝕刻工藝過程中,濕法蝕刻的基本(baseline)上會出現(xiàn)類似“老鼠咬(mousebite)”的切口,嚴重的會使金屬線斷開。例如下述中現(xiàn)有技術(shù)的一種濕法蝕刻流程,該流程包含以下步驟:步驟1、在晶圓上依次金屬濺鍍(sputter)一層400埃(?)的鈦金屬(TI)層、一層1000埃的氮化鈦(TIN)層,以及一層40000埃的鋁金屬(AL)層。步驟2、根據(jù)光刻掩膜版上所設(shè)計的圖案,在晶圓上涂覆光刻膠(PR)并進行光刻(PH),在晶圓表面上(即上述的鋁金屬層表面上)設(shè)計作為金屬線(M1)的區(qū)域留下光刻膠。步驟3、由于經(jīng)過光刻顯影后,保留下來的光刻膠膜發(fā)生了軟化和膨脹,光刻膠與鋁金屬層表面的附著力下降,為了保證下一道對鋁金屬進行濕法蝕刻工序能順利進行,需使光刻膠和鋁金屬層表面更好地粘結(jié),所以對保留下的光刻膠進行紫外線硬化(UVcure)工藝。步驟4、濕法蝕刻去除未被光刻膠覆蓋的鋁金屬層、氮化鈦(TIN)層和鈦金屬(TI)層的相應(yīng)多余部分。步驟5、經(jīng)過濕法蝕刻并完成金屬線(M1)的形成后,對其進行金屬濕法蝕刻后的灰化處理(ASHING-AFTERMETALWETET),去除金屬線(M1)表面上保留的光刻膠。步驟6、在晶圓表面涂覆清洗溶劑(SOLVENT),并運用超聲波(MEGASONIC)對晶圓表面以及其表面形成的金屬線(M1)進行清洗。步驟7、對晶圓進行55秒的后道制程的灰化處理(ASHING-BEOL),BEOL即backendofline,指接觸(contact)之后所涉及到的工藝步驟。步驟8、對晶圓進行蝕刻后檢查(AEI,AfterEtchingInspection)。在通過濕法蝕刻完成金屬線的制成工藝后,對晶圓產(chǎn)品實施全檢或抽樣檢查,以提高產(chǎn)品良率,避免不良品外流;達到品質(zhì)的一致性和制程的重復(fù)性;顯示制程能力的指針;阻止異常擴大、節(jié)省成本。在上述的一種濕法蝕刻流程的缺點在于,在對鋁金屬(AL)層表面涂覆光刻膠(PR)時,由于鋁金屬層表面粗糙不平,使光刻膠(PR)與鋁金屬層表面之間的附著力不理想,最終會導(dǎo)致通過濕法蝕刻鋁金屬層形成的金屬線(M1)上產(chǎn)生金屬線切口問題。
技術(shù)實現(xiàn)要素:本發(fā)明提供了一種無金屬線切口問題的金屬濕法蝕刻方法,提高金屬與光刻膠之間的附著力,解決濕法蝕刻中由于金屬與光刻膠附著力不理想,造成的金屬線切口問題。為實現(xiàn)上述目的,本發(fā)明提供了一種無金屬線切口問題的金屬濕法蝕刻方法,其特點是,該方法包含以下步驟:步驟1、在晶圓上依次濺鍍鈦金屬層、氮化鈦層和鋁金屬層,再在鋁金屬層的表面上濺鍍一層氮化鈦薄膜;步驟2、采用光刻,在鋁金屬層上的整個氮化鈦薄膜的表面上涂覆光刻膠,再根據(jù)光刻掩膜版的設(shè)計進行顯影,在晶圓上需要制成金屬線的區(qū)域內(nèi)保留光刻膠;步驟3、對氮化鈦薄膜表面上涂覆的光刻膠進行紫外線硬化工藝處理;步驟4、在未涂覆有光刻膠的區(qū)域內(nèi)采用濕法蝕刻去除鋁金屬層和鋁金屬層表面上氮化鈦薄膜,從而在涂覆有光刻膠的區(qū)域內(nèi)制成鍍有氮化鈦薄膜的金屬線;步驟5、將鍍有氮化鈦薄膜的金屬線上所涂覆的光刻膠去除;步驟6、清洗晶圓表面以及其上制成的鍍有氮化鈦薄膜的金屬線;步驟7、將未制成金屬線區(qū)域內(nèi)的鈦金屬層、氮化鈦層,以及金屬線上鍍有的氮化鈦薄膜采用濕法蝕刻去除,完成金屬線的制成;步驟8、對晶圓進行蝕刻后灰化處理;步驟9、對晶圓進行蝕刻后檢查。上述的步驟5中,采用金屬濕法蝕刻后的灰化處理去除光刻膠。上述的步驟6中,在晶圓表面以及其晶圓表面制成的鍍有氮化鈦薄膜的金屬線上采用涂覆清洗溶劑及超聲波進行清洗。上述的步驟8中,對制成金屬線的晶圓進行55秒的后道制程的灰化處理。上述的步驟9中,晶圓的蝕刻后檢查采用全檢或抽樣檢查。本發(fā)明一種無金屬線切口問題的金屬濕法蝕刻方法和現(xiàn)有技術(shù)的濕法蝕刻制成金屬線的工藝相比,其優(yōu)點在于,本發(fā)明在用于制成金屬線的鋁金屬層的表面上增加一層氮化鈦薄膜,利用氮化鈦薄膜的平滑表面,優(yōu)化了光刻膠與鋁金屬層之間的附著力,解決了在對鋁金屬層進行濕法蝕刻以制成金屬線時,由于鋁金屬層表面的粗糙不平,造成光刻膠與鋁金屬層之間的附著力不理想,從而導(dǎo)致在最終制成的金屬線上發(fā)生金屬線切口的問題,提高產(chǎn)品良率;本發(fā)明中上述增加的氮化鈦薄膜又可以最后用濕法蝕刻來去除,從而獲得和原來一樣的金屬層結(jié)構(gòu)。附圖說明圖1為本發(fā)明一種無金屬線切口問題的金屬濕法蝕刻方法的流程圖;圖2為本發(fā)明一種無金屬線切口問題的金屬濕法蝕刻方法的步驟1和步驟2的示意圖;圖3為本發(fā)明一種無金屬線切口問題的金屬濕法蝕刻方法的步驟4的示意圖;圖4為本發(fā)明一種無金屬線切口問題的金屬濕法蝕刻方法的步驟5的示意圖;圖5為本發(fā)明一種無金屬線切口問題的金屬濕法蝕刻方法的步驟7的示意圖。具體實施方式以下結(jié)合附圖,進一步說明本發(fā)明具體實施例。如圖1所示,本發(fā)明公開了一種無金屬線切口問題的金屬濕法蝕刻方法,該方法包含以下步驟:步驟1、如圖2所示,在晶圓上濺鍍一層400埃(?)的鈦金屬(TI)層,在鈦金屬(TI)層上濺鍍一層1000埃的氮化鈦(TIN)層,再在氮化鈦(TIN)層上濺鍍一層40000埃的鋁金屬(AL)層。本發(fā)明的區(qū)別技術(shù)特征在于,在40000埃的鋁金屬層的表面上再濺鍍一層250埃的氮化鈦薄膜(TINfilm)。步驟2、采用光刻(PH)技術(shù),在鋁金屬層上的整個氮化鈦薄膜的表面上涂覆光刻膠(PR),再根據(jù)光刻掩膜版上所設(shè)計的圖案,進行顯影,在晶圓上設(shè)計用于制成金屬線區(qū)域內(nèi)的氮化鈦薄膜的表面上保留光刻膠。步驟3、對氮化鈦薄膜表面上涂覆的光刻膠進行紫外線硬化工藝(UVcure)處理,以解決光刻膠膜在進行光刻后發(fā)生的軟化和膨脹現(xiàn)象,保證下一道對鋁金屬進行濕法蝕刻工序的順利進行。步驟4、如圖3所示,采用濕法蝕刻去除鋁金屬層和鋁金屬層表面上氮化鈦薄膜,從而在涂覆有光刻膠的區(qū)域內(nèi)制成鍍有一層250埃的氮化鈦薄膜的金屬線(M1),同時也保留該金屬線(M1)區(qū)域下氮化鈦(TIN)層和鈦金屬(TI)層的相應(yīng)部分。步驟5、如圖4所示,經(jīng)過濕法蝕刻形成鍍有氮化鈦薄膜的金屬線(M1)后,對其進行金屬濕法蝕刻后的灰化處理(ASHING-AFTERMETALWETET),將鍍有氮化鈦薄膜的金屬線上所涂覆的光刻膠去除。步驟6、在晶圓表面涂覆清洗溶劑(SOLVENT),并對晶圓運用超聲波(MEGASONIC),清洗晶圓表面以及其上制成的鍍有氮化鈦薄膜的金屬線。步驟7、如圖5所示,將未制成有金屬線的區(qū)域內(nèi)的位于底部的400埃鈦金屬層、1000埃的氮化鈦層,以及金屬線頂部上鍍有的250埃的氮化鈦薄膜,采用濕法蝕刻去除。保留金屬線(M1)以及金屬線下的鈦金屬層和氮化鈦層,將鋁金屬層所制成的金屬線露出,完成金屬線的制成。步驟8、對制成金屬線的晶圓進行55秒的后道制程的灰化處理(ASHING-BEOL)。步驟9、在通過濕法蝕刻完成金屬線的制成工藝后,對晶圓進行蝕刻后檢查(AEI),蝕刻后檢查采用全檢或抽樣檢查。盡管本發(fā)明的內(nèi)容已經(jīng)通過上述優(yōu)選實施例作了詳細介紹,但應(yīng)當(dāng)認識到上述的描述不應(yīng)被認為是對本發(fā)明的限制。在本領(lǐng)域技術(shù)人員閱讀了上述內(nèi)容后,對于本發(fā)明的多種修改和替代都將是顯而易見的。因此,本發(fā)明的保護范圍應(yīng)由所附的權(quán)利要求來限定。