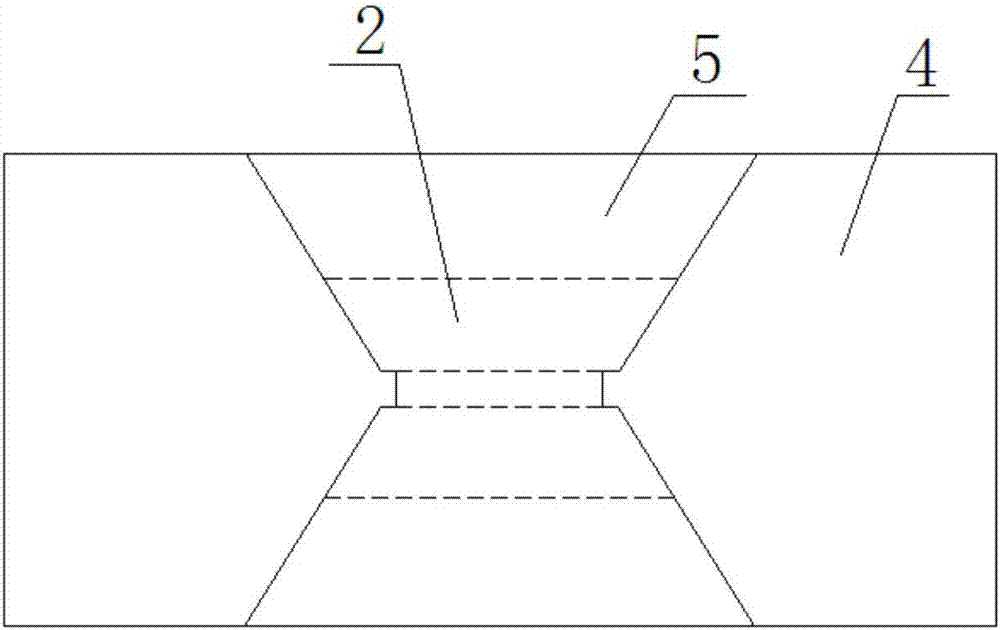
本發(fā)明屬于電火工品技術(shù)領(lǐng)域,具體涉及一種片式合金箔點(diǎn)火電阻器及其制備方法。
背景技術(shù):通常,橋絲式電火工品點(diǎn)火器是人們一直普遍使用的點(diǎn)火方式,是由一跟懸吊式電阻加熱絲和兩個(gè)電極相連組成,這種結(jié)構(gòu)的點(diǎn)火器在較強(qiáng)的振動環(huán)境下,橋絲徑向存在的拉伸作用容易導(dǎo)致橋絲發(fā)生變形,造成橋絲阻值改變從而影響點(diǎn)火器點(diǎn)火性能,并可能造成橋絲斷裂及焊點(diǎn)破裂脫焊,造成點(diǎn)火器瞎火,極大的降低了橋絲式點(diǎn)火器的可靠性水平,且橋絲式點(diǎn)火器一般無法滿足低發(fā)火能量和快速發(fā)火的要求。通常的金屬薄膜橋點(diǎn)火器采用物理氣相沉積方式直接沉積在基底上,基體采用聚酰亞胺基板,全套工藝采用濺射的方法進(jìn)行制備。該方法能量低,一致性差,而且成本高。
技術(shù)實(shí)現(xiàn)要素:為解決上述技術(shù)問題,本發(fā)明提供了一種片式合金箔點(diǎn)火電阻器及其制備方法,該片式合金箔點(diǎn)火電阻器通過采用FR-4雙面覆銅玻纖板做基體、鎳鉻合金箔做點(diǎn)火材料、聚酰亞胺做保護(hù)層,解決了橋絲式點(diǎn)火器可靠性低、無法滿足低發(fā)火能量和快速發(fā)火的要求的問題。本發(fā)明通過以下技術(shù)方案得以實(shí)現(xiàn)。本發(fā)明提供的一種片式合金箔點(diǎn)火電阻器,包括基板、抗靜電層、聚酰亞胺膜、電阻層、保護(hù)層、表背搭接層、銅層、鎳層、錫層和焊盤;所述基板的上表面中部設(shè)置有抗靜電層,下表面的兩端分別設(shè)置有焊盤;所述聚酰亞胺膜設(shè)置在基板和抗靜電層的上表面上,所述聚酰亞胺膜的上表面設(shè)置有電阻層,且所述電阻層的兩端分別通過表背搭接層與焊盤連接,所述電阻層上還設(shè)置有保護(hù)層;所述銅層于保護(hù)層的兩側(cè)設(shè)置在電阻層上,且銅層將表背搭接層和焊盤的外表面覆蓋,所述銅層的外表面上還依次設(shè)置有鎳層和錫層。所述基板為FR-4雙面覆銅玻纖板。所述基板的外形尺寸為50mm×60mm,厚度為0.35mm~0.6mm。所述抗靜電層和焊盤的材料為Cu。所述抗靜電層和焊盤的厚度為0.018mm~0.03mm。所述聚酰亞胺膜的厚度為0.025mm~0.04mm。所述電阻層的材料為NiCr合金或Ni-80.Cr-20合金。所述電阻層的厚度為0.0035mm~0.005mm。所述保護(hù)層的材料為光敏性聚酰亞胺。所述表背搭接層的材料為銀漿。一種片式合金箔點(diǎn)火電阻器的制備方法,包括以下步驟:A、對基板進(jìn)行清洗,去除表面的油污及雜質(zhì);B、通過光刻技術(shù)在基板的上表面的中部形成抗靜電層,并在基板的下表面的兩端形成焊盤;C、通過熱壓的方法將聚酰亞胺膜貼在基板和抗靜電層的上表面;D、通過壓合的方法將電阻層貼在聚酰亞胺膜的上表面;E、采用濕法刻蝕技術(shù)對電阻層進(jìn)行刻蝕加工出橋絲,刻蝕的深度為電阻層的厚度;F、采用光刻技術(shù)在步驟E進(jìn)行刻蝕處理的部位上形成保護(hù)層,且保護(hù)層還覆蓋于電阻層的橋絲上;G、采用端面涂銀的技術(shù)在基板的兩端形成表背搭接層;H、根據(jù)產(chǎn)品尺寸要求,按常規(guī)方法對基片進(jìn)行劃片切割;I、通過電鍍的方法依次形成銅層、鎳層和錫層。所述步驟B中形成的抗靜電層及焊盤的厚度為15~22μm。本發(fā)明的有益效果在于:采用成熟的半導(dǎo)體工藝技術(shù)和材料,在基板上制備出片式合金箔點(diǎn)火電阻器,通過選擇散熱系數(shù)更低的基板材料和熱隔離材料,實(shí)現(xiàn)了片式合金箔點(diǎn)火電阻器焦耳熱的更少散失,使得片式合金箔點(diǎn)火電阻器產(chǎn)生更多的用于加熱藥劑,從而提高了能量利用效率,有效降低了金箔點(diǎn)火電阻器的工作能量和點(diǎn)火時(shí)間。本發(fā)明的片式合金箔點(diǎn)火電阻器的點(diǎn)火電流1.5A,點(diǎn)火時(shí)間≤500μs,發(fā)火能量5毫焦,實(shí)現(xiàn)了小激發(fā)下快速發(fā)火;簡單可靠,大大提高了點(diǎn)火電阻器工作的可靠性及一致性;生產(chǎn)工藝簡單,具有靠性高、一致性好、質(zhì)量輕、發(fā)火能量高、可量產(chǎn)等。附圖說明圖1是本發(fā)明的結(jié)構(gòu)示意圖;圖2是圖1去除銅層、鎳層和錫層后的俯視圖;圖3是圖1中電阻層的結(jié)構(gòu)示意圖;圖中:1-基板,2-抗靜電層,3-聚酰亞胺膜,4-電阻層,41-橋絲,5-保護(hù)層,6-表背搭接層,7-銅層,8-鎳層,9-錫層,10-焊盤。具體實(shí)施方式下面進(jìn)一步描述本發(fā)明的技術(shù)方案,但要求保護(hù)的范圍并不局限于所述。如圖1和圖2所示的一種片式合金箔點(diǎn)火電阻器,包括基板1、抗靜電層2、聚酰亞胺膜3、電阻層4、保護(hù)層5、表背搭接層6、銅層7、鎳層8、錫層9和焊盤10;所述基板1的上表面中部設(shè)置有抗靜電層2,下表面的兩端分別設(shè)置有焊盤10;所述聚酰亞胺膜3設(shè)置在基板1和抗靜電層2的上表面上,所述聚酰亞胺膜3的上表面設(shè)置有電阻層4,且所述電阻層4的兩端分別通過表背搭接層6與焊盤10連接,所述電阻層4上還設(shè)置有保護(hù)層5;所述銅層7于保護(hù)層5的兩側(cè)設(shè)置在電阻層4上,且銅層7將表背搭接層6和焊盤10的外表面覆蓋,所述銅層7的外表面上還依次設(shè)置有鎳層8和錫層9。所述基板1為FR-4雙面覆銅玻纖板,F(xiàn)R-4雙面覆銅玻纖板具有較高的機(jī)械性能和介電性能,較好的耐熱性和耐潮性并有良好的機(jī)械加工性,可作為片式合金箔點(diǎn)火電阻器的基體材料,能有效降低熱量通過基板的散失,基板2外形尺寸為50mm×60mm,厚度為0.35mm~0.6mm。所述抗靜電層2和焊盤10的材料為Cu;所述抗靜電層2和焊盤10的厚度為0.018mm~0.03mm。所述抗靜電層2及焊盤10的材料為Cu,表面銅層目的是為了在電阻器遇到靜電情況時(shí),靜電產(chǎn)生的瞬間電流可通過,基板1上的銅層實(shí)際上就相當(dāng)于一個(gè)靜電釋放通道,背面銅層為焊盤10,作為焊接用的一個(gè)背電極,其厚度為0.018mm~0.03mm。所述聚酰亞胺膜3的厚度為0.025mm~0.04mm。設(shè)置聚酰亞胺膜3目的是將電阻層4緊密的貼合在抗靜電層2的表面上,并和抗靜電層2絕緣。所述電阻層4的材料為NiCr合金或Ni-80.Cr-20合金;所述電阻層4的厚度為0.0035mm~0.005mm。所述保護(hù)層5的材料為光敏性聚酰亞胺,保護(hù)層5的厚度為0.004mm~0.006mm。所述銅層8材料為硫酸銅,其厚度為4~12μm;所述鎳層9材料為鎳扣,其厚度為2~8μm;所述錫層10材料為純錫球,其厚度為3~14μm。所述表背搭接層6的材料為銀漿,厚度為0.2mm~0.4mm。一種如圖1和圖2所示的片式合金箔點(diǎn)火電阻器的制備方法,包括以下步驟:A、對基板1進(jìn)行清洗,去除表面的油污及雜質(zhì);B、通過光刻技術(shù)在基板1的上表面的中部形成抗靜電層2,并在基板1的下表面的兩端形成焊盤10;C、通過熱壓的方法將聚酰亞胺膜3貼在基板1和抗靜電層2的上表面;D、通過壓合的方法將電阻層4貼在聚酰亞胺膜3的上表面;E、采用濕法刻蝕技術(shù)對電阻層4進(jìn)行刻蝕加工出橋絲41,刻蝕后的電阻層4如圖3所示,刻蝕的深度為電阻層4的厚度;F、采用光刻技術(shù)在步驟E進(jìn)行刻蝕處理的部位上形成保護(hù)層5,且保護(hù)層5還覆蓋于電阻層4的橋絲41上,該保護(hù)層主要目的是保護(hù)橋絲(41);G、采用端面涂銀的技術(shù)在基板1的兩端形成表背搭接層6;H、根據(jù)產(chǎn)品尺寸要求,按常規(guī)方法對基片進(jìn)行劃片切割;I、通過電鍍的方法依次形成銅層8、鎳層9和錫層10。所述步驟B中形成的抗靜電層2及焊盤10的厚度為15~22μm。制備好的片式合金箔點(diǎn)火電阻器可直接用回流焊的方式焊接在點(diǎn)火頭上完成安裝。本發(fā)明采用成熟的半導(dǎo)體工藝技術(shù)和材料,在基板上制備出片式合金箔點(diǎn)火電阻器,通過選擇散熱系數(shù)更低的基板材料和熱隔離材料,實(shí)現(xiàn)了片式合金箔點(diǎn)火電阻器焦耳熱的更少散失,使得片式合金箔點(diǎn)火電阻器產(chǎn)生更多的用于加熱藥劑,從而提高了能量利用效率,有效降低了金箔點(diǎn)火電阻器的工作能量和點(diǎn)火時(shí)間。本發(fā)明的式合金箔點(diǎn)火電阻器的點(diǎn)火電流1.5A,點(diǎn)火時(shí)間≤500μs,發(fā)火能量5毫焦,實(shí)現(xiàn)了小激發(fā)下快速發(fā)火;本發(fā)明的點(diǎn)火電阻器能量高、重量輕、可靠性高。本發(fā)明采用貼片式的制備方法,方便了安裝而且可以適應(yīng)回流焊,加工技術(shù)簡單可靠,大大提高了點(diǎn)火電阻器工作的可靠性及一致性。