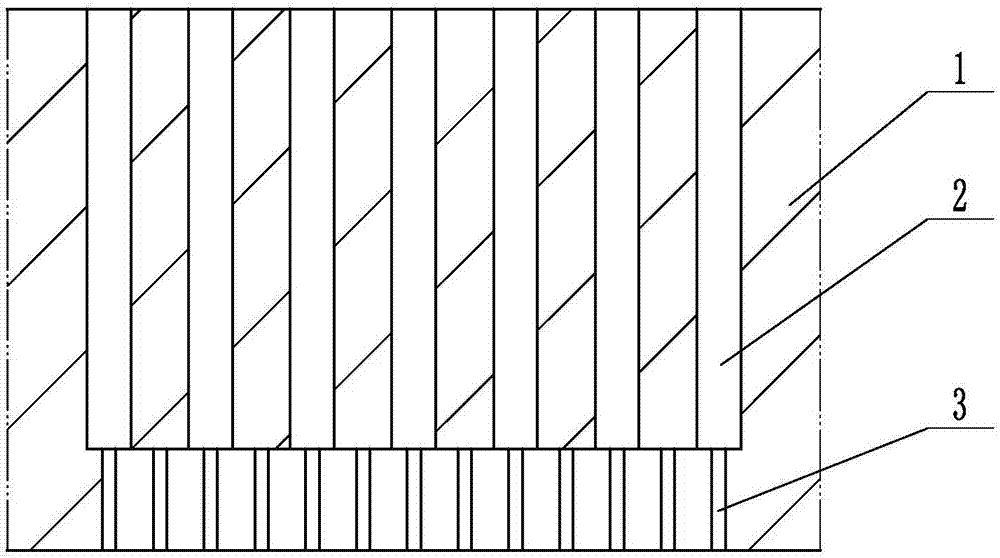
本發(fā)明涉及蜂窩陶瓷模具的制造技術(shù)領(lǐng)域,特別涉及薄壁大規(guī)格蜂窩陶瓷載體的制造方法。
背景技術(shù):已知的蜂窩陶模具都是由眾多進料孔和與之貫通的出料槽組成。薄壁大規(guī)格模具槽寬的寬度容易在使用過程中因泥料在槽中擠出磨損而變寬,當(dāng)槽寬超過規(guī)定值,擠出的大規(guī)格載體壁厚就超過標(biāo)準(zhǔn)值上限,該模具即為失效報廢;并且薄壁大載體擠出的泥料硬度比普通大載體要較硬,水分較低,從而才能保證薄壁大載體擠出時的泥坯有較好的保形性而避免了坯體成型時所產(chǎn)生的坯體整體變形、孔道和孔壁扭曲等缺陷。泥料水分低,硬度高,則擠出時泥料對出料槽內(nèi)表面的摩擦力會增大,槽寬更容易變寬,模具使用壽命降低;同時擠出的阻力會增大,模具所承受的壓力會增大,模具變形或開裂失效的風(fēng)險也將增大。因此薄壁大規(guī)格模具承受的負(fù)載壓力比普通壁厚大規(guī)格模具更大,在使用過程中更易變形和開裂,導(dǎo)致模具失效,無法生產(chǎn)或使用壽命很低。要實現(xiàn)模具主體具備足夠高的強度和抗疲勞性能,必須增加模具主體的厚度,即增加模具進料孔的深度。模具進料孔深度H需達到40-60mm。通常大規(guī)格載體模具主體采用兩件模板組合而成,如圖1所示,由一件主模1和一件副模10組合而成,其使用壽命只能達到1000米,使用壽命短。主模由貫通的眾多進料孔2和出料槽3組成,副模10僅有貫通的進料孔2。副模10的作用是增加模具的厚度,從而增加模具的強度和承壓能力,減少模具的變形和開裂失效風(fēng)險。如圖1所示,通常主模1的進料孔2深度是20-25mm,副模10的厚度為18-24mm。采用這種組合式的結(jié)構(gòu)是由于進料孔加工的限制,通常的進料孔加工采用的機床是雕刻機或加工中心等能實現(xiàn)鉆孔功能的數(shù)控機床,使用的刀具是麻花鉆,規(guī)格是直徑1.1-1.8,采用的工藝是垂直方向,啄孔加工的鉆孔方式。對于此類小深孔,鉆孔深度受到限制,一般最深不能超過25mm。如鉆孔深度過深,鉆頭長度必須加長,鉆頭剛度差,鉆削時鉆頭易斷。另外,孔深度過深,鉆削時排屑不暢,鉆頭時鉆頭易斷。此類小深孔,又是盲孔,如斷鉆頭,無法取出鉆頭而會導(dǎo)致模具報廢。同時由于進料孔是小而深的盲孔,不能采用鉸孔的方式對孔進行精加工。因此,用這種鉆削方式加工出來的孔的內(nèi)壁的粗糙度很差,只有Ra12.5-6.3。并且由于是垂直加工,必須采用啄孔方式來排屑,多次進刀多次退刀到模板表面以上來排屑,所以鉆孔效率較低。采用兩塊模板組合,不可避免存在定位偏差,增加擠出阻力。
技術(shù)實現(xiàn)要素:本申請人針對現(xiàn)有技術(shù)的上述缺點,進行研究和改進,提供一種可反復(fù)涂覆的薄壁大規(guī)格蜂窩陶瓷載體模具的制造方法,其制作高強度大規(guī)格載體模具,并對大規(guī)格模具進行循環(huán)涂覆,從而提高模具使用壽命。為了解決上述問題,本發(fā)明采用如下方案:一種可反復(fù)涂覆的薄壁大規(guī)格蜂窩陶瓷載體模具的制造方法,所述載體模具包括主模,主模上帶有多個進料孔及與進料孔相對應(yīng)的出料槽;所述載體模具的制造方法包括以下步驟:第一步:用模具鋼或其他合金鋼鋼材制作模板毛坯;第二步:編制進料孔鉆孔加工程序,再數(shù)控深孔鉆鉆孔;所述鉆孔加工程序包括一次鉆孔過程和兩次清底孔過程;所述一次鉆孔過程為:用普通槍鉆進行鉆孔,鉆孔深度比最終加工深度小0.3-0.5mm,鉆孔的孔底為W形;所述兩次清底孔過程包括第一清底孔及第二清底孔過程,第一次清底孔過程為:用特殊修磨的第一清孔槍鉆加工,鉆孔深度與鉆孔過程的深度相等,將W形孔底的中部凸起去除;第二次清底孔過程為:用特殊修磨的第二清孔槍鉆加工,將孔底加工成V形;第四步:編制線切割加工程序,在線切割機床上加工出料槽;第五步:在擠出機上預(yù)擠壓,對進料孔和出料槽內(nèi)表面進行研磨去毛刺和拋光;第六步:對所述載體模具的進料孔及出料槽的表面進行首次涂覆加工;第七步:利用涂覆后的所述載體模具進行第一次批量生產(chǎn)蜂窩陶瓷,擠出成型一定數(shù)量的陶瓷坯體后,再對所述載體模具的進料孔及出料槽進行第二次表面涂覆加工;第八步:利用第二次涂覆后的所述載體模具進行第二次批量生產(chǎn),生產(chǎn)一定數(shù)量的陶瓷坯體后,再次進行涂覆加工;如此重復(fù),進行3-6次循環(huán)的表面涂覆加工。作為上述技術(shù)方案的進一步改進:所述進料孔加工采用的機床是數(shù)控精密深孔鉆機床,所述清底孔過程使用的刀具為整體式硬質(zhì)合金槍鉆。所述進料孔的加工采用水平方向鉆孔及一次進刀的工藝。所述進料孔加工時,通過鉆套頂住模板,槍鉆進入所述鉆套后,再進行切削。所述普通槍鉆的主切削刃修磨到其直徑的1/4處,所述主切削刃的角度為40度;所述第一清孔槍鉆的主切削刃修磨到槍鉆直徑的1/2處,角度為30度;所述第二清孔槍鉆的主切削刃修磨到槍鉆直徑的1/2處,角度為40度。所述第一清孔槍鉆及第二清孔槍鉆的進刀量的設(shè)定范圍為10-20mm/min。所述出料槽使用中速走絲或低速走絲線切割機床加工。本發(fā)明的技術(shù)效果在于:本發(fā)明制作的模具為一體模具,其強度高,可進行反復(fù)表面涂覆,大大提高模具使用壽命。模具的進料孔可鉆到深度為60mm,進料孔的孔徑為1.1-1.8mm,完全消除了組合式模具的定位偏差的缺陷,減少了擠出阻力及模具所承受的壓力,減少了模具變形或開裂的風(fēng)險,提高模具使用壽命,使用壽命是原來的5-7倍,可生產(chǎn)5000-7000米。本發(fā)明中,進料孔的加工效率高、質(zhì)量好。附圖說明圖1為現(xiàn)有技術(shù)中陶瓷載體模具的結(jié)構(gòu)圖。圖2為本發(fā)明中陶瓷載體模具的結(jié)構(gòu)圖。圖3為本發(fā)明中模具進料孔的加工工藝圖。具體實施方式下面結(jié)合附圖對本發(fā)明的具體實施方式作進一步說明。如圖2所示,本實施例的可反復(fù)涂覆的薄壁大規(guī)格蜂窩陶瓷載體模具的制造方法,載體模具包括主模1,主模1上帶有多個進料孔2及與進料孔2相對應(yīng)的出料槽3;本發(fā)明的載體模具可用于生產(chǎn)孔密度100-600目,壁厚0.10-0.40mm,直徑190-330的薄壁大規(guī)格蜂窩陶瓷載體,并能夠承受15MPA-30MPA的壓力。載體模具的制造方法包括以下步驟:第一步:用模具鋼或其他合金鋼鋼材制作模板毛坯;第二步:編制進料孔鉆孔加工程序,再數(shù)控深孔鉆鉆孔;由于普通槍鉆4鉆出的孔的底部是W形結(jié)構(gòu),對于通常深孔加工通孔來講,這沒有任何影響。但是,蜂窩陶模具的進料孔2為盲孔,W形孔底結(jié)構(gòu)不利于泥料擠出,泥料容易在W底的兩個溝槽底部,形成死角,泥料擠出不流暢,擠出阻力加大。為解決上述問題,本發(fā)明的鉆孔加工程序包括一次鉆孔過程和兩次清底孔過程,如圖3所示,一次鉆孔過程為:用普通槍鉆4進行鉆孔,鉆孔深度比最終加工深度小0.3-0.5mm,鉆孔的孔底為W形;兩次清底孔過程包括第一清底孔及第二清底孔過程,第一次清底孔過程為:用特殊修磨的第一清孔槍鉆5加工,鉆孔深度與鉆孔過程的深度相等,將W形孔底的中部凸起去除;第二次清底孔過程為:用特殊修磨的第二清孔槍鉆6加工,將孔底加工成V形;第四步:編制線切割加工程序,在線切割機床上加工出料槽3;第五步:在擠出機上預(yù)擠壓,對進料孔2和出料槽3內(nèi)表面進行研磨去毛刺和拋光;第六步:對載體模具的進料孔2及出料槽3的表面進行首次涂覆加工;第七步:利用涂覆后的載體模具進行第一次批量生產(chǎn)蜂窩陶瓷,擠出成型一定數(shù)量的陶瓷坯體后,再對載體模具的進料孔2及出料槽3進行第二次表面涂覆加工;第八步:利用第二次涂覆后的載體模具進行第二次批量生產(chǎn),生產(chǎn)一定數(shù)量的陶瓷坯體后,再次進行涂覆加工;如此重復(fù),進行3-6次循環(huán)的表面涂覆加工。本發(fā)明中,如圖2所示,主模的進料孔2可鉆到深度為60mm,進料孔2的孔徑為1.1-1.8mm,完全消除了組合式模具的定位偏差的缺陷,減少了擠出阻力,減少了模具所承受的壓力,減少了模具變形或開裂的風(fēng)險,提高了模具使用壽命,使用壽命是原來的5-7倍,可生產(chǎn)5000-7000米。本發(fā)明中,進料孔2加工采用的機床是數(shù)控精密深孔鉆機床,清底孔過程使用的刀具為整體式硬質(zhì)合金槍鉆。進料孔2采用水平方向鉆孔及一次進刀的工藝,無需通過退刀來排屑。槍鉆為中空結(jié)構(gòu),其中心帶有通孔,高壓油從通孔中心噴出,將鐵屑沿排屑槽沖掉。鉆孔時,通過鉆套頂住模板,槍鉆進入鉆套后,再進行切削,其定心效果好,鉆出的深孔垂直度偏差可在0.005mm以內(nèi)。由于槍鉆鉆削方式是擠壓式切削,光潔度比傳統(tǒng)的麻花鉆切削提高很多,能達到Ra0.8;并且,一次進刀,無需退刀,比麻花鉆切削效率提高了20%。由于孔內(nèi)壁的光潔度從6.3提高到0.8,模具的擠出阻力可降低30%-50%,即擠出壓力可降低30%-50%。為提高鉆孔效率和進料孔2的加工質(zhì)量,如圖3所示,本發(fā)明中的普通槍鉆4的主切削刃修磨到其直徑的1/4處,主切削刃的角度為40度;第一清孔槍鉆5的主切削刃修磨到槍鉆直徑的1/2處,角度為30度;第二清孔槍鉆6的主切削刃修磨到槍鉆直徑的1/2處,角度為40度。由于這種經(jīng)過特殊修磨,主切削刃修磨到槍鉆1/2的槍鉆,極易斷刀或崩刀,本發(fā)明采用了專門的加工工藝,分兩次進行底孔成形加工,進刀量也設(shè)定在合理范圍,在10-20mm/min之間。這樣有效避免了斷刀和崩刀。出料槽3使用中速走絲或低速走絲線切割機床加工。低速走絲線切割機床為優(yōu)先選用方案,可以得到更好更低的槽內(nèi)壁粗糙度,即更光滑的槽內(nèi)壁表面。以上所舉實施例為本發(fā)明的較佳實施方式,僅用來方便說明本發(fā)明,并非對本發(fā)明作任何形式上的限制,任何所屬技術(shù)領(lǐng)域中具有通常知識者,若在不脫離本發(fā)明所提技術(shù)特征的范圍內(nèi),利用本發(fā)明所揭示技術(shù)內(nèi)容所作出局部改動或修飾的等效實施例,并且未脫離本發(fā)明的技術(shù)特征內(nèi)容,均仍屬于本發(fā)明技術(shù)特征的范圍內(nèi)。