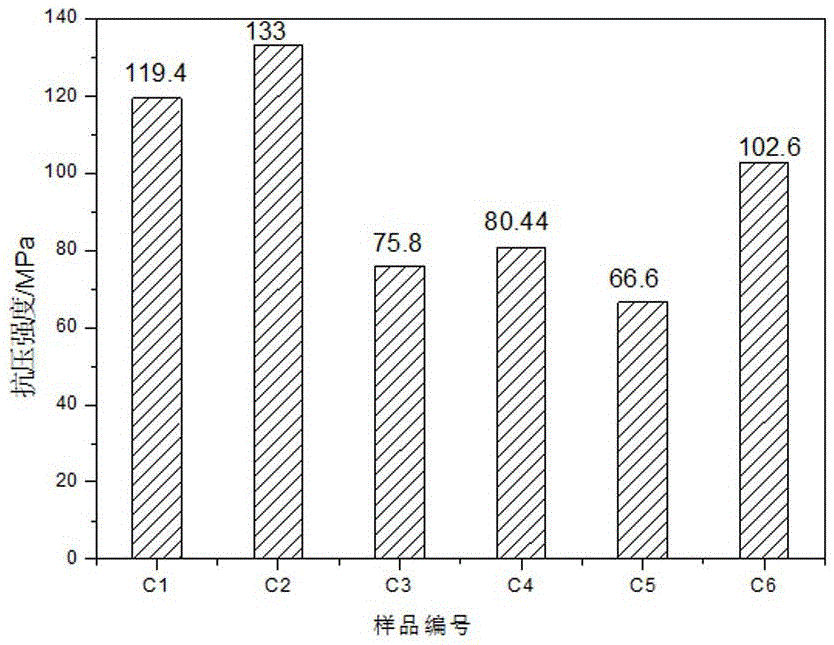
本發(fā)明涉及一種新型建筑材料,特別是一種綜合利用工業(yè)副產(chǎn)石膏與鋁硅酸鹽類工業(yè)廢渣耦合制造建筑材料的方法。
背景技術(shù):
:氟石膏是氫氟酸生產(chǎn)過程中的副產(chǎn)品,由硫酸與螢石反應(yīng)產(chǎn)出的以含硫酸鈣為主的廢渣,主要產(chǎn)自無機(jī)氟化物和有機(jī)氟化物生產(chǎn)廠及其他氫氟酸生產(chǎn)廠,產(chǎn)量相當(dāng)可觀,每生產(chǎn)lt氫氟酸約產(chǎn)氟石膏4t以上,每年我國氟化鹽廠排出的氟石膏量達(dá)100多萬噸。剛出裝置時氟石膏中含有殘余的螢石與硫酸,其中氟及硫酸含量較高,都超過危險廢物鑒別標(biāo)準(zhǔn)所規(guī)定的限值,屬腐蝕性強(qiáng)的有害固體廢棄物,對植物、動物和人都具有極大的副作用。其活性小,不能單獨(dú)作為一種膠凝材料使用,大部分在稍加中和處理后就作為一般固體廢棄物堆存,直接堆存不僅占用土地,還污染土壤和地下水環(huán)境。因此,處理和利用氟石膏,對生態(tài)環(huán)境具有十分重要的意義。由于生產(chǎn)氟化氫所用的原料酸級螢石純度很高,反應(yīng)過程處于無水狀態(tài),所副產(chǎn)的氟石膏為無水石膏,其中CaSO4含量很高達(dá)95%以上,氟石膏晶體顆粒表面光滑,其中細(xì)小顆粒較多,呈粒狀或球狀。其屬于二型無水石膏的一個變體,具有水化生成二水石膏的能力,但無水氟石膏酸性強(qiáng)、水化活性低,水化速度小。利用氟石膏開發(fā)生產(chǎn)出了石膏磚和石膏彩磚。由于氟石膏本身的一些特性對石膏磚的體積穩(wěn)定性和強(qiáng)度造成了一定的影響。如彩磚的抗壓強(qiáng)度僅為15MPa,低于20MPa的國家建材標(biāo)準(zhǔn)要求。這些質(zhì)量缺陷的存在,極大地限制了其市場的推廣。鈦石膏是采用硫酸酸解鈦鐵礦生產(chǎn)鈦白粉時,加入石灰或電石渣中和大量的酸性廢水所產(chǎn)生的以二水石膏為主要成分的廢渣。其處理過程是先用石灰石中和至PH為7。然后加入絮凝劑在增稠器中沉降,清液合理溢流排放。下層濃漿通過壓濾機(jī)壓濾.壓濾后的濾渣即為鈦石膏,每生產(chǎn)1噸鈦白粉副產(chǎn)10噸鈦石膏。全世界每年鈦石膏的排放量為1775萬噸;我國每年約為715萬噸。鈦石膏含水量高、粘度大、雜質(zhì)含量高,呈弱酸性,從廢渣處理車間出來時。先是灰褐色。置于空氣中二價鐵離子逐漸被氧化成三價鐵離子而變成紅色(偏黃),故又名紅泥,紅、黃石膏??捎渺褵拟伿唷⒎勖夯?、礦渣、硅酸鹽水泥、激發(fā)劑配制復(fù)合膠結(jié)材料,或鈦石膏烘干后用做水泥緩凝劑,以高鈣灰與鈦石膏復(fù)合制作路基材料等。值得注意的是。和天然石膏相比,鈦石膏中的鐵含量較高。因此.鈦石膏具有黏度大、置于空氣中易變成紅色等特點(diǎn).這給鈦石膏的處理工藝帶來一定困難。鹽石膏在海水制鹽過程中排放的固體廢渣通常稱為鹽石膏。氯化鈉NaCl是化學(xué)工業(yè)的重要原料,鹽場用海水曬鹽制造的過程中需產(chǎn)生大量的固體廢渣鹽石膏(俗稱硝皮)。每生產(chǎn)20噸原鹽大約產(chǎn)生1噸鹽石膏。鹽石膏外觀呈灰黃色,主要成分是二水硫酸鈣,多為柱狀結(jié)晶體,并含有少量Mg2+、Al3+、Fe3+等無機(jī)鹽類和大量泥沙。因摻有大量雜質(zhì)以廢棄物形式堆放填埋,不但占用土地污染環(huán)境,還給鹽場再擴(kuò)建帶來一定的困難,如何將大量廢渣處理再利用是企業(yè)亟待解決的問題。檸檬酸石膏是食品化工業(yè)采用石灰法制取檸檬酸時的一種化學(xué)沉積物,渣量與產(chǎn)品量基本相當(dāng),因此產(chǎn)生的工業(yè)廢渣較多。我國檸檬酸年產(chǎn)量達(dá)70余萬噸,檸檬酸石膏排放量達(dá)105萬噸,占全世界排放總量的63%左右。檸檬酸石膏細(xì)度大(4900孔篩篩余為25%~40%),三氧化硫含量高達(dá)45%以上,R2O等有害成分較少。檸檬酸石膏的礦物組成主要為二水硫酸鈣,含量達(dá)90%以上,根據(jù)其礦物組成分析可以替代天然二水石膏。但其含水量大,可達(dá)30%~40%且含有一定的殘余酸和有機(jī)物(菌絲體),使其凝結(jié)時間變長,利用困難。以上所述的工業(yè)副產(chǎn)石膏都是在工業(yè)生產(chǎn)中產(chǎn)生的以硫酸鈣為主要成分的工業(yè)廢料,堆放這些廢料不僅占用大量土地,而且污染環(huán)境和地下水資源。應(yīng)用于建筑材料又存在性能差的缺點(diǎn)。技術(shù)實(shí)現(xiàn)要素:本發(fā)明要解決的技術(shù)問題是提供一種利用工業(yè)副產(chǎn)石膏制備建筑材料的方法,至少克服現(xiàn)有石膏類產(chǎn)品強(qiáng)度低、耐久性差的缺點(diǎn)。為解決以上技術(shù)問題,本發(fā)明采用的技術(shù)方案是:一種利用工業(yè)副產(chǎn)石膏制備建筑材料的方法,包括步驟:S1:以質(zhì)量百分比計的如下原料制成干混料,工業(yè)副產(chǎn)石膏15%~65%,鋁硅酸鹽類工業(yè)廢渣10%~60%,集料22%~35%,鈣質(zhì)膠凝材料3%~12%;S2:向步驟S1制得的干混料加入水或溶入了激發(fā)劑的水溶液濕混制得濕混料,其中水占全部固體物料干基質(zhì)量的12%~20%,激發(fā)劑為鋁硅酸鹽類工業(yè)廢渣干基質(zhì)量的0.2%~1.5%;S3:將濕混料進(jìn)行靜置,靜置時間為15min~2h;S4:將經(jīng)步驟S3處理的物料進(jìn)行靜壓成型得到坯體,成型壓力為20MPa~50MPa,保壓時間為15s~1min;S5:將步驟S4制得的坯體進(jìn)行自然養(yǎng)護(hù)28天或經(jīng)靜停0.5h~3h后蒸汽養(yǎng)護(hù)3h~24h,制得所述材料,其中蒸汽養(yǎng)護(hù)溫度為70℃~100℃。作為優(yōu)選的技術(shù)方案,所述的工業(yè)副產(chǎn)石膏是以硫酸鈣礦物為主要成分的工業(yè)廢渣。作為優(yōu)選的技術(shù)方案,所述的工業(yè)副產(chǎn)石膏為氟石膏、鈦石膏、鹽石膏、檸檬酸石膏中的一種或幾種的組合。所述的鋁硅酸鹽類工業(yè)廢渣優(yōu)選自礦渣、水淬礦渣、粉煤灰、鋁鋅渣、磷渣中的一種或幾種的組合。作為優(yōu)選的技術(shù)方案,所述的鈣質(zhì)膠凝材料是以氧化鈣、硅酸鈣或鋁酸鈣為主要礦物的材料。作為優(yōu)選的技術(shù)方案,鈣質(zhì)膠凝材料是指石灰、電石渣、水泥熟料和水泥中的一種或多種的組合。作為優(yōu)選的技術(shù)方案,所述的集料是粒徑在0.1~10mm的河砂、機(jī)制砂、水淬鎳鐵渣顆粒、礦渣顆粒、爐渣顆粒、建筑垃圾再生細(xì)集料、各種尾礦中的一種或幾種的組合。作為優(yōu)選的技術(shù)方案,工業(yè)副產(chǎn)石膏、鋁硅酸鹽類工業(yè)廢渣和鈣質(zhì)膠凝材料采用單獨(dú)粉磨后混合或者混合后粉磨的方式處理,制得混合粉體,控制混合粉體的比表面積在400m2/kg~800m2/kg。作為優(yōu)選的技術(shù)方案,混合粉體與集料按比例混合3~5min制得所述的干混料。作為優(yōu)選的技術(shù)方案,干混料加入水或溶入了激發(fā)劑的水混合3~10min制得濕混料。本發(fā)明利用工業(yè)副產(chǎn)石膏與鋁硅酸鹽類工業(yè)廢渣耦合制備超高強(qiáng)材料的機(jī)理:(1)根據(jù)材料最緊密堆積原理和水化活性增強(qiáng)原理設(shè)計粉體材料(工業(yè)副產(chǎn)石膏、鋁硅酸鹽類工業(yè)廢渣、鈣質(zhì)膠凝材料)與集料最佳配比范圍,與水混合后在較高壓力下(以集料抗壓強(qiáng)度為限)靜壓模壓成型,獲得致密坯體。(2)經(jīng)過細(xì)磨的工業(yè)副產(chǎn)石膏在致密坯體孔隙液中發(fā)生溶解和再結(jié)晶反應(yīng),受到致密坯體孔隙大小和相貌的影響,生成數(shù)量巨大的納米石膏晶須(見圖1),穿插在孔隙中和鋁硅酸鹽礦物的水化產(chǎn)物中,起到了進(jìn)一步增加致密度和纖維增強(qiáng)作用,極大程度提高了材料強(qiáng)度。(3)石膏中的硫酸根離子、鈣離子與冶金礦渣、硅鋁質(zhì)輔助膠凝材料水化產(chǎn)物反應(yīng)生成鈣礬石,既提高了坯體致密度,提高材料強(qiáng)度,又提高了材料的耐水性。(4)冶金礦渣水化產(chǎn)物在堿激發(fā)劑作用下還與硫酸根離子(或石膏)反應(yīng)生成水合硫酸方柱石,如:(CaO,xNa2O)[ySiO2·zAl2O3]SO3·nH2O)(見圖2),使得礦渣水化產(chǎn)物與石膏晶體或晶須表面薄弱結(jié)合區(qū)減少,提高了材料的強(qiáng)度和耐水性。本發(fā)明與現(xiàn)有方法相比,具有如下有益效果:(1)強(qiáng)度高,各種冶金礦渣的強(qiáng)度如表1所示,是現(xiàn)有常規(guī)方法制備的石膏基材料強(qiáng)度(10~30MPa)或鋁硅酸鹽類工業(yè)廢渣基材料(10~40MPa)的數(shù)倍,甚至十多倍,實(shí)現(xiàn)了此類材料強(qiáng)度突破;表1工業(yè)副產(chǎn)石膏種類氟石膏鈦石膏鹽石膏檸檬酸石膏強(qiáng)度(單位:MPa)60~15060~18060~15060~200(2)耐水性好,克服了石膏制品耐水性差的致命缺陷;(3)生產(chǎn)工藝簡單,可以通過對現(xiàn)有粉煤灰免燒磚生產(chǎn)線進(jìn)行簡單改造即可實(shí)現(xiàn)規(guī)模化生產(chǎn);(4)產(chǎn)品品種調(diào)節(jié)容易,以實(shí)現(xiàn)功能化。利用本發(fā)明的技術(shù),可通過變化成型模具方法制備高強(qiáng)建筑磚、高強(qiáng)道路磚、高強(qiáng)透水磚、路沿石、各種裝飾板材等各種高強(qiáng)、高耐久性產(chǎn)品;(5)本發(fā)明的實(shí)施屬于工業(yè)固廢資源化利用采用本發(fā)明的技術(shù)方案,對工業(yè)副產(chǎn)石膏等固體廢棄物的利用率可達(dá)90%以上,因此,它可以提高固體廢棄物的附加值,真正地實(shí)現(xiàn)變廢為寶。附圖說明圖1為水化產(chǎn)物特征(晶須增強(qiáng))。圖2為實(shí)施例1-4材料的強(qiáng)度。圖3為實(shí)施例5-8材料的強(qiáng)度。圖4為實(shí)施例9-12材料的強(qiáng)度。圖5為實(shí)施例13-16材料的強(qiáng)度。具體實(shí)施方式為了使本領(lǐng)域技術(shù)人員更好的理解本發(fā)明,以下結(jié)合實(shí)施例對本發(fā)明作進(jìn)一步清楚、完整的說明。需要說明的是,在不沖突的情況下,本申請中的實(shí)施例及實(shí)施例中的特征可以相互組合。實(shí)施例1將比表面積600m2/kg氟石膏400g(40%)、比表面積600m2/kg礦渣300g(30%)、比表面積780m2/kgP·O42.5水泥50g(5%)和細(xì)度模數(shù)為2.8的河砂250g(25%)在混合機(jī)中干混3min;然后加入180g水(全部固體物料干基質(zhì)量的18%),水中額外加入1.5g堿性激發(fā)劑(占礦渣粉的0.5%),濕混10min;靜置15min后在40MPa下保壓30s,制得超強(qiáng)材料坯體;在混凝土養(yǎng)護(hù)室內(nèi)常溫飽水養(yǎng)護(hù)28天得超高強(qiáng)材料C1,經(jīng)靜停1h后在100℃下飽和蒸汽養(yǎng)護(hù)9h,制得超高強(qiáng)材料C2,抗壓強(qiáng)度見圖2。實(shí)施例2將氟石膏2500g、磷渣2500g放入500×500mm標(biāo)準(zhǔn)球磨機(jī)粉磨50min,制得比表面積650m2/kg的混合料,取620g混合料(其中干氟石膏占總干基物料的31%,磷渣占總干基物料的31%),與比表面積480m2/kgP·O42.5水泥80g(占總干基物料的8%)和細(xì)度模數(shù)為2.8的河砂300g(占總干基物料的30%)在混合機(jī)中干混4min;然后加入180g的水(加上石膏帶入的水占總干基物料的18%),水中額外加入1.8g堿性激發(fā)劑(占CFB粉的0.6%),濕混8min;靜置30min后在45MPa下保壓15s,制得超強(qiáng)材料坯體;在實(shí)驗(yàn)室(溫度20℃~31℃)常溫飽水養(yǎng)護(hù)28天得超高強(qiáng)材料C3,經(jīng)靜停1h后在75℃下飽和蒸汽養(yǎng)護(hù)12h,制得超高強(qiáng)材料C4,抗壓強(qiáng)度見圖2。實(shí)施例3將氟石膏2800g、水淬礦渣2200g放入500×500mm標(biāo)準(zhǔn)球磨機(jī)粉磨65min,制得比表面積580m2/kg的混合料,取670g混合料(其中氟石膏占總干基物料的37.5%,水淬礦渣占總干基物料的29.5%),與比表面積600m2/kgP·O42.5水泥90g(占總干基物料的9%)和細(xì)度模數(shù)為3.2的機(jī)制砂240g(占總干基物料的24%)在混合機(jī)中干混3min;然后加入200g的水(加上石膏帶入的水占總干基物料的20%),水中額外加入1.4g堿性激發(fā)劑(占水淬礦渣粉的0.47%),濕混9min;靜置30min后在45MPa下保壓50s,制得超強(qiáng)材料坯體;經(jīng)靜停3h后在90℃下飽和蒸汽養(yǎng)護(hù)6h,制得超高強(qiáng)材料C5,抗壓強(qiáng)度見圖2。實(shí)施例4將氟石膏2400g、粉煤灰2200g和石灰400g放入500×500mm標(biāo)準(zhǔn)球磨機(jī)粉磨60min,制得比表面積532m2/kg的混合料,取700g混合料(其中粉煤灰占總干基物料的30.8%、干氟石膏占總干基物料的33.6%、石灰占總干基物料的5.6%),和細(xì)度模數(shù)為2.8的砂漿再生集料300g(占總干基物料的30%)在混合機(jī)中干混3min;然后加入190g的水(占總干基物料的19%),濕混7min;靜置30min后在43MPa下保壓45s,制得超強(qiáng)材料坯體;經(jīng)靜停2h后在90℃下飽和蒸汽養(yǎng)護(hù)6h,制得超高強(qiáng)材料C6,抗壓強(qiáng)度見圖2。實(shí)施例5將比表面積450m2/kg鈦石膏400g(40%)、比表面積600m2/kg水淬礦渣粉300g(30%)、比表面積380m2/kgP·O42.5水泥50g(5%)和細(xì)度模數(shù)為2.8的河砂250g(25%)在混合機(jī)中干混3min;然后加入180g水(全部固體物料干基質(zhì)量的18%),水中額外加入1.5g堿性激發(fā)劑(占礦渣粉的0.5%),濕混10min;靜置15min后在40MPa下保壓30s,制得超強(qiáng)材料坯體;在混凝土養(yǎng)護(hù)室內(nèi)自然養(yǎng)護(hù)28天得超高強(qiáng)材料F1,經(jīng)靜停1h后在100℃下飽和蒸汽養(yǎng)護(hù)9h,制得超高強(qiáng)材料F2,抗壓強(qiáng)度見圖3。實(shí)施例6將烘干鈦石膏2500g、干磷渣2500g放入500×500mm標(biāo)準(zhǔn)球磨機(jī)粉磨50min,制得比表面積583m2/kg的混合料,取620g混合料(其中鈦石膏占總干基物料的31%,磷渣占總干基物料的31%),與比表面積380m2/kgP·O42.5水泥80g(占總干基物料的8%)和細(xì)度模數(shù)為2.8的河砂300g(占總干基物料的30%)在混合機(jī)中干混4min;然后加入180g的水(加上石膏帶入的水占總干基物料的18%),水中額外加入1.8g堿性激發(fā)劑(占CFB粉的0.6%),濕混8min;靜置30min后在45MPa下保壓15s,制得超強(qiáng)材料坯體;在實(shí)驗(yàn)室(溫度20℃~31℃)自然養(yǎng)護(hù)28天得超高強(qiáng)材料F3,經(jīng)靜停1h后在75℃下飽和蒸汽養(yǎng)護(hù)12h,制得超高強(qiáng)材料F4,抗壓強(qiáng)度見圖3。實(shí)施例7將烘干鈦石膏2400g、水淬礦渣2400g放入500×500mm標(biāo)準(zhǔn)球磨機(jī)粉磨65min,制得比表面積611m2/kg的混合料,取670g混合料(其中鈦石膏占總干基物料的33.5%,水淬礦渣占總干基物料的33.5%),與比表面積380m2/kgP·O42.5水泥90g(占總干基物料的9%)和細(xì)度模數(shù)為3.2的機(jī)制砂240g(占總干基物料的24%)在混合機(jī)中干混3min;然后加入200g的水(加上石膏帶入的水占總干基物料的20%),水中額外加入1.4g堿性激發(fā)劑(占水淬礦渣粉的0.47%),濕混9min;靜置30min后在45MPa下保壓50s,制得超強(qiáng)材料坯體;經(jīng)靜停3h后在90℃下飽和蒸汽養(yǎng)護(hù)6h,制得超高強(qiáng)材料F5,抗壓強(qiáng)度見圖3。實(shí)施例8將烘干鈦石膏2200g、粉煤灰2400g和石灰400g放入500×500mm標(biāo)準(zhǔn)球磨機(jī)粉磨60min,制得比表面積586m2/kg的混合料,取700g混合料(其中粉煤灰占總干基物料的33.6%、鈦石膏占總干基物料的30.8%、石灰占總干基物料的5.6%),和細(xì)度模數(shù)為2.8的砂漿再生集料300g(占總干基物料的30%)在混合機(jī)中干混3min;然后加入190g的水(占總干基物料的19%),濕混7min;靜置30min后在43MPa下保壓45s,制得超強(qiáng)材料坯體;經(jīng)靜停2h后在90℃下飽和蒸汽養(yǎng)護(hù)6h,制得超高強(qiáng)材料F6,抗壓強(qiáng)度見圖3。實(shí)施例9將比表面積400m2/kg鹽石膏400g(40%)、比表面積600m2/kg水淬礦渣粉300g(30%)、比表面積380m2/kgP·O42.5水泥50g(5%)和細(xì)度模數(shù)為2.8的河砂250g(25%)在混合機(jī)中干混3min;然后加入180g水(全部固體物料干基質(zhì)量的18%),水中額外加入1.5g堿性激發(fā)劑(占水淬礦渣粉的0.5%),濕混10min;靜置15min后在40MPa下保壓30s,制得超強(qiáng)材料坯體;在混凝土養(yǎng)護(hù)室內(nèi)自然養(yǎng)護(hù)28天得超高強(qiáng)材料E1,經(jīng)靜停1h后在100℃下飽和蒸汽養(yǎng)護(hù)9h,制得超高強(qiáng)材料E2,抗壓強(qiáng)度見圖4。實(shí)施例10將鹽石膏2500g、干磷渣(CFB)2500g放入500×500mm標(biāo)準(zhǔn)球磨機(jī)粉磨50min,制得比表面積564m2/kg的混合料,取620g混合料(其中鹽石膏占總干基物料的31%,磷渣占總干基物料的31%),與比表面積380m2/kgP·O42.5水泥80g(占總干基物料的8%)和細(xì)度模數(shù)為2.8的河砂300g(占總干基物料的30%)在混合機(jī)中干混4min;然后加入180g的水(加上石膏帶入的水占總干基物料的18%),水中額外加入1.8g堿性激發(fā)劑(占CFB粉的0.6%),濕混8min;靜置30min后在45MPa下保壓15s,制得超強(qiáng)材料坯體;在實(shí)驗(yàn)室(溫度20℃~31℃)自然養(yǎng)護(hù)28天得超高強(qiáng)材料E3,經(jīng)靜停1h后在75℃下飽和蒸汽養(yǎng)護(hù)12h,制得超高強(qiáng)材料E4,抗壓強(qiáng)度見圖4。實(shí)施例11將鹽石膏2800g、水淬礦渣2200g放入500×500mm標(biāo)準(zhǔn)球磨機(jī)粉磨65min,制得比表面積608m2/kg的混合料,取670g混合料(其中鹽石膏占總干基物料的37.5%,水淬礦渣占總干基物料的29.5%),與比表面積380m2/kgP·O42.5水泥90g(占總干基物料的9%)和細(xì)度模數(shù)為3.2的機(jī)制砂240g(占總干基物料的24%)在混合機(jī)中干混3min;然后加入200g的水(加上石膏帶入的水占總干基物料的20%),水中額外加入1.4g堿性激發(fā)劑(占水淬礦渣粉的0.47%),濕混9min;靜置30min后在45MPa下保壓50s,制得超強(qiáng)材料坯體;經(jīng)靜停3h后在90℃下飽和蒸汽養(yǎng)護(hù)6h,制得超高強(qiáng)材料E5,抗壓強(qiáng)度見圖4。實(shí)施例12將鹽石膏2400g、粉煤灰2200g和石灰400g放入500×500mm標(biāo)準(zhǔn)球磨機(jī)粉磨60min,制得比表面積532m2/kg的混合料,取700g混合料(其中粉煤灰占總干基物料的30.8%、鹽石膏占總干基物料的33.6%、石灰占總干基物料的5.6%),和細(xì)度模數(shù)為2.8的砂漿再生集料300g(占總干基物料的30%)在混合機(jī)中干混3min;然后加入190g的水(占總干基物料的19%),濕混7min;靜置30min后在43MPa下保壓45s,制得超強(qiáng)材料坯體;經(jīng)靜停2h后在90℃下飽和蒸汽養(yǎng)護(hù)6h,制得超高強(qiáng)材料E6,抗壓強(qiáng)度見圖4。實(shí)施例13將比表面積489m2/kg檸檬酸石膏400g(40%)、比表面積600m2/kg礦渣300g(30%)、比表面積380m2/kgP·O42.5水泥50g(5%)和細(xì)度模數(shù)為2.4的河砂250g(25%)在混合機(jī)中干混3min;然后加入150g水(全部固體物料干基質(zhì)量的15%),水中額外加入1.5g堿性激發(fā)劑(占礦渣粉的0.5%),濕混10min;靜置15min后在40MPa下保壓30s,制得超強(qiáng)材料坯體;在混凝土養(yǎng)護(hù)室內(nèi)自然養(yǎng)護(hù)28天得超高強(qiáng)材料D1,經(jīng)靜停1h后在80℃下飽和蒸汽養(yǎng)護(hù)9h,制得超高強(qiáng)材料D2,抗壓強(qiáng)度見圖5。實(shí)施例14將含水率10%檸檬酸石膏2500g、干磷渣2500g放入500×500mm標(biāo)準(zhǔn)球磨機(jī)粉磨55min,制得比表面積601m2/kg的混合料,取620g混合料(其中干檸檬酸石膏占總干基物料的28.8%,磷渣占總干基物料的32%),與比表面積380m2/kgP·O42.5水泥60g(占總干基物料的6.2%)和細(xì)度模數(shù)為2.4的河砂320g(占總干基物料的33%)在混合機(jī)中干混4min;然后加入150g的水(加上石膏帶入的水占總干基物料的18.7%),水中額外加入1.8g堿性激發(fā)劑(占CFB粉的0.6%),濕混8min;靜置30min后在45MPa下保壓15s,制得超強(qiáng)材料坯體;在實(shí)驗(yàn)室(溫度20℃~31℃,相對濕度67%~83%)自然養(yǎng)護(hù)28天得超高強(qiáng)材料D3,經(jīng)靜停1h后在75℃下飽和蒸汽養(yǎng)護(hù)12h,制得超高強(qiáng)材料D4,抗壓強(qiáng)度見圖5。實(shí)施例15將含水率7%檸檬酸石膏2800g、水淬礦渣2200g放入500×500mm標(biāo)準(zhǔn)球磨機(jī)粉磨54min,制得比表面積590m2/kg的混合料,取670g混合料(其中干檸檬酸石膏占總干基物料的35.8%,水淬礦渣占總干基物料的30.3%),與比表面積380m2/kgP·O42.5水泥90g(占總干基物料的9.2%)和細(xì)度模數(shù)為3.2的機(jī)制砂240g(占總干基物料的24.6%)在混合機(jī)中干混3min;然后加入140g的水(加上石膏帶入的水占總干基物料的16.6%),水中額外加入1.4g堿性激發(fā)劑(占水淬礦渣粉的0.47%),濕混9min;靜置30min后在45MPa下保壓50s,制得超強(qiáng)材料坯體;經(jīng)靜停3h后在90℃下飽和蒸汽養(yǎng)護(hù)6h,制得超高強(qiáng)材料D5,抗壓強(qiáng)度見圖5。實(shí)施例16將含水率0%檸檬酸石膏2300g、粉煤灰2200g和石灰500g放入500×500mm標(biāo)準(zhǔn)球磨機(jī)粉磨60min,制得比表面積512m2/kg的混合料,取700g混合料(其中粉煤灰占總干基物料的30.8%、干檸檬酸石膏占總干基物料的32.3%、石灰占總干基物料的7%),和細(xì)度模數(shù)為2.8的砂漿再生集料300g(占總干基物料的30%)在混合機(jī)中干混3min;然后加入150g的水(占總干基物料的15%),濕混7min;靜置30min后在43MPa下保壓45s,制得超強(qiáng)材料坯體;經(jīng)靜停2h后在90℃下飽和蒸汽養(yǎng)護(hù)6h,制得超高強(qiáng)材料D6,抗壓強(qiáng)度見圖5。實(shí)施例17將鈦石膏3900g、粉煤灰600g放入500×500mm標(biāo)準(zhǔn)球磨機(jī)粉磨67min,制得比表面積400m2/kg的混合料,取750g混合料(其中鈦石膏占總干基物料的65%,粉煤灰占總干基物料的10%),與比表面積800m2/kgP·O42.5電石渣30g(占總干基物料的3%)和細(xì)度模數(shù)為3.2的爐渣顆粒220g(占總干基物料的22%)在混合機(jī)中干混5min;然后加入120g的水(占總干基物料的12%),水中額外加入0.2g堿性激發(fā)劑(占粉煤灰的0.2%),濕混3min;靜置2h后在20MPa下保壓1min,制得坯體;經(jīng)靜停0.5h后在70℃下飽和蒸汽養(yǎng)護(hù)3h,制得超高強(qiáng)材料F7。實(shí)施例18將鹽石膏900g、磷渣3600g放入500×500mm標(biāo)準(zhǔn)球磨機(jī)粉磨58min,制得比表面積624m2/kg的混合料,取750g混合料(其中鹽石膏占總干基物料的15%,磷渣占總干基物料的60%),與比表面積380m2/kgP·O42.5水泥30g(占總干基物料的3%)和細(xì)度模數(shù)為2.4的河砂100g和機(jī)制砂120g(總共占總干基物料的22%)在混合機(jī)中干混5min;然后加入150g的水(占總干基物料的15%),水中額外加入9.0g堿性激發(fā)劑(占磷渣的1.5%),濕混10min;靜置30min后在50MPa下保壓15s,制得坯體;在實(shí)驗(yàn)室(溫度20℃~31℃,相對濕度67%~83%)自然養(yǎng)護(hù)28天得超高強(qiáng)材料F8,經(jīng)靜停2h后在100℃下飽和蒸汽養(yǎng)護(hù)24h,制得超高強(qiáng)材料F9。實(shí)施例19將氟石膏1500g、磷渣1000g和水淬鎳鐵渣680g放入500×500mm標(biāo)準(zhǔn)球磨機(jī)粉磨58min,制得比表面積624m2/kg的混合料,取530g混合料(其中氟石膏占總干基物料的25%,磷渣和水淬鎳鐵渣占總干基物料的28%),與比表面積380m2/kgP·O42.5水泥100g和石灰20g(總共占總干基物料的12%)和細(xì)度模數(shù)為2.4的河砂350g(占總干基物料的35%)在混合機(jī)中干混4min;然后加入180g的水(占總干基物料的18%),水中額外加入2.8g堿性激發(fā)劑(占磷渣和水淬鎳鐵渣1.0%),濕混5min;靜置60min后在30MPa下保壓30s,制得坯體;經(jīng)靜停1h后在75℃下飽和蒸汽養(yǎng)護(hù)10h,制得超高強(qiáng)材料F10。當(dāng)前第1頁1 2 3