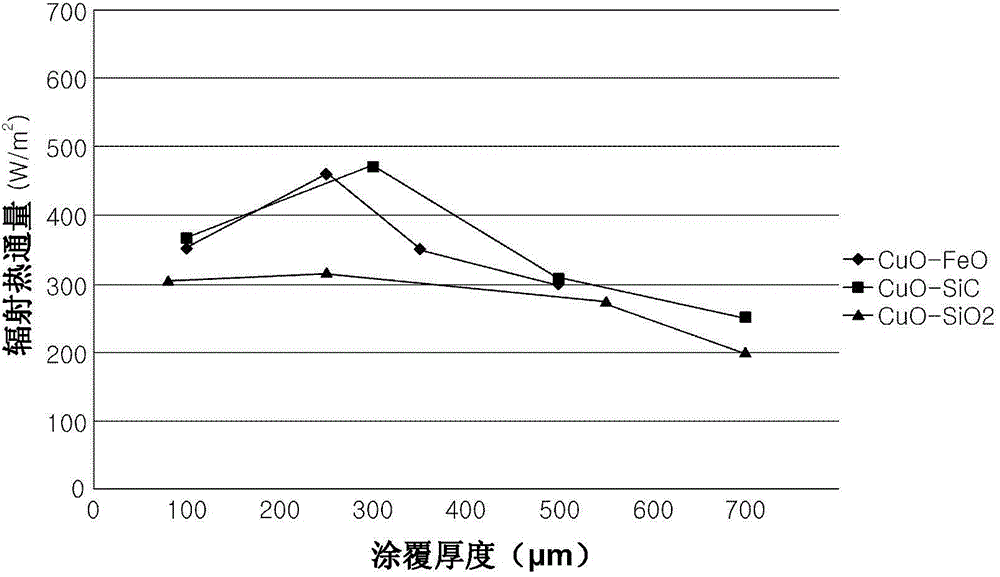
本發(fā)明涉及施用在金屬材料的表面上以確保由金屬材料制成的機(jī)械和電子部件的性能和耐久性的散熱涂覆組合物及其制備方法。更具體地說,本發(fā)明涉及使用通過化學(xué)結(jié)合多種陶瓷材料所得到的陶瓷化合物而可使散熱特性能得到改善的散熱涂覆組合物及其制備方法。
背景技術(shù):
:在整個(gè)工業(yè)領(lǐng)域中通常廣泛有用的各種機(jī)械和電子部件取決于裝置的工作生成熱。當(dāng)其溫度升高到任何臨界水平或更大時(shí),相應(yīng)的裝置或附近的裝置可能會變形或損壞,從而經(jīng)常導(dǎo)致較差的性能或較短的壽命。將熱從溫度高于周圍的部件向外側(cè)散發(fā)的散熱性能在設(shè)計(jì)所有生成熱的電子部件的過程中被認(rèn)為是重要的。為了防止各種機(jī)器和部件的溫度因生成的熱而升高至預(yù)定水平或更高,使用散熱單元,其例子可包括散熱器、散熱板、散熱墊、散熱帶和散熱涂層。具體地,在用于吸收或生成熱的材料(即具有較低發(fā)射率的金屬材料)的表面上將散熱涂層施用至預(yù)定厚度,從而迅速將熱散發(fā)到材料之外,以使該材料保持在預(yù)定的溫度范圍內(nèi)。散熱涂層主要施涂在材料表面上,或以膜形式層積在材料的表面上。這樣的散熱涂層通常通過將陶瓷材料與樹脂和稀釋劑混合來進(jìn)行制備。由于暴露于高溫,陶瓷材料須具有優(yōu)異的耐熱性、熱沖擊和機(jī)械強(qiáng)度以及較高的固有發(fā)射率。陶瓷材料可以包括氧化亞鐵(FeO)、三氧化二鐵(Fe2O3)、氧化銅(CuO)、碳化硅(SiC)、二氧化硅(SiO2)和氧化鋁(Al2O3),并且表現(xiàn)出0.8~0.9的發(fā)射率。通常,散熱涂層通過將樹脂和稀釋劑添加到如下混合物進(jìn)行制備, 該混合物得自以適當(dāng)比例簡單地混合多種具有優(yōu)異散熱性能的陶瓷材料。圖1是示出單個(gè)陶瓷材料取決于涂覆厚度的輻射熱通量的圖。如圖1所示,作為單個(gè)陶瓷材料的氧化銅(CuO)和氧化亞鐵(FeO)相比于其它陶瓷材料具有較高的散熱性能。當(dāng)涂層以200~300μm的厚度形成時(shí),可以得到優(yōu)異的散熱性能。圖2是示出通過簡單地混合單個(gè)陶瓷材料而得到的傳統(tǒng)混合物取決于涂覆厚度的輻射熱通量的圖。如圖1和2所示,通過簡單地混合單個(gè)陶瓷材料所制備的散熱材料對散熱性能的改善沒有影響。此外,其散熱性能可能變得與各個(gè)單獨(dú)的單個(gè)材料相似或比其更小。一種用于垂直排列結(jié)晶石墨粉末以提高散熱效率的技術(shù)在題為“Coatingcompositeforsinkingheat,heatsinkcoatingthatandmanufacturingmethodoftheheatsink”的韓國傳統(tǒng)技術(shù)中公開。雖然這樣的傳統(tǒng)技術(shù)旨在經(jīng)由陶瓷材料排列的變化來增強(qiáng)散熱效率,但是陶瓷材料的固有發(fā)射率無法經(jīng)由諸如陶瓷材料的顆粒大小、排列和簡單混合的物理方法得到增加,因此增強(qiáng)散熱性能有限制。技術(shù)實(shí)現(xiàn)要素:因此,鑒于相關(guān)技術(shù)中遇到的上述問題制作本發(fā)明,并且本發(fā)明的目的是提供不是通過簡單地物理混合陶瓷材料而是通過使陶瓷材料復(fù)合而具有改善的散熱特性的散熱涂覆組合物及其制備方法。根據(jù)其實(shí)施方式,本發(fā)明提供一種散熱涂覆組合物,包括:通過化學(xué)結(jié)合多種具有單一組成的陶瓷材料而獲得的復(fù)合陶瓷化合物;以及包含樹脂和稀釋劑的粘合劑。復(fù)合陶瓷化合物可以是通過將FeO和SiO2混合、熔融并且淬滅而制備的FeO-SiO2化合物。FeO-SiO2化合物可以以1:1~4的重量比包括FeO和SiO2。根據(jù)其另一實(shí)施方式,本發(fā)明提供制備散熱涂覆組合物的方法,包括:制備復(fù)合陶瓷化合物;以及將復(fù)合陶瓷化合物與包含樹脂和稀釋劑的粘合劑混合,從而制備散熱涂覆組合物,其中復(fù)合陶瓷化合物 通過化學(xué)結(jié)合多種具有單一組成的陶瓷材料而獲得。如此,制備復(fù)合陶瓷化合物的處理可包括:混合多種陶瓷材料,從而制備陶瓷混合物;對陶瓷混合物進(jìn)行球磨,從而制備混合陶瓷粉末;經(jīng)由加熱使混合陶瓷粉末熔融,從而制備陶瓷溶液;以及經(jīng)由淬滅使陶瓷溶液固化,從而制備復(fù)合陶瓷化合物。多種陶瓷材料可以以1:1~4的重量比包括FeO和SiO2。此外,可執(zhí)行對陶瓷混合物進(jìn)行球磨的處理,以使得陶瓷混合物具有45μm或更小(不包括零)的粒徑。此外,使混合陶瓷粉末熔融的處理可在惰性氣氛中在1400~1600℃執(zhí)行。根據(jù)本發(fā)明的實(shí)施方式,復(fù)合陶瓷化合物通過化學(xué)結(jié)合多種單個(gè)陶瓷材料而形成,從而形成與由陶瓷材料混合物制成的傳統(tǒng)涂覆組合物相比具有優(yōu)異散熱性能的散熱涂覆組合物。此外,復(fù)合陶瓷化合物通過使用具有較低價(jià)格和相對較低熔點(diǎn)的單個(gè)陶瓷材料來制備,從而有效改善散熱性能并減少制備成本。附圖說明根據(jù)以下具體實(shí)施方式并結(jié)合附圖,將更清楚地理解本發(fā)明的上述和其它目的、特征和優(yōu)點(diǎn):圖1是示出單個(gè)陶瓷材料取決于涂覆厚度的輻射熱通量的圖。圖2是示出通過簡單地混合單個(gè)陶瓷材料而得到的傳統(tǒng)混合物取決于涂覆厚度的輻射熱通量的圖。圖3是示出根據(jù)本發(fā)明的實(shí)施例中的復(fù)合陶瓷化合物取決于涂覆厚度的輻射熱通量的圖。圖4是示出根據(jù)本發(fā)明的實(shí)施例中的散熱涂覆組合物取決于涂覆厚度的輻射熱通量的圖;圖5是示出SiO2取決于溫度的相變的圖;圖6是示出作為傳統(tǒng)陶瓷材料的FeO和SiO2的混合物以及根據(jù)本發(fā)明的實(shí)施例4的復(fù)合陶瓷化合物的X射線衍射(XRD)測試結(jié)果的圖。圖7是示出傳統(tǒng)單個(gè)陶瓷材料CuO和根據(jù)本發(fā)明的實(shí)施例4的輻射熱通量的圖;并且圖8A和圖8B是示出在室溫(22℃)和高溫(70℃)的音頻散熱器的散熱性能測試結(jié)果的圖。具體實(shí)施方式在下文中,將參照附圖給出本發(fā)明優(yōu)選實(shí)施方式的詳細(xì)說明,但這樣的實(shí)施方式不解釋為限制本發(fā)明。在整個(gè)附圖中,相同的附圖標(biāo)記指代相同或相似的部件,并且可以參考其它附圖中所描繪的內(nèi)容加以描述。此外,對本領(lǐng)域技術(shù)人員而言被認(rèn)為是明顯的或者重復(fù)的描述可以省略。為了改善散熱性能,本發(fā)明采用通過化學(xué)結(jié)合多種單個(gè)陶瓷材料而制備的復(fù)合陶瓷化合物,而不是通過簡單混合單個(gè)陶瓷材料而得到的傳統(tǒng)陶瓷混合物。根據(jù)本發(fā)明的實(shí)施方式,散熱涂覆組合物由復(fù)合陶瓷化合物以及包含樹脂和稀釋劑的粘合劑組成。如此,復(fù)合陶瓷化合物通過化學(xué)結(jié)合多種具有單一組成的陶瓷材料來制備。通常,用于金屬材料散熱的典型涂覆組合物主要包括陶瓷材料,諸如氧化銅(CuO)、氧化亞鐵(FeO)、氧化鋁(Al2O3)、二氧化硅(SiO2)和碳化硅(SiC)。陶瓷材料的價(jià)格和熔點(diǎn)在下表1中示出。[表1]價(jià)格(won/kg)熔點(diǎn)(℃)氧化銅(CuO)16,5001,326氧化亞鐵(FeO)6,0001,377氧化鋁(Al2O3)6002,050二氧化硅(SiO2)3001,610碳化硅(SiC)1,0002,700如從表1中可明顯看出,陶瓷材料具有高于1,000℃的熔點(diǎn),并且可以在高達(dá)2,000℃或更高的溫度下熔融。在本發(fā)明中,由于復(fù)合陶瓷化合物應(yīng)當(dāng)通過熔融多種陶瓷材料來制備,所以優(yōu)選選擇具有相對較低熔點(diǎn)的陶瓷材料以減少制備成本。因此,根據(jù)本發(fā)明的復(fù)合陶瓷化合物的陶瓷材料較為價(jià)廉且具有較低熔點(diǎn)。根據(jù)用于形成根據(jù)本發(fā)明實(shí)施方式的復(fù)合陶瓷化合物的需求,考慮到具有單一組成的陶瓷材料的熔點(diǎn)和單位(units),使用具有相對較低熔點(diǎn)和較低價(jià)格的FeO和SiO2。如表1所示,F(xiàn)eO具有1377℃的熔點(diǎn),而SiO2具有1610℃的熔點(diǎn)。通常,兩種或更多種化合物材料取決于其組分比例在比各個(gè)單獨(dú)的材料的固有熔融溫度更低的溫度下熔融。因此,當(dāng)復(fù)合陶瓷化合物經(jīng)由FeO和SiO2的化學(xué)結(jié)合而形成時(shí),SiO2是與FeO相比具有相對較高熔點(diǎn)的陶瓷材料,但其熔融溫度因復(fù)合陶瓷化合物的形成而被降低至約1400℃。各個(gè)單獨(dú)的陶瓷材料具有固有發(fā)射率值。隨著陶瓷材料的顏色接近黑色,其固有發(fā)射率增加。事實(shí)上,具有高固有發(fā)射率的陶瓷粉末(除了Al2O3)通常顯示致密黑色。對于根據(jù)本發(fā)明實(shí)施方式的復(fù)合陶瓷化合物的制備,選擇具有致密黑色的FeO。根據(jù)本發(fā)明實(shí)施方式的復(fù)合陶瓷化合物通過將FeO和SiO2混合、熔融并且淬滅來制備。在本發(fā)明的各種實(shí)施例中,F(xiàn)eO和SiO2的混合比在下表2中給出。[表2]FeO(wt%)SiO2(wt%)實(shí)施例12080實(shí)施例24060實(shí)施例35050實(shí)施例46040實(shí)施例58020圖3是示出根據(jù)本發(fā)明的各種實(shí)施例中的復(fù)合陶瓷化合物取決于涂覆厚度的輻射熱通量的圖。如表2和圖3中所示,通過混合FeO和SiO2而制備的復(fù)合陶瓷化合物的所有輻射熱通量值是500W/m2,其與具有單一組成的傳統(tǒng)陶瓷材料相比相對較高,從而導(dǎo)致改善的散熱性能。特別地,以1:1~1:4的重量比包括FeO和SiO2的復(fù)合陶瓷化合物具有600W/m2或更多的輻射熱通量,因此散熱性能顯著增加。根據(jù)本發(fā)明實(shí)施方式的復(fù)合陶瓷化合物優(yōu)選由FeO和SiO2以1:1~4的重量比組成。圖4是示出本發(fā)明的各種實(shí)施例中的散熱涂覆組合物取決于涂覆厚度的輻射熱通量的圖。如圖4所示,當(dāng)根據(jù)本發(fā)明實(shí)施方式的散熱涂覆組合物施用至300μm的厚度時(shí),可以表現(xiàn)最大的散熱性能。因此,根據(jù)本發(fā)明實(shí)施方式的涂覆組合物優(yōu)選施用至約300μm的厚度。此外,隨著SiO2的量越大,散熱性能提高。這是因?yàn)镾iO2相變成方石英,并且形成基于FeO-SiO2的化合物,從而提高了散熱性能,這在根據(jù)本發(fā)明的另一實(shí)施方式的散熱涂覆組合物的制備方法中再次描述。根據(jù)本發(fā)明的另一實(shí)施方式,制備散熱涂覆組合物的方法包括制備復(fù)合陶瓷化合物,以及將復(fù)合陶瓷化合物與樹脂和稀釋劑混合。在本發(fā)明中,制備復(fù)合陶瓷化合物的處理可以通過如下執(zhí)行:將多種陶瓷材料混合,從而制備陶瓷混合物;研磨該陶瓷混合物,從而制備陶瓷粉末;使陶瓷粉末熔融,從而制備陶瓷溶液;并且經(jīng)由冷卻使陶瓷溶液固化。在制備陶瓷混合物時(shí),單個(gè)陶瓷材料,例如FeO和SiO2可以以1:1~4的重量比混合。重量比如上限制的原因如上關(guān)于散熱涂覆組合物的描述中所述。在研磨陶瓷混合物時(shí),使以預(yù)定混合比包括FeO和SiO2的陶瓷混合物球磨約24小時(shí),得到陶瓷粉末。如此,陶瓷粉末優(yōu)選具有45μm或更小(不包括零)的粒徑。這是因?yàn)?,散熱性能在涂覆過程中與用于散熱涂層的陶瓷材料的粒徑的降低成比例地增強(qiáng)。在熔融陶瓷粉末時(shí),將陶瓷粉末加熱以得到陶瓷溶液。根據(jù)本發(fā)明實(shí)施方式的熔融過程優(yōu)選以如下方式執(zhí)行,即,使陶瓷粉末在惰性氣氛中在1400~1600℃下熔融。雖然FeO具有1377℃的熔點(diǎn),而SiO2具有1610℃的熔點(diǎn),但是 兩種或更多種化合物材料的熔融過程取決于如上所述的其組分比率在比各個(gè)單獨(dú)的材料的固有熔融溫度更低的溫度下進(jìn)行。參與反應(yīng)之后剩余的SiO2在1400~1600℃形成為具有立方結(jié)構(gòu)的方石英相。因此,復(fù)合陶瓷化合物的發(fā)射率可以提高,同時(shí)減少陶瓷粉末熔融成本。圖5是示出SiO2取決于溫度的相變的圖,且圖6是示出用作傳統(tǒng)陶瓷材料的FeO和SiO2的混合物以及根據(jù)本發(fā)明的實(shí)施例4的復(fù)合陶瓷化合物的XRD測試結(jié)果的圖。如圖5和圖6所示,SiO2在1400~1700℃經(jīng)歷從HCP結(jié)構(gòu)到立方結(jié)構(gòu)的相變。雖然SiO2的這種相變是不論發(fā)射率的,但是具有立方結(jié)構(gòu)的方石英顯示出淬滅效應(yīng),從而增加了本發(fā)明實(shí)施例中制備的復(fù)合陶瓷化合物的發(fā)射率。如圖6所示,在XRD分析時(shí),F(xiàn)eO和SiO2的混合物同時(shí)表現(xiàn)FeO相和SiO2相兩者,而實(shí)施例4的化學(xué)結(jié)合的FeO和SiO2顯示出新相。如此,在根據(jù)本發(fā)明的實(shí)施例4中觀察到方石英,其被認(rèn)為得自與FeO反應(yīng)之后剩余的SiO2。在熔融過程完成之后,陶瓷溶液經(jīng)由諸如水淬滅的冷卻過程固化,得到FeO-SiO2化合物。圖7是示出傳統(tǒng)單個(gè)陶瓷材料CuO和根據(jù)本發(fā)明的實(shí)施例4的輻射熱通量的圖。如圖7所示,與沒有被球磨的稀CuO相比,經(jīng)球磨的CuO的散熱效果提高。根據(jù)本發(fā)明的實(shí)施方式,當(dāng)球磨具有高輻射熱通量的CuO時(shí),其散熱效果相比于研磨具有好散熱效果的CuO可變得優(yōu)異。圖8A是示出在室溫(22℃)的音頻散熱器的散熱性能測試結(jié)果的圖,而圖8B是示出在高溫(70℃)的音頻散熱器的散熱性能測試結(jié)果的圖。如圖8A和8B所示,未涂覆有壓鑄合金的音頻散熱器的溫度在30分鐘的輸出時(shí)間是100.2℃,涂覆有傳統(tǒng)單個(gè)陶瓷材料CuO的音頻散熱器的溫度在30分鐘的輸出時(shí)間是98.8℃,并且陽極氧化的音頻散熱器的溫度在30分鐘的輸出時(shí)間是94.9℃。然而,涂覆有包括根據(jù)本發(fā)明實(shí)施方式的基于FeO-SiO2的復(fù)合陶瓷化合物的散熱涂覆組合物的音 頻散熱器的溫度在30分鐘的輸出時(shí)間是88.9℃。因此,與傳統(tǒng)情況相比,包括根據(jù)本發(fā)明實(shí)施方式的散熱涂覆組合物的涂層可以表現(xiàn)出改善的散熱性能。特別地,經(jīng)涂覆的音頻散熱器的溫度與未涂覆的音頻散熱器的溫度相差11.3℃,因此呈現(xiàn)優(yōu)異的散熱性能。另一方面,在70℃的爐中,未涂覆的音頻散熱器的溫度在30分鐘的輸出時(shí)間是143.3℃,涂覆有傳統(tǒng)單個(gè)陶瓷材料CuO的音頻散熱器的溫度在30分鐘的輸出時(shí)間是137.5℃,并且陽極氧化的音頻散熱器的溫度在30分鐘的輸出時(shí)間是137.2℃。然而,涂覆有包括根據(jù)本發(fā)明實(shí)施方式的基于FeO-SiO2的復(fù)合陶瓷化合物的散熱涂覆組合物的音頻散熱器的溫度在30分鐘的輸出時(shí)間是132.3℃。在高溫下的散熱性能測試中,涂覆有包括根據(jù)本發(fā)明實(shí)施方式的復(fù)合陶瓷化合物的散熱涂覆組合物的音頻散熱器的溫度在30分鐘的輸出時(shí)間被測量為較低,從而相比于其它情況,表現(xiàn)出優(yōu)異的散熱性能。此外,其溫度比未涂覆的音頻散熱器的溫度更低11.0℃。如上所述,根據(jù)本發(fā)明的復(fù)合陶瓷化合物配置成使得多種陶瓷材料形成為化合物,而不是簡單的物理混合物,最終獲得優(yōu)異的散熱性能。因此,散熱涂覆組合物的散熱性顯著增強(qiáng)。盡管本發(fā)明的優(yōu)選實(shí)施方式已被公開用于示例說明的目的,但是本領(lǐng)域的技術(shù)人員將理解,在不脫離如所附權(quán)利要求中公開的本發(fā)明的范圍和精神的情況下,可以進(jìn)行各種修改、添加和替換。當(dāng)前第1頁1 2 3