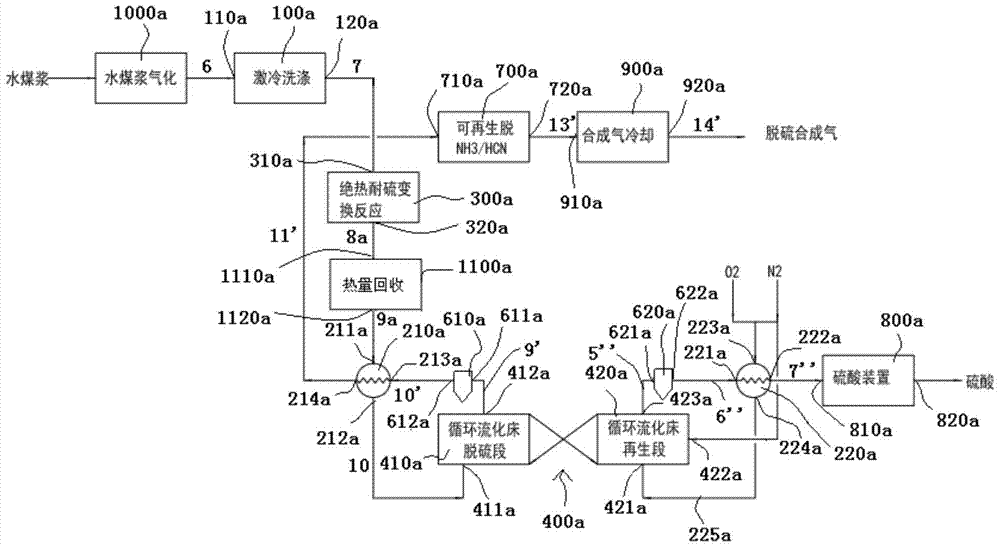
本發(fā)明涉及煤或其它含碳材料的氣化產(chǎn)生的粗合成氣中脫除雜質(zhì)的凈化技術(shù)領(lǐng)域,特別涉及一種結(jié)合耐硫變換和循環(huán)流化床熱法脫硫的合成氣凈化方法及裝置和應(yīng)用。本發(fā)明除去合成氣中含硫化合物、砷及其化合物、硒及其化合物、輕質(zhì)芳烴和痕量的雜質(zhì),雜質(zhì)例如氨、氰化物、汞、氯化氫,適用于該領(lǐng)域的新建或改造項(xiàng)目。
背景技術(shù):在現(xiàn)有的技術(shù)和工業(yè)實(shí)踐中,通常采用兩種方法實(shí)現(xiàn)從合成氣中除去酸性氣體以及其他雜質(zhì)。一種是使用溶劑進(jìn)行物理或化學(xué)的液相吸收;一種是使用固體吸附劑在固定床中脫除。通過液相吸收脫除氣體中的硫化合物,已經(jīng)實(shí)現(xiàn)工業(yè)化有Linde和Lurgi許可的Rectisol以及上海國際化建工程咨詢公司的分流式低溫甲醇洗(專利號:ZL200910052424.1),該工藝采用甲醇為吸收溶劑,在極低的溫度下操作,需消耗大量冷量,對設(shè)備材質(zhì)的要求較高且工藝流程復(fù)雜,導(dǎo)致裝置成本投資高。此外,其他實(shí)現(xiàn)液相吸收脫除氣體中的硫化合物工業(yè)化還有Selexol工藝,該工藝中使用聚乙二醇二甲醚為溶劑,但該工藝對脫除合成氣中的COS有一定的困難,如要將酸性氣體中濃度高的COS除去,需增加COS水解單元,且溶劑的循環(huán)量大導(dǎo)致操作成本高。來自氣化的高溫合成氣經(jīng)過耐硫變換反應(yīng)后,溫度通常在270-450℃,而以上液相吸收法在這樣的高溫氣體中是無效的,因?yàn)檫@些方法典型地需要在零度以下較低的溫度下操作,因此合成氣需要進(jìn)行熱回收、冷卻處理,以滿足液相吸收法除去雜質(zhì)的低溫條件。顯而易見,這樣的冷卻、熱回收和相關(guān)處理會導(dǎo)致下游合成氣利用的熱效率降低。通過使用固體吸附劑在固定床中脫除氣體中的硫化合物的方法存在處理能力小,吸附劑再生困難的缺點(diǎn)。
技術(shù)實(shí)現(xiàn)要素:本發(fā)明所要解決的技術(shù)問題之一在于針對現(xiàn)有技術(shù)所存在的不足之處而提供一種結(jié)合耐硫變換和循環(huán)流化床熱法脫硫的合成氣凈化方法。本發(fā)明所要解決的技術(shù)問題之二在于提供實(shí)現(xiàn)上述合成氣凈化方法的裝置。本發(fā)明所要解決的技術(shù)問題之三在于提供上述合成氣凈化方法的應(yīng)用。作為本發(fā)明第一方面的第一種結(jié)合耐硫變換和循環(huán)流化床熱法脫硫的合成氣凈化方法,其是將經(jīng)過煤或其它含碳材料的氣化產(chǎn)生第一粗合成氣送入一水激冷洗滌裝置進(jìn)行水激冷洗滌形成第二粗合成氣送入耐硫變換反應(yīng)系統(tǒng);在所述耐硫變換反應(yīng)系統(tǒng)內(nèi),第二粗合成氣發(fā)生如下反應(yīng)CO+H2O→CO2+H2形成第三粗合成氣送出;送出的第三粗合成氣進(jìn)入熱量回收裝置進(jìn)行降溫形成第四粗合成氣送出;送出的第四粗合成氣進(jìn)入第一換熱器,與進(jìn)入第一換熱器的第一脫硫后的合成氣換熱后形成第五粗合成氣送出;送出的第五粗合成氣由循環(huán)流化床的吸附反應(yīng)器中的提升管的底部進(jìn)入到循環(huán)流化床的吸附反應(yīng)器中的提升管內(nèi),與從循環(huán)流化床的再生反應(yīng)器來的再生固體吸附劑在循環(huán)流化床的吸附反應(yīng)器中的提升管內(nèi)混合反應(yīng),混合反應(yīng)過程中所述再生固體吸附劑中的活性金屬氧化物MO與第五粗合成氣中的含有硫雜質(zhì)反應(yīng),產(chǎn)生載有硫的吸附劑MS,具體反應(yīng)式如下:H2S+MO→MS+H2OCOS+MO→CO2+MS其中,M為存在于再生固體吸附劑中的金屬;混合反應(yīng)過程后形成的含固體吸附顆粒的第二脫硫后的合成氣由循環(huán)流化床的吸附反應(yīng)器中的旋風(fēng)分離器上部進(jìn)入到所述循環(huán)流化床的吸附反應(yīng)器中的旋風(fēng)分離器內(nèi)進(jìn)行旋風(fēng)分離;經(jīng)過所述循環(huán)流化床的吸附反應(yīng)器中的旋風(fēng)分離器分離后形成第三脫硫后的合成氣,所述的第三脫硫后的合成氣由所述循環(huán)流化床的吸附反應(yīng)器中的旋風(fēng)分離器的頂部送出,送出的第三脫硫后的合成氣經(jīng)過第一過濾器過濾后形成所述的第一脫硫后的合成氣送入到第一換熱器內(nèi),經(jīng)過與進(jìn)入第一換熱器內(nèi)的第四粗合成氣換熱后形成所述的第四脫硫后的合成氣進(jìn)入一可再生脫NH3/HCN裝置中脫除第四脫硫后的合成氣中的NH3/HCN形成第五脫硫后的合成氣,所述第五脫硫后的合成氣送入一冷卻裝置中進(jìn)行冷卻形成第六脫硫后的合成氣送出;經(jīng)過所述循環(huán)流化床的吸附反應(yīng)器中的旋風(fēng)分離器分離后的固體吸附顆粒一部分為活性金屬氧化物MO,另一部分為載有硫的吸附劑MS,經(jīng)過所述旋風(fēng)分離器分離后的活性金屬氧化物MO和載有硫的吸附劑MS通過所述循環(huán)流化床的吸附反應(yīng)器中的下降管循環(huán)進(jìn)入到循環(huán)流化床的吸附反應(yīng)器中的提升管內(nèi),活性金屬氧化物MO與循環(huán)流化床的吸附反應(yīng)器中的提升管內(nèi)的第五粗合成氣中的含有硫雜質(zhì)反應(yīng),產(chǎn)生載有硫的吸附劑MS;經(jīng)過所述循環(huán)流化床的吸附反應(yīng)器中的旋風(fēng)分離器分離后的載有硫的吸附劑MS通過所述循環(huán)流化床的吸附反應(yīng)器中的下降管進(jìn)入到循環(huán)流化床的再生反應(yīng)器中的提升管內(nèi),與進(jìn)入循環(huán)流化床的再生反應(yīng)器中的提升管內(nèi)的再生空氣或O2與N2的混合氣體混合反應(yīng),使得載有硫的吸附劑MS得以再生形成所述的再生固體吸附劑,具體反應(yīng)式如下:MS+3/2O2→MO+SO2;混合反應(yīng)后形成的含有所述的再生固體吸附劑的第一富SO2的氣體進(jìn)入到循環(huán)流化床的再生反應(yīng)器中的旋風(fēng)分離器中進(jìn)行旋風(fēng)分離,循環(huán)流化床的再生反應(yīng)器中的旋風(fēng)分離器分離后的第二富SO2的氣體由所述循環(huán)流化床的再生反應(yīng)器中的旋風(fēng)分離器的頂部送出,經(jīng)過第二過濾器過濾后所形成的第三富SO2的氣體送入第二換熱器,與進(jìn)入到所述第二換熱器內(nèi)的再生所需要的所述的再生空氣或O2與N2的混合氣體進(jìn)行換熱形成第四富SO2的氣體送出至下游去生產(chǎn)硫酸或者單質(zhì)硫;循環(huán)流化床的再生反應(yīng)器中的旋風(fēng)分離器分離后的所述的再生固體吸附劑通過所述循環(huán)流化床的再生反應(yīng)器中的下降管送入到循環(huán)流化床的吸附反應(yīng)器中的提升管內(nèi)。在本發(fā)明第一種結(jié)合耐硫變換和循環(huán)流化床熱法脫硫的合成氣凈化方法的一個(gè)優(yōu)選實(shí)施例中,在所述可再生脫NH3/HCN裝置與所述冷卻裝置之間增加一脫除汞和氯化物裝置,以脫除所述第五脫硫后的合成氣中的汞和氯化物,經(jīng)過脫除汞和氯化物裝置脫除汞和氯化物的第七脫硫后的合成氣送入所述冷卻裝置中進(jìn)行冷卻形成第六脫硫后的合成氣送出。在本發(fā)明第一種結(jié)合耐硫變換和循環(huán)流化床熱法脫硫的合成氣凈化方法的一個(gè)優(yōu)選實(shí)施例中,所述經(jīng)過煤或其它含碳材料的氣化產(chǎn)生第一粗合成氣為水煤漿氣化、粉煤氣化或碎煤固定床氣化產(chǎn)生第一粗合成氣。在本發(fā)明第一種結(jié)合耐硫變換和循環(huán)流化床熱法脫硫的合成氣凈化方法的一個(gè)優(yōu)選實(shí)施例中,所述第二粗合成氣的溫度為180-250℃。在本發(fā)明第一種結(jié)合耐硫變換和循環(huán)流化床熱法脫硫的合成氣凈化方法的一個(gè)優(yōu)選實(shí)施例中,所述耐硫變換反應(yīng)系統(tǒng)使用絕熱耐硫變換反應(yīng)器或等溫耐硫變換反應(yīng)器或本申請人申請的中國專利號ZL201210040295.6發(fā)明名稱為帶有支撐式槽孔板分布器的徑向或軸徑向固定床反應(yīng)器;所述帶有支撐式槽孔板分布器的徑向或軸徑向固定床反應(yīng)器,包括承壓殼體和設(shè)置在所述承壓殼體內(nèi)且與承壓殼體同軸的催化劑外框和氣體收集中心管,所述承壓殼體上設(shè)置有氣體進(jìn)口和氣體出口,所述催化劑外框由支撐在承壓殼體內(nèi)壁上的支撐式槽孔板分布器構(gòu)成;所述支撐式槽孔板分布器有由規(guī)格一致的若干槽孔分布板相互搭接構(gòu)成;所述的槽孔分布板采用角鋼和支座支撐在承壓殼體的內(nèi)壁上,所述角鋼與支座之間采用螺栓連接,所述支座固定在承壓殼體的內(nèi)壁上,所述槽孔分布板與承壓殼體之間保留一定的弧形間隙;所述槽孔分布板為其上開設(shè)有密集槽孔的弧形長條板。在本發(fā)明第一種結(jié)合耐硫變換和循環(huán)流化床熱法脫硫的合成氣凈化方法的一個(gè)優(yōu)選實(shí)施例中,所述循環(huán)流化床的吸附反應(yīng)器和循環(huán)流化床的再生反應(yīng)器形成一流化催化裂化FCC工藝系統(tǒng)。在本發(fā)明第一種結(jié)合耐硫變換和循環(huán)流化床熱法脫硫的合成氣凈化方法的一個(gè)優(yōu)選實(shí)施例中,所述第三粗合成氣的溫度為270-450℃。在本發(fā)明第一種結(jié)合耐硫變換和循環(huán)流化床熱法脫硫的合成氣凈化方法的一個(gè)優(yōu)選實(shí)施例中,所述第四粗合成氣的溫度為75-200℃。在本發(fā)明第一種結(jié)合耐硫變換和循環(huán)流化床熱法脫硫的合成氣凈化方法的一個(gè)優(yōu)選實(shí)施例中,所述第五粗合成氣的溫度為300-550℃。在本發(fā)明第一種結(jié)合耐硫變換和循環(huán)流化床熱法脫硫的合成氣凈化方法的一個(gè)優(yōu)選實(shí)施例中,所述再生固體吸附劑中的活性金屬氧化物MO與第五粗合成氣中的含有硫雜質(zhì)反應(yīng)時(shí)的溫度為320-580℃。在本發(fā)明第一種結(jié)合耐硫變換和循環(huán)流化床熱法脫硫的合成氣凈化方法的一個(gè)優(yōu)選實(shí)施例中,所述第三脫硫后的合成氣中的硫含量低至0.5-5ppmv。在本發(fā)明第一種結(jié)合耐硫變換和循環(huán)流化床熱法脫硫的合成氣凈化方法的一個(gè)優(yōu)選實(shí)施例中,所述第四脫硫后的合成氣的溫度為170-230℃。在本發(fā)明第一種結(jié)合耐硫變換和循環(huán)流化床熱法脫硫的合成氣凈化方法的一個(gè)優(yōu)選實(shí)施例中,所述第六脫硫后的合成氣送入下游的脫二氧化碳單元裝置中,以脫除其中的二氧化碳。在本發(fā)明第一種結(jié)合耐硫變換和循環(huán)流化床熱法脫硫的合成氣凈化方法的一個(gè)優(yōu)選實(shí)施例中,所述脫二氧化碳單元裝置為液相吸收脫二氧化碳單元裝置或干法化學(xué)吸附脫二氧化碳單元裝置。在本發(fā)明第一種結(jié)合耐硫變換和循環(huán)流化床熱法脫硫的合成氣凈化方法的一個(gè)優(yōu)選實(shí)施例中,所述可再生脫NH3/HCN裝置為吸附床。在本發(fā)明第一種結(jié)合耐硫變換和循環(huán)流化床熱法脫硫的合成氣凈化方法的一個(gè)優(yōu)選實(shí)施例中,所述吸附床為固定式吸附床。在本發(fā)明第一種結(jié)合耐硫變換和循環(huán)流化床熱法脫硫的合成氣凈化方法的一個(gè)優(yōu)選實(shí)施例中,所述脫除汞和氯化物裝置為保護(hù)床。在本發(fā)明第一種結(jié)合耐硫變換和循環(huán)流化床熱法脫硫的合成氣凈化方法的一個(gè)優(yōu)選實(shí)施例中,所述第一富SO2的氣體的溫度為650-750℃。在本發(fā)明第一種結(jié)合耐硫變換和循環(huán)流化床熱法脫硫的合成氣凈化方法的一個(gè)優(yōu)選實(shí)施例中,所述第四富SO2的氣體的溫度為330-530℃。在本發(fā)明第一種結(jié)合耐硫變換和循環(huán)流化床熱法脫硫的合成氣凈化方法的一個(gè)優(yōu)選實(shí)施例中,所述進(jìn)入循環(huán)流化床的再生反應(yīng)器中的提升管內(nèi)的再生空氣或O2與N2的混合氣體的溫度為450-550℃。在本發(fā)明第一種結(jié)合耐硫變換和循環(huán)流化床熱法脫硫的合成氣凈化方法的一個(gè)優(yōu)選實(shí)施例中,所述M為存在于再生固體吸附劑中的金屬。例如Zn。作為本發(fā)明第一方面的實(shí)現(xiàn)上述第一種結(jié)合耐硫變換和循環(huán)流化床熱法脫硫的合成氣凈化方法的裝置,包括:一水激冷洗滌裝置,所述水激冷洗滌裝置具有一粗合成氣輸入口和粗合成氣輸出口,該水激冷洗滌裝置的粗合成氣輸入口通過一第一粗合成氣輸送管線連接一煤氣化裝置;一耐硫變換反應(yīng)系統(tǒng),該耐硫變換反應(yīng)系統(tǒng)具有一粗合成氣輸入口和粗合成氣輸出口,所述耐硫變換反應(yīng)系統(tǒng)的粗合成氣輸入口通過一第二粗合成氣輸送管線連接所述水激冷洗滌裝置的粗合成氣輸出口;一熱量回收裝置,該熱量回收裝置具有一粗合成氣輸入口和粗合成氣輸出口,所述熱量回收裝置的粗合成氣輸入口通過一第三粗合成氣輸送管線連接所述耐硫變換反應(yīng)系統(tǒng)的粗合成氣輸出口;一第一換熱器,所述第一換熱器具有一粗合成氣輸入口、一粗合成氣輸出口、一脫硫后的合成氣輸入口和一脫硫后的合成氣輸出口,所述第一換熱器的粗合成氣輸入口通過一第四粗合成氣輸送管線連接所述熱量回收裝置的粗合成氣輸出口;一循環(huán)流化床的吸附反應(yīng)器,所述循環(huán)流化床的吸附反應(yīng)器包括一提升管、一旋風(fēng)分離器和一下降管,所述循環(huán)流化床的吸附反應(yīng)器的提升管的底部具有一粗合成氣輸入口,所述循環(huán)流化床的吸附反應(yīng)器的提升管的下部配置有再生吸附劑入口和循環(huán)吸附劑入口,所述循環(huán)流化床的吸附反應(yīng)器的提升管的上部配置有含固體吸附顆粒的脫硫后的合成氣出口;所述循環(huán)流化床的吸附反應(yīng)器的旋風(fēng)分離器的上部配置有含固體吸附顆粒的脫硫后的合成氣入口,所述循環(huán)流化床的吸附反應(yīng)器的旋風(fēng)分離器的頂部配置有脫硫后的合成氣輸出口,所述循環(huán)流化床的吸附反應(yīng)器的旋風(fēng)分離器的下部配置有載有硫的吸附劑出口;所述循環(huán)流化床的吸附反應(yīng)器的下降管的上部配置有載有硫的吸附劑入口,所述循環(huán)流化床的吸附反應(yīng)器的下降管的下部配置有一載有硫的吸附劑循環(huán)出口和一載有硫的吸附劑待再生出口;所述循環(huán)流化床的吸附反應(yīng)器的提升管底部的粗合成氣輸入口通過一第五粗合成氣輸送管線連接所述的第一換熱器的粗合成氣輸出口;所述循環(huán)流化床的吸附反應(yīng)器的提升管下部的循環(huán)吸附劑入口與所述循環(huán)流化床的吸附反應(yīng)器的下降管的載有硫的吸附劑循環(huán)出口連接,所述循環(huán)流化床的吸附反應(yīng)器的提升管上部的含固體吸附顆粒的脫硫后的合成氣出口通過一含固體吸附顆粒的第二脫硫后的合成氣輸送管線與所述循環(huán)流化床的吸附反應(yīng)器的旋風(fēng)分離器上部的含固體吸附顆粒的脫硫后的合成氣入口連接;一第一過濾器,所述第一過濾器具有一脫硫后的合成氣輸入口和一脫硫后的合成氣輸出口,所述第一過濾器的脫硫后的合成氣輸入口通過一第三脫硫后的合成氣輸送管線與所述循環(huán)流化床的吸附反應(yīng)器的旋風(fēng)分離器頂部的脫硫后的合成氣輸出口連接,所述第一過濾器的脫硫后的合成氣輸出口通過一第一脫硫后的合成氣輸送管線與所述第一換熱器的脫硫后的合成氣輸入口連接;一循環(huán)流化床的再生反應(yīng)器,所述循環(huán)流化床的再生反應(yīng)器包括一提升管、一旋風(fēng)分離器和一下降管,所述循環(huán)流化床的再生反應(yīng)器的提升管的下部配置有載有硫的吸附劑待再生入口,所述循環(huán)流化床的再生反應(yīng)器的提升管的底部配置有再生空氣或O2與N2的混合氣體入口,所述循環(huán)流化床的再生反應(yīng)器的提升管的上部配置有含有再生固體吸附劑的富SO2的氣體出口;所述循環(huán)流化床的再生反應(yīng)器的旋風(fēng)分離器的上部配置有含有再生固體吸附劑的富SO2的氣體入口,所述循環(huán)流化床的再生反應(yīng)器的旋風(fēng)分離器的頂部配置有富SO2的氣體出口,所述循環(huán)流化床的再生反應(yīng)器的旋風(fēng)分離器的下部配置有再生吸附劑出口;所述循環(huán)流化床的再生反應(yīng)器的下降管的上部配置有再生吸附劑入口,所述循環(huán)流化床的再生反應(yīng)器的下降管的下部配置有再生吸附劑出口;所述循環(huán)流化床的再生反應(yīng)器的提升管下部的載有硫的吸附劑入口與所述循環(huán)流化床的吸附反應(yīng)器的下降管的吸附劑待再生出口連接;所述循環(huán)流化床的再生反應(yīng)器的旋風(fēng)分離器上部的含有再生固體吸附劑的富SO2的氣體入口通過一含有再生固體吸附劑的第一富SO2的氣體輸送管線與所述循環(huán)流化床的再生反應(yīng)器的提升管上部的含有再生固體吸附劑的富SO2的氣體出口連接;所述循環(huán)流化床的再生反應(yīng)器的旋風(fēng)分離器的下部的再生固體吸附劑出口與所述循環(huán)流化床的再生反應(yīng)器的下降管的上部再生固體吸附劑入口連接;所述循環(huán)流化床的再生反應(yīng)器的下降管的下部的再生吸附劑出口通過一再生吸附劑輸送管線與所述循環(huán)流化床的吸附反應(yīng)器的提升管下部的再生吸附劑入口連接;一第二過濾器,所述第二過濾器具有一富SO2的氣體入口和富SO2的氣體出口,所述第二過濾器的富SO2的氣體入口與所述循環(huán)流化床的再生反應(yīng)器的旋風(fēng)分離器頂部的富SO2的氣體出口通過一第二富SO2的氣體輸送管線連接;一第二換熱器,所述第二換熱器具有一富SO2的氣體入口、富SO2的氣體出口、再生空氣或O2與N2的混合氣體入口、再生空氣或O2與N2的混合氣體出口,所述第二換熱器的富SO2的氣體入口通過一第三富SO2的氣體輸送管線連接所述第二過濾器的富SO2的氣體出口,所述第二換熱器的再生空氣或O2與N2的混合氣體入口連接空氣源或O2與N2的混合氣體源;所述第二換熱器的再生空氣或O2與N2的混合氣體出口通過再生空氣或O2與N2的混合氣體輸送管線連接所述循環(huán)流化床的再生反應(yīng)器的提升管底部的再生空氣或O2與N2的混合氣體入口;一可再生脫NH3/HCN裝置,所述可再生脫NH3/HCN裝置具有脫硫后的合成氣入口和脫硫后的合成氣出口,所述再生脫NH3/HCN裝置的脫硫后的合成氣入口通過一第四脫硫后的合成氣輸送管線與所述第一換熱器的脫硫后的合成氣輸出口連接;一冷卻裝置,所述冷卻裝置具有脫硫后的合成氣入口和脫硫后的合成氣出口,所述冷卻裝置的脫硫后的合成氣入口通過一第五脫硫后的合成氣輸送管線與所述可再生脫NH3/HCN裝置的脫硫后的合成氣出口連接,所述冷卻裝置的脫硫后的合成氣出口通過一第六脫硫后的合成氣輸送管線與下游的脫二氧化碳單元裝置連接。在本發(fā)明實(shí)現(xiàn)上述第一種結(jié)合耐硫變換和循環(huán)流化床熱法脫硫的合成氣凈化方法的裝置的一個(gè)優(yōu)選實(shí)施例中,在所述可再生脫NH3/HCN裝置與所述冷卻裝置之間增加一脫除汞和氯化物裝置,所述脫除汞和氯化物裝置具有脫硫后的合成氣入口和脫硫后的合成氣出口,所述脫除汞和氯化物裝置的脫硫后的合成氣入口通過一第五脫硫后的合成氣輸送管線與所述可再生脫NH3/HCN裝置的脫硫后的合成氣出口連接,所述脫除汞和氯化物裝置的脫硫后的合成氣出口通過一第七脫硫后的合成氣輸送管線與所述冷卻裝置的脫硫后的合成氣入口連接。在本發(fā)明實(shí)現(xiàn)上述第一種結(jié)合耐硫變換和循環(huán)流化床熱法脫硫的合成氣凈化方法的裝置的一個(gè)優(yōu)選實(shí)施例中,所述煤氣化裝置為水煤漿氣化裝置、粉煤氣化裝置或碎煤固定床氣化裝置。在本發(fā)明實(shí)現(xiàn)上述第一種結(jié)合耐硫變換和循環(huán)流化床熱法脫硫的合成氣凈化方法的裝置的一個(gè)優(yōu)選實(shí)施例中,所述耐硫變換反應(yīng)系統(tǒng)使用絕熱耐硫變換反應(yīng)器或等溫耐硫變換反應(yīng)器或本申請人申請的中國專利號ZL201210040295.6、發(fā)明名稱為帶有支撐式槽孔板分布器的徑向或軸徑向固定床反應(yīng)器;所述帶有支撐式槽孔板分布器的徑向或軸徑向固定床反應(yīng)器,包括承壓殼體和設(shè)置在所述承壓殼體內(nèi)且與承壓殼體同軸的催化劑外框和氣體收集中心管,所述承壓殼體上設(shè)置有氣體進(jìn)口和氣體出口,所述催化劑外框由支撐在承壓殼體內(nèi)壁上的支撐式槽孔板分布器構(gòu)成;所述支撐式槽孔板分布器有由規(guī)格一致的若干槽孔分布板相互搭接構(gòu)成;所述的槽孔分布板采用角鋼和支座支撐在承壓殼體的內(nèi)壁上,所述角鋼與支座之間采用螺栓連接,所述支座固定在承壓殼體的內(nèi)壁上,所述槽孔分布板與承壓殼體之間保留一定的弧形間隙;所述槽孔分布板為其上開設(shè)有密集槽孔的弧形長條板。在本發(fā)明實(shí)現(xiàn)上述第一種結(jié)合耐硫變換和循環(huán)流化床熱法脫硫的合成氣凈化方法的裝置的一個(gè)優(yōu)選實(shí)施例中,所述循環(huán)流化床的吸附反應(yīng)器和循環(huán)流化床的再生反應(yīng)器形成一流化催化裂化FCC工藝系統(tǒng)。在本發(fā)明實(shí)現(xiàn)上述第一種結(jié)合耐硫變換和循環(huán)流化床熱法脫硫的合成氣凈化方法的裝置的一個(gè)優(yōu)選實(shí)施例中,所述脫二氧化碳單元裝置為液相吸收脫二氧化碳單元裝置或干法化學(xué)吸附脫二氧化碳單元裝置。在本發(fā)明實(shí)現(xiàn)上述第一種結(jié)合耐硫變換和循環(huán)流化床熱法脫硫的合成氣凈化方法的裝置的一個(gè)優(yōu)選實(shí)施例中,所述可再生脫NH3/HCN裝置為吸附床。在本發(fā)明實(shí)現(xiàn)上述第一種結(jié)合耐硫變換和循環(huán)流化床熱法脫硫的合成氣凈化方法的裝置的一個(gè)優(yōu)選實(shí)施例中,所述吸附床為固定式吸附床。在本發(fā)明實(shí)現(xiàn)上述第一種結(jié)合耐硫變換和循環(huán)流化床熱法脫硫的合成氣凈化方法的裝置的一個(gè)優(yōu)選實(shí)施例中,所述脫除汞和氯化物裝置為保護(hù)床。作為本發(fā)明第三方面的應(yīng)用,本發(fā)明的第一種結(jié)合耐硫變換和循環(huán)流化床熱法脫硫的合成氣凈化方法可以用于IGCC、合成氨、甲醇合成、F-T合成烴類油類產(chǎn)品、合成氣制SNG、生產(chǎn)氫氣、合成氣制乙二醇的粗合成氣的凈化工藝。作為本發(fā)明第一方面的第二種結(jié)合耐硫變換和循環(huán)流化床熱法脫硫的合成氣凈化方法,其是將經(jīng)過煤或其它含碳材料的氣化產(chǎn)生第六粗合成氣送入一水激冷洗滌裝置進(jìn)行水激冷洗滌形成第七粗合成氣送入到耐硫變換反應(yīng)系統(tǒng);在所述耐硫變換反應(yīng)系統(tǒng)內(nèi),第七粗合成氣發(fā)生如下反應(yīng)CO+H2O→CO2+H2形成第八粗合成氣送出;送出的第八粗合成氣進(jìn)入熱量回收裝置進(jìn)行降溫形成第九粗合成氣送出;送出的第九粗合成氣進(jìn)入第三換熱器,與進(jìn)入第三換熱器的第八脫硫后的合成氣換熱后形成第十粗合成氣送出;送出的第十粗合成氣進(jìn)入到循環(huán)流化床脫硫系統(tǒng)的吸附反應(yīng)脫硫段,與進(jìn)入循環(huán)流化床脫硫系統(tǒng)的吸附反應(yīng)脫硫段的再生固體吸附劑混合反應(yīng),混合反應(yīng)過程中所述再生固體吸附劑中的活性金屬氧化物MO與第十粗合成氣中的含有硫雜質(zhì)反應(yīng),產(chǎn)生載有硫的吸附劑MS,具體反應(yīng)式如下:H2S+MO→MS+H2OCOS+MO→CO2+MS其中,M為存在于再生固體吸附劑中的金屬;混合反應(yīng)過程后形成的含固體吸附顆粒的脫硫后的合成氣經(jīng)過循環(huán)流化床脫硫系統(tǒng)的吸附反應(yīng)脫硫段中的旋風(fēng)分離器旋風(fēng)分離后形成第九脫硫后的合成氣,所述的第九脫硫后的合成氣經(jīng)過循環(huán)流化床脫硫系統(tǒng)的吸附反應(yīng)脫硫段中的過濾器過濾后形成所述的第八脫硫后的合成氣送入到第三換熱器內(nèi),經(jīng)過與進(jìn)入第三換熱器內(nèi)的第九粗合成氣換熱后形成所述的第十脫硫后的合成氣送入一可再生脫NH3/HCN裝置中脫除第十脫硫后的合成氣中的NH3/HCN形成第十一脫硫后的合成氣,所述第十一脫硫后的合成氣送入一冷卻裝置中進(jìn)行冷卻形成第十二脫硫后的合成氣送出;經(jīng)過循環(huán)流化床脫硫系統(tǒng)的吸附反應(yīng)脫硫段中的旋風(fēng)分離器旋風(fēng)分離后的載有硫的吸附劑MS進(jìn)入到循環(huán)流化床脫硫系統(tǒng)的再生段中,與進(jìn)入循環(huán)流化床脫硫系統(tǒng)的再生段的再生空氣或O2與N2的混合氣體混合反應(yīng),使得載有硫的吸附劑MS得以再生形成所述的再生固體吸附劑,具體反應(yīng)式如下:MS+3/2O2→MO+SO2;混合反應(yīng)后形成的含有所述的再生固體吸附劑的第五富SO2的氣體進(jìn)入到循環(huán)流化床脫硫系統(tǒng)的再生段中的旋風(fēng)分離器中進(jìn)行旋風(fēng)分離,旋風(fēng)分離后的第六富SO2的氣體經(jīng)過循環(huán)流化床脫硫系統(tǒng)的再生段的過濾器過濾后所形成的第七富SO2的氣體送入第四換熱器,與進(jìn)入到所述第四換熱器內(nèi)的再生所需要的所述的再生空氣或O2與N2的混合氣體進(jìn)行換熱形成第八富SO2的氣體送出至下游去生產(chǎn)硫酸或者單質(zhì)硫;旋風(fēng)分離后的所述的再生固體吸附劑送入到循環(huán)流化床脫硫系統(tǒng)的吸附反應(yīng)脫硫段中。在本發(fā)明第二種結(jié)合耐硫變換和循環(huán)流化床熱法脫硫的合成氣凈化方法的一個(gè)優(yōu)選實(shí)施例中,所述送出的第九粗合成氣進(jìn)入熱量回收裝置進(jìn)行降溫后再分出第十一粗合成氣進(jìn)行液相吸收脫硫脫碳后得到凈化氣。在本發(fā)明第二種結(jié)合耐硫變換和循環(huán)流化床熱法脫硫的合成氣凈化方法的一個(gè)優(yōu)選實(shí)施例中,所述凈化氣送入一提氫裝置經(jīng)過提氫后得到氫氣送出。在本發(fā)明第二種結(jié)合耐硫變換和循環(huán)流化床熱法脫硫的合成氣凈化方法的一個(gè)優(yōu)選實(shí)施例中,所述冷卻裝置送出第十二脫硫后的合成氣送入一PSA凈化工段凈化后得到氫氣送出。在本發(fā)明第二種結(jié)合耐硫變換和循環(huán)流化床熱法脫硫的合成氣凈化方法的一個(gè)優(yōu)選實(shí)施例中,所述凈化氣送入一提氫裝置經(jīng)過提氫后得到氫氣送出;所述冷卻裝置送出第十二脫硫后的合成氣送入一PSA凈化工段凈化后得到氫氣送出。在本發(fā)明第二種結(jié)合耐硫變換和循環(huán)流化床熱法脫硫的合成氣凈化方法的一個(gè)優(yōu)選實(shí)施例中,所述凈化氣送入一提氫裝置經(jīng)過提氫后得到氫氣送出;所述冷卻裝置送出第十二脫硫后的合成氣送入一PSA凈化工段凈化后得到氫氣送出,兩股氫氣送入一合成氨裝置中,補(bǔ)充N2得到產(chǎn)品氨。在本發(fā)明第二種結(jié)合耐硫變換和循環(huán)流化床熱法脫硫的合成氣凈化方法的一個(gè)優(yōu)選實(shí)施例中,所述經(jīng)過煤或其它含碳材料的氣化產(chǎn)生第六粗合成氣為水煤漿氣化、粉煤氣化或碎煤固定床氣化產(chǎn)生第六粗合成氣。在本發(fā)明第二種結(jié)合耐硫變換和循環(huán)流化床熱法脫硫的合成氣凈化方法的一個(gè)優(yōu)選實(shí)施例中,所述第七粗合成氣的溫度為180-250℃。在本發(fā)明第二種結(jié)合耐硫變換和循環(huán)流化床熱法脫硫的合成氣凈化方法的一個(gè)優(yōu)選實(shí)施例中,所述耐硫變換反應(yīng)系統(tǒng)使用絕熱耐硫變換反應(yīng)器或等溫耐硫變換反應(yīng)器或本申請人申請的中國專利號ZL201210040295.6、發(fā)明名稱為帶有支撐式槽孔板分布器的徑向或軸徑向固定床反應(yīng)器或本申請人申請的中國專利號ZL201320176372.0、發(fā)明名稱為一種將催化劑置于換熱管之間的等溫固定床反應(yīng)器或本申請人申請的中國專利號ZL200910056432.4、發(fā)明名稱為分流式等溫耐硫變換工藝及其設(shè)備;所述帶有支撐式槽孔板分布器的徑向或軸徑向固定床反應(yīng)器,包括承壓殼體和設(shè)置在所述承壓殼體內(nèi)且與承壓殼體同軸的催化劑外框和氣體收集中心管,所述承壓殼體上設(shè)置有氣體進(jìn)口和氣體出口,所述催化劑外框由支撐在承壓殼體內(nèi)壁上的支撐式槽孔板分布器構(gòu)成;所述支撐式槽孔板分布器有由規(guī)格一致的若干槽孔分布板相互搭接構(gòu)成;所述的槽孔分布板采用角鋼和支座支撐在承壓殼體的內(nèi)壁上,所述角鋼與支座之間采用螺栓連接,所述支座固定在承壓殼體的內(nèi)壁上,所述槽孔分布板與承壓殼體之間保留一定的弧形間隙;所述槽孔分布板為其上開設(shè)有密集槽孔的弧形長條板;所述一種將催化劑裝于換熱管之間的等溫固定床反應(yīng)器,包括承壓殼體、安裝在承壓殼體內(nèi)的多個(gè)換熱管;在所述承壓殼體上設(shè)有氣體進(jìn)口、換熱介質(zhì)出口、氣體出口、換熱介質(zhì)進(jìn)口和催化劑卸料口;所述換熱管的兩端分別與所述換熱介質(zhì)出口和換熱介質(zhì)進(jìn)口相連接;所述多個(gè)換熱管之間存在空隙形成催化劑填充區(qū),并且氣體進(jìn)口、換熱管之間的空隙以及氣體出口形成氣體通道;所述分流式等溫耐硫變換設(shè)備,至少包括一第一變換反應(yīng)器和一鍋爐給水預(yù)熱器以及熱回收冷卻系統(tǒng),第一變換反應(yīng)器的第一變換氣出口管與鍋爐給水預(yù)熱器進(jìn)氣口連接,鍋爐給水預(yù)熱器出氣口與所述熱回收冷卻系統(tǒng)連接;第一變換反應(yīng)器的原料氣入口接原料煤氣;所述的分流式等溫耐硫變換設(shè)備還包括一汽包,所述第一變換反應(yīng)器為等溫變換反應(yīng)器,所述第一變換反應(yīng)器通過一由泵及管線構(gòu)成的強(qiáng)制循環(huán)移熱回路與汽包連接,所述鍋爐給水預(yù)熱器的鍋爐給水管與汽包連接,向汽包輸送預(yù)熱后的鍋爐給水;原料煤氣配入過熱蒸汽,將溫度提高至200-300℃后通過第一變換反應(yīng)器的原料氣入口進(jìn)入第一變換反應(yīng)器進(jìn)行變換反應(yīng),產(chǎn)出第一變換氣,第一變換氣通過第一變換氣出口管送入所述鍋爐給水預(yù)熱器回收熱量后,再送入所述熱回收冷卻系統(tǒng)分離出變換氣和冷凝液;第一變換反應(yīng)器副產(chǎn)中壓飽和蒸汽,副產(chǎn)中壓飽和蒸汽通過強(qiáng)制循環(huán)移熱回路送入汽包進(jìn)行分離,所述汽包分離出的中壓飽和蒸汽通過汽包的蒸汽出口管送出;或者,所述分流式等溫耐硫變換設(shè)備,至少包括一第一變換反應(yīng)器和一鍋爐給水預(yù)熱器以及熱回收冷卻系統(tǒng),第一變換反應(yīng)器的第一變換氣出口管與鍋爐給水預(yù)熱器進(jìn)氣口連接,鍋爐給水預(yù)熱器出氣口與所述熱回收冷卻系統(tǒng)連接;第一變換反應(yīng)器的原料氣入口接原料煤氣;所述的分流式等溫耐硫變換設(shè)備還包括一第二變換反應(yīng)器、一蒸汽過熱器、一汽包,其中第一變換反應(yīng)器為絕熱變換反應(yīng)器,第二變換反應(yīng)器為等溫變換反應(yīng)器,其中第一變換反應(yīng)器的第一變換氣出口管與蒸汽過熱器的第一變換氣入口管直接,蒸汽過熱器的第一變換氣輸送管與第二變換反應(yīng)器的原料氣入口連接,第二變換反應(yīng)器的原料氣入口還接原料煤氣;所述第二變換反應(yīng)器通過一由泵及管線構(gòu)成的強(qiáng)制循環(huán)移熱回路與汽包連接,第二變換反應(yīng)器的第二變換氣出口管與鍋爐給水預(yù)熱器進(jìn)氣口連接,所述鍋爐給水預(yù)熱器的鍋爐給水管與汽包連接,向汽包輸送預(yù)熱后的鍋爐給水;汽包的蒸汽出口管接蒸汽過熱器的中壓飽和蒸汽入口,蒸汽過熱器的中壓過熱蒸汽出口管送出中壓過熱蒸汽;或者,所述分流式等溫耐硫變換設(shè)備,至少包括一第一變換反應(yīng)器和一鍋爐給水預(yù)熱器以及熱回收冷卻系統(tǒng),第一變換反應(yīng)器的第一變換氣出口管與鍋爐給水預(yù)熱器進(jìn)氣口連接,鍋爐給水預(yù)熱器出氣口與所述熱回收冷卻系統(tǒng)連接;第一變換反應(yīng)器的原料氣入口接原料煤氣;所述的分流式等溫耐硫變換設(shè)備還包括一第二變換反應(yīng)器、一蒸汽過熱器、一廢熱鍋爐,其中第一變換反應(yīng)器和第二變換反應(yīng)器均為絕熱變換反應(yīng)器,其中第一變換反應(yīng)器的第一變換氣出口管與蒸汽過熱器的第一變換氣入口管直接,蒸汽過熱器的第一變換氣輸送管與第二變換反應(yīng)器的原料氣入口連接,第二變換反應(yīng)器的原料氣入口還接原料煤氣;所述第二變換反應(yīng)器的第二變換氣出口管與廢熱鍋爐的第二變換氣入口管直連,廢熱鍋爐的第二變換氣輸送管與鍋爐給水預(yù)熱器進(jìn)氣口連接,所述鍋爐給水預(yù)熱器的鍋爐給水管與廢熱鍋爐的給水口連接,向廢熱鍋爐輸送預(yù)熱后的鍋爐給水;廢熱鍋爐的蒸汽出口管接蒸汽過熱器的中壓飽和蒸汽入口,蒸汽過熱器的中壓過熱蒸汽出口管送出中壓過熱蒸汽。在本發(fā)明第二種結(jié)合耐硫變換和循環(huán)流化床熱法脫硫的合成氣凈化方法的一個(gè)優(yōu)選實(shí)施例中,所述第八粗合成氣的溫度為270-450℃。在本發(fā)明第二種結(jié)合耐硫變換和循環(huán)流化床熱法脫硫的合成氣凈化方法的一個(gè)優(yōu)選實(shí)施例中,所述第九粗合成氣的溫度為75-200℃。在本發(fā)明第二種結(jié)合耐硫變換和循環(huán)流化床熱法脫硫的合成氣凈化方法的一個(gè)優(yōu)選實(shí)施例中,所述第十粗合成氣的溫度為300-550℃。在本發(fā)明第二種結(jié)合耐硫變換和循環(huán)流化床熱法脫硫的合成氣凈化方法的一個(gè)優(yōu)選實(shí)施例中,所述再生固體吸附劑中的活性金屬氧化物MO與第十粗合成氣中的含有硫雜質(zhì)反應(yīng)時(shí)的溫度為320-580℃。在本發(fā)明第二種結(jié)合耐硫變換和循環(huán)流化床熱法脫硫的合成氣凈化方法的一個(gè)優(yōu)選實(shí)施例中,所述第九脫硫后的合成氣中的硫含量低至0.5-5ppmv。在本發(fā)明第二種結(jié)合耐硫變換和循環(huán)流化床熱法脫硫的合成氣凈化方法的一個(gè)優(yōu)選實(shí)施例中,所述第十脫硫后的合成氣的溫度為170-230℃。在本發(fā)明第二種結(jié)合耐硫變換和循環(huán)流化床熱法脫硫的合成氣凈化方法的一個(gè)優(yōu)選實(shí)施例中,所述第十二脫硫后的合成氣送入下游的脫二氧化碳單元裝置中,以脫除其中的二氧化碳。在本發(fā)明第二種結(jié)合耐硫變換和循環(huán)流化床熱法脫硫的合成氣凈化方法的一個(gè)優(yōu)選實(shí)施例中,所述脫二氧化碳單元裝置為液相吸收脫二氧化碳單元裝置或干法化學(xué)吸附脫二氧化碳單元裝置。在本發(fā)明第二種結(jié)合耐硫變換和循環(huán)流化床熱法脫硫的合成氣凈化方法的一個(gè)優(yōu)選實(shí)施例中,所述可再生脫NH3/HCN裝置為吸附床。在本發(fā)明第二種結(jié)合耐硫變換和循環(huán)流化床熱法脫硫的合成氣凈化方法的一個(gè)優(yōu)選實(shí)施例中,所述吸附床為固定式吸附床。在本發(fā)明第二種結(jié)合耐硫變換和循環(huán)流化床熱法脫硫的合成氣凈化方法的一個(gè)優(yōu)選實(shí)施例中,所述第五富SO2的氣體的溫度為650-750℃。在本發(fā)明第二種結(jié)合耐硫變換和循環(huán)流化床熱法脫硫的合成氣凈化方法的一個(gè)優(yōu)選實(shí)施例中,所述第八富SO2的氣體的溫度為330-530℃。在本發(fā)明第二種結(jié)合耐硫變換和循環(huán)流化床熱法脫硫的合成氣凈化方法的一個(gè)優(yōu)選實(shí)施例中,所述進(jìn)入所述循環(huán)流化床脫硫系統(tǒng)的再生段的再生空氣或O2與N2的混合氣體的溫度為450-550℃。在本發(fā)明第二種結(jié)合耐硫變換和循環(huán)流化床熱法脫硫的合成氣凈化方法的一個(gè)優(yōu)選實(shí)施例中,所述第八富SO2的氣體送出至下游的硫酸裝置去生產(chǎn)硫酸。在本發(fā)明第二種結(jié)合耐硫變換和循環(huán)流化床熱法脫硫的合成氣凈化方法的一個(gè)優(yōu)選實(shí)施例中,所述第八富SO2的氣體送出至下游的硫回收裝置生產(chǎn)硫磺。在本發(fā)明第二種結(jié)合耐硫變換和循環(huán)流化床熱法脫硫的合成氣凈化方法的一個(gè)優(yōu)選實(shí)施例中,所述M為存在于再生固體吸附劑中的金屬。例如Zn。作為本發(fā)明第一方面的實(shí)現(xiàn)上述第二種結(jié)合耐硫變換和循環(huán)流化床熱法脫硫的合成氣凈化方法的裝置,包括一水激冷洗滌裝置,所述水激冷洗滌裝置具有一粗合成氣輸入口和粗合成氣輸出口,該水激冷洗滌裝置的粗合成氣輸入口通過一第六粗合成氣輸送管線連接一煤氣化裝置;一耐硫變換反應(yīng)系統(tǒng),該耐硫變換反應(yīng)系統(tǒng)具有一粗合成氣輸入口和粗合成氣輸出口,所述耐硫變換反應(yīng)系統(tǒng)的粗合成氣輸入口通過一第七粗合成氣輸送管線連接所述水激冷洗滌裝置的粗合成氣輸出口;一熱量回收裝置,該熱量回收裝置具有一粗合成氣輸入口和粗合成氣輸出口,所述熱量回收裝置的粗合成氣輸入口通過一第八粗合成氣輸送管線連接所述耐硫變換反應(yīng)系統(tǒng)的粗合成氣輸出口;一第三換熱器,所述第三換熱器具有一粗合成氣輸入口、一粗合成氣輸出口、一脫硫后的合成氣輸入口和一脫硫后的合成氣輸出口,所述第三換熱器的粗合成氣輸入口通過一第九粗合成氣輸送管線連接所述熱量回收裝置的粗合成氣輸出口;一循環(huán)流化床,該循環(huán)流化床具有一循環(huán)流化床脫硫段和循環(huán)流化床再生段,所述循環(huán)流化床脫硫段具有一粗合成氣輸入口和脫硫后的合成氣輸出口;循環(huán)流化床再生段具有一再生空氣或O2與N2的混合氣體入口和一富SO2的氣體出口,所述循環(huán)流化床脫硫段的粗合成氣輸入口通過一第十粗合成氣輸送管線連接所述的第三換熱器的粗合成氣輸出口;所述循環(huán)流化床脫硫段的脫硫后的合成氣輸出口通過一第八脫硫后的合成氣輸送管線與所述第三換熱器的脫硫后的合成氣輸入口連接;一第三過濾器,所述第三過濾器具有一脫硫后的合成氣輸入口和一脫硫后的合成氣輸出口,所述第三過濾器的脫硫后的合成氣輸入口通過一第九脫硫后的合成氣輸送管線與所述循環(huán)流化床的循環(huán)流化床脫硫段的脫硫后的合成氣輸出口連接,所述第三過濾器的脫硫后的合成氣輸出口通過一第八脫硫后的合成氣輸送管線與所述第三換熱器的脫硫后的合成氣輸入口連接;一第四換熱器,所述第四換熱器具有一富SO2的氣體入口、富SO2的氣體出口、再生空氣或O2與N2的混合氣體入口、再生空氣或O2與N2的混合氣體出口,所述第四換熱器的富SO2的氣體入口通過一第七富SO2的氣體輸送管線連接所述循環(huán)流化床再生段的富SO2的氣體出口,所述第四換熱器的再生空氣或O2與N2的混合氣體入口連接空氣源或O2與N2的混合氣體源,所述第四換熱器的再生空氣或O2與N2的混合氣體出口通過再生空氣或O2與N2的混合氣體輸送管線連接所述循環(huán)流化床再生段的再生空氣或O2與N2的混合氣體入口;一硫酸裝置或硫回收裝置,所述硫酸裝置或硫回收裝置具有一富SO2的氣體入口、一硫酸輸出口或硫磺輸出口,所述硫酸裝置或硫回收裝置的富SO2的氣體入口通過第八富SO2的氣體輸送管線連接至所述第四換熱器的富SO2的氣體出口;所述硫酸裝置或硫回收裝置的硫酸輸出口或硫磺輸出口輸出硫酸或硫磺;一可再生脫NH3/HCN裝置,所述可再生脫NH3/HCN裝置具有脫硫后的合成氣入口和脫硫后的合成氣出口,所述再生脫NH3/HCN裝置的脫硫后的合成氣入口通過一第十脫硫后的合成氣輸送管線與所述第三換熱器的脫硫后的合成氣輸出口連接;一冷卻裝置,所述冷卻裝置具有脫硫后的合成氣入口和脫硫后的合成氣出口,所述冷卻裝置的脫硫后的合成氣入口通過一第十一脫硫后的合成氣輸送管線與所述可再生脫NH3/HCN裝置的脫硫后的合成氣出口連接,所述冷卻裝置的脫硫后的合成氣出口通過一第十二脫硫后的合成氣輸送管線與下游的脫二氧化碳單元裝置連接。在本發(fā)明實(shí)現(xiàn)上述第二種結(jié)合耐硫變換和循環(huán)流化床熱法脫硫的合成氣凈化方法的裝置的一個(gè)優(yōu)選實(shí)施例中,所述熱量回收裝置還具有另一粗合成氣輸出口并還包括一液相吸收脫硫脫碳裝置,所述液相吸收脫硫脫碳裝置具有粗合成氣輸入口和凈化氣輸出口,所述液相吸收脫硫脫碳裝置的粗合成氣輸入口通過一第十一粗合成氣輸送管線與所述熱量回收裝置的另一粗合成氣輸出口連接,所述液相吸收脫硫脫碳裝置的凈化氣輸出口送出凈化合成氣。在本發(fā)明實(shí)現(xiàn)上述第二種結(jié)合耐硫變換和循環(huán)流化床熱法脫硫的合成氣凈化方法的裝置一個(gè)優(yōu)選實(shí)施例中,還包括一提氫裝置,所述提氫裝置具有一凈化氣輸入口和一氫氣出口,所述提氫裝置的凈化氣輸入口通過凈化氣輸送管線與所述液相吸收脫硫脫碳裝置的凈化氣輸出口連接,所述提氫裝置的氫氣出口送出氫氣。在本發(fā)明實(shí)現(xiàn)上述第二種結(jié)合耐硫變換和循環(huán)流化床熱法脫硫的合成氣凈化方法的裝置一個(gè)優(yōu)選實(shí)施例中,還包括一PSA凈化工段,所述PSA凈化工段具有一脫硫后的合成氣輸入口和一氫氣出口,所述PSA凈化工段的脫硫后的合成氣輸入口通過所述第十二脫硫后的合成氣輸送管線與所述冷卻裝置的脫硫后的合成氣出口連接,所述PSA凈化工段的氫氣出口送出氫氣。在本發(fā)明實(shí)現(xiàn)上述第二種結(jié)合耐硫變換和循環(huán)流化床熱法脫硫的合成氣凈化方法的裝置一個(gè)優(yōu)選實(shí)施例中,還包括一提氫裝置、PSA凈化工段和合成氨裝置,所述提氫裝置具有一凈化氣輸入口和一氫氣出口,所述PSA凈化工段具有一脫硫后的合成氣輸入口和一氫氣出口,所述合成氨裝置具有兩個(gè)氫氣入口、一個(gè)N2補(bǔ)充口和一個(gè)產(chǎn)品氨輸出口;其中所述提氫裝置的凈化氣輸入口通過凈化氣輸送管線與所述液相吸收脫硫脫碳裝置的凈化氣輸出口連接,所述提氫裝置的氫氣出口通過一氫氣輸送管線與所述合成氨裝置的一個(gè)氫氣輸入口連接;所述PSA凈化工段的脫硫后的合成氣輸入口通過所述第十二脫硫后的合成氣輸送管線與所述冷卻裝置的脫硫后的合成氣出口連接,所述PSA凈化工段的氫氣出口通過另一氫氣輸送管線與所述合成氨裝置的另一個(gè)氫氣輸入口連接;所述合成氨裝置的N2補(bǔ)充口通過N2輸送管線連接N2氣源;所述合成氨裝置的產(chǎn)品氨輸出口送出產(chǎn)品氨。在本發(fā)明實(shí)現(xiàn)上述第二種結(jié)合耐硫變換和循環(huán)流化床熱法脫硫的合成氣凈化方法的裝置的一個(gè)優(yōu)選實(shí)施例中,所述煤氣化裝置為水煤漿氣化裝置、粉煤氣化裝置或碎煤固定床氣化裝置。在本發(fā)明實(shí)現(xiàn)上述第二種結(jié)合耐硫變換和循環(huán)流化床熱法脫硫的合成氣凈化方法的裝置的一個(gè)優(yōu)選實(shí)施例中,所述耐硫變換反應(yīng)系統(tǒng)使用絕熱耐硫變換反應(yīng)器或等溫變換反應(yīng)器或本申請人申請的中國專利號ZL201210040295.6、發(fā)明名稱為帶有支撐式槽孔板分布器的徑向或軸徑向固定床反應(yīng)器或本申請人申請的中國專利號ZL201320176372.0、發(fā)明名稱為一種將催化劑置于換熱管之間的等溫固定床反應(yīng)器或本申請人申請的中國專利號ZL200910056432.4、發(fā)明名稱為分流式等溫耐硫變換工藝及其設(shè)備;所述帶有支撐式槽孔板分布器的徑向或軸徑向固定床反應(yīng)器,包括承壓殼體和設(shè)置在所述承壓殼體內(nèi)且與承壓殼體同軸的催化劑外框和氣體收集中心管,所述承壓殼體上設(shè)置有氣體進(jìn)口和氣體出口,所述催化劑外框由支撐在承壓殼體內(nèi)壁上的支撐式槽孔板分布器構(gòu)成;所述支撐式槽孔板分布器有由規(guī)格一致的若干槽孔分布板相互搭接構(gòu)成;所述的槽孔分布板采用角鋼和支座支撐在承壓殼體的內(nèi)壁上,所述角鋼與支座之間采用螺栓連接,所述支座固定在承壓殼體的內(nèi)壁上,所述槽孔分布板與承壓殼體之間保留一定的弧形間隙;所述槽孔分布板為其上開設(shè)有密集槽孔的弧形長條板;所述一種將催化劑裝于換熱管之間的等溫固定床反應(yīng)器,包括承壓殼體、安裝在承壓殼體內(nèi)的多個(gè)換熱管;在所述承壓殼體上設(shè)有氣體進(jìn)口、換熱介質(zhì)出口、氣體出口、換熱介質(zhì)進(jìn)口和催化劑卸料口;所述換熱管的兩端分別與所述換熱介質(zhì)出口和換熱介質(zhì)進(jìn)口相連接;所述多個(gè)換熱管之間存在空隙形成催化劑填充區(qū),并且氣體進(jìn)口、換熱管之間的空隙以及氣體出口形成氣體通道;所述分流式等溫耐硫變換設(shè)備,至少包括一第一變換反應(yīng)器和一鍋爐給水預(yù)熱器以及熱回收冷卻系統(tǒng),第一變換反應(yīng)器的第一變換氣出口管與鍋爐給水預(yù)熱器進(jìn)氣口連接,鍋爐給水預(yù)熱器出氣口與所述熱回收冷卻系統(tǒng)連接;第一變換反應(yīng)器的原料氣入口接原料煤氣;所述的分流式等溫耐硫變換設(shè)備還包括一汽包,所述第一變換反應(yīng)器為等溫變換反應(yīng)器,所述第一變換反應(yīng)器通過一由泵及管線構(gòu)成的強(qiáng)制循環(huán)移熱回路與汽包連接,所述鍋爐給水預(yù)熱器的鍋爐給水管與汽包連接,向汽包輸送預(yù)熱后的鍋爐給水;原料煤氣配入過熱蒸汽,將溫度提高至200-300℃后通過第一變換反應(yīng)器的原料氣入口進(jìn)入第一變換反應(yīng)器進(jìn)行變換反應(yīng),產(chǎn)出第一變換氣,第一變換氣通過第一變換氣出口管送入所述鍋爐給水預(yù)熱器回收熱量后,再送入所述熱回收冷卻系統(tǒng)分離出變換氣和冷凝液;第一變換反應(yīng)器副產(chǎn)中壓飽和蒸汽,副產(chǎn)中壓飽和蒸汽通過強(qiáng)制循環(huán)移熱回路送入汽包進(jìn)行分離,所述汽包分離出的中壓飽和蒸汽通過汽包的蒸汽出口管送出;或者,所述分流式等溫耐硫變換設(shè)備,至少包括一第一變換反應(yīng)器和一鍋爐給水預(yù)熱器以及熱回收冷卻系統(tǒng),第一變換反應(yīng)器的第一變換氣出口管與鍋爐給水預(yù)熱器進(jìn)氣口連接,鍋爐給水預(yù)熱器出氣口與所述熱回收冷卻系統(tǒng)連接;第一變換反應(yīng)器的原料氣入口接原料煤氣;所述的分流式等溫耐硫變換設(shè)備還包括一第二變換反應(yīng)器、一蒸汽過熱器、一汽包,其中第一變換反應(yīng)器為絕熱變換反應(yīng)器,第二變換反應(yīng)器為等溫變換反應(yīng)器,其中第一變換反應(yīng)器的第一變換氣出口管與蒸汽過熱器的第一變換氣入口管直接,蒸汽過熱器的第一變換氣輸送管與第二變換反應(yīng)器的原料氣入口連接,第二變換反應(yīng)器的原料氣入口還接原料煤氣;所述第二變換反應(yīng)器通過一由泵及管線構(gòu)成的強(qiáng)制循環(huán)移熱回路與汽包連接,第二變換反應(yīng)器的第二變換氣出口管與鍋爐給水預(yù)熱器進(jìn)氣口連接,所述鍋爐給水預(yù)熱器的鍋爐給水管與汽包連接,向汽包輸送預(yù)熱后的鍋爐給水;汽包的蒸汽出口管接蒸汽過熱器的中壓飽和蒸汽入口,蒸汽過熱器的中壓過熱蒸汽出口管送出中壓過熱蒸汽;或者,所述分流式等溫耐硫變換設(shè)備,至少包括一第一變換反應(yīng)器和一鍋爐給水預(yù)熱器以及熱回收冷卻系統(tǒng),第一變換反應(yīng)器的第一變換氣出口管與鍋爐給水預(yù)熱器進(jìn)氣口連接,鍋爐給水預(yù)熱器出氣口與所述熱回收冷卻系統(tǒng)連接;第一變換反應(yīng)器的原料氣入口接原料煤氣;所述的分流式等溫耐硫變換設(shè)備還包括一第二變換反應(yīng)器、一蒸汽過熱器、一廢熱鍋爐,其中第一變換反應(yīng)器和第二變換反應(yīng)器均為絕熱變換反應(yīng)器,其中第一變換反應(yīng)器的第一變換氣出口管與蒸汽過熱器的第一變換氣入口管直接,蒸汽過熱器的第一變換氣輸送管與第二變換反應(yīng)器的原料氣入口連接,第二變換反應(yīng)器的原料氣入口還接原料煤氣;所述第二變換反應(yīng)器的第二變換氣出口管與廢熱鍋爐的第二變換氣入口管直連,廢熱鍋爐的第二變換氣輸送管與鍋爐給水預(yù)熱器進(jìn)氣口連接,所述鍋爐給水預(yù)熱器的鍋爐給水管與廢熱鍋爐的給水口連接,向廢熱鍋爐輸送預(yù)熱后的鍋爐給水;廢熱鍋爐的蒸汽出口管接蒸汽過熱器的中壓飽和蒸汽入口,蒸汽過熱器的中壓過熱蒸汽出口管送出中壓過熱蒸汽。在本發(fā)明實(shí)現(xiàn)上述第二種結(jié)合耐硫變換和循環(huán)流化床熱法脫硫的合成氣凈化方法的裝置的一個(gè)優(yōu)選實(shí)施例中,所述脫二氧化碳單元裝置為液相吸收脫二氧化碳單元裝置或干法化學(xué)吸附脫二氧化碳單元裝置。在本發(fā)明實(shí)現(xiàn)上述第二種結(jié)合耐硫變換和循環(huán)流化床熱法脫硫的合成氣凈化方法的裝置的一個(gè)優(yōu)選實(shí)施例中,所述可再生脫NH3/HCN裝置為吸附床。在本發(fā)明實(shí)現(xiàn)上述第二種結(jié)合耐硫變換和循環(huán)流化床熱法脫硫的合成氣凈化方法的裝置的一個(gè)優(yōu)選實(shí)施例中,所述吸附床為固定式吸附床。本發(fā)明第二種結(jié)合耐硫變換和循環(huán)流化床熱法脫硫的合成氣凈化方法可以用于IGCC、合成氨、甲醇合成、F-T合成烴類油類產(chǎn)品、合成氣制SNG、生產(chǎn)氫氣、合成氣制乙二醇的粗合成氣的凈化工藝。由于采用了上述技術(shù)方案,本發(fā)明具有如下特點(diǎn):(1)本發(fā)明可以適用于多種煤氣化方式產(chǎn)的粗合成氣的凈化,例如水煤漿氣化、粉煤氣化、碎煤固定床氣化。(2)本發(fā)明可以用來改造采用耐硫變換技術(shù)結(jié)合液相吸收法脫硫工藝凈化粗合成氣的增產(chǎn)工況,可以使得已有耐硫變換系統(tǒng)內(nèi)的冷卻裝置和液相吸收法脫硫能夠保持在原工況下操作,增產(chǎn)部分氣體的提溫和脫硫均可由新增循環(huán)流化床系統(tǒng)完成,做到改造對舊系統(tǒng)的影響最小,可大大減少改造的設(shè)備和降低投資費(fèi)用,改造工作量最少最可靠。(3)本發(fā)明中的耐硫變換反應(yīng)工藝,可以是全部變換或部分變換工藝,可以選擇絕熱變換流程,也可以選擇等溫變換流程。(4)本發(fā)明從合成氣中脫二氧化碳的單元裝置可使用液相吸收法或干法化學(xué)吸附,來進(jìn)一步凈化合成氣。(5)本發(fā)明粗合成氣經(jīng)過一氧化碳耐硫變換反應(yīng),熱量回收后不需要經(jīng)過水冷和洗滌降低溫度,而是以熱狀態(tài)進(jìn)入循環(huán)流化床脫硫系統(tǒng)。(6)本發(fā)明經(jīng)過循環(huán)流化床熱法脫硫后的高溫凈化氣可用來加熱一氧化碳耐硫變換反應(yīng)后的合成氣,將粗合成氣的溫度提升至循環(huán)流化床脫硫入口所需的溫度。(7)本發(fā)明經(jīng)過循環(huán)流化床再生后的高溫富SO2氣體與再生空氣或O2與N2的混合氣換熱,使得再生空氣溫度升高至再生反應(yīng)所需要的溫度,同時(shí)高溫富SO2氣體溫度降低。(8)本發(fā)明使用循環(huán)流化床熱法脫除合成氣中的雜質(zhì),整個(gè)工藝過程在300-600℃,保持了煤氣化產(chǎn)生的合成氣的高位熱值,避免了合成氣下游利用再補(bǔ)充熱量,有效提高了合成氣的熱效率。(9)本發(fā)明使用上述工藝過程脫除粗合成氣中的雜質(zhì),粗合成氣處理能力大。(10)本發(fā)明工藝流程簡單,設(shè)備投資少。(11)本發(fā)明工藝過程不受到反應(yīng)體系的壓力影響,整個(gè)循環(huán)流化床脫硫體系壓降低,動力損失少。(12)本發(fā)明工藝過程使用固體吸附劑脫除粗合成氣中的含硫化合物、輕質(zhì)芳烴、砷及其化合物、硒及其化合物、氰化物、氨,并可選地增加保護(hù)床除去合成氣中的汞和氯化氫等其他微量雜質(zhì)。整個(gè)工藝合成氣脫除雜質(zhì)流程比傳統(tǒng)合成氣凈化過程中的水量消耗大幅度降低,同時(shí)減少了微量雜質(zhì)組分對水的污染。(13)本發(fā)明工藝過程使用循環(huán)流化床進(jìn)行熱法脫粗合成氣中的含硫雜質(zhì),例如H2S和COS,使合成氣中的硫含量降低至0.5-5ppmv。(14)工藝過程中的循環(huán)流化床脫硫系統(tǒng)類似于流化催化裂化工藝系統(tǒng),可使得固體吸附劑有效的再生循環(huán)。本發(fā)明通過耐硫變換與循環(huán)流化床熱脫硫技術(shù)的合理配置,可以避免上述液相吸收法脫硫和固定床吸附劑脫硫的缺點(diǎn),同時(shí)通過工藝參數(shù)和能量的合理優(yōu)化,達(dá)到高溫脫除粗合成氣中含硫化合物、砷及其化合物、硒及其化合物、輕質(zhì)芳烴的目的,通過固定床吸附劑脫除合成氣中的氨和氰化物,也可選用保護(hù)床裝置除去汞、氯化氫等雜質(zhì),最終實(shí)現(xiàn)粗合成氣的干法凈化。本發(fā)明旨在提供一種新的耐硫變換技術(shù)結(jié)合循環(huán)流化床熱法脫硫技術(shù)工藝脫除合成氣中的含硫化合物、砷及其化合物、硒及其化合物、輕質(zhì)芳烴,通過固定床吸附劑脫除合成氣中的氨和氰化物,通過可選地增加保護(hù)床裝置脫除其他微量雜質(zhì),雜質(zhì)可包括但不限于汞和氯化氫,實(shí)現(xiàn)粗合成氣的凈化。本發(fā)明可解決傳統(tǒng)的耐硫變換工藝后配置液相吸收法脫硫工藝中存在的合成氣熱量利用率低的問題。本發(fā)明專利主要是通過耐硫變換技術(shù)結(jié)合循環(huán)流化床脫硫技術(shù),合理配置變換反應(yīng)與循環(huán)流化床脫硫系統(tǒng)的熱量,脫除合成氣中的含硫化合物、砷及其化合物、硒及其化合物、輕質(zhì)芳烴,通過固定床吸附劑脫除合成氣中的氨和氰化物,并可選地增加保護(hù)床裝置除去合成氣其他微量雜質(zhì)如汞、氯化氫,實(shí)現(xiàn)合成氣凈化的目標(biāo)。采用耐硫變換技術(shù)結(jié)合循環(huán)流化床脫硫技術(shù)脫除凈化氣的工藝,可以簡化凈化流程,減少設(shè)備,從而有效節(jié)省設(shè)備占地面積和降低合成氣凈化裝置的投資成本。本發(fā)明的工藝方法和流程配置,通過耐硫變換技術(shù)與循環(huán)流化床熱法脫硫技術(shù)的有效配置,并通過流程合理設(shè)計(jì)充分利用了上述反應(yīng)的熱量。最后可以使得凈化后合成氣的硫含量降低至0.5-5ppmv,并可脫除輕質(zhì)芳烴、砷及其化合物、硒及其化合物,通過固定床吸附劑和可選擇保護(hù)床,可以有效的脫除了合成氣中氨、氰化物、汞、氯化氫等其他雜質(zhì)。附圖說明圖1為本發(fā)明實(shí)施例1結(jié)合耐硫變換和循環(huán)流化床熱法脫硫的合成氣凈化裝置結(jié)構(gòu)示意圖。圖2為本發(fā)明實(shí)施例2結(jié)合耐硫變換和循環(huán)流化床熱法脫硫的合成氣凈化裝置結(jié)構(gòu)示意圖。圖3為本發(fā)明實(shí)施例3結(jié)合耐硫變換和循環(huán)流化床熱法脫硫的合成氣凈化裝置結(jié)構(gòu)示意圖。圖4為本發(fā)明實(shí)施例4結(jié)合耐硫變換和循環(huán)流化床熱法脫硫的合成氣凈化裝置結(jié)構(gòu)示意圖。圖5為本發(fā)明實(shí)施例5結(jié)合耐硫變換和循環(huán)流化床熱法脫硫的合成氣凈化裝置用于合成氨節(jié)能增產(chǎn)結(jié)構(gòu)示意圖。圖6為本發(fā)明實(shí)施例6結(jié)合耐硫變換和循環(huán)流化床熱法脫硫的合成氣凈化裝置用于煤制氫節(jié)能增產(chǎn)結(jié)構(gòu)示意圖。圖7為本發(fā)明實(shí)施例7結(jié)合耐硫變換和循環(huán)流化床熱法脫硫的合成氣凈化裝置用于新建煤制氫流程結(jié)構(gòu)示意圖。具體實(shí)施方式實(shí)施例1參見圖1,圖中給出了一種結(jié)合耐硫變換和循環(huán)流化床熱法脫硫的合成氣凈化裝置,包括水激冷洗滌裝置100,換熱器210、220,熱量回收裝置1100,耐硫變換反應(yīng)系統(tǒng)300,循環(huán)流化床的吸附反應(yīng)器400,循環(huán)流化床的再生反應(yīng)器500,過濾器610、620,可再生脫NH3/HCN裝置700,脫除汞和氯化物裝置800,冷卻裝置900。水激冷洗滌裝置100具有一粗合成氣輸入口110和粗合成氣輸出口120,水激冷洗滌裝置100的粗合成氣輸入口110通過一粗合成氣輸送管線1連接一煤氣化裝置1000,煤氣化裝置1000為水煤漿氣化裝置、粉煤氣化裝置或碎煤固定床氣化裝置。耐硫變換反應(yīng)系統(tǒng)300可使用絕熱耐硫變換反應(yīng)器或等溫耐硫變換反應(yīng)器或本申請人申請的中國專利號ZL201210040295.6、發(fā)明名稱為帶有支撐式槽孔板分布器的徑向或軸徑向固定床反應(yīng)器。耐硫變換反應(yīng)系統(tǒng)300具有一粗合成氣輸入口310和粗合成氣輸出口320。耐硫變換反應(yīng)系統(tǒng)300的粗合成氣輸入口310通過一粗合成氣輸送管線2連接水激冷洗滌裝置100的粗合成氣輸出口120。熱量回收裝置1100具有一粗合成氣輸入口1110和一粗合成氣輸出口1120。熱量回收裝置1100的粗合成氣輸入口1110通過一粗合成氣輸送管線3a連接耐硫變換反應(yīng)系統(tǒng)300的粗合成氣輸出口320。熱量回收裝置1100的粗合成氣輸出口1120通過一粗合成氣輸送管線4a與換熱器210的粗合成氣輸入口211連接。換熱器210具有一粗合成氣輸入口211、一粗合成氣輸出口212、一脫硫后的合成氣輸入口213和一脫硫后的合成氣輸出口214,換熱器210的粗合成氣輸入口211通過一粗合成氣輸送管線4a連接熱量回收裝置1100的粗合成氣輸出口1120。換熱器210的脫硫后的合成氣輸出口214通過通過一脫硫后的合成氣輸送管線4′與再生脫NH3/HCN裝置700的脫硫后的合成氣入口710連接。循環(huán)流化床的吸附反應(yīng)器400和循環(huán)流化床的再生反應(yīng)器500形成一流化催化裂化FCC工藝系統(tǒng)。循環(huán)流化床的吸附反應(yīng)器400包括一提升管410、一旋風(fēng)分離器450和一下降管420,循環(huán)流化床的吸附反應(yīng)器400的提升管410的底部具有一粗合成氣輸入口411,提升管410的下部配置有再生吸附劑入口412和再生吸附劑循環(huán)入口413,提升管410的上部配置有含固體吸附顆粒的脫硫后的合成氣出口414。循環(huán)流化床的吸附反應(yīng)器400的旋風(fēng)分離器450的下部配置有載有硫的吸附劑出口451,旋風(fēng)分離器450的上部配置有含固體吸附顆粒的脫硫后的合成氣入口452,旋風(fēng)分離器450的頂部配置有脫硫后的合成氣輸出口453。循環(huán)流化床的吸附反應(yīng)器400的下降管420的下部配置有載有硫的吸附劑循環(huán)出口421和載有硫的吸附劑待再生出口422。提升管410底部的粗合成氣輸入口411通過一粗合成氣輸送管線5連接換熱器210的粗合成氣輸出口212;提升管410下部的吸附劑循環(huán)入口通過一斜管430與下降管420下部的載有硫的吸附劑循環(huán)出口421連接,提升管410上部的含固體吸附顆粒的脫硫后的合成氣出口414通過一含固體吸附顆粒的脫硫后的合成氣輸送管線2′與旋風(fēng)分離器450上部的含固體吸附顆粒的脫硫后的合成氣入口452連接。過濾器610具有一脫硫后的合成氣輸入口611和一脫硫后的合成氣輸出口612,過濾器610的脫硫后的合成氣輸入口611通過一脫硫后的合成氣輸送管線3′與旋風(fēng)分離器450頂部的脫硫后的合成氣輸出口453連接,過濾器610的脫硫后的合成氣輸出口612通過一脫硫后的合成氣輸送管線1′與換熱器210的脫硫后的合成氣輸入口213連接。循環(huán)流化床的再生反應(yīng)器500包括一提升管510、一旋風(fēng)分離器530和一下降管520。提升管510的下部具有一載有硫的吸附劑待再生入口511,底部配置有再生空氣或O2與N2的混合氣體入口512,提升管510的上部配置有含有再生固體吸附劑的富SO2的氣體出口513。旋風(fēng)分離器530的上部配置有含有再生固體吸附劑的富SO2的氣體入口531,頂部配置有富SO2的氣體出口532,底部配置有再生固體吸附劑出口533。下降管520的下部配置有再生吸附劑出口523。提升管510下部的載有硫的吸附劑入口511通過斜管440與下降管420下部的載有硫的吸附劑待再生出口422連接;旋風(fēng)分離器530上部的含有再生固體吸附劑的富SO2的氣體入口521通過一含有再生固體吸附劑的富SO2的氣體輸送管線1″與提升管510上部的含有再生固體吸附劑的富SO2的氣體出口513連接;下降管520底部的再生吸附劑出口523通過一再生吸附劑輸送管線(圖中未示出)與循環(huán)流化床的吸附反應(yīng)器400的提升管410下部的再生吸附劑入口412連接。過濾器620具有一富SO2的氣體入口621和富SO2的氣體出口622,過濾器620的富SO2的氣體入口621與循環(huán)流化床的再生反應(yīng)器500的旋風(fēng)分離器520頂部的富SO2的氣體出口522通過一富SO2的氣體輸送管線2″連接。換熱器220具有一富SO2的氣體入口221、富SO2的氣體出口222、再生空氣或O2與N2的混合氣體入口223、再生空氣或O2與N2的混合氣體出口224,換熱器220的富SO2的氣體入口221通過一富SO2的氣體輸送管線3″連接過濾器620的富SO2的氣體出口622,換熱器220的再生空氣或O2與N2的混合氣體入口223連接空氣源或O2與N2的混合氣體源;換熱器220的再生空氣或O2與N2的混合氣體出口224通過再生空氣或O2與N2的混合氣體輸送管線225連接循環(huán)流化床的再生反應(yīng)器500的提升管510底部的再生空氣或O2與N2的混合氣體入口512??稍偕揘H3/HCN裝置700為固定式吸附床,具有脫硫后的合成氣入口710和脫硫后的合成氣出口720,再生脫NH3/HCN裝置700的脫硫后的合成氣入口710通過一脫硫后的合成氣輸送管線4′與換熱器210的脫硫后的合成氣輸出口214連接。脫除汞和氯化物裝置800為保護(hù)床,具有脫硫后的合成氣入口810和脫硫后的合成氣出口820,脫除汞和氯化物裝置800的脫硫后的合成氣入口810通過一脫硫后的合成氣輸送管線6′與可再生脫NH3/HCN裝置700的脫硫后的合成氣出口720連接。冷卻裝置900具有脫硫后的合成氣入口910和脫硫后的合成氣出口920,冷卻裝置900的脫硫后的合成氣入口910通過一脫硫后的合成氣輸送管線8′與可再生脫NH3/HCN裝置800的脫硫后的合成氣出口820連接,冷卻裝置900的脫硫后的合成氣出口920通過一脫硫后的合成氣輸送管線7′與下游的脫二氧化碳單元裝置(圖中未示出)連接。脫二氧化碳單元裝置為液相吸收脫二氧化碳單元裝置或干法化學(xué)吸附脫二氧化碳單元裝置。經(jīng)過煤或其它含碳材料的氣化產(chǎn)生粗合成氣,例如水煤漿氣化、粉煤氣化、碎煤固定床氣化,該粗合成氣通過粗合成氣輸送管線1送入到水激冷洗滌裝置100中,經(jīng)過水激冷洗滌裝置100洗滌后,形成溫度為180-250℃的粗合成氣,該粗合成氣有含硫化合物、氨、氰化物并可能含有輕質(zhì)芳烴、砷及其化合物、硒及其化合物、汞、氯化物等雜質(zhì)。溫度為180-250℃的粗合成氣通過粗合成氣輸送管線2進(jìn)入耐硫變換反應(yīng)系統(tǒng)300,耐硫變換反應(yīng)系統(tǒng)300可采用全部變換或部分變換工藝,耐硫變換反應(yīng)系統(tǒng)300可使用絕熱耐硫變換反應(yīng)器或等溫耐硫變換反應(yīng)器或本申請人申請的中國專利號ZL201210040295.6、發(fā)明名稱為帶有支撐式槽孔板分布器的徑向或軸徑向固定床反應(yīng)器。在耐硫變換反應(yīng)系統(tǒng)300中,粗合成氣發(fā)生如下反應(yīng)CO+H2O→CO2+H2,反應(yīng)放出大量的熱量,粗合成氣的溫度也隨之升高至270-450℃。粗合成氣...