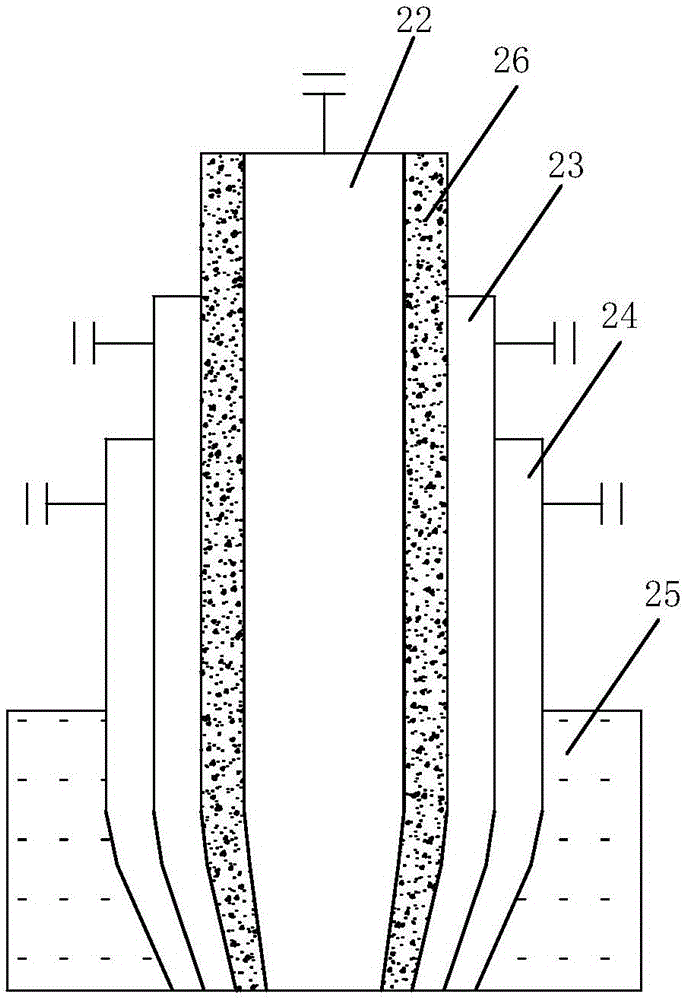
本發(fā)明涉及到化工設備,具體指一種煤熱解制油裝置及煤熱解制油方法。
背景技術:
:煤直接加氫工藝過程主要包括煤的破碎與干燥、煤漿制備、加氫液化、固液分離、氣體凈化、液體產品分餾和精制以及制氫等部分。主要流程為:在高溫高壓下,高濃度煤漿中的煤發(fā)生熱解,在催化劑作用下進行加氫和分解,最終成為穩(wěn)定的液體分子。液化過程中,將煤、催化劑和循環(huán)油制成的煤漿,與制得的氫氣混合送入反應器。在液化反應器內,煤首先發(fā)生熱解反應,生成自由基“碎片”,不穩(wěn)定的自由基“碎片”再與氫在催化劑存在條件下結合,形成分子量比煤低得多的初級加氫產物。出反應器的產物構成十分復雜,包括氣、液、固三相。氣相的主要成分是氫氣,分離后循環(huán)返回反應器重新參加反應;固相為未反應的煤、礦物質及催化劑;液相則為輕油(粗汽油)、中油等餾份油及重油。液相餾份油經提質加工(如加氫精制、加氫裂化和重整等)得到合格的汽油、柴油和航空煤油等產品。重質的液固淤漿經進一步分離得到重油和殘渣,重油作為循環(huán)溶劑用于煤漿制備?,F有的煤直接液化技術中,反應器反應壓力高達17MPa-30Mpa,氫耗量高達6%-10%,流程復雜,投資成本高。工藝過程中不僅要補充大量新氫,還需要循環(huán)油作供氫溶劑,裝置生產能力降低,出液化反應器的產物組成復雜,固液兩相分離困難,產油率低。技術實現要素:本發(fā)明所要解決的技術問題是針對現有技術的現狀提供一種反應條件溫和、氫耗量小、產油率高的煤熱解制油裝置。本發(fā)明所要解決的另一個技術費問題是針對現有技術的現狀提供一種煤熱解制油方法。本發(fā)明解決上述技術問題所采用的技術方案為:該煤熱解制油裝置,包括氣化爐,所述氣化爐的頂部設有氣化噴嘴,所述氣化爐的上部為氣化室,所述氣化室的底部為激冷室,所述氣化室的底部出口和激冷室通過下降管相連通,所述氣化爐的底部設有渣出口;其特征在于:所述氣化爐通過合成氣輸送通道連接熱解室;所述熱解室的頂部設有煤噴嘴4,所述熱解室的中部設有減溫噴嘴,所述熱解室的底部設有產品出口。所述氣化室為熱壁結構,所述氣化室的底部為錐形結構;所述氣化爐的側部上間隔設有多個蒸汽噴嘴,各所述蒸汽噴嘴的出口均對向所述氣化室的出口與所述下降管的入口交接處。所述熱解室的下部相對于所述熱解室的上部傾斜設置。該結構能夠對油氣和煤焦進行初步分離,方便下游的分離工序。上述各方案中的所述氣化噴嘴優(yōu)選包括第一本體,所述第一本體上由內而外依次設有燃料通道、氧氣通道、蒸汽通道和第一冷卻通道。作為改進,所述燃料通道與所述氧氣通道之間的隔層采用耐磨材料制備,以保證使用壽命。所述煤噴嘴可以根據需要選用現有技術中的任意一種,較好的,所述煤噴嘴包括第二本體,所述第二本體上設有粉煤通道,所述粉煤通道外設有第二冷卻通道。所述本體采用耐磨材料制備。使用上述煤熱解制油裝置的煤熱解制油方法,其特征在于包括下述步驟:燃料、氧氣和水蒸汽自所述氣化噴嘴的對應通道內進入所述氣化室內,在1000~1700℃、3~9MPa下反應,生成的合成氣和液態(tài)渣從所述氣化室的底部出口進入所述下降管內;水蒸汽通過所述蒸汽噴嘴噴向氣化室的出口物料,對出口物料進行一次降溫,同時與出口物料中的合成氣進行二次反應,增加合成氣中的氫氣含量;液態(tài)渣在重力作用下經由所述下降管進入所述激冷室,冷卻后從所述渣出口排出;控制所述激冷室內溫度小于等于300℃;合成氣經由所述合成氣輸送通道進入所述熱解室內;煤粉從所述煤噴嘴噴入到所述熱解室內,煤粉在高溫臨氫條件下進行煤加氫快速熱解反應,產出油氣并生成煤渣;控制所述熱解室內反應溫度為600~1500℃,反應壓力3~9MPa;冷卻介質從所述減溫噴嘴噴入所述熱解室內,對熱解室產物進行冷卻,冷卻后的產物從所述產品出口排至下游??刂七M入所述熱解室內合成氣中氫氣含量為干基煤粉質量的5.5%。所述產品出口內的物料出口溫度為490-510℃。所述燃料為煤粉、焦粉或天然氣。與現有技術相比,本發(fā)明所提供的煤熱解制油裝置及煤熱解制油方法本發(fā)明提供一種應用煤快速熱解技術的外置組合反應器,可以滿足煤快速熱解的工業(yè)化應用。本反應器可以同時滿足煤氣化和煤加氫的需要,不需要另外提供氫源。其氣化系統(tǒng)與熱解系統(tǒng)相對獨立,有利于反應器的穩(wěn)定運行,有利于裝置的大型化。附圖說明圖1為本發(fā)明實施例示意圖;圖2為本發(fā)明實施例中氣化噴嘴的剖視示意圖;圖3為本發(fā)明實施例中煤噴嘴的剖視示意圖。具體實施方式以下結合附圖實施例對本發(fā)明作進一步詳細描述。如圖1至圖3所示,該煤熱解制油裝置包括相互連通的氣化爐1和熱解室3。氣化爐1自上而下依次包括氣化室11、下降管12和激冷室13。氣化室11為熱壁反應器結構,其頂部設有氣化噴嘴2,其下部為錐形結構,其底部出口15連通下降管12的入口。下降管12連接有冷卻水管道16,通過冷卻水管道16向下降管12表面通入激冷水,在下降管內壁形成水膜保護下降管。下降管12的入口為外擴的喇叭口,以方便承接氣化室出口物料。下降管12的出口插入到激冷室13的液面內。激冷室13連接有激冷水管道17,通過激冷水管道向激冷室內輸送激冷水;激冷室13的底部設有渣出口14。蒸汽噴嘴6,有多個,間隔設置在氣化爐的側壁上并沿氣化爐的周向均勻布置;各蒸汽噴嘴6的出口均對向氣化室的底部出口與下降管的入口交界處,以使蒸汽噴向氣化室出口物料。本實施例中蒸汽噴嘴6的軸線與氣化室的底部錐形側壁平行。氣化爐1的合成氣出口通過合成氣輸送通道31連接熱解室3。熱解室3分為上部和下部兩部分,熱解室上部豎直設置,熱解室3的下部相對于熱解室的上部傾斜設置,以使熱解室內產物中的氣相和固相進行初步分層,方便下游工序的分離。熱解室3的頂部設有煤噴嘴4,熱解室的中部設有減溫噴嘴5,熱解室3的底部設有產品出口31。上述蒸汽噴嘴6和減溫噴嘴5的結構可根據需要選用現有技術中的任意一種或多種組合使用。氣化噴嘴2包括第一本體,第一本體上由內而外依次設有燃料通道22、氧氣通道23、蒸汽通道24和第一冷卻通道25;燃料通道22與所述氧氣通道23之間的隔層26采用耐磨材料制備。煤噴嘴4包括第二本體41,第二本體41上設有粉煤通道42,粉煤通道42外設有第二冷卻通道43。第二本體41采用耐磨材料制備。使用上述煤熱解制油裝置的煤熱解制油方法包括下述步驟:燃料、氧氣和水蒸汽自所述氣化噴嘴2的對應通道內進入氣化室11內,在1500℃、4MPa下反應,生成的合成氣和液態(tài)渣從氣化室11的底部出口進入下降管12內;燃料可以根據方便選用煤粉、焦粉或天然氣。水蒸汽通過所述蒸汽噴嘴6噴向氣化室的出口物料,對出口物料進行一次降溫,同時與出口物料中的合成氣進行二次反應,增加合成氣中的氫氣含量;液態(tài)渣在重力作用下經由下降管12進入激冷室13,冷卻后從渣出口14排出;控制激冷室內溫度小于等于300℃;合成氣經由合成氣輸送通道31進入所述熱解室3內;煤粉從煤噴嘴4噴入到熱解室3內,煤粉在高溫臨氫條件下進行煤加氫快速熱解反應,產出油氣并生成煤渣;控制所述熱解室3內反應溫度為1300℃,反應壓力3.8MPa;進入熱解室3內合成氣中氫氣含量為干基煤粉質量的5.5%。冷卻水從減溫噴嘴5噴入到熱解室3內,對熱解室產物進行冷卻,冷卻后的產物從產品出口31排至下游,控制產品出口31內的物料出口溫度為500℃。將本實施例與常規(guī)煤制油方法進行比較,結果見表1。表1煤炭直接液化煤炭間接液化煤炭干餾實施例氫耗制氫裝置制氫裝置-----不需額外補充氫氣項目煤耗3.5噸/噸油品4噸/噸油品25噸/噸油品3.34噸/噸油品當前第1頁1 2 3