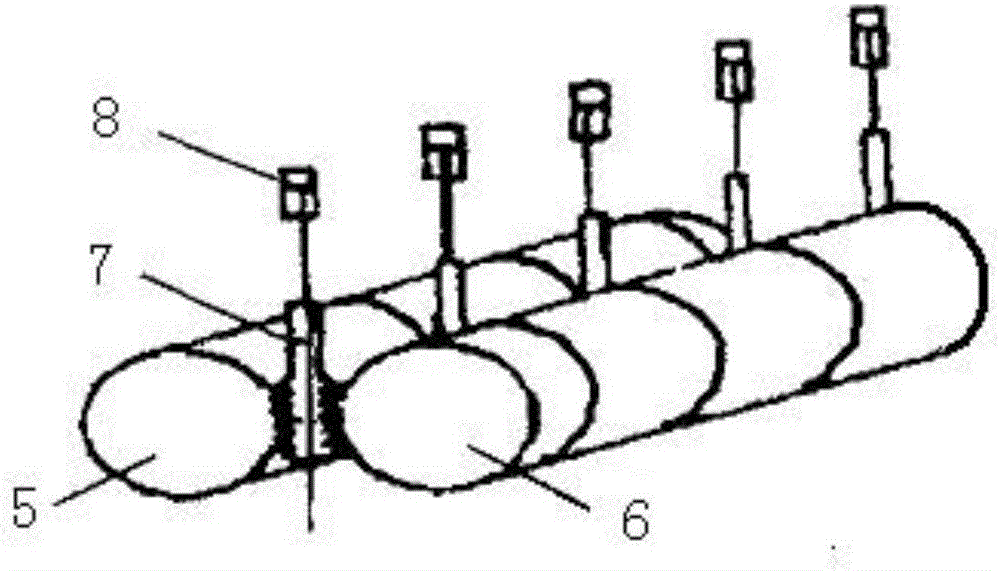
本發(fā)明涉及一種取向硅鋼板形控制方法,尤其涉及一種取向硅鋼楔形板板形控制方法。
背景技術:
:帶鋼軋制板形對于取向硅鋼非常重要,直接影響變壓器鐵芯的疊裝系數(shù)和噪音等技術指標,越來越受到生產廠商與用戶的重視。對板形的質量控制,不僅提高冷軋工序的成材率,減少斷帶,提高產量,而且直接提升帶材在市場的占有率。取向硅鋼的冷軋坯料供貨寬度通常在1300mm左右,對于650mm廿輥軋機在冷軋之前需對坯料進行分剪。由于坯料普遍存在中間厚而兩邊薄的現(xiàn)象,在分剪之后就形成一邊厚一邊薄的楔形板,尤其對0.15~0.23mm薄規(guī)格取向硅鋼的板形影響尤其顯著。楔形板給冷軋板形質量的提升帶來很大困難。在楔形板的軋制過程中,會出現(xiàn)板帶跑偏,造成一中間錐度調整不到位問題,進而導致軋制板型質量問題。實際生產過程中通常采用板形調整機構對板形進行調節(jié)來改善板形,但ASU齒條對軋輥輥縫形狀進行微量調整,楔形板可通過人工對其板型進行調整。但一中間輥(1st)因楔形板帶鋼軋制中心偏移,其調整范圍達到了橫向位移的極限限制而影響人工板型調整。技術實現(xiàn)要素:本發(fā)明的目的是克服現(xiàn)有技術存在的缺陷,提供一種經濟有效,能明顯改善取向硅鋼楔形板軋制后板形的控制方法。實現(xiàn)本發(fā)明目的的技術方案是:一種取向硅鋼楔形板板形控制方法,包括如下步驟:(1)將熱軋原料對切后,分為A、B卷,A卷為軋機進料操作側偏厚的板帶,B卷為傳動側偏厚板帶;(2)將軋機上一中間輥和下一中間輥相反兩端加工成錐形,上一中間輥錐度在操作側,下一中間輥錐度在傳動側,以其相向或相反的軸向移動來調整重合平行部分的長度,在軋制過程中通過上一中間輥和下一中間輥的軸向竄動改變帶鋼邊部輥縫的形狀;(3)軋制A卷時,增加上一中間輥的有效平面量,減小下一中間輥的有效平面量,縮小上一中間輥錐度長度L,同時增大下一中間輥錐度長度L;軋制B卷時,減小上一中間輥的有效平面量,增大下一中間輥的有效平面量,增大上一中間輥錐度長度L,同時縮小下一中間輥錐度長度;(4)軋制過程中,軋機調整工通過敲板時手感彈性檢測兩邊部松緊程度,通過ASU齒條徑向輥型調整機構對工作輥輥縫形狀進行調整對板形進行控制。上述技術方案,所述A卷和B卷均為楔形板,楔形板兩側厚度差為0.04~0.07mm。上述技術方案,所述上一中間輥、下一中間輥錐度長度L為帶鋼板寬的18~20%,錐度高度S為L*2~3‰/2。上述技術方案,當帶鋼板寬為645~655mm時,錐度長度為L為120~130mm,錐度高度S為0.125~0.15mm。上述技術方案,軋制A卷時,上一中間輥錐度長度L為120mm,錐度高度S為0.125mm,下一中間錐度長度L為130mm,錐度高度S為0.15mm;軋制B卷時,上一中間錐度長度L為130mm,錐度高度S為0.15mm,下一中間輥錐度長度L為120mm,錐度高度S為0.125mm。上述技術方案,所述ASU齒條徑向輥型調整機構調整方法為B支撐輥、C支撐輥在沿軸長方向有4個支撐軸承,每個支撐軸承位置的變化由5個ASU齒條帶動偏心環(huán)進行調整,經過第二中間輥、第一中間輥傳到工作輥上,對工作輥輥縫形狀進行調整。上述技術方案,在軋制生產組織中,采取同側厚板組批軋制的方法,即A、B卷分別組批軋制的方法,減少換輥次數(shù)。采用上述技術方案后,本發(fā)明具有以下積極的效果:(1)本發(fā)明通過一頭具有一定錐度的上、下一中間輥的軸向竄動改變帶鋼邊部輥縫形狀,從而實現(xiàn)板形的調節(jié),并根據(jù)兩種不同形狀的楔形板卷材,調節(jié)一中間輥錐度長度和錐度高度的變化,改變一中間輥的有效平面量,避免一中間輥調整時一側調整范圍受到極限值限制的缺陷,從而提高板形調整效果;(2)本發(fā)明一中間軸向調整,不僅可使帶材沿橫向尺寸均勻外,還可以用來消除在軋制過程中由于工作輥彎曲變形而產生的帶材邊浪,對帶鋼邊部延伸變形有很大作用;(3)本發(fā)明通過調整ASU凸度,來調節(jié)帶鋼中部和邊部的延伸變形量。增大凸度,帶鋼中部延伸量變大,減小凸度,帶鋼邊部延伸量變大,從而可根據(jù)板形狀況對ASU凸度進行調節(jié),從而改善板形;當帶鋼來料橫截面楔形較大時,通過調節(jié)ASU,使支撐輥軸線傾斜,也可調整板型;(4)本發(fā)明采用A、B卷分別組批軋制的方法,可針對A、B卷的轉換同步更換不同錐度的一中間輥,從而減少換輥次數(shù),對提高軋制生產效率和提升板型質量都帶來積極效應。附圖說明為了使本發(fā)明的內容更容易被清楚地理解,下面根據(jù)具體實施例并結合附圖,對本發(fā)明作進一步詳細的說明,其中圖1為本發(fā)明一中間輥軸向調整機構示意圖;圖2為本發(fā)明一中間輥錐度示意圖;圖3為本發(fā)明ASU齒條徑向輥型調整機構示意圖;圖中1、上一中間輥;2、下一中間輥;3、工作輥;4、工作輥止推軸承;5、B支撐輥;6、C支撐輥;7、ASU齒條;8、ASU油缸。具體實施方式(實施例1)取向硅鋼坯料厚度為2.3mm,寬度為1300mm。將坯料由中間分剪,定義軋機進料工作側(即靠近主操手一側)偏厚的板帶為A卷,反之工作側偏薄的板帶為B卷。在帶鋼工作側與傳動側邊部隨機選取五個位置測量板帶厚度,數(shù)據(jù)如表1所示:表1:測量數(shù)據(jù)顯示:坯料切分后楔形板厚度差在0.04~0.07mm范圍內,符合熱軋坯料供貨標準。以軋鋼出口導向輥的長度850mm為基準,取坯料寬度為650mm,按標準軋制工藝進行實驗,在軋鋼出口工作側按軋鋼四個道次分別測量帶鋼邊部與導向輥邊部的距離(各三個點),分別定義為S1、S2、S3、S4,此四項數(shù)據(jù)的差值即可反映楔形板在軋制過程中的板帶軋制中心偏移量趨勢。經實驗軋制,得出如下數(shù)據(jù):表2:根據(jù)以上數(shù)據(jù)可知:軋制第一道次軋制中心線偏移量很小(±0.5mm內),以后軋制道次中板帶軋制中心偏移量逐漸增大,最大偏移量達8~9mm。如:A卷在軋制過程中板帶向著工作側偏移,B卷在軋制過程中板帶向著傳動側偏移,即板帶在軋制過程中會向著板帶厚的一側進行偏移,A卷總偏移量達8.2mm,B卷偏移量達6.2mm。在帶鋼軋制過程中發(fā)現(xiàn)板形不良時,可利用這兩個調整機構進行在線調節(jié)。一中間輥(1st)軸向輥形調整機構的基本原理是:見圖1,在上、下兩對第一中間輥上,在相反的兩端將軋輥加工成錐形,上一中間輥1錐度在操作側,下一中間輥2錐度在傳動側,以其相向或相反的軸向移動來調整重合的平行部分(即有效平面量)的長度,這樣在軋制過程中通過一中間輥的軸向竄動主要改變帶鋼邊部輥縫的形狀,除了可以促使帶材沿橫向尺寸均勻外,還可以用來消除在軋制過程中由于工作輥彎曲變形而產生的帶材邊浪,對帶鋼邊部延伸變形有很大作用。ASU齒條徑向輥型調整機構的基本原理是:見圖2,B、C支撐輥在沿軸長發(fā)方向有4個支撐軸承,每個支撐軸承位置的變化由5個ASU齒條7帶動偏心環(huán)任意調整,經過第二中間輥、第一中間輥傳到工作輥3上,對軋輥輥縫形狀進行微量調整。調整ASU凸度,對帶鋼中部和邊部的延伸變形有影響。增大凸度,帶鋼中部延伸變大。減小凸度,帶鋼邊部延伸變大。當帶鋼來料橫截面楔形較大時,調節(jié)ASU使支撐輥軸線傾斜,也可調整板型。實驗軋制過程中,調整工通過手感(敲棒)對各道次鋼卷板型進行調整正常后,各ASU齒條7位置及一中間輥數(shù)(1st)值數(shù)據(jù)整理如下:表3:注:上圖中ASU齒條7數(shù)值越大表示軋制力越小;1st數(shù)值表示有效平面量,調整行程0-100以上數(shù)據(jù)表明,ASU齒條7對軋輥輥縫形狀進行微量調整,楔形板可通過人工對其板型進行調整。但一中間輥(1st)因楔形板帶鋼軋制中心偏移,其調整范圍達到了橫向位移的極限而影響人工板型調整。根據(jù)軋制原理,帶鋼對正軋制中心線生產時,軋制力在軋輥長度方向最終是通過支撐輥裝置的軸承座(鞍座)傳遞給機架的,機架承受的彎曲力矩,從機架邊緣到中心是連續(xù)加大的,中心部位力矩最大。對于楔形板發(fā)生偏移后,板帶各位置的受力分布發(fā)生變化,最大力矩位置向薄側偏移,厚側受力減小,而薄側受力增加。受力分布的變化導致厚側延展不足,而薄側延展加大,反映到板形上則表現(xiàn)為厚側偏緊而薄側偏松。本發(fā)明提出的對策方案的關鍵點在于一中間輥磨削錐度值的調整來應對板帶的偏移。表4:一中間輥錐度磨削示意圖見圖3,磨削數(shù)據(jù)如下表所示:表5:上一中間輥1錐度下一中間輥2錐度調整前A,B卷L=130mm;s=0.15mmL=130mm;s=0.15mm調整后A卷L=120mm;s=0.125mmL=130mm;s=0.15mm調整后B卷L=130mm;s=0.15mmL=120mm;s=0.125mm一中間輥按照以上數(shù)據(jù)磨削后進行軋制實驗,各道次鋼卷板型調整正常后各齒條位置及一中間輥數(shù)值數(shù)據(jù)整理如下:表6:以上數(shù)據(jù)結果顯示,按對策方案將一中間輥錐度值進行調整以后,楔形板在軋制過程中,一中間輥的調整范圍較之前有明顯優(yōu)化,不再出現(xiàn)一中間輥一側調整范圍受到極限值的限制,板型調整效果明顯提高。優(yōu)選地,在軋制生產組織中,采取同側厚板組批軋制的方法,即A、B卷分別組批軋制的方法,針對A、B卷的轉換同步更換不同錐度的一中間輥,可減少換輥次數(shù),對提高軋制生產效率和提升板型質量都帶來積極效應。本發(fā)明方法適用于各種寬度規(guī)格取向硅鋼的軋制過程中的板形控制,針對不同板寬,僅需對上、下一中間輥錐度磨削數(shù)據(jù)進行變化,其中錐度長度L為帶鋼板寬的18~20%,錐度高度S為L*2~3‰/2,當板寬較窄時取S的上限值,反之取S下限值。本發(fā)明方法同樣適用于軋制不同厚度規(guī)格的取向硅鋼的板形控制,尤其0.15~0.27mm薄規(guī)格取向硅鋼板形更容易變形,采用本方法對板形控制更具有積極意義。以上所述的具體實施例,對本發(fā)明的目的、技術方案和有益效果進行了進一步詳細說明,所應理解的是,以上所述僅為本發(fā)明的具體實施例而已,并不用于限制本發(fā)明,凡在本發(fā)明的精神和原則之內,所做的任何修改、等同替換、改進等,均應包含在本發(fā)明的保護范圍之內。當前第1頁1 2 3