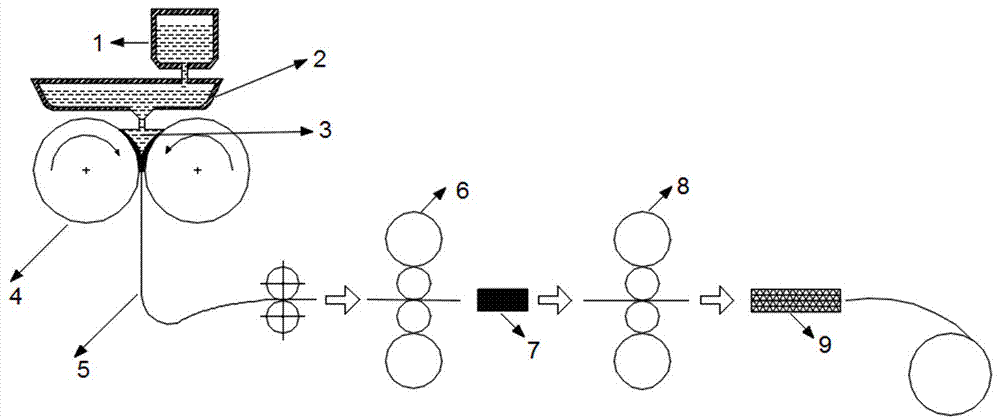
本發(fā)明屬于冶金技術(shù)領(lǐng)域,特別涉及一種基于薄帶連鑄制備高磁感高強度無取向硅鋼的方法。
背景技術(shù):隨著全球環(huán)境污染的加劇,氣候問題成了各個國家工業(yè)發(fā)展必須考慮的重要因素之一。我國是一個人口大國、消費大國,能源與環(huán)境問題是21世紀(jì)面對的棘手問題。近年來,國家大力提倡開發(fā)清潔能源,綠色環(huán)保的新能源電動汽車正是在這樣的背景下得以快速發(fā)展,是未來汽車發(fā)展的主流,而電動汽車的核心在于高速驅(qū)動電機的使用。高速驅(qū)動電機的特點是不通過齒輪傳動直接使車輪旋轉(zhuǎn),故對于無刷直流驅(qū)動馬達(dá)具有高的要求。電機在高速運轉(zhuǎn)時,存在一定的損耗,包括鐵損和銅損,這些損耗與電機的功率存在很大的關(guān)系,功率越大,鐵損所占的比例越大;電機的高速運轉(zhuǎn)要求鐵心材料具有高頻低鐵損的特點。作為一種高速驅(qū)動電機產(chǎn)品的鐵心,在電機高速旋轉(zhuǎn)時,會產(chǎn)生很大的離心力,同時有些轉(zhuǎn)子由于形狀特殊在高速旋轉(zhuǎn)時局部容易產(chǎn)生應(yīng)力集中,這就要求其既具有高的強度和硬度,同時也要保證電機具有高的效率與高的轉(zhuǎn)矩,即要求鐵心材料鐵損低,磁感強度高。以往電工鋼的關(guān)注點僅僅為獲得良好的磁性能,現(xiàn)在對其力學(xué)性能提出了更高的標(biāo)準(zhǔn)。高速驅(qū)動電機用無取向硅鋼對性能的高要求使得其對生產(chǎn)工藝的控制難度大大加強。鞍鋼公開了一種高強度專用冷軋無取向硅鋼的生產(chǎn)方法(CN103882288A),具有一定的新穎性,采用常規(guī)冶煉澆鑄工藝進(jìn)行生產(chǎn),加上熱軋,常化,冷軋,退火等后處理工藝,控制材料的強度與磁性能。目前國外的研究以日本采用常規(guī)流程生產(chǎn)的高強度無取向硅鋼性能最為優(yōu)良,日本新日鐵(US8097094B2)曾公開過關(guān)于高強度電工鋼的報導(dǎo),主要特點是通過在基體中添加大量的Cu元素(0.6~8.0%),采用轉(zhuǎn)爐冶煉,連鑄,熱軋,常化,冷軋,退火等工藝流程,特別是最終退火后還要在一定溫度采用時間較長的時效退火工藝,控制Cu以細(xì)小的ε-Cu金屬相形式析出,提高強度,磁性能也不降低。通過這些專利的介紹可以看出,利用常規(guī)方法制備高磁感高強度電工鋼存在生產(chǎn)過程復(fù)雜,工藝要求嚴(yán)格,投資成本高、生產(chǎn)時間長、生產(chǎn)效率低等問題。雙輥薄帶連鑄技術(shù)是進(jìn)入21世紀(jì)以來國家大力提倡的一種近終成形技術(shù),在雙輥鑄軋機上澆注0.7~3mm厚薄帶產(chǎn)品具有很大的優(yōu)勢。較傳統(tǒng)的連鑄工藝,這種工藝的主要優(yōu)勢在于:1.簡化了常規(guī)生產(chǎn)工藝,從而大大方便了生產(chǎn),節(jié)約了生產(chǎn)成本。2.設(shè)備占地面積小,免去了傳統(tǒng)工藝熱軋系統(tǒng)所需要的加熱爐、緩沖爐等高污染設(shè)備,減少了投資成本,且生產(chǎn)過程更加節(jié)能與環(huán)保。3.薄帶連鑄工藝凝固速度在102~103K/s的亞快速凝固范圍內(nèi),凝固速度快,生產(chǎn)效率高。4.對難于加工的脆性材料來說,傳統(tǒng)工藝生產(chǎn)易產(chǎn)生裂紋等缺陷,而鑄軋工藝不僅能夠滿足材料的成品厚度要求,而且對有害元素的敏感性極低,凝固帶鋼幾乎無裂紋、偏析及傳統(tǒng)方法易產(chǎn)生的質(zhì)量缺陷。正是由于薄帶連鑄工藝在節(jié)能、經(jīng)濟與冶金上的突出優(yōu)點,因而世界各國均投入較大力度發(fā)展該技術(shù);現(xiàn)有結(jié)果表明,薄帶連鑄技術(shù)在制備高磁感高強度無取向硅鋼上存在明顯優(yōu)勢;為滿足對高磁感高強度無取向硅鋼的要求,應(yīng)用薄帶連鑄技術(shù)生產(chǎn)無取向硅鋼已經(jīng)成為了研究熱點。無取向硅鋼隨硅含量的增加鐵損降低,磁感降低,但強度增加,同時硅屬于脆性元素,其添加的量越多,越難進(jìn)行后續(xù)加工;無取向硅鋼中硅元素添加量的這種矛盾導(dǎo)致低硅無取向硅鋼具有高磁感、高鐵損、低強度的特點,而高硅鋼磁感和鐵損較低,強度較高;針對目前對無取向硅鋼產(chǎn)品高磁感高強度的需求,如何能夠生產(chǎn)出較高磁感,且力學(xué)性能優(yōu)良的無取向硅鋼成了難題。
技術(shù)實現(xiàn)要素:針對現(xiàn)有無取向硅鋼在制備技術(shù)及性能上存在的上述問題,本發(fā)明提供一種基于薄帶連鑄制備高磁感高強度無取向硅鋼的方法,基于雙輥薄帶連鑄技術(shù),通過設(shè)計成分及后續(xù)的軋制和熱處理,制備性能優(yōu)良的高磁感高強度無取向硅鋼。本發(fā)明的方法按以下步驟進(jìn)行:1、按設(shè)定成分冶煉鋼水,其成分按重量百分比含C0.001~0.005%,Si2.4~3.5%,Mn0.2~2%,Alt0.35~1.0%,Ni0.4~3%,Cr0.5~4%,Sn0.02~0.2%,O≤0.005%,S≤0.005%,N≤0.005%,P≤0.005%,余量為Fe;2、將鋼水通過澆口、中間包和布流式水口澆入雙輥薄帶連鑄裝置進(jìn)行連鑄,中間包預(yù)熱溫度1100~1200℃,澆入時鋼水溫度1520~1580℃,鑄軋輥轉(zhuǎn)速50~80m/min,獲得厚度2~2.5mm的鑄帶;3、鑄帶出鑄軋輥后采用空冷方式進(jìn)行二次冷卻至室溫,然后進(jìn)行單道次熱軋,熱軋開軋溫度900~1100℃,壓下量在20~40%,熱軋后空冷至室溫,獲得熱軋板;4、將熱軋板酸洗去除表面氧化鐵皮,然后進(jìn)行5~7道次冷軋,總壓下量為69~83%,獲得厚度為0.35~0.5mm的冷軋板;5、將冷軋板進(jìn)行最終退火處理,最終退火處理是將冷軋板置于25%H2+75%N2氣氛條件下,升溫至600~850℃,保溫20~120s,并在線涂絕緣涂層,最后卷取獲得高強度高磁感無取向硅鋼的成品板。上述的高磁感高強度無取向硅鋼的成品板的{100}織構(gòu)組分體積分?jǐn)?shù)占總織構(gòu)組分體積分?jǐn)?shù)的比例為30~80%,成品板再結(jié)晶分?jǐn)?shù)比例為40~70%。上述的高磁感高強度無取向硅鋼的磁感應(yīng)強度B50為1.68~1.73T,鐵損值P10/400為25.5~37.5W/Kg,屈服強度...