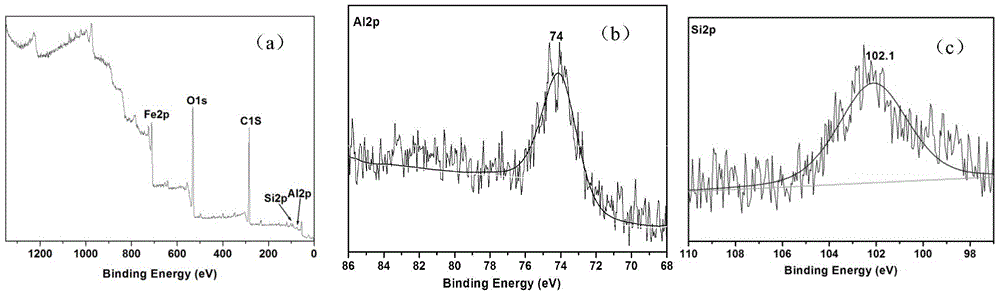
本發(fā)明涉及一種制備具有優(yōu)異耐磨、抗氧化和機(jī)械性能的陶瓷涂層的方法,屬于涂層制備領(lǐng)域。
背景技術(shù):隨著現(xiàn)代科學(xué)技術(shù)的高速發(fā)展,各種機(jī)械部件的工作條件日益苛刻,要求材料必須具有耐高溫、耐腐蝕、抗震動(dòng)、抗疲勞、抗溫度急變以及耐沖刷等性能,以致單獨(dú)的金屬材料難以滿(mǎn)足要求。陶瓷材料大多具有高熔點(diǎn)、高硬度、高化學(xué)穩(wěn)定性、熱膨脹系數(shù)小、摩擦系數(shù)小和無(wú)延展性等特點(diǎn)。但是陶瓷的塑性變形差,抗熱振和抗疲勞性差,對(duì)應(yīng)力集中和裂紋敏感、質(zhì)脆,使其應(yīng)用受到一定限制。因此,利用在金屬表面加陶瓷涂層的方法,制備既有金屬?gòu)?qiáng)度和韌性,又有陶瓷耐高溫、耐腐蝕、耐磨損等優(yōu)點(diǎn)的復(fù)合材料,越來(lái)越受重視。目前陶瓷涂層的制備方法有化學(xué)氣相沉積法(CVD)、溶膠–凝膠法、電致發(fā)熱法、聚合物先驅(qū)體轉(zhuǎn)化法(PDC)等。PDC法具有原料選取范圍廣、制備工藝簡(jiǎn)單和先驅(qū)體的裂解溫度較低等優(yōu)點(diǎn),并且可以對(duì)陶瓷材料的結(jié)構(gòu)進(jìn)行設(shè)計(jì),以改變產(chǎn)物的組成、結(jié)構(gòu)和性能,滿(mǎn)足不同材料的使用要求。由于先驅(qū)體的裂解產(chǎn)物為陶瓷材料,其高溫性能穩(wěn)定且與陶瓷基體的熱膨脹系數(shù)接近;同時(shí)先驅(qū)體作為有機(jī)高分子材料又具有流動(dòng)性好、成形方便以及結(jié)構(gòu)、組分可設(shè)計(jì)等特點(diǎn)。因此,PDC法開(kāi)創(chuàng)了從有機(jī)物制備無(wú)機(jī)物的新領(lǐng)域,實(shí)現(xiàn)了陶瓷制備工藝的革命性創(chuàng)新。在陶瓷涂層材料設(shè)計(jì)方面,碳化硅(SiC)作為人造強(qiáng)共價(jià)鍵的非氧化物陶瓷材料,具有離子鍵和共價(jià)鍵結(jié)構(gòu),鍵能高,原子間結(jié)合力強(qiáng),表面自由能低,原子間距小,堆積致密,無(wú)自由電子運(yùn)動(dòng)。這些特性賦予了SiC陶瓷材料高熔點(diǎn)、高硬度、高剛度、高耐磨性、高絕緣絕熱能力、低熱導(dǎo)率、較小熱膨脹系數(shù)和無(wú)延展性等特征。但是SiC陶瓷的塑性變形差,抗熱震和抗疲勞性差,對(duì)應(yīng)力集中和裂紋敏感、質(zhì)脆,使其應(yīng)用受到一定限制。氧化鋁陶瓷是應(yīng)用最廣泛的一種結(jié)構(gòu)陶瓷材料,有較好的傳導(dǎo)性、機(jī)械強(qiáng)度、耐高溫性、耐腐蝕性、耐磨性。然而,氧化鋁陶瓷的斷裂強(qiáng)度、抗熱震性和抗蠕變性較差,將碳化硅和氧化鋁兩種材料復(fù)合,可得到力學(xué)性能明顯提升的SiC/Al2O3復(fù)相陶瓷。在先驅(qū)體中加入活性填料,一方面利用活性填料來(lái)提高先驅(qū)體的陶瓷產(chǎn)率,控制先驅(qū)體在裂解過(guò)程中的收縮;另一方面改善燒成體的微觀(guān)結(jié)構(gòu),提高材料的力學(xué)性能。原位生成碳化物、氮化物等納米粒子或微米級(jí)粒子,與基體構(gòu)成復(fù)相陶瓷,利用裂紋釘扎和顆粒強(qiáng)化作用,改善增強(qiáng)相與基體的界面結(jié)合,提高基體的強(qiáng)度和斷裂性。較佳的活性填料是,當(dāng)聚合物先驅(qū)體部分裂解時(shí),能與游離碳、氣態(tài)裂解產(chǎn)物、N2反應(yīng),提高陶瓷產(chǎn)率,發(fā)生恰當(dāng)?shù)捏w積膨脹,抑制陶瓷燒成體的收縮。將Al粉等活性填料引入到先驅(qū)體轉(zhuǎn)化法中,彌補(bǔ)聚合物熱處理過(guò)程中材料損傷和體積收縮,同時(shí)可以消耗氧元素,使制備的SiC/Al2O3納米復(fù)相涂層表面平整、致密,無(wú)明顯裂紋和孔洞等缺陷存在。本發(fā)明提出一種簡(jiǎn)單易行、低成本的先驅(qū)體轉(zhuǎn)化制備陶瓷涂層新方法。該方法從先驅(qū)體轉(zhuǎn)化法出發(fā),以納米SiC顆粒作為惰性填料、以金屬Al粉作為活性填料,通過(guò)在金屬零部件表面預(yù)先涂覆一層陶瓷先驅(qū)體聚合物或第二相與先驅(qū)體聚合物復(fù)合的漿料,該涂層經(jīng)干燥、固化、裂解,在一定條件下反應(yīng)生成一種或幾種覆層材料,并牢固結(jié)合在金屬零部件表面,形成一層適宜厚度、致密的SiC/Al2O3復(fù)相陶瓷。
技術(shù)實(shí)現(xiàn)要素:本發(fā)明的目的是提供一種SiC/Al2O3復(fù)相陶瓷涂層的有效制備方法。一種由先驅(qū)體轉(zhuǎn)化法制備SiC/Al2O3涂層的方法,其特征在于,由如下步驟實(shí)現(xiàn):(1)基體處理:選擇高速鋼、硬質(zhì)合金、金屬陶瓷或陶瓷中的一種為基體材料,采用機(jī)械或者電化學(xué)方法對(duì)基體表面進(jìn)行處理,使表面粗糙度0.1~1μm,然后對(duì)基體表面進(jìn)行去污和清洗處理,最后吹干基體表面水分后放入烘箱烘干備用;(2)漿料制備:在100g聚碳硅烷先驅(qū)體中,加入相對(duì)于聚合物質(zhì)量分?jǐn)?shù)為10~60%的Al粉,10~20%的SiC納米粉末,同時(shí)加入50~200mL的溶劑,攪拌分散后,使用球磨機(jī)研磨3~5小時(shí),使之成為均勻的漿料;(3)涂層制備:采用刷涂或噴涂的方式將漿料涂覆在經(jīng)過(guò)處理的基體表面;(4)固化過(guò)程:將涂層預(yù)制體放入加熱爐中,在空氣中升溫至200℃保溫2h進(jìn)行交聯(lián);(5)熱解過(guò)程:將固化后的涂層預(yù)制體在N2氛圍中進(jìn)行熱解,并且在1200℃保溫1h,隨后降至室溫;(6)增強(qiáng)處理:重復(fù)上述步驟(3)—(6)。進(jìn)一步,所述采用機(jī)械或電化學(xué)方法對(duì)基體材料表面進(jìn)行預(yù)處理,是指表面噴砂處理、表面陽(yáng)極氧化處理或微弧氧化處理。進(jìn)一步,聚碳硅烷分子量為1000~2000之間。進(jìn)一步,Al粉粒度為50~100nm;SiC納米粉末粒度為10~100nm。該方法可在金屬材料等的表面制備優(yōu)異耐磨、抗氧化和機(jī)械性能良好的陶瓷涂層。與現(xiàn)有的陶瓷涂層相比,本發(fā)明的陶瓷涂層具有如下優(yōu)點(diǎn):(1)先驅(qū)體轉(zhuǎn)化法可通過(guò)有機(jī)先驅(qū)體分子設(shè)計(jì)和工藝來(lái)控制陶瓷的組成和結(jié)構(gòu),原料及基體組成選取范圍廣。(2)先驅(qū)體的原料為液態(tài)聚合物,可以借用高分子加工工藝制備出形狀復(fù)雜的近尺寸的復(fù)合材料零部件。(3)制備工藝簡(jiǎn)單,漿料的制備僅需要分散和研磨兩個(gè)步驟,通過(guò)刷涂或噴涂的方式涂覆于基體表面。固化預(yù)處理和高溫裂解反應(yīng)可在同一臺(tái)設(shè)備內(nèi)進(jìn)行,便于操作。(4)機(jī)械性能優(yōu)異:在保持材料較好韌性和高溫性能的同時(shí),可大幅提高材料的強(qiáng)度和彈性模量,SiC/Al2O3納米復(fù)相涂層的硬度為12.3GPa,平均模量為160GPa。(5)涂層厚度為10~22μm,增強(qiáng)體表面無(wú)污染,避免了與基體浸潤(rùn)不良的問(wèn)題,涂層與基體的界面結(jié)合良好。附圖說(shuō)明圖1是本發(fā)明制備的SiC/Al2O3納米復(fù)相涂層的XRD譜圖圖2是本發(fā)明制備的SiC/Al2O3納米復(fù)相涂層的XPS譜圖圖中:(a)涂層的全譜;(b)Al2p譜峰;(c)Si2p譜峰圖3是本發(fā)明制備的SiC/Al2O3納米復(fù)相涂層的截面SEM照片具體實(shí)施方式下面結(jié)合附圖和具體實(shí)施例對(duì)本發(fā)明做進(jìn)一步說(shuō)明。實(shí)施例1取分子量在1000~2000之間的聚碳硅烷100g,取相對(duì)于聚碳硅烷質(zhì)量分?jǐn)?shù)為10%的Al粉,粒徑為20nm的SiC納米粉末10g,攪拌后加入對(duì)二甲苯溶劑90mL,攪拌分散后,使用球磨機(jī)研磨3~5小時(shí),使之成為均勻的漿料。利用浸漬-提拉法將得到的漿料涂覆于基體材料上,浸漬和提拉的速度為4cm·min-1?;w材料為45鋼,尺寸為10mm×20mm×1.0mm,并且被打磨、拋光到1μm。在涂覆前,基體都經(jīng)超聲清洗,然后經(jīng)蒸餾水和丙酮沖洗并吹干。涂層預(yù)制體經(jīng)干燥,在空氣中升溫至200℃保溫2h進(jìn)行交聯(lián),交聯(lián)后的涂層在N2氛圍中進(jìn)行熱解,并且在1200℃保溫1h,隨后降至室溫。將已制得的涂層預(yù)制體再次利用浸漬-提拉法涂覆先驅(qū)體漿料,然后進(jìn)行交聯(lián)和固化處理,最終得到以45鋼為基底材料的陶瓷涂層,厚度約為10μm,硬度為12.3GPa,彈性模量為160GPa。下面對(duì)照附圖作進(jìn)一步說(shuō)明。圖1為SiC/Al2O3納米復(fù)相涂層的XRD譜圖。圖中36.5°、60.1°和71.9°處的衍射峰分別對(duì)應(yīng)于β-SiC的(111)、(220)和(311)晶面;其它衍射峰對(duì)應(yīng)的是α-Al2O3和45鋼基體的晶面,說(shuō)明該涂層主要由α-Al2O3和β-SiC組成。圖2為SiC/Al2O3納米復(fù)相涂層的XPS譜圖。從圖2(a)全譜中可以看出該涂層中確實(shí)含有SiC、Al2O3。圖2(b)是涂層的Al2p譜圖,其結(jié)合能位置為74.0eV,與α-Al2O3的Al2p標(biāo)準(zhǔn)譜吻合;圖2(c)是涂層的Si2p譜圖,其結(jié)合能位置為102.1eV,表明涂層的Si元素以Si4+狀態(tài)呈現(xiàn);XPS數(shù)據(jù)進(jìn)一步說(shuō)明SiC/Al2O3納米復(fù)相涂層的主要成分為α-Al2O3和β-SiC,這與XRD結(jié)果一致。圖3為SiC/Al2O3納米復(fù)相涂層的截面SEM照片。從圖中可以看出,SiC陶瓷涂層與金屬基體之間有一層熱生長(zhǎng)過(guò)渡層(TGO),TGO層的出現(xiàn)使陶瓷涂層與金屬基體之間的結(jié)合更加緊密。實(shí)施例2取分子量在1000~2000之間的聚碳硅烷100g,取相對(duì)于聚碳硅烷質(zhì)量分?jǐn)?shù)為30%的Al粉,粒徑為20nm的SiC納米粉末10g,攪拌后加入對(duì)二甲苯溶劑100mL,攪拌分散后,使用球磨機(jī)研磨3~5小時(shí),使之成為均勻的漿料。利用浸漬-提拉法將得到的漿料涂覆于基體材料上,浸漬和提拉的速度為4cm·min-1?;w材料為45鋼,尺寸為10mm×20mm×1.0mm,并且被打磨、拋光到1μm。在涂覆前,基體都經(jīng)超聲清洗,然后經(jīng)蒸餾水和丙酮沖洗并吹干。涂層預(yù)制體經(jīng)干燥,在空氣中升溫至200℃保溫2h進(jìn)行交聯(lián),交聯(lián)后的涂層在N2氛圍中進(jìn)行熱解,并且在1200℃保溫1h,隨后降至室溫。將已制得的涂層預(yù)制體再次利用浸漬-提拉法涂覆先驅(qū)體漿料,然后進(jìn)行交聯(lián)和固化處理,最終得到以45鋼為基底材料的陶瓷涂層,厚度約為18μm,硬度為12.8GPa,彈性模量為240GPa。實(shí)施例3取分子量在1000~2000之間的聚碳硅烷100g,取相對(duì)于PCS質(zhì)量分?jǐn)?shù)為60%的Al粉,粒徑為20nm的SiC納米粉末10g,攪拌后加入對(duì)二甲苯溶劑120mL,攪拌分散后,使用球磨機(jī)研磨3~5小時(shí),使之成為均勻的漿料。利用浸漬-提拉法將得到的漿料涂覆于基體材料上,浸漬和提拉的速度為4cm·min-1?;w材料為45鋼,尺寸為10mm×20mm×1.0mm,并且被打磨、拋光到1μm。在涂覆前,基體都經(jīng)超聲清洗,然后經(jīng)蒸餾水和丙酮沖洗并吹干。涂層預(yù)制體經(jīng)干燥,在空氣中升溫至200℃保溫2h進(jìn)行交聯(lián),交聯(lián)后的涂層在N2氛圍中進(jìn)行熱解,并且在1200℃保溫1h,隨后降至室溫。將已制得的涂層預(yù)制體再次利用浸漬-提拉法涂覆先驅(qū)體漿料,然后進(jìn)行交聯(lián)和固化處理,最終得到以45鋼為基底材料的陶瓷涂層,厚度約為22μm,硬度為16GPa,彈性模量為137GPa。