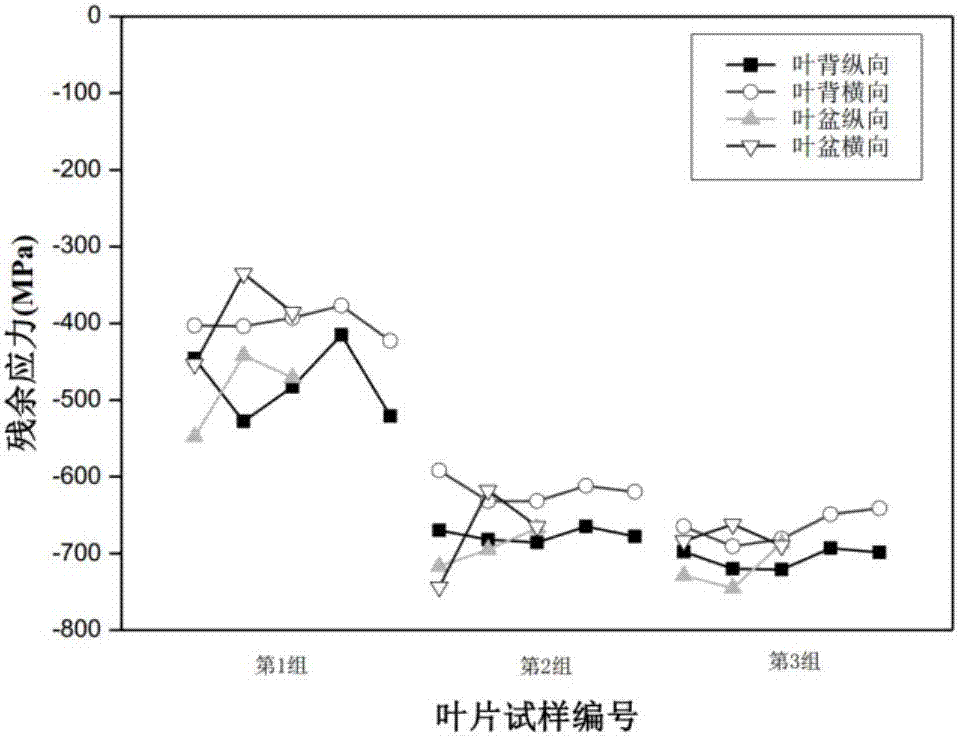
本發(fā)明屬于鈦合金葉片表面處理
技術(shù)領(lǐng)域:
,具體涉及一種鈦合金葉片殘余應(yīng)力噴丸-電磁場復(fù)合調(diào)控方法。
背景技術(shù):
:鈦合金葉片是航空發(fā)動機(jī)的關(guān)鍵構(gòu)件,對航空發(fā)動機(jī)性能和壽命有著決定性影響。鈦合金葉片在服役過程中承受高溫、振動、氣動、離心力等負(fù)荷,工作條件苛刻,其組織狀態(tài)和殘余應(yīng)力分布要求十分嚴(yán)格。一旦葉片斷裂失效將會導(dǎo)致航空發(fā)動機(jī)停車,進(jìn)而導(dǎo)致飛機(jī)出現(xiàn)災(zāi)難性故障。鈦合金葉片表面和近表面的殘余應(yīng)力分布,直接影響到葉片的工作性能和服役壽命。鈦合金葉片制造中,傳統(tǒng)工藝需要通過噴丸調(diào)控表面和近表面的殘余應(yīng)力分布。在噴丸工藝中,一方面可以有效地細(xì)化表面和近表面晶粒組織,同時產(chǎn)生殘余壓應(yīng)力,這對葉片的性能和壽命是有利的;另一方面,噴丸又會導(dǎo)致表面損傷及微裂紋,以致?lián)p害葉片性能與壽命,嚴(yán)重時甚至導(dǎo)致葉片報廢。所以發(fā)展鈦合金葉片表面和近表面的殘余應(yīng)力調(diào)控新方法,克服葉片噴丸強(qiáng)化的缺點,成為葉片制造亟待解決的世界性難題。利用電磁場調(diào)控材料殘余應(yīng)力分布,延長零件使用壽命是一種新型的技術(shù),具有處理效果好、時間短、無附加變形等優(yōu)點。目前,關(guān)于殘余應(yīng)力的電磁場調(diào)控技術(shù)已有一些文獻(xiàn)報道,但調(diào)控對象幾乎全部針對鋼鐵等鐵磁性材料,而關(guān)于針對非鐵磁性材料特別是鈦合金,采用電磁場調(diào)控的報道卻尚未見到。技術(shù)實現(xiàn)要素:為消除噴丸工藝對鈦合金葉片表面損傷的缺點,本發(fā)明提供一種鈦合金葉片殘余應(yīng)力噴丸-電磁場復(fù)合調(diào)控方法,它針對新制鈦合金葉片,在傳統(tǒng)噴丸工藝的基礎(chǔ)上,增加電磁場調(diào)控工藝,利用電磁場調(diào)控材料表層及近表層殘余應(yīng)力分布,延長零件使用壽命。本發(fā)明解決其技術(shù)問題所采用的技術(shù)方案是:一種鈦合金葉片殘余應(yīng)力噴丸-電磁場復(fù)合調(diào)控方法,包括以下步驟:先對鈦合金葉片進(jìn)行噴丸處理,使其表面產(chǎn)生塑性變形,形成冷硬層和殘余壓應(yīng)力;再在常溫下對經(jīng)噴丸處理后的鈦合金葉片進(jìn)行電磁場調(diào)控處理,處理時間為3~600s,所述電磁場由交變磁場和脈沖電場耦合而成,交變磁場的強(qiáng)度為500~30000a/m,交變磁場的頻率為1~1000hz,脈沖電場的最大峰值電流為5~20000a,脈沖電場的脈沖周期為0.01~1.0s。按上述技術(shù)方案,在噴丸處理中,利用壓縮空氣將大量直徑為φ0.1mm~φ1.2mm的彈丸以高速向鈦合金葉片表面垂直或以一定角度噴射,噴丸壓力為0.1~2.0mpa、流量為1~30kg.min-1。按上述技術(shù)方案,所述交變磁場由電源輸出的交變電流在含有鐵芯的勵磁線圈中產(chǎn)生。按上述技術(shù)方案,所述脈沖電場由脈沖電源輸出特定周期的高密度脈沖電流,并在被處理材料內(nèi)部產(chǎn)生周期性電場。按上述技術(shù)方案,所述鈦合金葉片由精密鍛造、精密鑄造或數(shù)控加工工藝制作。本發(fā)明,具有以下有益效果:本發(fā)明先對鈦合金葉片進(jìn)行噴丸處理,經(jīng)噴丸處理后的鈦合金葉片表面金屬晶體發(fā)生塑性變形,位錯、空位等晶體缺陷增加,造成晶格畸變,改變了原有晶格原子的排列狀態(tài),內(nèi)部材料能量分布不均勻,導(dǎo)致表層和近表層產(chǎn)生殘余壓應(yīng)力狀態(tài);然后再對噴丸處理后的鈦合金葉片進(jìn)行電磁場調(diào)控處理,一旦施加外能量場,晶界、亞晶界等高能量區(qū)域在外能量場能量的疊加作用下,將會超過微區(qū)相變的臨界能量,進(jìn)而發(fā)生相變析出二次相粒子,使基體相(α相)的形態(tài)發(fā)生改變,并起到強(qiáng)烈釘扎位錯和亞結(jié)構(gòu)的作用,阻礙位錯的運動及晶界、亞晶界遷移,導(dǎo)致壓應(yīng)力整體升高。本發(fā)明中,由于經(jīng)過噴丸處理的鈦合金葉片內(nèi)部能量分布并不均勻,局部發(fā)生第二相粒子析出和α相畸形的概率也不相同,于是通過施加外部電磁場,使得鈦合金葉片內(nèi)部能量較高且內(nèi)應(yīng)力也較高的微區(qū)發(fā)生相變,在一定程度上釋放部分較高的內(nèi)應(yīng)力,進(jìn)而使殘余壓應(yīng)力均勻性得到提升。本發(fā)明可以顯著增加鈦合金葉片近表層及表面壓應(yīng)力,并且使鈦合金葉片表面殘余壓應(yīng)力分布更加均勻,消除噴丸工藝對鈦合金葉片表面造成的微損傷和缺陷,可以大幅提升鈦合金葉片疲勞強(qiáng)度,延長鈦合金葉片的疲勞壽命。附圖說明下面將結(jié)合附圖及實施例對本發(fā)明作進(jìn)一步說明,附圖中:圖1a是本發(fā)明實施例中鈦合金葉片葉盆(局部)的示意圖。圖1b是本發(fā)明實施例中鈦合金葉片葉背(局部)的示意圖。圖2是本發(fā)明實施例中鈦合金葉片表面殘余應(yīng)力測試結(jié)果的示意圖。圖3是本發(fā)明實施例中鈦合金葉片沿層深分布的殘余應(yīng)力測試結(jié)果的示意圖。具體實施方式為了使本發(fā)明的目的、技術(shù)方案及優(yōu)點更加清楚明白,以下結(jié)合附圖及實施例,對本發(fā)明進(jìn)行進(jìn)一步詳細(xì)說明。應(yīng)當(dāng)理解,此處所描述的具體實施例僅用以解釋本發(fā)明,并不用于限定本發(fā)明。在本發(fā)明的較佳實施例中,一種鈦合金葉片殘余應(yīng)力噴丸-電磁場復(fù)合調(diào)控方法,包括以下步驟:先對鈦合金葉片進(jìn)行噴丸處理,使其表面產(chǎn)生塑性變形,形成冷硬層和殘余壓應(yīng)力;再在常溫下對經(jīng)噴丸處理后的鈦合金葉片進(jìn)行電磁場調(diào)控處理,處理時間為3~600s,電磁場由交變磁場和脈沖電場耦合而成,交變磁場的強(qiáng)度為500~30000a/m,交變磁場的頻率為1~1000hz,脈沖電場的最大峰值電流為5~20000a,脈沖電場的脈沖周期為0.01~1.0s。在本發(fā)明的優(yōu)選實施例中,在噴丸處理中,利用壓縮空氣將大量直徑為φ0.1mm~φ1.2mm的彈丸以高速向鈦合金葉片表面垂直或以一定角度噴射,噴丸壓力為0.1~2.0mpa、流量為1~30kg.min-1。在本發(fā)明的優(yōu)選實施例中,交變磁場由電源輸出的交變電流在含有鐵芯的勵磁線圈中產(chǎn)生。在本發(fā)明的優(yōu)選實施例中,脈沖電場由脈沖電源輸出特定周期的高密度脈沖電流,并在被處理材料內(nèi)部產(chǎn)生周期性電場。在本發(fā)明的優(yōu)選實施例中,鈦合金葉片由精密鍛造、精密鑄造或數(shù)控加工工藝制作。以下列舉本發(fā)明的三個實施例。實施例1一種鈦合金葉片殘余應(yīng)力噴丸-電磁場復(fù)合調(diào)控方法,包括以下步驟:s1、采用精密鍛造、數(shù)控加工等工藝制成鈦合金葉片;s2、對新制鈦合金葉片表面進(jìn)行噴丸處理:噴丸工藝參數(shù)為:與葉片表面呈垂直角度噴射彈丸,彈丸直徑為φ0.1mm~φ0.5mm,噴丸壓力為0.1~0.3mpa,流量為1~8kg.min-1;s3、將噴丸后的鈦合金葉片在常溫下置于特制的電磁場發(fā)生裝置中,利用電磁場對鈦合金葉片進(jìn)行處理,電磁場調(diào)控處理時間為3~10s,電磁場主要由交變磁場和脈沖電場耦合而成,磁場主要處理工藝參數(shù)為磁場強(qiáng)度500~5000a/m、頻率1~20hz,電場主要處理工藝參數(shù)為最大峰值電流5~500a、脈沖周期為0.01~0.08s。采用x射線衍射法對鈦合金葉片進(jìn)行表面殘余應(yīng)力測試,測試點布置方式如圖1a、圖1b所示,其中葉盆上布置3個測試點(圖中標(biāo)記1、2、3),葉背上布置5個測試點(圖中標(biāo)記1、2、3、4、5)。對于所有測試點均分別測試沿試樣長度與寬度方向的殘余應(yīng)力應(yīng)力分量。除此之外,對于葉背測試點2采用電解拋光剝層,測試殘余應(yīng)力沿層深方向的分布規(guī)律。本發(fā)明分三組進(jìn)行測試,第1組為新制鈦合金葉片,即噴丸前的鈦合金葉片,第1組為經(jīng)噴丸處理后的鈦合金葉片,第3組為經(jīng)噴丸和電磁場復(fù)合處理后的鈦合金葉片。殘余應(yīng)力測試結(jié)果如圖2、圖3所示,可以看出,與新制鈦合金葉片的殘余應(yīng)力相比,經(jīng)過噴丸工藝處理后,鈦合金葉片表面殘余壓應(yīng)力增大約41%~73%,但殘余壓應(yīng)力分布均勻性明顯變差,均方差最大63mpa;葉片殘余壓應(yīng)力自表面沿層深方向先緩慢降低,在層深20μm后迅速降低;與噴丸后殘余壓應(yīng)力分布相比,經(jīng)噴丸-電磁場復(fù)合調(diào)控工藝處理后鈦合金葉片殘余壓應(yīng)力均有一定程度的提升,最大提升幅度為7.7%,同時消除了噴丸工藝造成的應(yīng)力分布不均勻結(jié)果,與噴丸工藝處理后的殘余壓應(yīng)力相比,葉片沿層深方向上近表層形成了較強(qiáng)的殘余壓應(yīng)力場,其中層深35~65μm的區(qū)間殘余壓應(yīng)力最大提升了1.5倍。利用葉片疲勞強(qiáng)度試驗臺架,測試了在噴丸后和噴丸-電磁場復(fù)合調(diào)控處理后的葉片疲勞通過應(yīng)力,測試結(jié)果如表1所示。與噴丸后鈦合金葉片疲勞強(qiáng)度相比,利用噴丸-電磁場復(fù)合工藝調(diào)控殘余應(yīng)力后鈦合金葉片疲勞強(qiáng)度提升約33%~36%。表1噴丸-電磁場復(fù)合調(diào)控工藝對葉片疲勞失效強(qiáng)度的影響鈦合金葉片狀態(tài)最小失效強(qiáng)度(mpa)最大失效強(qiáng)度(mpa)噴丸工藝調(diào)控后450550噴丸-電磁場復(fù)合調(diào)控后600750實施例2一種鈦合金葉片殘余應(yīng)力噴丸-電磁場復(fù)合調(diào)控方法,包括以下步驟:s1、采用精密鍛造、數(shù)控加工等工藝制成鈦合金葉片;s2、對新制鈦合金葉片表面進(jìn)行噴丸處理:噴丸工藝參數(shù)為:與葉片表面呈80~85°角度噴射彈丸,彈丸直徑為φ0.4mm~φ0.8mm,噴丸壓力為0.8~1.2mpa,流量為5~15kg.min-1;s3、將噴丸后的鈦合金葉片在常溫下置于特制的電磁場發(fā)生裝置中,利用電磁場對葉片進(jìn)行調(diào)控處理,電磁場調(diào)控處理時間為100~160s,電磁場主要由交變磁場和脈沖電場耦合而成,磁場主要處理工藝參數(shù)為磁場強(qiáng)度10000~15000a/m、頻率40~50hz,電場主要處理工藝參數(shù)為最大峰值電流8000~120000a、脈沖周期為0.45~0.75s。采用x射線衍射法對葉片進(jìn)行表面殘余應(yīng)力測試,測試點布置方式及測試方法與實施例1相同。與新制葉片表面殘余應(yīng)力相比,經(jīng)噴丸-電磁場復(fù)合調(diào)控工藝處理后葉片殘余壓應(yīng)力提升了17%-60%,殘余應(yīng)力均方差值減少了24mpa,即消除了噴丸工藝造成的應(yīng)力分布不均勻結(jié)果;同時葉片沿層深方向上近表層形成了較強(qiáng)的殘余壓應(yīng)力場,其中層深15~35μm區(qū)域殘余壓應(yīng)力較噴丸后提升了76%。利用葉片疲勞強(qiáng)度試驗臺架,測試了在噴丸后和噴丸-電磁場復(fù)合調(diào)控處理后的葉片疲勞通過應(yīng)力。與噴丸后葉片疲勞強(qiáng)度相比,利用噴丸-電磁場復(fù)合工藝調(diào)控殘余應(yīng)力后葉片疲勞強(qiáng)度提升約9%~11%。實施例3一種鈦合金葉片殘余應(yīng)力噴丸-電磁場復(fù)合調(diào)控方法,包括以下步驟:s1、采用精密鍛造、數(shù)控加工等工藝制成鈦合金葉片;s2、噴丸工藝中,采用彈丸對鈦合金材料表面進(jìn)行:噴丸工藝參數(shù)為:與葉片表面呈60~75°角度噴射彈丸,彈丸直徑為φ0.8mm~φ1.2mm,噴丸壓力為1.8~2.0mpa,流量為25~30kg.min-1;s3、將噴丸后的鈦合金葉片在常溫下置于特制的電磁場發(fā)生裝置中,利用電磁場對葉片進(jìn)行處理,處理時間為500~600s,磁場主要處理工藝參數(shù)為磁場強(qiáng)度25000~30000a/m、頻率800~1000hz,電場主要處理工藝參數(shù)為最大峰值電流18000~20000a、脈沖周期為0.8~1.0s。采用x射線衍射法對葉片進(jìn)行表面殘余應(yīng)力測試,測試點布置方式及測試方法與實施例1相同。與新制葉片表面殘余應(yīng)力相比,經(jīng)噴丸-電磁場復(fù)合調(diào)控工藝處理后葉片殘余壓應(yīng)力提升了17%-60%,殘余應(yīng)力均方差值減少24mpa,即消除了噴丸工藝造成的應(yīng)力分布不均勻結(jié)果;同時葉片沿層深方向上近表層形成了較強(qiáng)的殘余壓應(yīng)力場,其中層深15~35μm區(qū)域殘余壓應(yīng)力較噴丸后提升了90%。利用葉片疲勞強(qiáng)度試驗臺架,測試了在噴丸后和噴丸-電磁場復(fù)合調(diào)控處理后的葉片疲勞通過應(yīng)力。與噴丸后葉片疲勞強(qiáng)度相比,利用噴丸-電磁場復(fù)合工藝調(diào)控殘余應(yīng)力后葉片疲勞強(qiáng)度提升約43%~45%。應(yīng)當(dāng)理解的是,對本領(lǐng)域普通技術(shù)人員來說,可以根據(jù)上述說明加以改進(jìn)或變換,而所有這些改進(jìn)和變換都應(yīng)屬于本發(fā)明所附權(quán)利要求的保護(hù)范圍。當(dāng)前第1頁12