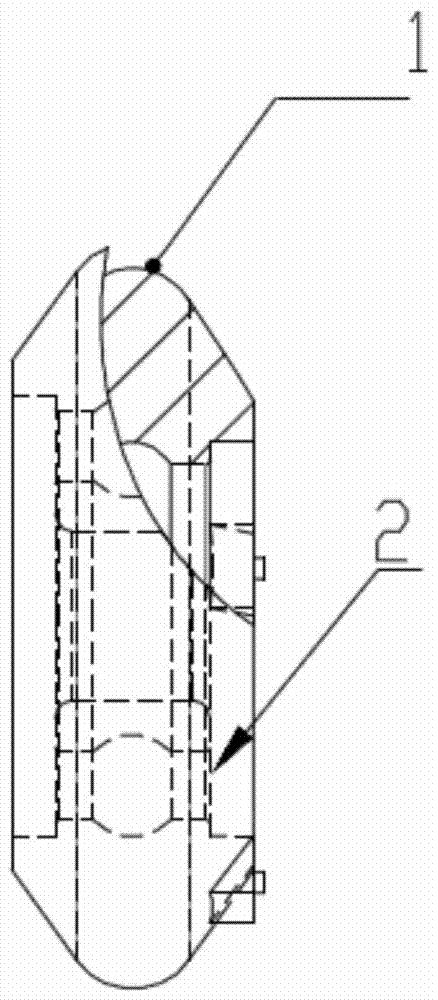
本發(fā)明涉及一種聚氨酯滾輪及其注塑工藝,通過此注塑工藝制備得到的滾輪制品,其聚氨酯胎圈與金屬輪轂具備良好的粘結(jié)性能,廣泛適用于自動扶梯滾輪、門掛輪等領(lǐng)域。
背景技術(shù):目前制造聚氨酯滾輪有兩種傳統(tǒng)工藝方法:注塑工藝和澆注工藝。注塑工藝一般程序為:先用熱塑性聚氨酯粒子注塑滾輪胎圈,再將輪轂通過低壓機過盈壓裝入聚氨酯胎圈內(nèi),使胎圈包緊輪轂,從而制得滾輪;其中熱塑性聚氨酯可選用聚酯MDI+抗水解劑熱塑性聚氨酯粒子,金屬輪轂可選用鋁合金或45#鋼,以及軸承可選用6203、6204等標準鋼鐵軸承。注塑工藝包括以下步驟:1)、聚氨酯胎圈注塑成型:使用160-260T低壓注塑機注塑聚氨酯胎圈,由注塑模具控制制品包膠尺寸,胎圈注塑固化成型周期為65-70秒,注塑完成后注塑模具自動打開,操作工取出成型完畢的滾輪制品;2)、將聚氨酯胎圈脫模后放入100℃烘箱進行16小時后熟化作業(yè);3)、再將輪轂通過低壓壓機過盈壓裝入聚氨酯胎圈內(nèi),使胎圈包緊輪轂;得到不帶軸承的滾輪制品;4)、將金屬輪轂包膠完成的聚氨酯滾輪進行軸承裝配,得到帶軸承的聚氨酯滾輪制品。注塑工藝使用的設備成本低,注塑設備成本:20-30萬元/套設備及注塑模具成本:3-4萬元/套模具/臺注塑機。注塑程序簡單,生產(chǎn)效率高;以100毫米外徑聚氨酯扶梯梯級運行滾輪為例,注塑成型時間為65-70秒/循環(huán),產(chǎn)量為1200-1300件/班(8小時)。人工成本低:每臺注塑需要2名操作員工;聚氨酯材料成本低:熱塑性聚氨酯材料均價為30-45元/公斤。但是由于金屬輪轂與聚氨酯胎圈之間是通過低壓壓機過盈壓裝配制得,因此輪轂與聚氨酯胎圈之間是完全沒有粘結(jié)力的,不能滿足使用需求。傳統(tǒng)注塑工藝生產(chǎn)的滾輪為例,其在20公斤負載,50米/分鐘運行速度的環(huán)境下,僅僅運行8-10分鐘就會出現(xiàn)胎圈脫出導致滾輪損壞的缺陷,而在<=150公斤負載,50米/分鐘運行速度的環(huán)境下,也只能正常運行2000小時。因此傳統(tǒng)注塑工藝制備的滾輪胎圈與輪轂的粘結(jié)力差,不能滿足高性能的需要。對于胎圈與金屬輪轂之間粘結(jié)力大于35牛頓/毫米的高性能滾輪制品,例如自動扶梯滾輪,一般需要采用熱固性聚氨酯和預噴膠處理好的金屬輪轂的高溫澆注工藝進行制作;其中熱固型聚氨酯可選用聚醚TDI聚氨酯預聚體,粘結(jié)劑可選用100-120℃高溫反應型聚氨酯膠粘劑,金屬輪轂可選用鋁合金或45#鋼,以及軸承可選用6203、6204等標準鋼鐵軸承。澆注工藝包括以下步驟:1)、對鋁合金輪轂噴膠面使用石英砂?;蜩F砂粒進行預噴砂打毛作業(yè);2)、對噴砂后輪轂進行表面脫脂清潔作業(yè);3)、對鋁合金輪轂與聚氨酯粘接面使用100-120℃高溫反應型聚氨酯膠粘劑進行噴膠;4)、將噴膠后的金屬輪轂放置于濕度<75%,于5-30℃環(huán)境中干燥2-3小時;5)、將噴膠后的干燥的金屬輪轂及滾輪澆注模具放入120℃烘箱預烘2-2.5小時;6)、將金屬輪轂放入澆注模具中,通過澆注模具控制制品包膠尺寸,使用兩組分或三組分低壓聚氨酯彈性體澆注機在輪轂外側(cè)澆注液態(tài)熱固性聚氨酯材料;7)、將澆注完成制品與澆注模具放入100-120℃烘道內(nèi),進行12-15分鐘液態(tài)聚氨酯高溫固化成型作業(yè);8)、熱固性聚氨酯成型完畢后,將制品脫模并放入100℃烘箱進行16小時后熟化作業(yè),得到滾輪制品;9)、將金屬輪轂包膠完成的聚氨酯滾輪進行軸承裝配,得到帶軸承的聚氨酯滾輪制品。通過此澆注工藝制備得到的滾輪制品,其金屬輪轂(鋁合金或45#鋼)與熱固性聚醚TDI聚氨酯預聚體形成的胎圈之間的粘結(jié)強度均達到了45-55牛頓/毫米,粘結(jié)性能高,能很好的滿足自動扶梯對其滾輪的高性能要求。以熱固性聚氨酯澆注工藝生產(chǎn)的某聚氨酯自動扶梯梯級運行滾輪為例,其規(guī)格為:外徑100毫米,寬度25毫米,內(nèi)徑20毫米,聚氨酯胎圈厚10毫米,硬度為95(邵氏A);鋁合金輪轂厚16毫米,裝配62042RS標準軸承。其在重載200公斤的條件下以50米/分鐘的速度下,可正常運行2000小時,且滾輪無脫膠,聚氨酯破損等缺陷。裝梯后可正常運行5年無質(zhì)量缺陷。因此,高性能聚氨酯滾輪通常需要澆注工藝生產(chǎn)。但是傳統(tǒng)澆注工藝也存在多個不足:1)、設備成本高,低壓澆注設備成本為70-80萬元/臺;另外如預熱烘道,烘箱,真空脫泡機,氮氣注入機,預攪拌機等附加組件,設備成本通常在110-120萬元/套;2)、生產(chǎn)效率低,澆注工藝聚氨酯固化成型需要20-25分鐘/循環(huán),一條澆注生產(chǎn)線產(chǎn)量為550-570件/班(8小時工作制);3)、人工成本高:4-5名操作人員;4)、材料成本高:目前熱固性聚氨酯常用材料聚醚TDI聚氨酯預聚體價格為50-85元/公斤。本發(fā)明目的在于克服通過傳統(tǒng)注塑和澆注工藝制備滾輪制品的各自不足,如傳統(tǒng)注塑工藝制得的聚氨酯滾輪其胎圈和金屬輪轂無粘結(jié)力,而傳統(tǒng)澆注工藝的生產(chǎn)效率低,設備、材料和人力的成本都較高。本發(fā)明旨在提供一種聚氨酯滾輪的新注塑工藝,其整合了傳統(tǒng)注塑和澆注工藝的優(yōu)點,其采用的設備成本、材料成本和人力成本低,生產(chǎn)效率高,且制得的滾輪制品的金屬輪轂和聚氨酯胎圈之間具備良好的粘結(jié)力(大于35牛頓/毫米),且具有高承載動態(tài)性能。
技術(shù)實現(xiàn)要素:本發(fā)明的發(fā)明思路在于吸取了傳統(tǒng)注塑工藝生產(chǎn)效率高,投資成本低,澆注工藝產(chǎn)品性能高的特點,將傳統(tǒng)注塑與澆注的優(yōu)勢結(jié)合;采用改良的注塑工藝生產(chǎn)出高性能要求的滾輪,該滾輪的金屬輪轂與聚氨酯胎圈間粘合力大于35牛頓/毫米,具有高承載動態(tài)性能。本發(fā)明提供了一種聚氨酯滾輪的注塑工藝,該聚氨酯滾輪的胎圈與金屬輪轂具有大于35牛頓/毫米的粘結(jié)力,其特征在于,該方法包括以下步驟:1)、對金屬輪轂的噴膠面進行預噴砂打毛作業(yè);2)、對步驟1)得到的金屬輪轂進行表面脫脂清潔作業(yè);3)、對步驟2)得到的金屬輪轂的噴膠面使用高溫反應型粘結(jié)劑進行預噴膠處理;4)、將步驟3)得到的預噴膠處理的金屬輪轂,在濕度≤75%下,在5-30℃環(huán)境中,初步干燥處理2-3小時;5)、將步驟4)得到的初步干燥的預噴膠處理的金屬輪轂在110-120℃下,預熱2-10小時;6)、將步驟5)得到的預噴好粘結(jié)劑的金屬輪轂先放入注塑模腔定位、固定后合模,再使用低壓注塑機將液態(tài)熱塑性聚氨酯材料由澆注機螺桿射入注塑模具膠口中,膠口為多點扇形均勻分布,且進膠方式為多點膠口同時進膠,使液態(tài)熱塑聚氨酯材料能在極短的時間內(nèi)在注塑模具內(nèi)匯流成胎圈的形狀,熱塑性聚氨酯材料與金屬輪轂的噴膠層的粘結(jié)劑充分接觸、反應約65-70秒后,從注塑模具中取出成型的滾輪制品;7)、將步驟6)得到的滾輪制品進行后熟化處理,得到聚氨酯滾輪。本發(fā)明的一種實施方式是將步驟7)得到的滾輪制品進行軸承裝配,得到帶有軸承的聚氨酯滾輪。本發(fā)明的一種實施方式中,所述步驟1)中采用石英砂粒或鐵砂粒預噴砂對金屬輪轂進行打毛作業(yè);且金屬輪轂由鋁合金或碳鋼材料制得。本發(fā)明的一種實施方式中,所述步驟3)中所述高溫反應性粘結(jié)劑是指使用在聚氨酯與鋁合金或碳鋼材料間,通過140-210℃的高反應溫度使聚氨酯與鋁合金或碳鋼材料間產(chǎn)生大于35牛頓/毫米的高粘結(jié)力的高性能高溫反應型粘結(jié)劑;該粘結(jié)劑可選自英國西邦公司的等粘結(jié)劑。本發(fā)明的一種實施方式中,所述步驟6)中所述熱塑性聚氨酯材料是指反應型滑劑含量低于0.3%非反應型滑劑、且能保證快速注塑周期的聚酯MDI+抗水解劑的熱塑性聚氨酯材料;該聚氨酯材料可選用BAYER公司的型號為U90、U95的TPU熱塑性粒子或95邵氏A的TPU材料。本發(fā)明的一種實施方式中,所述步驟6)中所述的膠口為多點扇形分布,其中多點是指超過兩點;優(yōu)選為3-8點。本發(fā)明的一種實施方式中,所述步驟7)的后熟化處理條件為:在80-100℃,干燥10-16小時;最佳后熟化條件為100℃,10小時。為了能通過注塑工藝生產(chǎn)金屬輪轂與聚氨酯胎圈間粘合力大的、且承載動態(tài)性能可以媲美澆注工藝生產(chǎn)的滾輪,本發(fā)明從五方面創(chuàng)新性地改進了傳統(tǒng)的注塑工藝:第一、選用特殊的熱塑性聚氨酯材料。普通熱塑性聚氨酯材料為保證注塑時螺桿順暢注塑周期短的工藝性能,在聚氨酯材料內(nèi)通常含有0.3-0.5%反應型滑劑,但反應型滑劑會與金屬輪轂表面的粘結(jié)劑進行反應,從而影響粘結(jié)劑與聚氨酯胎圈的粘結(jié)性能。因此,為了保證注塑生產(chǎn)的滾輪制品的粘結(jié)性能與傳統(tǒng)澆注滾輪制品具有相當?shù)恼辰Y(jié)性能,即粘結(jié)力大于35牛頓/毫米;發(fā)明人選擇了反應型滑劑含量低于0.3%、且能保證快速注塑周期的特殊聚酯MDI+抗水解劑的熱塑性聚氨酯材料進行生產(chǎn)。此類熱塑性聚氨酯材料屬性為MDI+抗水解劑;具體可以選用BAYER公司的型號為U90、U95的TPU熱塑性粒子或95邵氏A的TPU材料等。第二、選用特殊膠粘劑。由于選用的聚氨酯成型溫度為200-220℃,如果選用傳統(tǒng)澆注工藝時使用的100-120℃反應型聚氨酯膠粘劑,則會由于膠粘劑與聚氨酯的反應溫度不一致導致膠粘劑與聚氨酯胎圈反應不充分,從而造成金屬輪轂與聚氨酯胎圈的粘結(jié)力差甚至沒有粘結(jié)力的缺陷;因此,發(fā)明人選用了200-220℃高溫反應型特殊聚氨酯膠粘劑。此類高溫反應型膠粘劑屬性為聚氨酯與金屬反應性粘結(jié)劑,具體可以選用英國西邦公司的等粘結(jié)劑。第三、生產(chǎn)工藝改進。發(fā)明人采用特殊的注塑工藝方法:1)工序更變:不同于傳統(tǒng)聚氨酯滾輪注塑工序:即先使用熱塑性聚氨酯粒子注塑滾輪胎圈,再將輪轂通過低壓壓機過盈壓裝入聚氨酯胎圈內(nèi),使胎圈包緊輪轂,輪轂與胎圈之間是沒有粘結(jié)力。本發(fā)明是將用高溫反應型特殊聚氨酯膠粘劑進行預噴膠處理后的金屬輪轂放入注塑模具,使用注塑機在輪轂外側(cè)高溫下注塑聚氨酯胎圈,膠粘劑與聚氨酯在高溫注塑過程中,反應后固化,從而得到輪轂與胎圈之間具有高粘結(jié)力(一般大于35牛頓/毫米)的高性能滾輪制品。2)工藝參數(shù)改變-提高注塑溫度、注塑速度、降低保壓壓力。傳統(tǒng)聚氨酯注塑工藝中注塑溫度通常在170-195℃之間,這樣的注塑溫度不足以使200-220℃快速反應型膠粘劑與聚氨酯及金屬輪轂完全反應,導致聚氨酯胎圈與鋁合金或鋼等金屬輪轂之間的粘結(jié)力不佳,則滾輪負載運行時出現(xiàn)脫膠,胎圈破損缺陷,導致產(chǎn)品質(zhì)量不合格。發(fā)明人將注塑溫度提高至200-210℃之間,同時為了防止熱塑性聚氨酯材料在高溫注射成型過程中出現(xiàn)燒焦、窩氣缺陷,將注塑速度加快5-8%,而保壓壓力降低3-5%,從而使聚氨酯材料在高速注射過程中能達到200-205℃的高料溫,能與快速反應型聚氨酯膠粘劑充分反應,從而提高聚氨酯胎圈與鋁合金或鋼等金屬輪轂之間的粘結(jié)性能,并以高速注塑時較低保壓壓力的方式,輔助高速注塑TPU時消除窩氣缺陷,保證熱塑性聚氨酯胎圈質(zhì)量。第四、注塑模具結(jié)構(gòu)的改變。傳統(tǒng)注塑工藝中只注塑聚氨酯胎圈的模腔結(jié)構(gòu),而本發(fā)明是將預噴好粘結(jié)劑的金屬輪轂先放入注塑模腔定位、固定后合模直接注塑聚氨酯胎圈到金屬輪轂粘結(jié)面,從而滾輪制品成型。第五、改進模具的進膠方式:傳統(tǒng)注塑工藝中,聚氨酯胎圈由模腔結(jié)構(gòu)一點進膠匯流成型,而在本發(fā)明中,為了使熱塑聚氨酯材料在液態(tài)時以極短的時間內(nèi)在注塑模具內(nèi)匯流成胎圈的形狀,并與金屬輪轂表面的粘結(jié)劑在高溫下充分反應而提高了粘結(jié)性能,將進膠方式由一點式該改進為多點或者多點扇形式進膠,從而高速匯流成型。優(yōu)選地,多點扇形式進膠為均勻多點扇形式進膠。優(yōu)選地,多點扇形式進膠為3-8點式進膠。多點扇形進膠既減少了注塑時間,又提高了金屬輪轂與胎圈間的粘結(jié)性能。術(shù)語解釋PU是指聚氨酯。TPU是指熱塑性聚氨酯彈性體。MDI是指二苯基甲烷二異氰酸酯。TDI是指甲苯二異氰酸酯。附圖說明圖1顯示了本發(fā)明工藝中的一出四注塑模具示意圖,該模具具備三點扇形均勻分布膠口(1)。圖2顯示了注塑滾輪產(chǎn)品的基本結(jié)構(gòu):最外層為TPU胎圈(1),內(nèi)部為金屬軸承(2),金屬軸承(2)與TPU胎圈(1)之間由粘結(jié)劑粘結(jié)。圖3顯示了本發(fā)明工藝制備的滾輪制品的性能測試結(jié)果圖。發(fā)明效果相比選用熱固性聚氨酯彈性體的傳統(tǒng)澆注工藝,本發(fā)明的改進的熱塑性聚氨酯彈性體注塑成型技術(shù)有以下三點優(yōu)勢:其一、在金屬輪轂與胎圈的粘結(jié)性能方面,選用高溫反應型熱塑性聚氨酯彈性體經(jīng)本發(fā)明注塑工藝制備的聚氨酯滾輪優(yōu)于選用熱固性聚氨酯彈性體經(jīng)傳統(tǒng)澆注工藝制備的滾輪;粘結(jié)力測試結(jié)果對比見表1.表1.粘結(jié)力測試結(jié)果對比其二、改進后的注塑工藝比傳統(tǒng)澆注工藝生產(chǎn)效率高約4-5倍,傳統(tǒng)澆注工藝的生產(chǎn)效率為110-150件/人/班(8小時);而改進后的注塑工藝的生產(chǎn)效率是500-650件/人/班(8小時)。其三、在材料成本上,改進后的注塑工藝比傳統(tǒng)澆注工藝低40%;傳統(tǒng)澆注工藝選用的熱固性聚氨酯價格為50-80元/公斤,而改進后的注塑工藝選用的熱塑性聚氨酯價格為30-45元/公斤。其四、改進后的注塑工藝比傳統(tǒng)澆注工藝設備成本低。以下實施例僅僅是為了輔助理解本發(fā)明,并非因此限定本發(fā)明的范圍,凡是不脫離說明書中描述的本發(fā)明精神和范圍下所做任何等效助劑、工序、步驟替換或改變,或直接或間接見本發(fā)明運用在相關(guān)的技術(shù)領(lǐng)域,均包括在本發(fā)明專利的保護范圍之內(nèi)。具體實施例實施例1制備不帶軸承的聚氨酯滾輪,包括以下步驟:1)、對金屬輪轂的噴膠面進行預噴砂打毛作業(yè);2)、對步驟1)得到的金屬輪轂進行表面脫脂清潔作業(yè);3)、對步驟2)得到的金屬輪轂的噴膠面使用高溫反應型粘結(jié)劑進行預噴膠處理;4)、將步驟3)得到的預噴膠處理的金屬輪轂,在濕度≤75%下,在5-30℃環(huán)境中,初步干燥處理2-3小時;5)、將步驟4)得到的初步干燥的預噴膠處理的金屬輪轂在110-120℃下,預熱2-10小時;6)、將步驟5)得到的預噴好粘結(jié)劑的金屬輪轂先放入注塑模腔定位、固定后合模,再使用160-260T低壓注塑機將液態(tài)熱塑性聚氨酯材料由澆注機螺桿射入注塑模具膠口中,膠口為多點扇形均勻分布,且進膠方式為多點膠口同時進膠,使液態(tài)熱塑聚氨酯材料能在極短的時間內(nèi)在注塑模具內(nèi)匯流成胎圈的形狀,熱塑性聚氨酯材料與金屬輪轂的噴膠層的粘結(jié)劑充分接觸、反應約65-70秒后,從注塑模具中取出成型的滾輪制品;7)、將步驟6)得到的滾輪制品進行后熟化處理,得到聚氨酯滾輪。實施例2制備帶軸承的鋁合金輪轂的聚氨酯滾輪,包括以下步驟:1)、對鋁合金輪轂的噴膠面使用石英砂粒進行預噴砂打毛作業(yè);2)、使用自動水清洗機對步驟1)得到的金屬輪轂進行表面脫脂清潔作業(yè);3)、對步驟2)得到的金屬輪轂的噴膠面使用牌號為英國西邦49C的高溫反應型粘結(jié)劑進行預噴膠處理;4)、將步驟3)得到的預噴膠處理的金屬輪轂,在濕度<75%下,在5-30℃環(huán)境中,初步干燥處理2-3小時;5)、將步驟4)得到的初步干燥的預噴膠處理的金屬輪轂放入烘箱中在110-120℃下,預熱2-10小時;6)、將步驟5)得到的預噴好粘結(jié)劑的金屬輪轂先放入注塑模腔定位、固定后合模,通過注塑模具控制制品包膠尺寸,再使用160-260T低壓注塑機將牌號為BAYERU-95的液態(tài)熱塑性MDI和抗水解劑聚氨酯粒子由澆注機螺桿射入注塑模具膠口中,膠口為3點扇形均勻分布,且進膠方式為3點膠口同時進膠,使液態(tài)熱塑聚氨酯材料能在極短的時間內(nèi)快速均勻的灌滿模腔并使聚氨酯材料快速在注塑模具內(nèi)匯流成胎圈的形狀,熱塑性聚氨酯材料與金屬輪轂的噴膠層的粘結(jié)劑充分接觸、反應,胎圈注塑固化成型周期為65-80秒,注塑完成后注塑模具自動打開,操作工取出成型完畢的滾輪制品;7)、將步驟6)得到的滾輪制品取出并放入100℃烘箱進行10-16小時后熟化作業(yè);8)、步驟7)得到的滾輪制品進行軸承裝配,得到帶軸承的聚氨酯滾輪。實施例3制備不帶軸承的聚氨酯滾輪,包括以下步驟:1)、對金屬輪轂的噴膠面進行預噴砂打毛作業(yè);2)、對步驟1)得到的金屬輪轂進行表面脫脂清潔作業(yè);3)、對步驟2)得到的金屬輪轂的噴膠面使用高溫反應型粘結(jié)劑進行預噴膠處理;4)、將步驟3)得到的預噴膠處理的金屬輪轂,在濕度≤75%下,在5-30℃環(huán)境中,初步干燥處理2-3小時;5)、將步驟4)得到的初步干燥的預噴膠處理的金屬輪轂在110-120℃下,預熱2-10小時;6)、將步驟5)得到的預噴好粘結(jié)劑的金屬輪轂先放入注塑模腔定位、固定后合模,再使用160-260T低壓注塑機將液態(tài)熱塑性聚氨酯材料由澆注機螺桿射入注塑模具膠口中,膠口為三點扇形均勻分布,且進膠方式為三點膠口同時進膠,使液態(tài)熱塑聚氨酯材料能在極短的時間內(nèi)在注塑模具內(nèi)匯流成胎圈的形狀,熱塑性聚氨酯材料與金屬輪轂的噴膠層的粘結(jié)劑充分接觸、反應約65-70秒后,從注塑模具中取出成型的滾輪制品;7)、將步驟6)得到的滾輪制品進行后熟化處理,得到聚氨酯滾輪。為了更好地實現(xiàn)注塑產(chǎn)品聚氨酯胎圈與金屬輪轂間的大于35牛頓/毫米的高粘結(jié)力又不會出現(xiàn)產(chǎn)品胎圈燒焦、縮水嚴重等不良缺陷,步驟6)中的注塑工藝參數(shù)改良為分段操作參數(shù):1、高注射溫度:第一段加溫溫度:198℃;第二段加溫溫度:210℃;第三段加溫溫度:215℃;第四段加溫溫度:195℃;第五段加溫溫度:205℃。2、高速注射:第一段注射速度:25%速度,第二段注射速度,壓力:25%;第三段注射速度,壓力:20%速度。3、降低保壓壓力:第一段保壓壓力:115bar,第二段保壓壓力:100bar。本發(fā)明工藝制備的滾輪制品的性能測試實驗測試了本發(fā)明工藝制備的滾輪制品的輪轂與聚氨酯胎圈粘結(jié)性能,測試參數(shù)為:試樣1:平均力=84.2848牛頓/毫米;最小力=55.9422牛頓/毫米;最大峰力=99.6134牛頓/毫米;平均峰力=83.0508牛頓/毫米;最小峰力=55.9422牛頓/毫米;中位峰力=99.6134牛頓/毫米試樣2:平均力=94.8886牛頓/毫米;最小力=56.4578牛頓/毫米;最大峰力=119.5669牛頓/毫米;平均峰力=97.7442牛頓/毫米;最小峰力=59.8091牛頓/毫米;中位峰力=100.2834牛頓/毫米試樣3:平均力=96.4850牛頓/毫米;最小力=65.4809牛頓/毫米;最大峰力=121.5263牛頓/毫米;平均峰力=92.4286牛頓/毫米;最小峰力=66.4088牛頓/毫米;中位峰力=96.5197牛頓/毫米性能測試結(jié)果見圖3。表2、實施例3制備的滾輪制品的輪轂與聚氨酯胎圈粘結(jié)性能測試結(jié)果被粘輪轂材料被粘聚氨酯材料粘結(jié)強度(牛頓/毫米)鋁合金熱塑性聚氨酯胎圈55-10045#鋼熱塑性聚氨酯胎圈55-100粘結(jié)力試驗結(jié)果表明:制備的滾輪制品的輪轂與聚氨酯胎圈之間具備卓越的粘結(jié)性能。測試了本發(fā)明注塑工藝制備的滾輪制品的動態(tài)壽命,試驗標準為:試驗機轉(zhuǎn)筒外徑為500毫米,高性能滾輪產(chǎn)品必須在轉(zhuǎn)速為50米/分鐘,200公斤受壓的環(huán)境下運行2000小時,運行后滾輪樣品必須仍能正常運行,胎圈、輪轂、軸承都無損壞。表3、動態(tài)壽命試驗報告:滾輪制造公司:依合斯電梯扶手(上海)有限公司使用軸承:BR62042RS胎圈材質(zhì):聚酯MDI+抗水劑95邵A硬度熱塑性聚氨酯滾輪尺寸規(guī)格:外徑100毫米,寬度25.0毫米生產(chǎn)日期:2012-6-15從表3的動態(tài)壽命試驗報告表明,本發(fā)明注塑工藝制備的熱塑性聚氨酯滾輪制品,其胎圈與鋁合金或鋼等金屬輪轂具備高粘結(jié)性能;能夠很好滿足載重電梯的動態(tài)壽命測試。