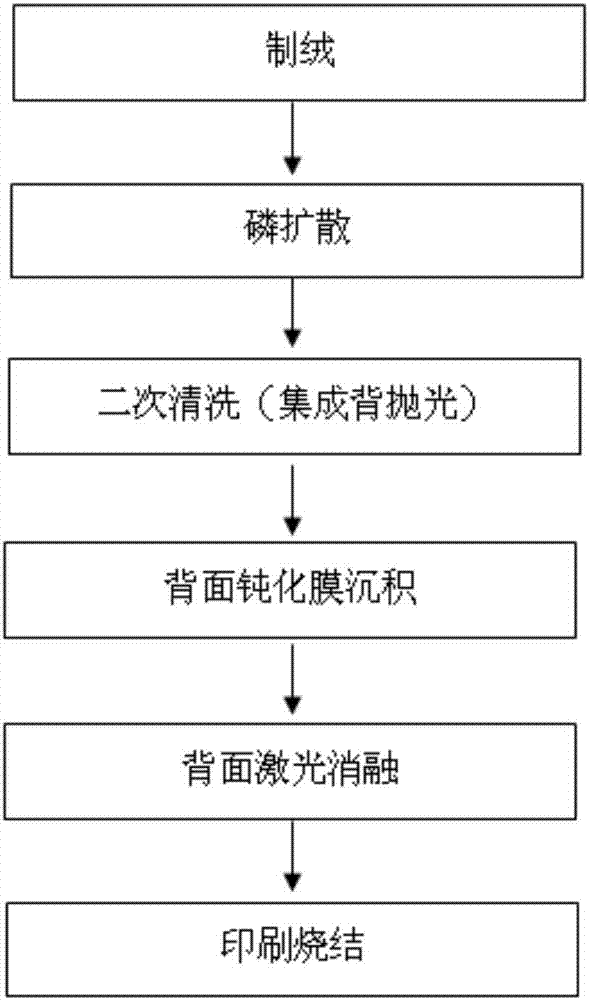
本發(fā)明屬于晶硅太陽(yáng)能電池領(lǐng)域,具體涉及一種背面拋光perc電池的制備方法。
背景技術(shù):
:晶硅太陽(yáng)能電池的有效少子壽命決定于正表面、背表面和基體復(fù)合速率?,F(xiàn)在產(chǎn)業(yè)化晶硅電池的正表面復(fù)合速率降低依靠正面沉積氮化硅減反射膜來(lái)實(shí)現(xiàn),但沒(méi)有專(zhuān)門(mén)的鈍化結(jié)構(gòu)來(lái)降低背表面復(fù)合速率。隨著晶硅太陽(yáng)能電池技術(shù)的進(jìn)步,晶硅體材料的質(zhì)量不斷提升,晶硅太陽(yáng)能電池的背表面復(fù)合問(wèn)題成為晶硅太陽(yáng)能電池效率進(jìn)一步提升的瓶頸。為了解決這一問(wèn)題,通常采用背面沉積sio2、al2o3等各種介質(zhì)膜,對(duì)背面進(jìn)行鈍化,由于采用了背面鈍化稱(chēng)為perc(passivatedemitterandrearcell)電池,常規(guī)電池工藝中只對(duì)電池正面發(fā)射結(jié)也就是emitter進(jìn)行了鈍化,鈍化膜采用的具有減反射效果的鈍化硅層,并沒(méi)有對(duì)電池背面也就是rear進(jìn)行鈍化。對(duì)于perc電池背面采用沉積薄膜的方法進(jìn)行鈍化,那么就十分有必要對(duì)背面進(jìn)行拋光處理,可以使得薄膜沉積更加均勻,特別是針對(duì)于原子層沉積ald(atomlayerdeposition)。原子層沉積氧化鋁厚度<10nm,就必須對(duì)背面進(jìn)行拋光,即便對(duì)于pecvd設(shè)備沉積,也可以降低鈍化膜膜厚,進(jìn)而能夠降低三甲基鋁耗量。由于太陽(yáng)能電池正面作為進(jìn)光面需要盡可能多的讓光進(jìn)入到電池內(nèi)部,正面必須是絨面結(jié)構(gòu),這意味著拋光只能在背面進(jìn)行。為了實(shí)現(xiàn)perc電池背面拋光,工業(yè)界構(gòu)建了多種解決途徑:第一種方法是在二次清洗階段增加酸刻蝕槽體長(zhǎng)度或反映溫度,以增加刻蝕量的方法增加拋光效果。這種方法不能與現(xiàn)有常規(guī)工藝的二次清洗設(shè)備兼容,需要新增設(shè)備;而且刻蝕量的增加會(huì)造成硅片變薄,增加后道工藝碎片率,而且還會(huì)降低電池吸收光波的有效厚度,對(duì)電池的短路電流造成影響。故在保證碎片率的前提下,反射率最多達(dá)到30-35%。第二種方法是在擴(kuò)散后先利用鏈?zhǔn)綕穹ㄔO(shè)備去除背面磷硅玻璃,然后在槽式設(shè)備中以四甲基氫氧化銨等為拋光溶液,利用正面磷硅玻璃的掩膜作用僅對(duì)背面進(jìn)行拋光,這的反射率能做到40%以上。但這種方法需要在擴(kuò)散工藝段做更改,將表面磷硅玻璃長(zhǎng)厚,同樣需要增加新的濕法設(shè)備,與常規(guī)產(chǎn)線兼容度差。第三種方法是在二次清洗階段的刻蝕槽使用堿刻蝕,反應(yīng)溫度60-80℃,反射率也能>40%。該方法除了需要購(gòu)買(mǎi)新設(shè)備外,更有研究文獻(xiàn)指出由于拋光階段使用堿溶液,溶液中金屬離子會(huì)對(duì)背面造成污染,進(jìn)而制備成的perc電池存在少子壽命低、效率低的問(wèn)題。綜上,現(xiàn)有的晶硅太陽(yáng)能電池單面拋光技術(shù)的缺點(diǎn)主要在于:1、現(xiàn)有的單面拋光工藝技術(shù),無(wú)論哪種都必須在常規(guī)產(chǎn)線上引入新的設(shè)備,例如需要增加新的濕法鏈?zhǔn)健⒉凼皆O(shè)備,或者對(duì)現(xiàn)有設(shè)備進(jìn)行較大程度改造,常規(guī)工藝的二次清洗設(shè)備喪失其利用價(jià)值,常規(guī)電池產(chǎn)線升級(jí)為perc電池產(chǎn)線設(shè)備投入成本增加。新的工藝技術(shù)引入需要投入精力進(jìn)行設(shè)備和工藝調(diào)試,對(duì)常規(guī)產(chǎn)線也是一個(gè)挑戰(zhàn)。2、為了平衡后道工序,反射率不能夠達(dá)到所設(shè)計(jì)的理想值;3、拋光效果都是基于一個(gè)宏觀尺寸,即通過(guò)表征反射率達(dá)到某一特定值進(jìn)而認(rèn)為達(dá)到了拋光效果,然而即便達(dá)到了某一反射率值,不同的拋光方法其微納結(jié)構(gòu)尺度的粗糙存在很大的差異,同樣會(huì)影響晶硅太陽(yáng)能電池的光電特性。上述的化學(xué)拋光效果都不能保證微納尺度上的平整性,如果方法不當(dāng)很容易引入一些微納結(jié)構(gòu),這些微納結(jié)構(gòu)在鈍化過(guò)程中不能被良好鈍化,很容易形成載流子捕獲中心,大幅降低晶硅電池電學(xué)性能,這也就是很多廠家遇到的雖然反射率基本相當(dāng),但是少子壽命和電池的轉(zhuǎn)換效率相差很大的原因。但是基于光伏生產(chǎn)控制成本和產(chǎn)能要求的特性,不可能引入集成電路領(lǐng)域的化學(xué)機(jī)械拋光(cmp)方法來(lái)實(shí)現(xiàn)微納尺度的平整性。因此,尋求一種新的實(shí)現(xiàn)perc電池背面拋光的制備工藝迫在眉睫。技術(shù)實(shí)現(xiàn)要素:本發(fā)明要解決的技術(shù)問(wèn)題是克服現(xiàn)有技術(shù)的不足,提供一種量產(chǎn)門(mén)檻低、運(yùn)營(yíng)成本低、尤其可實(shí)現(xiàn)微納尺度上的平整性從而大幅提升電池光電轉(zhuǎn)換效率的背面拋光perc電池的制備方法。為解決上述技術(shù)問(wèn)題,本發(fā)明采用以下技術(shù)方案:一種背面拋光perc電池的制備方法,包括以下步驟:(1)在硅片背面沉積一層保護(hù)膜,得到鍍有單面保護(hù)膜的硅片;(2)將步驟(1)所得鍍有單面保護(hù)膜的硅片進(jìn)行制絨,在制絨后的酸洗過(guò)程中去除硅片上的單面保護(hù)膜,得到單面制絨的硅片;(3)將步驟(2)所得單面制絨的硅片進(jìn)行擴(kuò)散;(4)將步驟(3)所得擴(kuò)散后的硅片進(jìn)行常規(guī)二次清洗;(5)在步驟(4)所得二次清洗后的硅片背面沉積氧化鋁/氮化硅疊層鈍化膜,然后對(duì)疊層鈍化膜進(jìn)行激光開(kāi)槽,經(jīng)絲網(wǎng)印刷和燒結(jié),得到背面拋光perc電池。上述的背面拋光perc電池的制備方法中,優(yōu)選的,所述步驟(1)中,所述硅片為金剛線切割單晶硅片或金剛線切割多晶硅硅片。上述的背面拋光perc電池的制備方法中,優(yōu)選的,所述步驟(1)中,所述保護(hù)膜為氮化硅薄膜、氧化硅薄膜或光刻膠薄膜,所述保護(hù)膜的厚度為20nm~50nm。上述的背面拋光perc電池的制備方法中,優(yōu)選的,所述步驟(1)中,采用pecvd法進(jìn)行背面沉積,沉積壓強(qiáng)為0.15mbar~0.3mbar,沉積溫度為250℃~450℃,微波功率為1000w~4000w,硅烷氣流量為100sccm~300sccm,氨氣流量為300sccm~900sccm,沉積時(shí)間為1min~5min。上述的背面拋光perc電池的制備方法中,優(yōu)選的,所述步驟(1)中,采用pecvd法進(jìn)行背面沉積,沉積壓強(qiáng)為0.15mbar,沉積溫度為450℃,微波功率為3000w,硅烷氣流量為190sccm,氨氣流量為570sccm,沉積時(shí)間為2min。上述的背面拋光perc電池的制備方法中,優(yōu)選的,所述步驟(2)中,所述制絨的溶液為氫氧化鉀水溶液,所述氫氧化鉀水溶液的質(zhì)量濃度為1%~4%,所述制絨的反應(yīng)溫度為70℃~85℃,所述制絨的反應(yīng)時(shí)間為15min~25min。上述的背面拋光perc電池的制備方法中,優(yōu)選的,所述步驟(3)中,所述擴(kuò)散的溫度為800℃~900℃,所述擴(kuò)散的完整工藝時(shí)間為90min~200min。上述的背面拋光perc電池的制備方法中,優(yōu)選的,所述步驟(4)中,所述常規(guī)二次清洗采用的設(shè)備為鏈?zhǔn)皆O(shè)備,擴(kuò)散制絨面朝上,刻蝕液為hf和hno3的混合水溶液,所述刻蝕液中hf的質(zhì)量濃度為5%~10%,所述刻蝕液中hno3的質(zhì)量濃度為10%~40%,刻蝕的溫度為8℃~15℃,刻蝕的時(shí)間為30s~120s,獲得的刻蝕量為0.1g~0.15g。上述的背面拋光perc電池的制備方法中,優(yōu)選的,在所述步驟(1)之前,還包括以下預(yù)處理步驟:將硅片進(jìn)行預(yù)清洗和去損傷層。上述的背面拋光perc電池的制備方法中,優(yōu)選的,所述預(yù)處理步驟中,所述預(yù)清洗采用的溶液為氫氧化鉀和h2o2的混合水溶液,溶液中氫氧化鉀的質(zhì)量濃度為1%~3%,溶液中h2o2的質(zhì)量濃度為0.5%~1.5%;所述去損傷層的處理時(shí)間為2min~7min,所述去損傷層處理后對(duì)所得硅片用去離子水清洗并烘干。本發(fā)明的步驟(3)中,擴(kuò)散的完整工藝時(shí)間包括:送舟、升溫、氧化、沉積磷硅玻璃、高溫推進(jìn)、降溫出舟的時(shí)間,以及自動(dòng)化、升溫、降溫等一些設(shè)備運(yùn)行需要的時(shí)間,為公知常識(shí)。本發(fā)明的步驟(4)中,常規(guī)二次清洗包括了刻蝕、堿洗、水洗等過(guò)程,通常是在同一臺(tái)設(shè)備的不同槽體中完成,工藝流程為公知技術(shù),其中刻蝕工藝最為核心。本發(fā)明保護(hù)關(guān)鍵點(diǎn)和創(chuàng)新點(diǎn)為:在perc電池制備過(guò)程中的二次清洗工藝與常規(guī)電池完全相同,制絨階段通過(guò)背面實(shí)施保護(hù)膜進(jìn)行單面制絨。背面拋光效果是通過(guò)單面制絨保留了金剛線切片特有的優(yōu)良光滑表面,實(shí)現(xiàn)了微納尺度平整性。本發(fā)明的關(guān)鍵特征在于制絨時(shí)單面存在一層保護(hù)膜,該層保護(hù)膜可以是氧化硅、氮化硅以及半導(dǎo)體領(lǐng)域應(yīng)用到的光刻膠等能夠避免制絨溶液對(duì)該保護(hù)面進(jìn)行制絨,在制絨設(shè)備中制絨槽后面的酸洗槽被同步去除掉。相當(dāng)于本發(fā)明的背面拋光perc電池只是增加了背面掩膜制備一步工藝。與現(xiàn)有技術(shù)相比,本發(fā)明的優(yōu)點(diǎn)在于:本發(fā)明提供了一種背面拋光perc電池的制備方法,目的在于量產(chǎn)門(mén)檻低、運(yùn)營(yíng)成本低的前提下實(shí)現(xiàn)微納尺度拋光效果,相比現(xiàn)有的拋光效果能夠大幅提升晶硅電池光電特性。perc電池常用工藝流程是在硅片清洗、去損傷層、制絨、擴(kuò)散、二次清洗(集成拋光,刻蝕量在0.3g以上),在硅片背面先制備氧化鋁或氧化硅鈍化層,再在這層鈍化層上制備氮化硅保護(hù)層,然后正面制備氮化硅減反射層,再將硅片背面的氧化鋁/氮化硅疊層膜通過(guò)激光開(kāi)槽,最后絲印燒結(jié)形成perc電池。本發(fā)明的技術(shù)原理在于:現(xiàn)在硅片多數(shù)為金剛線切割,切割過(guò)程已經(jīng)形成了比較光滑的表面,且該表面由于是物理方法(磨削)形成,具有微納尺度的平整性。但在制絨過(guò)程中硅片雙面被制成了絨面,反而喪失了先天的優(yōu)良結(jié)構(gòu)。如果能在制絨過(guò)程中保護(hù)該結(jié)構(gòu),即在制絨過(guò)程中實(shí)現(xiàn)單面制絨,那么就能很好的發(fā)揮該結(jié)構(gòu)的優(yōu)勢(shì)。故本發(fā)明的技術(shù)路線是:硅片清洗、去損傷層后,在背面制備保護(hù)膜,然后制絨段進(jìn)行單面制絨,制絨后去除背面保護(hù)膜,擴(kuò)散、二次清洗(常規(guī)刻蝕,刻蝕量0.1g左右),后道工序完全一致。再由于在目前的制絨設(shè)備中,出了制絨槽就會(huì)有酸洗步驟,那么背面保護(hù)膜的去除在制絨工藝中同時(shí)完成。本發(fā)明的特征在于制絨前單面制備保護(hù)膜,實(shí)現(xiàn)單面制絨,利用金剛線切割的優(yōu)勢(shì)實(shí)現(xiàn)背面單面拋光效果。該層保護(hù)膜可以是氧化硅、氮化硅以及光刻膠等。綜上,本發(fā)明的制備方法不用引入新的設(shè)備,不需要對(duì)常規(guī)工藝中擴(kuò)散和二次清洗工藝進(jìn)行調(diào)整。由于二次清洗工藝與常規(guī)電池工藝完全相同,刻蝕重量只有0.1g左右,硅片減薄量小,不會(huì)造成碎片率的上升,也不會(huì)影響電池對(duì)光的吸收厚度。最重要的是,本發(fā)明的方法實(shí)現(xiàn)了單面拋光在微納尺度上的平整性,消除了針狀的微納結(jié)構(gòu),在沉積鈍化膜層時(shí)獲得了明顯的鈍化效果增益,轉(zhuǎn)換效率增益在0.5%abs以上。本發(fā)明的方法不但可以對(duì)金剛線切割單晶硅片進(jìn)行拋光,同時(shí)可以對(duì)即將到來(lái)的金剛線切割多晶硅硅片進(jìn)行單面拋光。本發(fā)明的方法不但在制備perc電池有明顯的電性能增益,當(dāng)用于常規(guī)太陽(yáng)能電池時(shí)也能夠獲得明顯的效率增益。附圖說(shuō)明圖1為本發(fā)明實(shí)施例1背面拋光perc電池的制備方法的工藝流程圖。圖2為現(xiàn)有常用perc電池制備方法的工藝流程圖。圖3為本發(fā)明實(shí)施例和對(duì)比例工藝路線制備拋光面原子力顯微鏡線掃描曲線。具體實(shí)施方式以下結(jié)合說(shuō)明書(shū)附圖和具體優(yōu)選的實(shí)施例對(duì)本發(fā)明作進(jìn)一步描述,但并不因此而限制本發(fā)明的保護(hù)范圍。以下實(shí)施例中所采用的材料和儀器均為市售。實(shí)施例1:一種本發(fā)明的背面拋光perc電池的制備方法,如圖1所示,包括以下步驟:(1)將硅片進(jìn)行預(yù)清洗和去損傷層,硅片為金剛線切割單晶硅片(也可采用金剛線切割多晶硅硅片),預(yù)清洗溶液為氫氧化鉀和h2o2的混合水溶液,溶液中氫氧化鉀的濃度為2wt%,溶液中h2o2的濃度為1wt%,去損傷層的處理時(shí)間為5mins。處理后將所得硅片用去離子水清洗并烘干。(2)在步驟(1)得到的硅片背面沉積氮化硅薄膜作為保護(hù)膜,氮化硅薄膜的厚度為40nm,采用等離子化學(xué)氣相沉積法(pecvd法)進(jìn)行背面沉積,pecvd法的工藝參數(shù)為:沉積壓強(qiáng)為0.15mbar,沉積溫度450℃,微波功率3000w,硅烷氣流量190sccm,氨氣流量為570sccm,沉積時(shí)間2mins,得到鍍有單面保護(hù)膜的硅片。(3)將步驟(2)得到的鍍有單面保護(hù)膜的硅片采用制絨工藝進(jìn)行制絨,制絨溶液為氫氧化鉀水溶液,氫氧化鉀的濃度為2wt%,反應(yīng)溫度為80℃,反應(yīng)時(shí)間20mins。步驟(2)中制備的單面保護(hù)膜在制絨設(shè)備制絨槽后的酸洗槽中被同步去除。(4)將步驟(3)得于的單面制絨的硅片放入擴(kuò)散爐中進(jìn)行擴(kuò)散,擴(kuò)散溫度為850℃,擴(kuò)散的完整工藝時(shí)間90mins。(5)將步驟(4)擴(kuò)散后的硅片進(jìn)行二次清洗,設(shè)備為鏈?zhǔn)皆O(shè)備,二次清洗工藝與常規(guī)晶硅電池二次清洗工藝完全相同,擴(kuò)散制絨面朝上,刻蝕液為hf和hno3的混合水溶液,hf和hno3的濃度分別為5wt%和30wt%,刻蝕溫度為10℃,刻蝕時(shí)間為60s,獲得的刻蝕量為0.12g。(6)將步驟(5)二次清洗后的硅片背面先后進(jìn)行氧化鋁和氮化硅的沉積,得到氧化鋁/氮化硅疊層鈍化膜,然后在激光設(shè)備中,對(duì)背面疊層鈍化膜進(jìn)行激光開(kāi)槽,最后進(jìn)行絲網(wǎng)印刷和燒結(jié),得到背面拋光perc電池,并測(cè)試電性能。實(shí)施例2:一種本發(fā)明的背面拋光perc電池的制備方法,包括以下步驟:(1)在硅片背面沉積氧化硅薄膜作為保護(hù)膜硅片為金剛線切割單晶硅片(也可采用金剛線切割多晶硅硅片),氧化硅厚度20nm,氧化硅薄膜沉積設(shè)備為等離子體化學(xué)氣相沉積設(shè)備,所采用的pecvd法的工藝參數(shù)為沉積壓強(qiáng)為0.15mbar,沉積溫度400℃,微波功率3000w,硅烷氣流量190sccm,氨氣流量為570sccm,沉積時(shí)間5mins,得到鍍有單面保護(hù)膜的硅片。(2)將步驟(1)得到的鍍有單面保護(hù)膜的硅片采用制絨工藝進(jìn)行制絨,制絨溶液為氫氧化鉀水溶液,氫氧化鉀的濃度為2wt%,反應(yīng)溫度為75℃,反應(yīng)時(shí)間25mins。步驟(2)中制備的保護(hù)膜在制絨設(shè)備制絨槽后的酸洗槽中被同步去除。(3)將步驟(2)單面制絨的硅片放入擴(kuò)散爐中進(jìn)行擴(kuò)散(磷擴(kuò)散),擴(kuò)散溫度為820℃,擴(kuò)散的完整工藝時(shí)間為95mins。(4)將步驟(3)擴(kuò)散后的硅片進(jìn)行二次清洗,設(shè)備為鏈?zhǔn)皆O(shè)備,二次清洗工藝與常規(guī)晶硅電池二次清洗工藝完全相同,擴(kuò)散制絨面朝上,刻蝕液為hf和hno3的混合水溶液,hf和hno3的濃度分別為5wt%和30wt%,刻蝕溫度為11℃,刻蝕時(shí)間為60s,獲得的刻蝕量為0.15g。(6)在步驟(5)二次清洗后的硅片背面先后進(jìn)行氧化鋁和氮化硅的沉積,得到氧化鋁/氮化硅疊層鈍化膜,然后在激光設(shè)備中,對(duì)背面疊層鈍化膜進(jìn)行激光開(kāi)槽,最后進(jìn)行絲網(wǎng)印刷和燒結(jié),制成perc電池,并測(cè)試電性能。對(duì)比例:一種perc電池的制備方法,如圖2所示,包括以下步驟:(1)將硅片進(jìn)行制絨工藝,制絨溶液為氫氧化鉀水溶液,氫氧化鉀濃度為2wt%,反應(yīng)溫度為85℃,反應(yīng)時(shí)間20mins。(2)將制絨的硅片放入擴(kuò)散爐中進(jìn)行擴(kuò)散,擴(kuò)散溫度為850℃,完整工藝時(shí)間90mins;(3)將擴(kuò)散后的硅片進(jìn)行二次清洗,設(shè)備為鏈?zhǔn)皆O(shè)備,二次清洗工藝與常規(guī)晶硅電池二次清洗工藝完全相同,擴(kuò)散制絨面朝上,刻蝕液為hf和hno3的混合水溶液,hf和hno3的濃度分別為10wt%和30wt%,刻蝕溫度為15℃,當(dāng)刻蝕時(shí)間為60s,獲得的刻蝕量為0.1-0.15g,當(dāng)刻蝕時(shí)間為120s時(shí),獲得的刻蝕量為0.25-0.35g。(4)將二次清洗后的硅片背面進(jìn)行氧化鋁/氮化硅沉積,得到氧化鋁/氮化硅疊層鈍化膜;在激光設(shè)備中,對(duì)背面疊層鈍化膜進(jìn)行激光開(kāi)槽;最后進(jìn)行絲網(wǎng)印刷和燒結(jié)制成perc電池,并測(cè)試電性能。圖3為本發(fā)明實(shí)施例1刻蝕量為0.12g、對(duì)比例中刻蝕量分別為0.1g和0.3g時(shí),采用nt-mdt型原子力顯微鏡(afm)的線掃描圖,反應(yīng)了不同工藝微觀粗糙度情況。常規(guī)電池工藝刻蝕量為0.1g左右,反射率為10-15%,如圖3中曲線b所示,其微觀結(jié)構(gòu)高度波動(dòng)很大,且存在很多針狀微納結(jié)構(gòu),這種結(jié)構(gòu)鈍化十分困難。當(dāng)增加背面拋光時(shí)間時(shí),刻蝕量增加,如對(duì)比例中刻蝕量為0.3g,此時(shí)反射率增加到25-30%,但是仍然存在很多的針狀微納結(jié)構(gòu),如圖3中曲線c所示。本發(fā)明實(shí)施例1的微觀結(jié)構(gòu)如圖3中曲線a所示,雖然存在較寬的波谷和波峰,但是其少有針狀微納結(jié)構(gòu)。測(cè)試本發(fā)明實(shí)施例1、實(shí)施例2及對(duì)比例中制得的perc電池的電性能,測(cè)試結(jié)果如表1所示。由表1可知,本發(fā)明制得的perc電池的電性能明顯優(yōu)于常規(guī)工藝制備的perc電池,尤其在開(kāi)壓和短流方面表現(xiàn)優(yōu)異,實(shí)施例轉(zhuǎn)換效率增益在0.5%abs以上。表1本發(fā)明實(shí)施例1、實(shí)施例2及對(duì)比例中制得的perc電池平均電性能參數(shù)案例轉(zhuǎn)化效率(%)開(kāi)路電壓(mv)短路電流(a)填充因子(%)實(shí)施例121.236679.69279.74實(shí)施例220.9986659.7179.8對(duì)比例(0.1g)20.32651.89.46480.07對(duì)比例(0.3g)20.51654.39.562079.75以上所述,僅是本發(fā)明的較佳實(shí)施例而已,并非對(duì)本發(fā)明作任何形式上的限制。雖然本發(fā)明已以較佳實(shí)施例揭示如上,然而并非用以限定本發(fā)明。任何熟悉本領(lǐng)域的技術(shù)人員,在不脫離本發(fā)明的精神實(shí)質(zhì)和技術(shù)方案的情況下,都可利用上述揭示的方法和技術(shù)內(nèi)容對(duì)本發(fā)明技術(shù)方案做出許多可能的變動(dòng)和修飾,或修改為等同變化的等效實(shí)施例。因此,凡是未脫離本發(fā)明技術(shù)方案的內(nèi)容,依據(jù)本發(fā)明的技術(shù)實(shí)質(zhì)對(duì)以上實(shí)施例所做的任何簡(jiǎn)單修改、等同替換、等效變化及修飾,均仍屬于本發(fā)明技術(shù)方案保護(hù)的范圍內(nèi)。當(dāng)前第1頁(yè)12