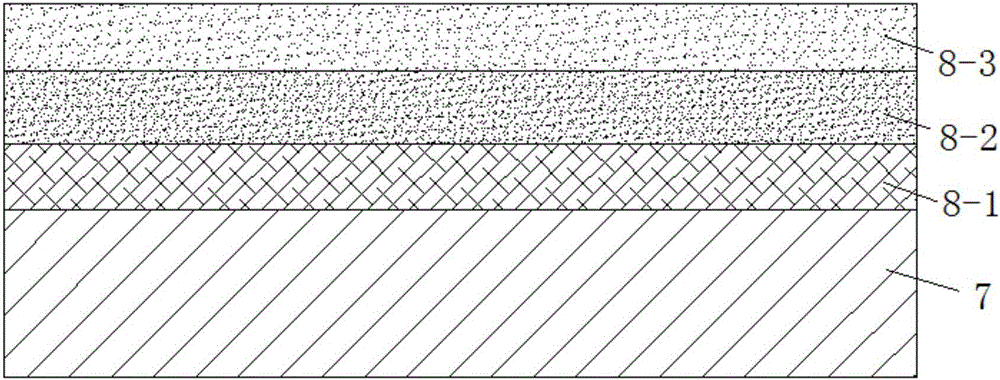
本發(fā)明涉及軸瓦,尤其涉及一種環(huán)保軸瓦。
背景技術(shù):
::軸瓦的作用是不但要能保護(hù)曲軸軸頸,而且在頻頻啟停時(shí),當(dāng)軸瓦摩擦副處于邊界潤滑或者混合潤滑狀態(tài)時(shí),也能防止曲軸軸頸的早期磨損,從而保護(hù)曲軸的運(yùn)轉(zhuǎn)可靠性。先進(jìn)的發(fā)動(dòng)機(jī)技術(shù)對(duì)軸瓦的要求越來越高;更加頻繁的啟動(dòng),啟停或混合動(dòng)力發(fā)動(dòng)機(jī)將導(dǎo)致軸瓦的早期磨損。發(fā)動(dòng)機(jī)爆發(fā)壓力的增加和發(fā)動(dòng)機(jī)的輕量化,增加了軸瓦的載荷。低粘度機(jī)油、粗糙化的曲軸表面,更高的溫度使得軸瓦早期磨損更加加劇。傳統(tǒng)結(jié)構(gòu)的軸瓦,已不滿足內(nèi)燃機(jī)技術(shù)的發(fā)展要求。在環(huán)保法規(guī)和排放標(biāo)準(zhǔn)越來越嚴(yán)格的今天,想要實(shí)現(xiàn)汽車內(nèi)燃機(jī)的環(huán)保問題,不僅是使用清潔能源和減少溫室氣體排放,更重要是其使用的零部件以及零部件制造過程要需要達(dá)到更加環(huán)保的要求。傳統(tǒng)方式所使用的含鉛元素的軸瓦材料及鍍層的,將被逐步淘汰。技術(shù)實(shí)現(xiàn)要素::為了彌補(bǔ)現(xiàn)有技術(shù)問題的不足,本發(fā)明的目的是提供一種環(huán)保軸瓦,既能防止因發(fā)動(dòng)機(jī)性能提高所造成的軸瓦早期磨損,又能滿足軸瓦在裝配使用過程中的無鉛化,同時(shí)又在軸瓦制造過程中到達(dá)無鉛化的目的,其性能大幅提高,堅(jiān)固耐用,同時(shí)又能減少摩擦,在其制造加工過程中以及裝配使用過程中實(shí)現(xiàn)環(huán)保無污染。本發(fā)明的技術(shù)方案如下:環(huán)保軸瓦,包括相對(duì)配合使用的上瓦片和下瓦片,其特征在于,所述的上瓦片和下瓦片的內(nèi)壁上設(shè)有合金層,合金層自上瓦片和下瓦片的對(duì)口面至中央底部逐漸變厚,合金層外設(shè)有電鍍無鉛減摩層。合金層采用CuSn8Ni或CuSn10Bi4材料的連續(xù)鑄造卷帶,當(dāng)采用CuSn8Ni材料的連續(xù)鑄造卷帶時(shí),成分含量為Sn:7.0~9.0%,Ni:0.7~1.3%,Cu:余量;當(dāng)采用CuSn10Bi4材料的連續(xù)鑄造卷帶時(shí),CuSn10Bi4成分含量為Sn:9~11%,Bi:3~5%,Cu:余量。所述的環(huán)保軸瓦,其特征在于,所述的電鍍無鉛減摩層有內(nèi)向外依次為電鍍鎳柵層、內(nèi)層錫銅減磨層、外層錫銅減磨層,其中電鍍鎳柵層厚度為1~3μm;內(nèi)層錫銅減磨層厚度為1~3μm,按重量百分比計(jì)含銅量為8~12%;外層錫銅減磨層厚度為15~20μm,按重量百分比計(jì)含銅量為1.5~4%。環(huán)保軸瓦,其特征在于,所述的電鍍無鉛減摩層有內(nèi)向外依次為電鍍鎳柵層、內(nèi)層錫銅減磨層、外層錫銅減磨層,其中電鍍鎳柵層厚度為1~3μm;內(nèi)層錫銅減磨層厚度為1~3μm,按重量百分比計(jì)含銅量為10%;外層錫銅減磨層厚度為15~20μm,按重量百分比計(jì)含銅量為3%。所述的環(huán)保軸瓦,其特征在于,所述的上瓦片和下瓦片內(nèi)壁依次設(shè)有合金層、電鍍無鉛減摩層后,在距離對(duì)口20°處壁厚比中央底部厚度減薄0.005~0.015mm,對(duì)口處壁厚比中央底部厚度減薄0.02~0.04mm。本發(fā)明的優(yōu)點(diǎn)是:1、本發(fā)明原材料合金層不含重金屬鉛元素,更加符合環(huán)保要求;該原材料為連續(xù)鑄造的卷帶,合金成分的晶粒度更細(xì),使用性能更高;2、本發(fā)明逐漸減薄式壁厚可以使產(chǎn)品在裝配后,形成更合理的油膜間隙;3、本發(fā)明電鍍無鉛減摩層采用無鉛雙層錫銅鍍層,提高了減摩層硬度,加工和使用過程中不含鉛元素,達(dá)到環(huán)保的同時(shí)提高了產(chǎn)品耐磨性能。附圖說明:圖1為本發(fā)明的結(jié)構(gòu)示意圖。圖2為本發(fā)明電鍍無鉛減摩層的分層結(jié)構(gòu)示意圖。圖3為本發(fā)明無鉛材料和傳統(tǒng)銅合金材料疲勞強(qiáng)度對(duì)比圖。具體實(shí)施方式:參見附圖:環(huán)保軸瓦,包括相對(duì)配合使用的上瓦片1和下瓦片2,上瓦片1和下瓦片2的內(nèi)壁上設(shè)有合金層3,合金層3自上瓦片和下瓦片的對(duì)口面至中央底部逐漸變厚,合金層3外設(shè)有電鍍無鉛減摩層4。合金層3采用CuSn8Ni或CuSn10Bi4材料的連續(xù)鑄造卷帶,當(dāng)采用CuSn8Ni材料的連續(xù)鑄造卷帶時(shí),成分含量為Sn:7.0~9.0%,Ni:0.7~1.3%,Cu:余量;當(dāng)采用CuSn10Bi4材料的連續(xù)鑄造卷帶時(shí),CuSn10Bi4成分含量為Sn:9~11%,Bi:3~5%,Cu:余量。電鍍無鉛減摩層4有內(nèi)向外依次為電鍍鎳柵層4-1、內(nèi)層錫銅減磨層4-2、外層錫銅減磨層4-3,其中電鍍鎳柵層4-1厚度為1~3μm;內(nèi)層錫銅減磨層4-2厚度為1~3μm,按重量百分比計(jì)含銅量為10%;外層錫銅減磨層4-3厚度為15~20μm,按重量百分比計(jì)含銅量為3%。上瓦片1和下瓦片2內(nèi)壁依次設(shè)有合金層3、電鍍無鉛減摩層4后,在距離對(duì)口20°處壁厚比中央底部厚度減薄0.005~0.015mm,對(duì)口處壁厚比中央底部厚度減薄0.02~0.04mm。具體分析如下:1、合金層成分分析:本發(fā)明所使用的合金層3位于上瓦片1和下瓦片2和電鍍無鉛減摩層4之間,合金層3選用CuSn8Ni或CuSn10Bi4這兩種牌號(hào)的無鉛連續(xù)鑄造的卷帶。傳統(tǒng)的方式所使用的銅基軸瓦原材料,最常用的是合金層牌號(hào)為CuPb24Sn或CuPb20Sn4這兩種,為了驗(yàn)證本發(fā)明所使用的無鉛合金層與傳統(tǒng)工藝中含鉛銅基合金層的優(yōu)勢(shì)及可靠性,做如下對(duì)比:材料成分及硬度對(duì)比:序號(hào)材料牌號(hào)主要成分含量,重量百分比(%)合金硬度ACuSn8NiSn:7.0~9.0,Ni:0.7~1.3,Cu:余量70~130HBBCuSn10Bi4Sn:7.0~9.0,Bi:3~5,Cu:余量76~114HBCCuPb24SnPb:19~27,Sn:0.6~2.0,Cu:余量45~70HBDCuPb20Sn4Pb:18~24,Sn:3.0~4.5,Cu:余量65~90HB上表中,A和B為本發(fā)明所使用的無鉛合金材料,C和D均為傳統(tǒng)的含Pb銅基合金材料,從上表中可以看出,本發(fā)明所使用的材料合金層均為不含重金屬元素Pb,并且其硬度也高于傳統(tǒng)含Pb材料的硬度。合金材料中添加的Pb元素,其主要作用為增強(qiáng)材料的抗咬粘性,提高其疲勞強(qiáng)度。本發(fā)明中使用的無鉛合金層中,不含鉛元素,為了驗(yàn)證其對(duì)使用性能的影響,我們進(jìn)行了疲勞強(qiáng)度的試驗(yàn),實(shí)驗(yàn)條件為:轉(zhuǎn)速2680r/min,試驗(yàn)采用梯級(jí)增載法,每級(jí)載荷增量為5MPa,每級(jí)載荷下運(yùn)轉(zhuǎn)3.12×106循環(huán),試驗(yàn)獲得的對(duì)比圖3如下:通過圖3中可以看出,本發(fā)明所使用的無鉛合金材料,其疲勞強(qiáng)度值與傳統(tǒng)的銅合金材料相比,接近或優(yōu)于傳統(tǒng)材含鉛合金材質(zhì)。通過比對(duì)專利申請(qǐng)?zhí)?01010506167.7,該專利合金層牌號(hào)為CuSn8InNi,其疲勞強(qiáng)度試驗(yàn)方法與本發(fā)明所使用的試驗(yàn)方法略有不同,雖然其極限值也可以達(dá)到150MPa,但因?yàn)槠涑煞种泻蠭n元素,制造成本更高,加工方法更加復(fù)雜。通過比對(duì)正申請(qǐng)專利號(hào)201410607907.4,該專利正在進(jìn)入實(shí)審狀態(tài)中,其合金層牌號(hào)為CuNi2,該材料由于沒有Sn等較軟的元素,使軸瓦應(yīng)該具備的嵌藏性和順應(yīng)性較差。上述兩項(xiàng)發(fā)明或正在實(shí)審的專利,雖然也能做到成分中無Pb的效果,但是其制造方法均為燒結(jié)而成,燒結(jié)片材在燒制過程中,必須要對(duì)鋼板先進(jìn)行打磨,這樣合金粉末鋪上之后,勢(shì)必會(huì)在結(jié)合層產(chǎn)生大小不一的尖角毛刺,這些尖角毛刺為后期使用過程中的疲勞源點(diǎn)。同時(shí)燒結(jié)片材會(huì)因?yàn)橥读喜痪鶆蛞约皽囟炔环€(wěn)定,會(huì)在合金層中產(chǎn)生氣孔,結(jié)合層也會(huì)因?yàn)樘幚聿划?dāng)而產(chǎn)生合金脫落。而本發(fā)明所使用的兩種合金材質(zhì)均為連續(xù)鑄造的卷帶。原材料合金層不含重金屬鉛元素,更加符合環(huán)保要求;同時(shí)由于制造過程為連續(xù)鑄造的卷帶,鋼板光潔,合金與鋼板的結(jié)合層更加平整緊密,同時(shí)連續(xù)鑄造的合金成分的晶粒度更細(xì),使用性能更高。2、合金層厚度尺寸分析:在本發(fā)明中,將軸瓦壁厚加工為逐漸均勻減薄樣式。這種設(shè)計(jì)便于油楔形成,可以使油膜達(dá)到一個(gè)穩(wěn)定的流體動(dòng)力潤滑。減少軸承的振動(dòng)和磨損,傳統(tǒng)加工中,壁厚均為經(jīng)由底部到達(dá)20°范圍內(nèi)厚度一致。這種厚度方式,會(huì)導(dǎo)致軸瓦的載荷被限制在一個(gè)較小的軸瓦表面積上,降低了油膜厚度的最大壓力點(diǎn)。此外這種方式會(huì)使軸瓦和軸承之間不能形成一個(gè)均勻的間隙,不合理的油隙會(huì)導(dǎo)致不穩(wěn)定的流體動(dòng)力潤滑及曲軸的振動(dòng)。這樣會(huì)導(dǎo)致軸瓦的早期疲勞和故障。在加工時(shí)候,我們將中央底部厚度作為整個(gè)軸瓦的最厚部位,距對(duì)口20°處壁厚比中央底部厚度減薄0.005~0.015mm,對(duì)口處壁厚比中央底部厚度減薄0.02~0.04mm左右,通過這種方式可以使軸瓦存在一個(gè)逐漸減薄間隙,當(dāng)軸瓦在通過合理的扭力裝配之后,能形成一個(gè)的圓整的封閉環(huán),油膜間隙均勻合理。3、電鍍無鉛減摩層:由于軸瓦既要承載重載荷,又要兼具保護(hù)曲軸的功能,這就要求軸瓦既要有高硬度的合金層,同時(shí)在合金層表面需要一層較軟的電鍍減磨層。國內(nèi)傳統(tǒng)軸瓦使用的電鍍減磨層絕大多數(shù)為為PbSnCu這種三元減磨層。這種含鉛鍍層由于Pb的存在,使軸瓦的磨合性能、嵌藏性、順應(yīng)性、抗咬粘性等良好,其弊端在于使軸瓦在磨損、腐蝕、穴蝕、疲勞等方面的失效現(xiàn)象增加,降低了軸瓦的使用壽命,同時(shí)在環(huán)保日益嚴(yán)峻的今天,Pb污染使其逐漸被淘汰。本發(fā)明的無鉛電鍍減磨層,采用無鉛雙層錫銅電鍍層,其結(jié)構(gòu)順序由內(nèi)向外依次為合金層3,在合金層3先電鍍厚度為1~3μm的鎳柵層4-1,然后再電鍍內(nèi)層錫銅減磨層4-2和外層錫銅減磨層4-3。同傳統(tǒng)的PbSnCu三元電鍍層一樣,無鉛雙層錫銅電鍍層與鎳柵層之間要有一層防擴(kuò)散層,來阻止銅的擴(kuò)散,以免降低軸瓦的耐磨性和抗疲勞性。按照此思路,當(dāng)SnCu鍍層在運(yùn)轉(zhuǎn)中受熱時(shí),鍍層中的銅元素會(huì)向鎳柵層中擴(kuò)散。為了防止銅的擴(kuò)散而影響鍍層性能,必須要使銅的擴(kuò)散達(dá)到最小。因此本發(fā)明在電鍍減磨層的過程中,采用雙層錫銅鍍層的結(jié)構(gòu):在靠近合金層4的內(nèi)層錫銅減磨層4-2中提高含銅量,在靠近曲軸的外層錫銅減磨層4-3中降低了銅含量,使外層錫銅減磨層4-3的成分和結(jié)構(gòu)滿足了鍍層表面所要求的性能,內(nèi)層層錫銅減磨層4-2高含銅量可以阻止外層中的銅向內(nèi)層擴(kuò)單擴(kuò)散,從而使表層始終保持SnCu鍍層本身的優(yōu)良性能.為了甄選出內(nèi)層錫銅減磨層,4-2中銅的具體含量,我們測(cè)試不同銅含量的鍍層,加熱到130°后觀察其顯微結(jié)構(gòu),通過比對(duì)最終選定內(nèi)層錫銅減磨層中按重量百分比計(jì)銅的含量為10%。為了確定外層錫銅減磨層4-3中的銅含量,我們采用咬粘咬試驗(yàn)來進(jìn)行篩選。我們選用軸瓦尺寸為∮50×寬B20×eT1.5,轉(zhuǎn)速為3600R/min,潤滑油入口溫度100℃,軸頸粗糙度為Rz0.8。載荷每次遞增5MPa。當(dāng)瓦背溫度超過200℃或扭矩達(dá)到預(yù)定極限值,則說明軸瓦出現(xiàn)咬粘,通過實(shí)驗(yàn)確定按重量百分比計(jì)含銅量為2%,將其厚度設(shè)定為1~3μm。通過含銅量與硬度、抗拉強(qiáng)度、延伸率的關(guān)系,最終選定合理的含銅量應(yīng)為1.5%~3.0%之間,將其厚度設(shè)定為15~20μm。模擬軸瓦使用環(huán)境并用X射線顯微分析儀,來試驗(yàn)鍍層隨溫度變化的情況,當(dāng)錫銅鍍層130℃的溫度下運(yùn)行1000h后,銅損失約50%,而雙層錫銅鍍層的銅損失量則低很多,至少能保持原有含銅量的70%。因此我們確定了內(nèi)層含銅量10%和外層含銅量為3%的雙層鍍層結(jié)構(gòu),當(dāng)該結(jié)構(gòu)在使用過程中,由于熱擴(kuò)散原理,使外層耐磨表面的銅含量保持在2%左右。這樣可以保持其原有的抗咬粘性能、耐磨和抗疲勞等性能。最后對(duì)雙層結(jié)構(gòu)鍍層進(jìn)行疲勞試驗(yàn)、磨損試驗(yàn)、穴蝕和腐蝕試驗(yàn),實(shí)驗(yàn)表明本發(fā)明的無鉛雙層錫銅結(jié)構(gòu)的抗疲勞性與傳統(tǒng)的PbSnCu三元電鍍層無差異,耐磨性能提高了2倍以上,抗穴蝕能力增加了30倍以上,抗腐蝕能力的提高,在1000h后達(dá)到8倍隨時(shí)間延長后續(xù)還會(huì)增加。本發(fā)明的雙層錫銅鍍層與傳統(tǒng)的PbSnCu三元電鍍層鍍層相比,具有更好的耐磨性、抗腐蝕、抗穴蝕性能,并且其抗疲勞和抗咬粘性能沒有降低。雙鍍層能有效阻止銅的熱擴(kuò)散,防止由于顆粒磨損腐蝕疲勞和穴蝕引起的鍍層損傷,提高了軸瓦的使用壽命。申請(qǐng)?zhí)?01020217382.0硬錫鍍層軸瓦,減摩層由錫銅合金鍍層和純錫鍍層構(gòu)成,錫銅合金鍍層電鍍?cè)阪嚃艑由?,純錫鍍層電鍍?cè)阱a銅合金鍍層上。錫銅合金鍍層按重量百分比計(jì)由錫85~98%,其余為銅的二元合金構(gòu)成,純錫鍍層按重量百分比計(jì)由100%的錫構(gòu)成,錫銅合金鍍層的厚度為3~5μm,純錫鍍層的厚度為3~5μm,鎳柵層的厚度為1~3μm。該專利雖然也為錫銅鍍層結(jié)構(gòu)的減磨層,但其只是單層錫銅結(jié)構(gòu),其弊端在于受熱后,銅元素會(huì)向鎳柵層擴(kuò)散,導(dǎo)致銅含量降低,同時(shí)該專利所描述的錫銅合金二元合金減磨層只有3~5μm的厚度,按照電鍍減磨層厚度為0.01~0.05mm的要求,其減磨層厚度太薄達(dá)不到電鍍層應(yīng)有的功能。申請(qǐng)?zhí)?01020217383.5雙硬錫鍍層軸瓦,第一錫銅合金鍍層按重量百分比計(jì)由錫85~95%,第二錫銅合金鍍層按重量百分比計(jì)由錫85~98%,第一錫銅合金鍍層的厚度為3~5μm,第二錫銅合金鍍層的厚度為5~8μm,純錫鍍層的厚度為3~5μm。鎳柵層的厚度為1~3μm。該專利雖然也有雙層錫銅二元合金結(jié)構(gòu),但其弊端是該專利的第一錫銅合金鍍層和第二錫銅合金鍍層的含量幾乎沒有明顯差別,該專利同樣忽略了錫銅合金鍍層受熱后的銅擴(kuò)散問題,雙層銅鉛合金未能有效起到阻止擴(kuò)散的作用。當(dāng)前第1頁1 2 3