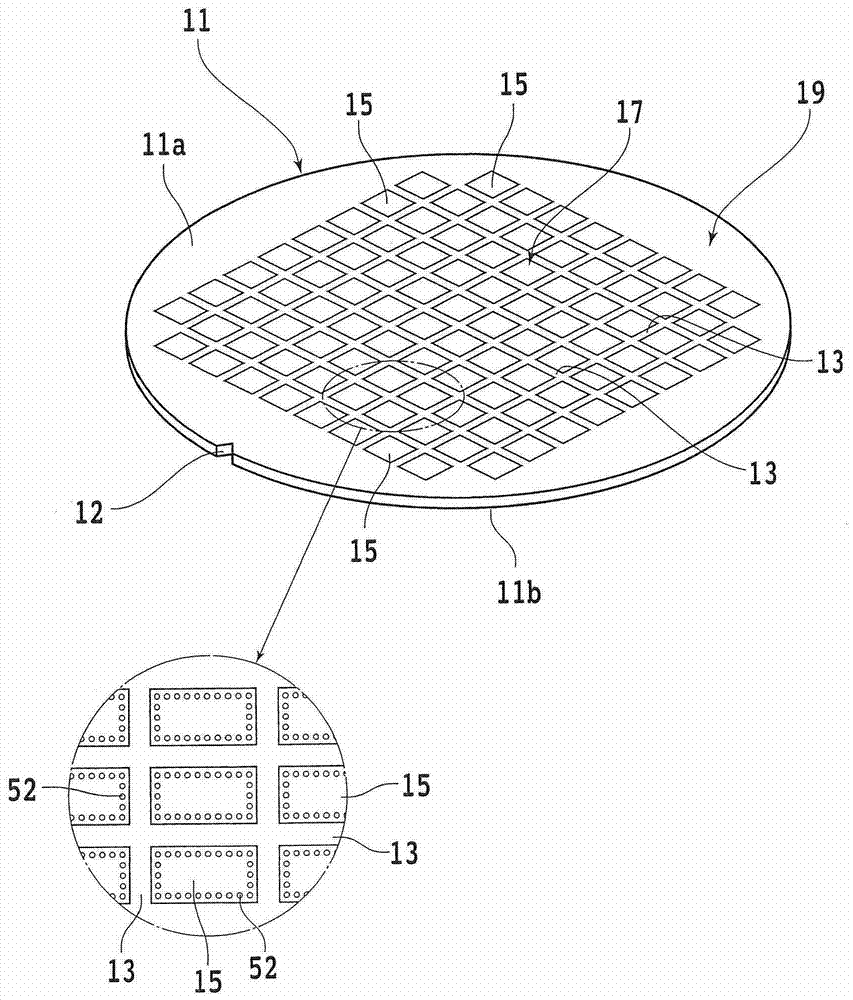
本發(fā)明涉及半導體器件晶片的加工方法,更詳細地講,涉及使薄化后的半導體器件晶片的操作容易進行的技術。
背景技術:在半導體器件晶片、光器件晶片等表面具有多個器件的晶片的加工中,例如,進行對晶片的背面磨削的薄化處理,以使晶片的厚度達到50μm以下。與更厚的晶片相比,晶片的厚度達到50μm以下的晶片的操作(處理)變得非常困難。產生了例如在晶片的外周產生破損或剛性顯著降低的問題。因此,已知下述技術:在利用粘接劑等將晶片的表面(器件面)粘貼至由玻璃或硅構成的載體晶片(也稱作支承晶片、支承板)上的狀態(tài)下,實施晶片的背面磨削(參照專利文獻1)。專利文獻1:日本特開2004-207606號公報然而,在半導體晶片的表面形成有多個凸塊的帶凸塊的器件晶片存在下述問題:粘接劑進入由凸塊形成的凹凸部位,在將器件從載體晶片剝離后,將所述進入微細的凹凸的粘接劑完全除去非常困難。而且,擔心由于殘留的粘接劑而引起器件不合格。另一方面,帶凸塊的器件晶片由形成有器件的器件區(qū)域和未形成有器件的外周剩余區(qū)域構成,但由于在外周剩余區(qū)域未形成有凸塊,所以器件區(qū)域和外周剩余區(qū)域的上表面高度(以器件晶片的背面為基準的高度)不同。因此,在將晶片保持于保持工作臺并磨削晶片的背面使晶片變薄時,假設未從下側保持外周剩余區(qū)域,則外周剩余區(qū)域成為從保持工作臺浮起的狀態(tài),因此擔心晶片破損。
技術實現要素:本發(fā)明正是鑒于以上問題點而完成的,其目的在于提供一種帶凸塊的器件晶片的加工方法,即使對帶凸塊的器件晶片也能夠進行薄化加工而不使其破損,并且,不會產生因粘接劑附著到由凸塊形成的凹凸部位而導致器件不合格。根據技術方案1記載的發(fā)明,提供一種帶凸塊的器件晶片的加工方法,所述帶凸塊的器件晶片具備器件區(qū)域和圍繞器件區(qū)域的外周剩余區(qū)域,所述器件區(qū)域在由形成于表面的交叉的多條分割預定線劃分出的各個區(qū)域分別形成有器件,器件具有多個凸塊,所述帶凸塊的器件晶片的加工方法的特征在于,所述帶凸塊的器件晶片的加工方法具備:載體晶片準備步驟,在所述載體晶片準備步驟中,準備載體晶片,所述載體晶片具備深度與凸塊的高度相當的凹部和與器件晶片的外周剩余區(qū)域對應并圍繞凹部的環(huán)狀凸部,在環(huán)狀凸部的上表面形成有環(huán)狀槽,所述載體晶片用于支承器件晶片的表面,所述凸塊形成于器件晶片的與器件區(qū)域對應的區(qū)域;粘接劑配設步驟,在所述粘接劑配設步驟中,在載體晶片的環(huán)狀槽以從環(huán)狀凸部的上表面突出的方式配設粘接劑,并且將所述粘接劑的量設定為不從所述環(huán)狀槽溢出的量;晶片貼合步驟,在所述晶片貼合步驟中,在實施粘接劑配設步驟后,使載體晶片的表面和器件晶片的表面貼合并借助粘接劑將器件晶片固定于載體晶片,并且將凸塊收納于載體晶片的凹部;以及薄化步驟,在所述薄化步驟中,在實施晶片貼合步驟后,對器件晶片的背面?zhèn)冗M行磨削或研磨,以將器件晶片薄化至預定的厚度,所述帶凸塊的器件晶片的加工方法還具備切離步驟,在所述切離步驟中,在實施薄化步驟后,利用切削刀具向器件晶片的、與載體晶片的環(huán)狀槽的內周和凹部的外周之間的區(qū)域對應的部位切入,從而將器件晶片的器件區(qū)域從載體晶片切離。在本發(fā)明中,僅將器件晶片的與外周剩余區(qū)域對應的區(qū)域借助粘接劑粘貼至載體晶片,因此不會在器件和凸塊附著粘接劑,不會產生粘接劑除去的必要性,和因粘接劑殘留而引起的器件不合格的不良情況。并且,在載體晶片的與器件晶片的器件區(qū)域對應的中央區(qū)域形成有凹部,因此在磨削器件晶片的背面使其變薄時,凸塊被收納于凹部,并且外周剩余區(qū)域由載體晶片的環(huán)狀凸部支承,從而能夠防止器件晶片的破損。附圖說明圖1是晶片的立體圖。圖2是說明晶片貼合步驟的立體圖。圖3是形成有凹部的載體晶片的剖視圖。圖4是形成有環(huán)狀槽的載體晶片的剖視圖。圖5是切削裝置的外觀的立體圖。圖6是示出基于切削裝置的環(huán)狀槽的形成的立體圖。圖7是示出基于切削裝置的環(huán)狀槽的形成的局部剖側視圖。圖8是實施粘接劑配設步驟后的載體晶片的剖視圖。圖9是說明晶片貼合步驟的剖視圖。圖10是貼合后的晶片和載體晶片的剖視圖。圖11是示出薄化步驟的立體圖。圖12是薄化步驟后的貼合于載體晶片的晶片的剖視圖。圖13是說明切離步驟的剖視圖。標號說明2:磨削裝置;11:器件晶片;11a:表面;11b:背面;12:缺口;15:器件;17:器件區(qū)域;19:外周剩余區(qū)域;52:凸塊;61:載體晶片;61a:表面;62:環(huán)狀凸部;63:環(huán)狀槽;64:粘接劑;67:凹部。具體實施方式下面,參照附圖對本發(fā)明的實施方式詳細地進行說明。圖1所示的器件晶片11(下面,也簡單記作“晶片11”)由例如厚度為700μm的硅晶片形成,在表面11a呈格子狀地形成有多條分割預定線(間隔道)13,并且,在由所述多條分割預定線13劃分出的多個區(qū)域分別形成有器件15。這樣構成的晶片11具備形成有器件15的器件區(qū)域17和圍繞器件區(qū)域17的外周剩余區(qū)域19。在晶片11的外周形成有作為表示硅晶片的結晶方位的標記的缺口12。而且,如圖1的放大圖所示,在各器件15的四邊形成有多個突起狀(球狀)的凸塊52。所述凸塊52被配置成從器件15的表面突出,由此,使得器件區(qū)域17的上表面高度比外周剩余區(qū)域19的上表面高度高。如上所述,在本發(fā)明中作為加工對象的晶片11構成為帶凸塊的器件晶片,其具備器件區(qū)域17和圍繞器件區(qū)域17的外周剩余區(qū)域19,并且器件15具有多個凸塊52,所述器件區(qū)域17在由形成于表面的交叉的多條分割預定線13劃分出的各個區(qū)域分別形成有器件15。而且,在本發(fā)明的器件晶片的加工方法中,在后面說明的薄化步驟中,為了防止例如因薄化至50μm以下的晶片11的破損或剛性下降而引起的不良情況的發(fā)生,實施準備如圖2所示的載體晶片61的載體晶片準備步驟。載體晶片61由圓盤狀的部件構成,用于支承翻轉的晶片11的表面11a。載體晶片61由例如硅、玻璃、陶瓷、金屬(例如不銹鋼)、合成樹脂等材料形成,并且構成為即使對在后面說明的薄化步驟中薄化至例如50μm以下的晶片11也能夠穩(wěn)定地進行支承。如圖3所示,在載體晶片61形成有深度與凸塊的高度H(參照圖9)相當的凹部67,所述凸塊形成于器件晶片11的與器件區(qū)域17對應的區(qū)域??梢酝ㄟ^在未圖示的車削裝置對載體晶片61的中心部分及其周圍進行車削來形成該凹部67。而且,通過形成凹部67,形成與器件晶...