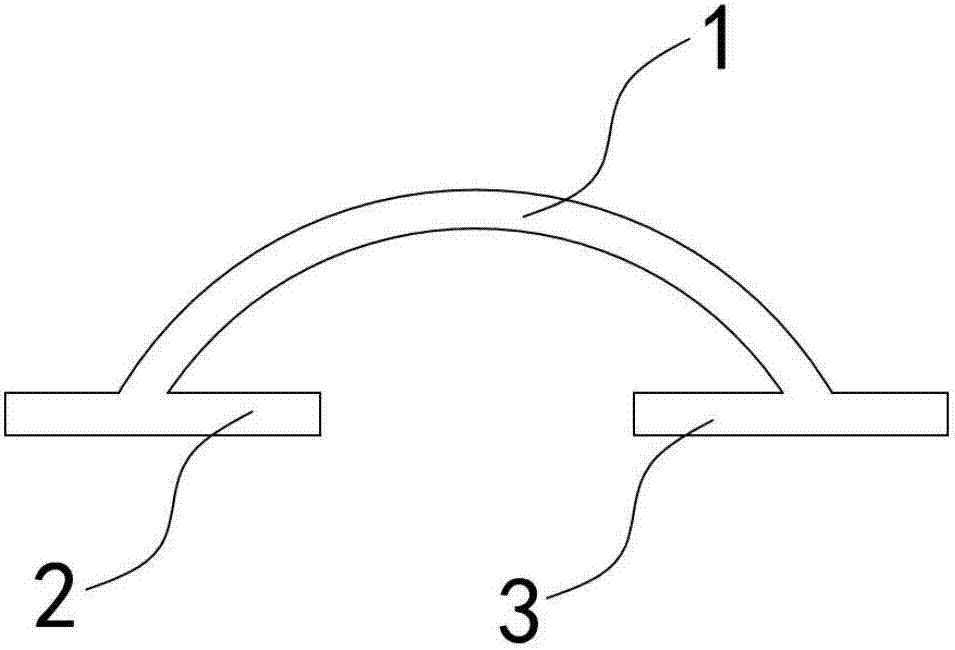
本發(fā)明涉及復(fù)合材料真空灌注成型
技術(shù)領(lǐng)域:
,尤其涉及一種復(fù)合材料真空灌注工藝成型用導(dǎo)流管。
背景技術(shù):
:隨著復(fù)合材料技術(shù)的飛速發(fā)展,用于纖維增強(qiáng)復(fù)合材料的結(jié)構(gòu)件也在不斷發(fā)展,復(fù)合材料結(jié)構(gòu)件的性能和質(zhì)量越來越重要?,F(xiàn)有技術(shù)中,復(fù)合材料成型結(jié)構(gòu)件主要由真空灌注工藝成型而成,而現(xiàn)有技術(shù)中真空灌注工藝影響因素復(fù)雜多變,成型后的構(gòu)件包含多種質(zhì)量缺陷,而成型結(jié)構(gòu)件灌注導(dǎo)流管下發(fā)白現(xiàn)象尤為常見。復(fù)合材料主要由基體和增強(qiáng)體組成,纖維增強(qiáng)復(fù)合材料則主要由基體樹脂和增強(qiáng)纖維組成,使基體材料及增強(qiáng)材料在性能上取長補(bǔ)短,產(chǎn)生協(xié)同效應(yīng),滿足實(shí)際應(yīng)用的要求。復(fù)合材料的基體通常使用熱塑性樹脂或熱固性樹脂,雖然這種材料的強(qiáng)度和模量都比較低,但由于其良好的粘彈性和彈塑性,可承受較大的應(yīng)變,基體樹脂通過和纖維表面上的粘結(jié)力、截面上的剪切應(yīng)力,支撐纖維、傳遞載荷、均勻載荷。復(fù)合材料作為各種終端產(chǎn)品結(jié)構(gòu)件的重要組成部分,其質(zhì)量決定著結(jié)構(gòu)件的性能和壽命,而結(jié)構(gòu)件的質(zhì)量及性能主要由組成結(jié)構(gòu)件的復(fù)合材料性能及其成型工藝來決定。對于選定復(fù)合材料的風(fēng)力發(fā)電葉片及船舶等大型結(jié)構(gòu)件來說,保證葉片或船舶的整體質(zhì)量和性能的關(guān)鍵就取決于結(jié)構(gòu)件的成型工藝。目前風(fēng)電葉片、船舶所用復(fù)合材料以玻璃纖維復(fù)合材料占主要地位,通過真空灌注工藝灌注而成,真空灌注工藝對于制品的品質(zhì)影響因素復(fù)雜多變,成型后的構(gòu)件可能包含多種質(zhì)量缺陷,而灌注導(dǎo)流管其流道下發(fā)白現(xiàn)象尤為常見,其流道下發(fā)白原因之一為導(dǎo)流管內(nèi)樹脂放熱溫度過高。這樣的缺陷嚴(yán)重影響結(jié)構(gòu)件的質(zhì)量和性能,最終影響終端產(chǎn)品的使用壽命及風(fēng)險(xiǎn)。本發(fā)明提出一種解決方法,藉由降低導(dǎo)流管內(nèi)樹脂總量,進(jìn)而降低固化反應(yīng)時(shí)樹脂的放熱量,有效解決導(dǎo)流管下發(fā)白的問題,實(shí)驗(yàn)灌注證明此方案不影響實(shí)際真空灌注成型效率,具有良好的灌注效果,對于保證和提高復(fù)合材料終端產(chǎn)品結(jié)構(gòu)件的實(shí)際應(yīng)用具有重要的現(xiàn)實(shí)意義。技術(shù)實(shí)現(xiàn)要素:本發(fā)明所要解決的技術(shù)問題是針對上述現(xiàn)有技術(shù)的缺陷,提供一種灌注效果好、可重復(fù)利用且能夠有效避免管道壁發(fā)白、材料浪費(fèi)的復(fù)合材料真空灌注工藝成型用導(dǎo)流管。本發(fā)明為解決上述技術(shù)問題采用以下技術(shù)方案:本發(fā)明提供了一種復(fù)合材料真空灌注工藝成型用導(dǎo)流管,包括導(dǎo)流管本體1,所述導(dǎo)流管本體1的弧形截面為劣弧形結(jié)構(gòu),所述導(dǎo)流管本體1的左右兩端分別水平設(shè)置有與其一體成型的左底板2和右底板3,所述左底板2和右底板3相對的一端位于所述導(dǎo)流管本體1下方位置。進(jìn)一步地,在所述的復(fù)合材料真空灌注工藝成型用導(dǎo)流管上,所述左底板2和右底板3相對的一端上沿所述導(dǎo)流管主體1延伸方向等間距設(shè)有多個(gè)導(dǎo)流孔4。進(jìn)一步優(yōu)選地,在所述的復(fù)合材料真空灌注工藝成型用導(dǎo)流管上,所述導(dǎo)流孔4的孔徑為15-20mm,相鄰兩導(dǎo)流孔4的間距為20-30mm。進(jìn)一步地,在所述的復(fù)合材料真空灌注工藝成型用導(dǎo)流管上,所述導(dǎo)流管由材質(zhì)為塑料、復(fù)合塑料材料、金屬或非金屬材料制成。進(jìn)一步地,在所述的復(fù)合材料真空灌注工藝成型用導(dǎo)流管上,所述導(dǎo)流管本體1弧形截面的弧度大小為0.2-0.8πrad。進(jìn)一步地,在所述的復(fù)合材料真空灌注工藝成型用導(dǎo)流管上,所述導(dǎo)流管本體1的半徑為15-25mm,其管壁的厚度為1.0-2.5mm。進(jìn)一步地,在所述的復(fù)合材料真空灌注工藝成型用導(dǎo)流管上,所述左底板2、右底板3的寬度與所述左底板2和右底板3之間的間距大小相同,為12-20mm。進(jìn)一步地,在所述的復(fù)合材料真空灌注工藝成型用導(dǎo)流管上,所述左底板2和右底板3的厚度為厚度為1.0-2.5mm。作為本發(fā)明的一個(gè)替代技術(shù)方案,本發(fā)明還提供了一種復(fù)合材料真空灌注工藝成型用導(dǎo)流管,與上述導(dǎo)流管本體1的弧形截面為劣弧形結(jié)構(gòu)不同的是,該替代技術(shù)方案中導(dǎo)流管本體1的橫截面為三角形結(jié)構(gòu),所述導(dǎo)流管本體1的左右兩端分別水平設(shè)置有與其一體成型的左底板2和右底板3。作為本發(fā)明的另一個(gè)替代技術(shù)方案,本發(fā)明還一種復(fù)合材料真空灌注工藝成型用導(dǎo)流管,與上述導(dǎo)流管本體1的弧形截面為劣弧形結(jié)構(gòu)不同的是,該替代技術(shù)方案中所述導(dǎo)流管本體1的橫截面為矩形結(jié)構(gòu),所述導(dǎo)流管本體1的左右兩端分別水平設(shè)置有與其一體成型的左底板2和右底板3。進(jìn)一步地,在所述的復(fù)合材料真空灌注工藝成型用導(dǎo)流管上,所述導(dǎo)流管本體1的弧形截面為長方形或正方形結(jié)構(gòu)。本發(fā)明采用以上技術(shù)方案,與現(xiàn)有技術(shù)相比,具有如下技術(shù)效果:本發(fā)明的復(fù)合材料真空灌注工藝成型用導(dǎo)流管,創(chuàng)造性的將導(dǎo)流管本體設(shè)置為劣弧形結(jié)構(gòu),并在其兩底端分別設(shè)置地板,使得本申請導(dǎo)流管內(nèi)部的截面積相比現(xiàn)有導(dǎo)流管的截面積減低了10-90%,同時(shí)樹脂固化反應(yīng)放熱峰溫度隨內(nèi)部填充樹脂量減少而降低,導(dǎo)流管內(nèi)樹脂放熱峰較現(xiàn)行技術(shù)導(dǎo)流管管內(nèi)樹脂放熱峰溫度小于10以上,有效避免了復(fù)合材料層因?qū)Я鞴軆?nèi)樹脂放熱高溫而產(chǎn)生的發(fā)白現(xiàn)象,同時(shí)為實(shí)際生產(chǎn)應(yīng)用節(jié)約一定樹脂用量,減少不必要的廢料。附圖說明圖1為現(xiàn)有技術(shù)中導(dǎo)流管的結(jié)構(gòu)示意圖;圖2為本發(fā)明一種復(fù)合材料真空灌注工藝成型用導(dǎo)流管的結(jié)構(gòu)示意圖;圖3為本發(fā)明一種復(fù)合材料真空灌注工藝成型用導(dǎo)流管的俯視結(jié)構(gòu)示意圖;圖4為本發(fā)明一種橫截面為三角形結(jié)構(gòu)的導(dǎo)流管的結(jié)構(gòu)示意圖;圖5為本發(fā)明一種橫截面為長方形形結(jié)構(gòu)的導(dǎo)流管的結(jié)構(gòu)示意圖;圖6為本發(fā)明一種橫截面為正方形形結(jié)構(gòu)的導(dǎo)流管的結(jié)構(gòu)示意圖;圖7為采用現(xiàn)有導(dǎo)流管下方復(fù)合材料樣品的光學(xué)顯微鏡圖;圖8為采用采用劣弧型導(dǎo)流管下方復(fù)合材料樣品的光學(xué)顯微鏡圖;圖9為采用現(xiàn)有導(dǎo)流管和采用本發(fā)明劣弧型導(dǎo)流管的進(jìn)膠量與時(shí)間曲線圖;圖10為采用現(xiàn)有導(dǎo)流管和采用本發(fā)明劣弧型導(dǎo)流管內(nèi)樹脂放熱溫度與時(shí)間曲線圖。具體實(shí)施方式在樹脂灌注生產(chǎn)過程中,對于不同基體不同材料結(jié)構(gòu)件需要選擇合適的工藝方法,而現(xiàn)有技術(shù)中在如何選擇合適的工藝方法沒有進(jìn)行深入研究。本發(fā)明針對這一問題進(jìn)行研究,也通過一定實(shí)驗(yàn)數(shù)據(jù)及理論依據(jù),提出了一種如何進(jìn)行設(shè)計(jì)合適的工藝成型構(gòu)件,對于改善復(fù)合材料發(fā)白缺陷具有良好的指導(dǎo)意義及良好的技術(shù)效果,同時(shí)也為實(shí)際生產(chǎn)應(yīng)用中節(jié)省基體材料。具體地,本發(fā)明所提出的導(dǎo)流管的截面積為其在真空灌注應(yīng)用中內(nèi)部填充樹脂量比現(xiàn)有技術(shù)中降低10%-90%(現(xiàn)行技術(shù)導(dǎo)流管設(shè)計(jì)樣式如圖1所示),本發(fā)明導(dǎo)流管的橫截面為劣弧形結(jié)構(gòu)、三角形結(jié)構(gòu)、長方形或正方形結(jié)構(gòu),或其它橫截面積比現(xiàn)有導(dǎo)流管的橫截面積小10%-90%的任何形狀的結(jié)構(gòu)。同時(shí)樹脂固化反應(yīng)放熱峰溫度隨內(nèi)部填充樹脂量減少而降低,減低復(fù)合材料層因?qū)Я鞴軆?nèi)樹脂放熱高溫而產(chǎn)生的發(fā)白現(xiàn)象,同時(shí)為實(shí)際生產(chǎn)應(yīng)用節(jié)約一定樹脂用量,減少不必要的廢料。下面通過具體實(shí)施例對本發(fā)明進(jìn)行詳細(xì)和具體的介紹,以使更好的理解本發(fā)明,但是下述實(shí)施例并不限制本發(fā)明范圍。實(shí)施例1如圖1所示為現(xiàn)有技術(shù)中的真空灌注用導(dǎo)流管,其由導(dǎo)流管本體1和設(shè)置在導(dǎo)流管本體1底端兩側(cè)的底板2和底部3組成,導(dǎo)流管本體1的截面為優(yōu)弧形結(jié)構(gòu),在采用該中導(dǎo)流管進(jìn)行真空灌注時(shí),導(dǎo)管內(nèi)樹脂固化反應(yīng)放熱峰溫度較高,使得導(dǎo)管復(fù)合材料層因?qū)Я鞴軆?nèi)樹脂放熱高溫而產(chǎn)生的發(fā)白現(xiàn)象,降低了導(dǎo)流管的使用壽命,且存在一定樹脂的材料浪費(fèi)。如圖2所示,為本實(shí)施例提供的一種復(fù)合材料真空灌注工藝成型用導(dǎo)流管,包括導(dǎo)流管本體1,導(dǎo)流管本體1的弧形截面為劣弧形結(jié)構(gòu),導(dǎo)流管本體1弧形截面的弧度大小為0.2-0.8πrad,導(dǎo)流管本體1的左右兩端分別水平設(shè)置有與其一體成型的左底板2和右底板3,左底板2和右底板3相對的一端位于導(dǎo)流管本體1下方位置,也就是說導(dǎo)流管本體1的兩端分別與左底板2和右底板3的上端面中部連接,使左底板2和右底板3相對的一端延伸至由導(dǎo)流管本體1所形成的圓形圈內(nèi)。在本實(shí)施例的復(fù)合材料真空灌注工藝成型用導(dǎo)流管上,如圖3所示,左底板2和右底板3相對的一端上沿導(dǎo)流管主體1延伸方向等間距設(shè)有多個(gè)導(dǎo)流孔4,其中導(dǎo)流孔4的個(gè)數(shù)可根據(jù)產(chǎn)品的規(guī)模大小進(jìn)行設(shè)置;且導(dǎo)流孔4的孔徑為15-20mm,相鄰兩導(dǎo)流孔4的間距為20-30mm;優(yōu)選地,導(dǎo)流孔4的孔徑為16-18mm,相鄰兩導(dǎo)流孔4的間距為22-26mm。這樣在真空灌注時(shí),樹脂基體能夠從左底板2和右底板3之間的開口以及導(dǎo)流孔4足量、快速、均勻的沿著導(dǎo)流管導(dǎo)入待灌注產(chǎn)品上,提高樹脂灌注效果。于上述技術(shù)方案的基礎(chǔ)上,在本實(shí)施例的復(fù)合材料真空灌注工藝成型用導(dǎo)流管中,導(dǎo)流管由材質(zhì)為塑料、復(fù)合塑料材料、金屬或非金屬材料制成。優(yōu)選的采用復(fù)合塑料材料或金屬材料制成;更為優(yōu)選地,采用聚丙烯樹脂材和聚乙烯樹脂混合材質(zhì)制成,聚丙烯樹脂材質(zhì)偏軟,聚乙烯樹脂材質(zhì)偏硬,將二者按一定的比例混合制得的導(dǎo)流管,不僅耐熱、耐低溫沖擊性能優(yōu)越,同時(shí)還能保持良好的剛性。于上述技術(shù)方案的基礎(chǔ)上,在本實(shí)施例的復(fù)合材料真空灌注工藝成型用導(dǎo)流管中,導(dǎo)流管本體1弧形截面的弧度大小為0.4-0.6πrad;優(yōu)選地,導(dǎo)流管本體1弧形截面的弧度大小為0.5πrad。采用劣弧形截面的導(dǎo)流管,能夠使得導(dǎo)流管內(nèi)部的截面積相比現(xiàn)有導(dǎo)流管的截面積減低10-90%,導(dǎo)流管內(nèi)樹脂放熱峰較現(xiàn)行技術(shù)導(dǎo)流管管內(nèi)樹脂放熱峰溫度小于10以上,有效避免了復(fù)合材料層因?qū)Я鞴軆?nèi)樹脂放熱高溫而產(chǎn)生的發(fā)白現(xiàn)象。于上述技術(shù)方案的基礎(chǔ)上,在本實(shí)施例的復(fù)合材料真空灌注工藝成型用導(dǎo)流管中,導(dǎo)流管本體1的半徑為15-25mm,其管壁的厚度為1.0-2.5mm;優(yōu)選地,導(dǎo)流管本體1的半徑為22mm,其管壁的厚度為2.2mm。左底板2、右底板3的寬度與左底板2和右底板3之間的間距大小相同,均為12-20mm,其中左底板2和右底板3之間的間距是指導(dǎo)流管開口的寬度。左底板2和右底板3的厚度為厚度為1.0-2.5mm。實(shí)施例2如圖4所示,與上述劣弧形結(jié)構(gòu)的導(dǎo)流管不同的是,本實(shí)施例提供了一種復(fù)合材料真空灌注工藝成型用導(dǎo)流管,本實(shí)施例導(dǎo)流管本體1的橫截面為三角形結(jié)構(gòu),所述導(dǎo)流管本體1的左右兩端分別水平設(shè)置有與其一體成型的左底板2和右底板3。該三角形結(jié)構(gòu)的導(dǎo)流管的水平高度為17-22mm;左底板2和右底板3的寬度均為15-22mm;左底板2和右底板3相對端之間的間距為15-16mm。導(dǎo)流管本體1、左底板2和右底板3的厚度為1-2.5mm。實(shí)施例3如圖5所示,與上述劣弧形結(jié)構(gòu)的導(dǎo)流管不同的是,本實(shí)施例提供了一種復(fù)合材料真空灌注工藝成型用導(dǎo)流管,該替代技術(shù)方案中所述導(dǎo)流管本體1的橫截面為張方形結(jié)構(gòu),所述導(dǎo)流管本體1的左右兩端分別水平設(shè)置有與其一體成型的左底板2和右底板3。該長方形結(jié)構(gòu)的導(dǎo)流管的水平高度為17-22mm;左底板2的寬度、右底板3的寬度與左底板2和右底板3相對端之間的間距相等,為20-25mm。導(dǎo)流管本體1、左底板2和右底板3的厚度為1-2.5mm。實(shí)施例4如圖6所示,與上述劣弧形結(jié)構(gòu)的導(dǎo)流管不同的是,本實(shí)施例提供了一種復(fù)合材料真空灌注工藝成型用導(dǎo)流管,所述導(dǎo)流管本體1的弧形截面為的正方形結(jié)構(gòu),該正方形結(jié)構(gòu)的導(dǎo)流管的水平高度為20-25mm;左底板2的寬度、右底板3的寬度與左底板2和右底板3相對端之間的間距相等,為20-25mm。導(dǎo)流管本體1、左底板2和右底板3的厚度為1-2.5mm。性能測試:1)拋光檢測:以現(xiàn)有技術(shù)的導(dǎo)流管為對比例,以本發(fā)明實(shí)施例1導(dǎo)流管為測試?yán)?,分別將現(xiàn)有技術(shù)的導(dǎo)流管和本發(fā)明實(shí)施例1的導(dǎo)流管應(yīng)用于厚件灌注上,將導(dǎo)流管下方的復(fù)合材料裁切下來并進(jìn)行拋光,拋光完的樣品分別經(jīng)由光學(xué)顯微鏡觀察玻纖層發(fā)白狀況:如圖7所示,為采用現(xiàn)有導(dǎo)流管所制的復(fù)合材料樣品,樣品拋光后的光學(xué)顯微鏡觀察圖,發(fā)白層(亮度較暗處)約為5~7層;圖8所示,為采用劣弧型導(dǎo)流管所制的復(fù)合材料樣品,樣品拋光后的光學(xué)顯微鏡觀察圖,發(fā)白層(亮度較暗處)約為1~2層。2)灌注效率測試:以現(xiàn)有技術(shù)的導(dǎo)流管為對比例,以本發(fā)明實(shí)施例1導(dǎo)流管為測試?yán)?,分別將現(xiàn)有技術(shù)的導(dǎo)流管和本發(fā)明實(shí)施例1的導(dǎo)流管應(yīng)用于厚件灌注上進(jìn)行灌注效率測試。如圖9所示,為現(xiàn)有導(dǎo)流管與實(shí)施例1劣弧型導(dǎo)流管復(fù)合材料灌注效率曲線比較圖,經(jīng)由實(shí)驗(yàn)比較后,采用劣弧型導(dǎo)流管灌注復(fù)合材料的進(jìn)膠量曲線符合采用現(xiàn)有導(dǎo)流管灌注復(fù)合材料的進(jìn)膠量曲線,證明采用劣弧型導(dǎo)流管灌注復(fù)合材料的灌注效率與采用現(xiàn)有導(dǎo)流管灌注復(fù)合材料的灌注效率一致。3)管內(nèi)樹脂放熱溫度測試:以現(xiàn)有技術(shù)的導(dǎo)流管為對比例,以本發(fā)明實(shí)施例1-4的導(dǎo)流管為測試?yán)?,分別將現(xiàn)有技術(shù)的導(dǎo)流管和本發(fā)明實(shí)施例1-4的導(dǎo)流管應(yīng)用于厚件灌注上,并分別進(jìn)行導(dǎo)流管內(nèi)樹脂放熱峰溫度測試,具體測試結(jié)果下表一所示:表一導(dǎo)流管內(nèi)樹脂放熱峰溫度測試結(jié)果導(dǎo)流管型試管內(nèi)樹脂放熱峰溫度(℃)實(shí)施例1劣弧形導(dǎo)流管118.8實(shí)施例2三角形導(dǎo)流管123.6實(shí)施例3長方形導(dǎo)流管134.3實(shí)施例4正方形導(dǎo)流管136.9對比例現(xiàn)行技術(shù)導(dǎo)流管157.5經(jīng)由測試后,本發(fā)明實(shí)施例1-4所提供的導(dǎo)流管其管內(nèi)樹脂放熱峰較現(xiàn)行技術(shù)導(dǎo)流管管內(nèi)樹脂放熱峰溫度小于20℃以上,本發(fā)明導(dǎo)流管有效減緩流道下發(fā)白的效應(yīng)。此外,以現(xiàn)有技術(shù)的導(dǎo)流管為對比例,以本發(fā)明實(shí)施例1的導(dǎo)流管為測試?yán)?,分別將現(xiàn)有技術(shù)的導(dǎo)流管和本發(fā)明實(shí)施例1的導(dǎo)流管應(yīng)用于厚件灌注上,測試導(dǎo)流管管內(nèi)樹脂放熱溫度與時(shí)間變化關(guān)系。如圖10所示,為導(dǎo)流管管內(nèi)樹脂放熱溫度與時(shí)間曲線比較圖,經(jīng)由熱電偶計(jì)記錄導(dǎo)流管管內(nèi)樹脂放熱溫度,劣弧型導(dǎo)流管管內(nèi)樹脂放熱峰溫度明顯低于現(xiàn)有導(dǎo)流管管內(nèi)樹脂放熱峰溫度,現(xiàn)有導(dǎo)流管管內(nèi)樹脂放熱峰最高溫度:157.5℃,實(shí)施例1劣弧型導(dǎo)流管管內(nèi)樹脂放熱峰最高溫度:118.8℃。綜上可知,經(jīng)由上述1)、2)和3)測試得知導(dǎo)流管在單位長度下的截面積比現(xiàn)有技術(shù)中降低40%~60%且制造材質(zhì)為pp與pe復(fù)合塑料材料的任意導(dǎo)流管設(shè)計(jì)型試(如圖2-6所示,但樣式不限于此),可以在不影響現(xiàn)有工藝效率下,有效降低因?qū)Я鞴軆?nèi)樹脂放熱溫度過高所造成復(fù)合材料層的發(fā)白現(xiàn)象。經(jīng)由測試后,其管內(nèi)樹脂放熱峰較現(xiàn)行技術(shù)導(dǎo)流管管內(nèi)樹脂放熱峰溫度小于20℃以上,可以明顯地看出此導(dǎo)流管對于減緩流道下發(fā)白的效應(yīng)。以上對本發(fā)明的具體實(shí)施例進(jìn)行了詳細(xì)描述,但其只是作為范例,本發(fā)明并不限制于以上描述的具體實(shí)施例。對于本領(lǐng)域技術(shù)人員而言,任何對本發(fā)明進(jìn)行的等同修改和替代也都在本發(fā)明的范疇之中。因此,在不脫離本發(fā)明的精神和范圍下所作的均等變換和修改,都應(yīng)涵蓋在本發(fā)明的范圍內(nèi)。當(dāng)前第1頁12