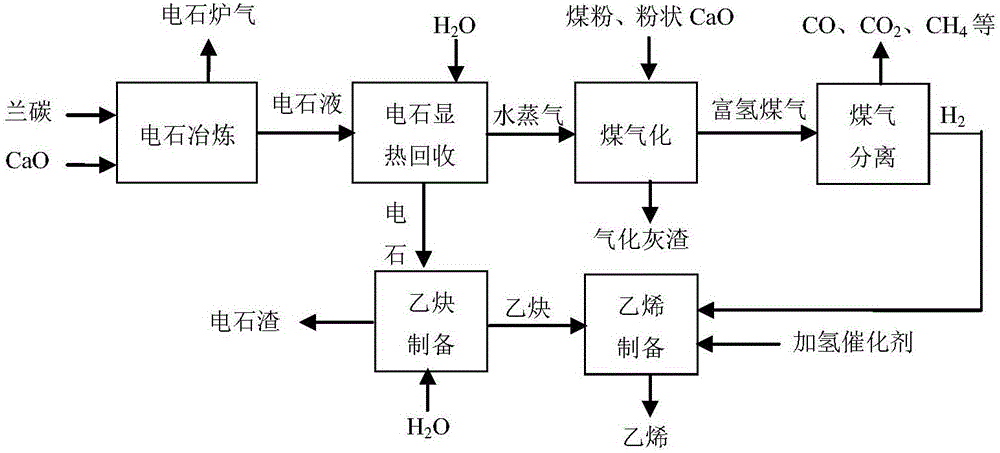
本發(fā)明總地涉及乙烯的制備工藝,具體涉及一種耦合制備乙烯的系統(tǒng)及方法。
背景技術(shù):
:目前在電石生產(chǎn)工藝中,電石在電石爐由2000℃以上的液態(tài)電石液流出電石爐至電石堝,然后在自然狀態(tài)下冷卻至室溫,無(wú)法利用電石顯熱,造成能源的極大浪費(fèi)。另外,由電石乙炔生產(chǎn)乙烯的過(guò)程中,需要外供大量的氫氣與乙炔發(fā)生加成反應(yīng)生成乙烯,氫源成為乙炔下游生產(chǎn)的關(guān)鍵制約因素,尋找廉價(jià)氫源及其生產(chǎn)工藝與電石冶煉、電石乙炔制乙烯耦合為目前的研究熱點(diǎn)問(wèn)題。技術(shù)實(shí)現(xiàn)要素:本發(fā)明的目的在于提供一種將煤氣化和乙烯制備等技術(shù)耦合的新工藝。本發(fā)明首先提供了一種耦合制備乙烯的系統(tǒng),所述系統(tǒng)包括氣化爐、煤氣分離提氫裝置和加氫反應(yīng)器;所述氣化爐包括煤粉入口、水蒸氣入口和富氫煤氣出口;所述煤氣分離提氫裝置包括富氫煤氣入口和氫氣出口,所述富氫煤氣入口與所述氣化爐的富氫煤氣出口相連;所述加氫反應(yīng)器包括氫氣入口、加氫催化劑入口、乙炔入口和乙烯出口,所述氫氣入口與所述煤氣分離提氫裝置的氫氣出口相連。在本發(fā)明的一個(gè)實(shí)施方案中,所述系統(tǒng)還包括電石爐、電石顯熱回收器和乙炔發(fā)生器;所述電石爐包括蘭炭入口、CaO入口和液體電石出口;所述電石顯熱回收器包括液體電石入口、水入口、水蒸氣出口和電石出口,所述液態(tài)電石入口與所述電石爐的液態(tài)電石出口相連,所述水蒸氣出口與所述氣化爐的水蒸氣入口相連;所述乙炔發(fā)生器包括電石入口、水入口和乙炔出口,所述電石入口與所述電石顯熱回收器的電石出口相連,所述乙炔出口與所述加氫反應(yīng)器的乙炔入口相連。在本發(fā)明的一個(gè)實(shí)施方案中,所述氣化爐還包括氣化催化劑入口。此外,本發(fā)明還提供了一種利用上述系統(tǒng)制備乙烯的方法,包括以下步驟:煤氣化:將煤粉和水蒸氣分別經(jīng)由所述煤入口和所述水蒸氣入口送入所述氣化爐中,在T1溫度下所述煤氣化,得到富氫煤氣;煤氣分離:將所述富氫煤氣送入所述煤氣分離提氫裝置中進(jìn)行分離,得到氫氣;乙烯制備:在T2溫度下,將乙炔、加氫催化劑和所述氫氣分別經(jīng)由所述乙炔入口、加氫催化劑入口和所述氫氣入口送入所述加氫反應(yīng)器中,所述乙炔和所述氫氣反應(yīng)生成乙烯。在本發(fā)明的一個(gè)實(shí)施方案中,所述方法還包括以下步驟:電石冶煉:在T3溫度下,用蘭炭和CaO進(jìn)行冶煉制備液態(tài)電石;顯熱回收:用所述液態(tài)電石與水間接換熱,得到固態(tài)電石和水蒸氣,將所述水蒸氣送入所述氣化爐中;乙炔制備:用固態(tài)電石制備乙炔,將所述乙炔送入所述加氫反應(yīng)器中。在本發(fā)明的一個(gè)實(shí)施方案中,在所述煤氣化步驟中,還往所述氣化爐中通入了氣化催化劑,所述煤粉與所述氣化催化劑的質(zhì)量比例為25:1-15:1。在本發(fā)明的一個(gè)實(shí)施方案中,所述氣化催化劑為粉狀CaO,所述粉狀CaO的粒徑≤0.2mm,優(yōu)選粒徑≤0.1mm。在本發(fā)明的一個(gè)實(shí)施方案中,所述煤的粒徑≤0.5mm,優(yōu)選粒徑≤0.1mm。所述煤的水分含量≤8wt%。所述煤的灰分含量≤15wt%。所述煤的揮發(fā)分含量≥30wt%。在本發(fā)明的一個(gè)實(shí)施方案中,所述T1為1200-2000℃。所述T2為150-250℃。在本發(fā)明的一個(gè)實(shí)施方案中,所述蘭炭的粒徑≤30mm,優(yōu)選粒徑≤25mm。所述蘭炭的水分含量≤2wt%。所述CaO的粒徑≤30mm,優(yōu)選粒徑≤25mm。所述T3為1900-2200℃,其優(yōu)選為2050℃。本發(fā)明將煤氣化與乙烯制備工藝耦合,利用煤氣化產(chǎn)生的煤氣中的氫氣與乙炔進(jìn)行加氫反應(yīng),制備乙烯,降低了生產(chǎn)成本。整個(gè)系統(tǒng)工藝路線非常簡(jiǎn)單。此外,本申請(qǐng)還回收了電石液的顯熱,極大程度地降低損耗、節(jié)約了能源。附圖說(shuō)明圖1為本發(fā)明實(shí)施例中的一種耦合制備乙烯的系統(tǒng)的結(jié)構(gòu)示意圖;圖2為本發(fā)明實(shí)施例中的一種利用上述系統(tǒng)制備乙烯的工藝流程圖。具體實(shí)施方式以下結(jié)合附圖和實(shí)施例,對(duì)本發(fā)明的具體實(shí)施方式進(jìn)行更加詳細(xì)的說(shuō)明,以便能夠更好地理解本發(fā)明的方案以及其各個(gè)方面的優(yōu)點(diǎn)。然而,以下描述的具體實(shí)施方式和實(shí)施例僅是說(shuō)明的目的,而不是對(duì)本發(fā)明的限制。參考圖1,本發(fā)明提供的制備乙烯的系統(tǒng)包括氣化爐1、煤氣分離提氫裝置2、加氫反應(yīng)器3、電石爐4、電石顯熱回收器5和乙炔發(fā)生器6。氣化爐1包括煤粉入口101、水蒸氣入口、氣化催化劑入口和富氫煤氣出口。氣化爐1優(yōu)選為氣流床氣化爐。煤氣分離提氫裝置2包括富氫煤氣入口、氫氣出口和煤氣出口,富氫煤氣入口與氣化爐1的富氫煤氣出口相連。加氫反應(yīng)器3包括氫氣入口、加氫催化劑入口301、乙炔入口和乙烯出口302,氫氣入口與煤氣分離提氫裝置2的氫氣出口相連。電石爐4包括蘭炭入口401、CaO入口402、電石爐氣出口和液體電石出口。電石顯熱回收器5包括液體電石入口、水入口501、水蒸氣出口和電石出口,液態(tài)電石入口與電石爐4的液態(tài)電石出口相連,水蒸氣出口與氣化爐1的水蒸氣入口相連。電石顯熱回收器5的換熱方式為間接換熱。乙炔發(fā)生器6包括電石入口、水入口601、電石渣出口602和乙炔出口,電石入口與所述電石顯熱回收器5的電石出口相連,乙炔出口與加氫反應(yīng)器3的乙炔入口相連。其中,電石爐4、電石顯熱回收器5和乙炔發(fā)生器6并不是系統(tǒng)必須有的裝置,用于制備乙烯的乙炔可由電石制備,也可直接外購(gòu);作為氣化劑的水蒸氣可由水與液態(tài)電石間接換熱制得,也可由其他方式制備。圖2為本發(fā)明一種利用上述系統(tǒng)制備乙烯的方式,該方法包括如下步驟:電石冶煉:在T3溫度下,用蘭炭和CaO進(jìn)行冶煉制備液態(tài)電石;顯熱回收:用所述液態(tài)電石與水間接換熱,得到固態(tài)電石和水蒸氣,將所述水蒸氣送入所述氣化爐中;乙炔制備:用固態(tài)電石制備乙炔,將所述乙炔送入所述加氫反應(yīng)器中。煤氣化:將煤粉和水蒸氣分別經(jīng)由所述煤入口和所述水蒸氣入口送入所述氣化爐中,在T1溫度下所述煤氣化,得到富氫煤氣;煤氣分離:將所述富氫煤氣送入所述煤氣分離提氫裝置中進(jìn)行分離,得到氫氣;乙烯制備:在T2溫度下,將乙炔、加氫催化劑和所述氫氣分別經(jīng)由所述乙炔入口、加氫催化劑入口和所述氫氣入口送入所述加氫反應(yīng)器中,所述乙炔和所述氫氣反應(yīng)生成乙烯。本發(fā)明采用水蒸氣作為煤氣化時(shí)的催化劑,水蒸氣與煤的質(zhì)量比≤0.96,優(yōu)選質(zhì)量比≤0.80。水蒸氣是水與高溫電石液間接換熱制備得到的,回收了電石液的顯熱,極大程度地降低損耗、節(jié)約了能源。上述工藝中用于制備乙烯的乙炔可直接外購(gòu),用作煤氣化劑的水蒸氣也可由其他方式制備。本發(fā)明將煤氣化與乙烯制備工藝耦合,利用煤氣化產(chǎn)生的煤氣中的氫氣與乙炔進(jìn)行加氫反應(yīng),制備乙烯,降低了生產(chǎn)成本。整個(gè)系統(tǒng)工藝路線非常簡(jiǎn)單。此外,本發(fā)明所有的設(shè)備均是在保溫、密閉及阻燃的條件下工作的,物料在各個(gè)設(shè)備間的輸送也均是在保溫及阻燃的條件下進(jìn)行的,充分了利用了氣化及電石冶煉的高溫顯熱,極大地降低了損耗,節(jié)約了能源。在氣化煤時(shí),還可往氣化爐1中通入催化劑,以提高煤氣化的效果,增加煤氣中氫氣的含量。CaO在煤氣化過(guò)程中具有較好的催化作用,并兼具良好的固硫性能,在提高煤氣化的反應(yīng)速率的同時(shí),能實(shí)現(xiàn)煤的潔凈轉(zhuǎn)化。經(jīng)過(guò)大量的實(shí)驗(yàn)發(fā)現(xiàn),粉狀CaO的添加量為煤的質(zhì)量的1/25-1/15時(shí),其催化效果最好。煤的粒徑越小、水分含量越少,氣化的效果越好。本申請(qǐng)中,煤的粒徑優(yōu)選≤0.5mm,更好地,粒徑最好≤0.1mm。同樣地,煤的水分含量越少、灰分含量越少、揮發(fā)分含量越多,其氣化的效果也越好。本申請(qǐng)中,煤的水分含量?jī)?yōu)選≤8wt%,煤的灰分含量?jī)?yōu)選≤15wt%,煤的揮發(fā)分含量?jī)?yōu)選≥30%。本申請(qǐng)采用蘭炭和石灰石冶煉電石,其粒徑越小冶煉的效果越好。蘭炭的粒徑優(yōu)選≤30mm,優(yōu)選粒徑優(yōu)選≤25mm。CaO的粒徑優(yōu)選≤30mm,優(yōu)選粒徑優(yōu)選≤25mm。蘭炭和CaO的質(zhì)量比為0.55-0.70,優(yōu)選0.63。煤氣化時(shí)的溫度T1最好為1200℃-2000℃。制備乙烯時(shí)的溫度T2最好為150-250℃。冶煉制備電石的溫度T3優(yōu)選為1900℃-2200℃,更好地,T3最好為2050℃。溫度太低,煤氣化、制備乙烯及冶煉電石的效果不好;溫度太高,浪費(fèi)能源。若T2太高,無(wú)法制得高品位的乙烯。此外,氣化爐1的操作壓力可為任意氣化爐所允許的壓力。下面參考具體實(shí)施例,對(duì)本發(fā)明進(jìn)行說(shuō)明。下述實(shí)施例中所取工藝條件數(shù)值均為示例性的,其可取數(shù)值范圍如前述
發(fā)明內(nèi)容中所示。下述實(shí)施例所用的檢測(cè)方法均為本行業(yè)常規(guī)的檢測(cè)方法。實(shí)施例1本實(shí)施例采用圖1所示的系統(tǒng)及圖2所示的工藝路線制備乙炔,具體如下:準(zhǔn)備原料:將不粘煤破碎,選取粒徑≤0.5mm的煤粉,再將其干燥至水分含量為8wt%;此煤的灰分含量為7wt%、揮發(fā)分含量為30wt%。將CaO破碎,分別選取粒徑≤30mm的CaO及粒徑≤0.2mm的粉狀CaO。將蘭炭破碎,選取粒徑≤30mm的蘭炭。電石冶煉:取550kg蘭炭送入電石爐4中,再往里面加入1000kg的CaO,在1900℃下冶煉制備液態(tài)電石。顯熱回收:用液態(tài)電石與水換熱,得到固態(tài)電石和水蒸氣。乙炔制備:取950kg固態(tài)電石與1400kg水反應(yīng)制備乙炔。煤氣化:取1000kg煤粉送入氣化爐1中,再往氣化爐1中加入40kg粉狀CaO和960kg水蒸氣,在2000℃進(jìn)行煤氣化,得到富氫煤氣。煤氣分離:將富氫煤氣送入煤氣分離提氫裝置2中進(jìn)行分離,得到氫氣。乙烯制備:將305m2乙炔、4.5kg加氫催化劑和310m2氫氣送入加氫反應(yīng)器3中,在250℃下,乙炔和氫氣反應(yīng)生成乙烯。產(chǎn)物及液體電石出口的溫度請(qǐng)見(jiàn)表1。實(shí)施例2本實(shí)施例采用圖1所示的系統(tǒng)及圖2所示的工藝路線制備乙炔,具體如下:準(zhǔn)備原料:將褐煤破碎,選取粒徑≤0.1mm的煤粉,再將其干燥至水分含量為5wt%;此煤的灰分含量為15wt%、揮發(fā)分含量為35wt%。將CaO破碎,分別選取粒徑≤25mm的CaO及粒徑≤0.1mm的粉狀CaO。將蘭炭破碎,選取粒徑≤25mm的蘭炭。電石冶煉:取700kg蘭炭送入電石爐4中,再往里面加入1000kg的CaO,在2050℃下冶煉制備液態(tài)電石。顯熱回收:用液態(tài)電石與水換熱,得到固態(tài)電石和水蒸氣。乙炔制備:取1014kg固態(tài)電石與1500kg水反應(yīng)制備乙炔。煤氣化:取1000kg煤粉送入氣化爐1中,再往氣化爐1中加入67kg粉狀CaO和800kg水蒸氣,在1200℃進(jìn)行煤氣化,得到富氫煤氣。煤氣分離:將富氫煤氣送入煤氣分離提氫裝置2中進(jìn)行分離,得到氫氣。乙烯制備:將311m2乙炔、4.7kg加氫催化劑和315m2氫氣送入加氫反應(yīng)器3中,在150℃下,乙炔和氫氣反應(yīng)生成乙烯。產(chǎn)物及液體電石出口的溫度請(qǐng)見(jiàn)表1。實(shí)施例3本實(shí)施例采用圖1所示的系統(tǒng)及圖2所示的工藝路線制備乙炔,具體如下:準(zhǔn)備原料:將長(zhǎng)焰煤破碎,選取粒徑≤0.3mm的煤粉,再將其干燥至水分含量為6wt%;此煤的灰分含量為10wt%、揮發(fā)分含量為32wt%。將CaO破碎,分別選取粒徑≤20mm的CaO及粒徑≤0.08mm的粉狀CaO。將蘭炭破碎,選取粒徑≤20mm的蘭炭。電石冶煉:取630kg蘭炭送入電石爐4中,再往里面加入1000kg的CaO,在2200℃下冶煉制備液態(tài)電石。顯熱回收:用液態(tài)電石與水換熱,得到固態(tài)電石和水蒸氣。乙炔制備:取997kg固態(tài)電石與1480kg水反應(yīng)制備乙炔。煤氣化:取1000kg煤粉送入氣化爐1中,再往氣化爐1中加入50kg粉狀CaO和600kg水蒸氣,在1600℃進(jìn)行煤氣化,得到富氫煤氣。煤氣分離:將富氫煤氣送入煤氣分離提氫裝置2中進(jìn)行分離,得到氫氣。乙烯制備:將315m2乙炔、4.5kg加氫催化劑和320m2氫氣送入加氫反應(yīng)器3中,在200℃下,乙炔和氫氣反應(yīng)生成乙烯。產(chǎn)物及液體電石出口的溫度請(qǐng)見(jiàn)表1。表1各實(shí)施例產(chǎn)物及液體電石出口的溫度實(shí)施例1實(shí)施例2實(shí)施例3煤氣/m3229723522346氫氣/m3137814131408電石/kg9501014997水蒸氣//kg960800600乙烯/m3294299302液體電石出口/℃176319752086從表1可以看出,本發(fā)明制得的煤氣中氫氣的含量比較多,完全可以用于制備乙烯。此外,由于利用了液體電石的顯熱,極大的降低了損耗,節(jié)約了能源。綜上,本發(fā)明將煤氣化與乙烯制備工藝耦合,利用煤氣化產(chǎn)生的煤氣中的氫氣與乙炔進(jìn)行加氫反應(yīng),制備乙烯,降低了生產(chǎn)成本。整個(gè)系統(tǒng)工藝路線非常簡(jiǎn)單。此外,本申請(qǐng)還回收了電石液的顯熱,極大程度地降低損耗、節(jié)約了能源。最后應(yīng)說(shuō)明的是:顯然,上述實(shí)施例僅僅是為清楚地說(shuō)明本發(fā)明所作的舉例,而并非對(duì)實(shí)施方式的限定。對(duì)于所屬領(lǐng)域的普通技術(shù)人員來(lái)說(shuō),在上述說(shuō)明的基礎(chǔ)上還可以做出其它不同形式的變化或變動(dòng)。這里無(wú)需也無(wú)法對(duì)所有的實(shí)施方式予以窮舉。而由此所引申出的顯而易見(jiàn)的變化或變動(dòng)仍處于本發(fā)明的保護(hù)范圍之中。當(dāng)前第1頁(yè)1 2 3